When builders need to deliver versatile, rapidly deployable structural solutions, portable buildings stand out as the construction industry’s answer. These adaptable structures—also called relocatable buildings (RBs)—represent a significant evolution in addressing temporary and semi-permanent construction needs, particularly in time-sensitive environments.
At their core, portable buildings are prefabricated structures engineered in controlled manufacturing facilities rather than conventional construction sites. These structures are built according to established building codes, ensuring they maintain safety and quality while offering the crucial advantage of mobility. Unlike traditional construction, these buildings don’t require permanent foundations, allowing them to be transported between locations as client needs evolve.
The growing demand for these structures reflects their practical versatility. From construction site offices and temporary classrooms to medical clinics and sales centers, portable buildings offer solutions that conventional construction simply can’t match in terms of deployment speed and flexibility. Their ability to be repurposed across multiple sites makes them particularly valuable in today’s fast-paced development landscape.
What Are the Different Types of Portable Buildings?
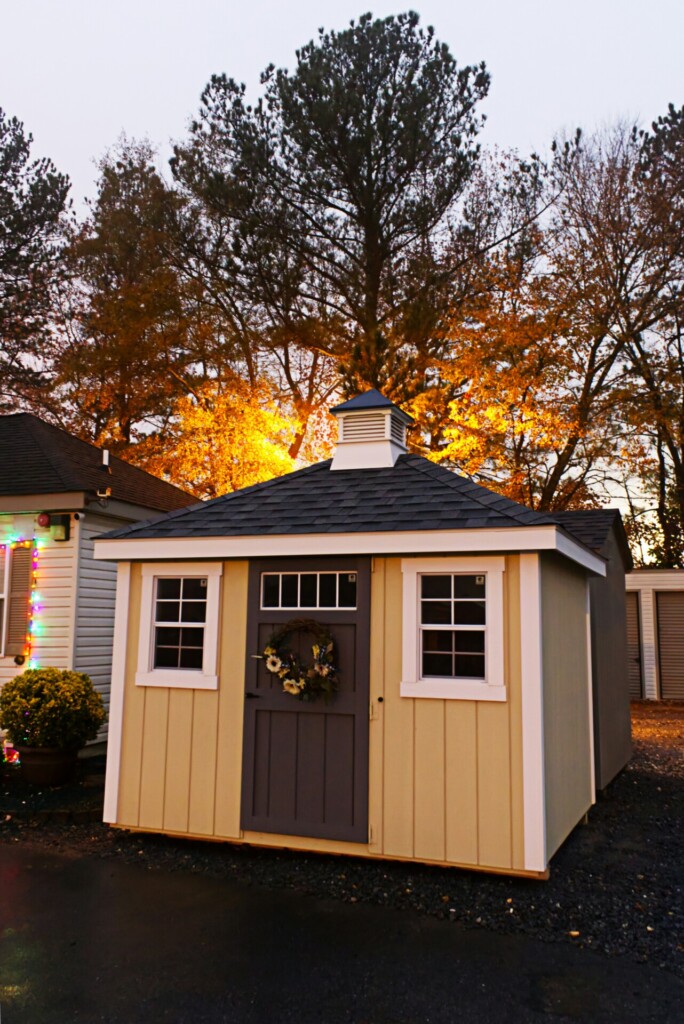
As general contractors, we regularly work with clients seeking flexible space solutions beyond traditional construction. Portable buildings offer versatility without the permanence and expense of conventional builds. These structures arrive either fully assembled or in components that we can quickly install on prepared sites.
Storage Sheds
Storage sheds are the most commonly deployed portable building type across our projects. We construct these practical structures using durable materials with secure locking systems to protect equipment and seasonal items. Many of our developer clients appreciate how these buildings can be strategically placed to maximize property functionality without extensive sitework.
The construction approach for storage sheds varies based on property requirements. We typically install these with reinforced flooring systems, customizable shelving, and organization features that transform otherwise unused space into valuable storage areas. For commercial properties, we often incorporate additional security elements and scaled dimensions to accommodate specific inventory needs.
Portable Barns
Agricultural applications demand specialized portable structures, which is why our barn construction focuses on practical, purpose-built designs. When developing rural properties, we implement pole barn structures featuring proper ventilation systems and strategically designed partitioning to accommodate livestock needs.
The lofted barn variation has become increasingly popular among our clients with space constraints. These designs incorporate overhead storage areas that maximize cubic footage without expanding the building’s footprint. For property owners with equipment storage requirements, we engineer these structures with reinforced entryways and increased ceiling clearance to accommodate larger agricultural implements.
Garage Structures
Vehicle protection remains a primary consideration across residential and commercial developments. Our portable garage implementations range from single-vehicle enclosures to multi-bay structures housing fleets or equipment. We construct these with reinforced framing capable of withstanding regional weather conditions while providing secure storage.
Beyond basic vehicle coverage, our garage structures often include workshop components tailored to specific property needs. For commercial developments, we frequently incorporate electrical systems, ventilation solutions, and specialized flooring options that transform these buildings into functional work environments. The adaptability of these structures makes them valuable additions to properties requiring flexible vehicle accommodation.
Type | Size Range | Materials | Common Applications |
---|---|---|---|
Storage Sheds | 8’x12′ to 16’x48′ | Wood, Metal | Equipment storage, Seasonal items |
Portable Barns | 12’x16′ to 16’x48′ | Wood, Metal | Livestock housing, Equipment storage |
Garage Structures | 12’x16′ to 16’x48′ | Wood, Metal | Vehicle storage, Workshops |
Cabins and Tiny Homes | 12’x16′ to 16’x48′ | Wood | Living spaces, Vacation homes |
Specialty Structures | Varies | Wood, Metal | Vendor booths, Temporary classrooms |
Cabins and Tiny Homes
The tiny home movement has transformed how we approach portable living spaces. When developing these structures, we focus on maximizing functionality through innovative space utilization. Our construction teams implement efficient heating and cooling systems, properly sized utilities, and storage solutions that transform compact footprints into comfortable living environments.
Cabins represent a more substantial portable dwelling option that we regularly construct for property developers. These structures typically incorporate porches, larger windows, and architectural elements that enhance their aesthetic appeal while maintaining transportability. For vacation property developers, we often customize these buildings with specific amenities that align with the intended guest experience.
Specialty and Custom Structures
Beyond standard categories, we regularly construct specialized portable buildings based on specific client requirements. For commercial developers, this might include vendor booths, retail spaces, or temporary classrooms. Each implementation requires careful consideration of occupancy requirements, access points, and utility connections.
Custom builds allow us to address unique property challenges through tailored design solutions. When conventional portable options fall short, we work with property owners to develop hybrid structures incorporating elements from multiple portable building types. These projects typically involve collaborative planning sessions where we map specific needs to construction methodologies, ensuring optimal functionality within the constraints of portable building frameworks.
What’s the Difference Between Relocatable Buildings and Permanent Modular Construction?
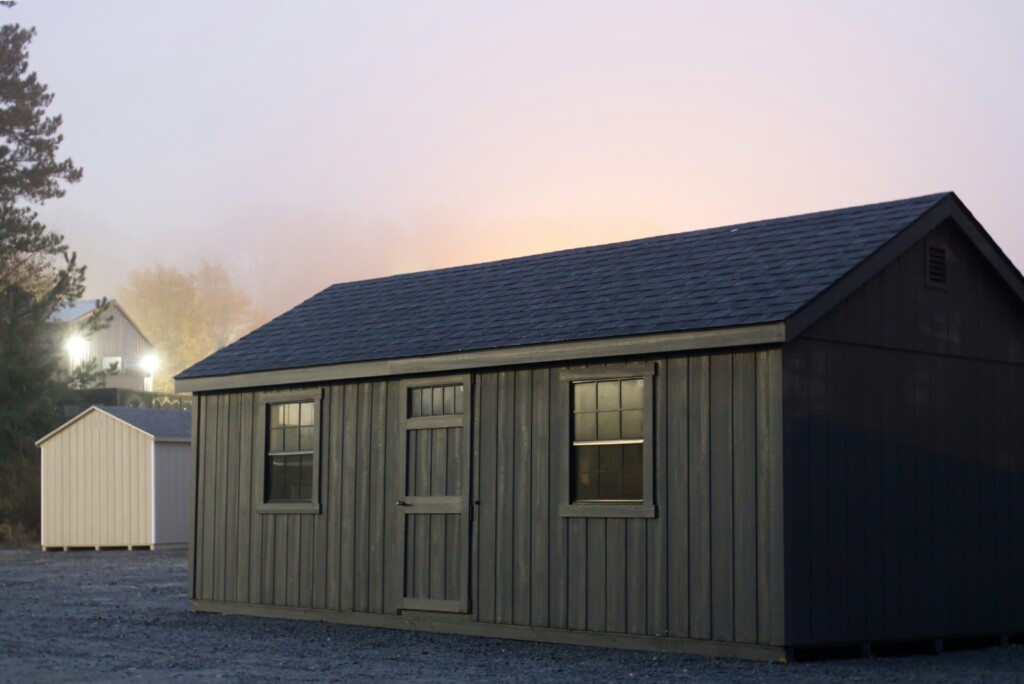
On construction sites across the country, there is a growing demand for modular solutions that offer efficiency without compromising quality. While both relocatable buildings and permanent modular construction use factory-based assembly processes, they serve fundamentally different purposes in project planning. Understanding these differences helps deliver the right solution for each client’s specific needs.
Duration and Purpose
Permanent modular construction (PMC) involves creating structures designed for long-term occupation at a fixed location. These buildings match or exceed the durability of traditional construction and can remain functional for over 60 years. The finished product is virtually indistinguishable from conventional construction to the end user.
In contrast, relocatable buildings provide a solution specifically engineered for temporary use and multiple relocations. These portable structures maintain their structural integrity through several moves between different sites, making them ideal for construction offices, temporary classrooms, or medical clinics during renovations.
Materials and Construction Methods
Permanent modular projects typically incorporate wood, steel, and concrete—the same materials used in conventional construction. These modules are designed to withstand decades of use, with the same load-bearing requirements and structural stability as traditionally-built structures.
For relocatable buildings, lightweight yet durable materials (predominantly wood) are prioritized to facilitate easier transportation and reinstallation. The construction methodology focuses on ensuring each module can withstand the stresses of being lifted, transported, and repositioned multiple times without compromising safety or functionality.
Foundation and Installation Requirements
Installing permanent modular buildings involves establishing proper foundations identical to traditional construction—concrete slabs, crawl spaces, or full basements. These foundations anchor the structure permanently to its location, creating the stability needed for long-term occupancy.
For relocatable buildings, simplified foundation systems designed for temporary placement are typically used. The installation process emphasizes efficiency and minimizes ground disturbance, allowing for quicker setup and easier removal when the building needs to be moved.
Design Flexibility and Customization
Permanent modular projects offer extensive design flexibility. While plans must be finalized before manufacturing begins, virtually any architectural style or layout can be created, including multi-story buildings with elevators, specialized rooms, and complex mechanical systems. The finished buildings comply with the same building codes as conventional construction.
Relocatable buildings offer more limited design options but excel in standardization and rapid deployment. These structures can be delivered to the site within weeks rather than months, though customization options are typically more constrained. Despite these limitations, all relocatable buildings meet or exceed relevant building codes for their intended use.
The choice between these construction methods ultimately depends on the project timeline, budget constraints, and long-term plans for the space. Both approaches offer significant advantages over conventional construction, including reduced waste, controlled manufacturing environments, and accelerated project timelines—allowing for the delivery of quality solutions more efficiently regardless of which modular approach best fits the client’s needs.
What Are the Key Benefits of Choosing Portable Buildings?
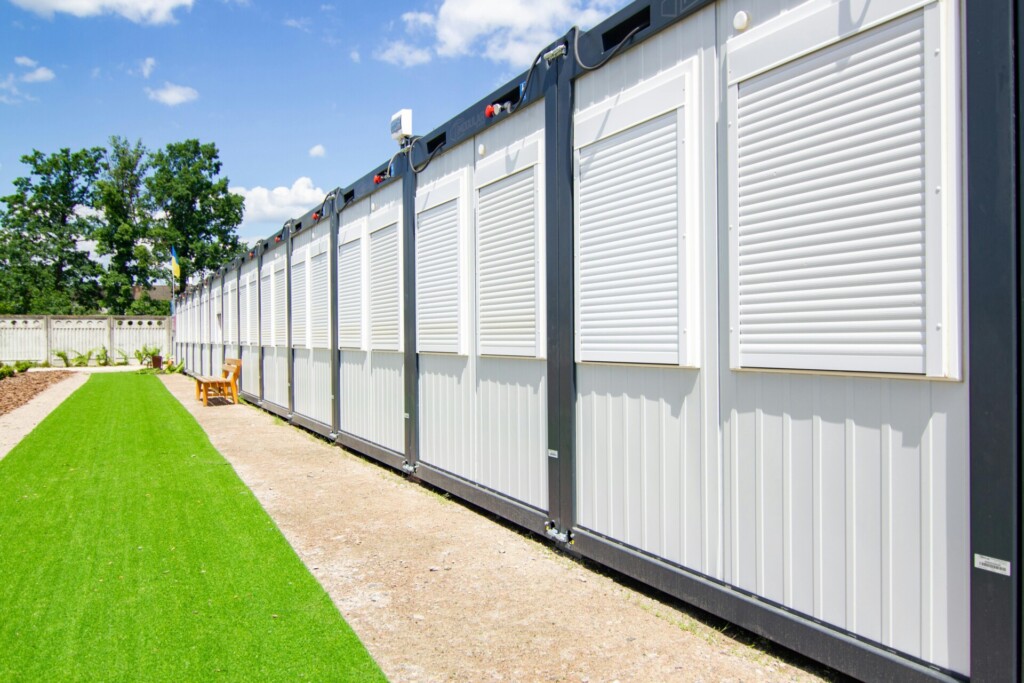
When developers and property owners need flexible space solutions, portable buildings offer significant advantages over conventional construction. These structures become valuable assets across various development projects, providing benefits that traditional buildings cannot match.
Exceptional Flexibility and Mobility
The main advantage of portable buildings is their inherent mobility. These structures can be relocated as property needs evolve, making them ideal for phased development projects or sites where permanent construction isn’t feasible. The 2023 industry shift toward more adaptable space solutions has enhanced this benefit.
Our construction teams can efficiently reposition, expand, or reconfigure these buildings without the demolition and reconstruction costs required by traditional structures. This adaptability is especially valuable for developers managing multiple properties or dealing with changing space requirements throughout project lifecycles.
The modular design allows for quick scaling of space up or down as needed. We’ve implemented portable solutions for developers who provided temporary offices during main building renovations, later repurposing those structures for equipment storage.
Impressive Durability and Weather Resistance
Despite the “portable” designation, these buildings are built to last. They are constructed using high-quality materials specifically selected to withstand challenging weather conditions. The controlled manufacturing environment allows for precise construction techniques that often surpass the quality of traditional on-site building methods.
Through rigorous quality control processes, we ensure each building component meets strict durability standards. Modern portable structures feature advanced insulation, robust structural elements, and weather-resistant exteriors that maintain integrity over years of use. Properly maintained portable buildings typically provide 20+ years of reliable service.
Recent advancements in materials science have dramatically improved portable building durability. The corrugated metal panels now used offer superior resistance to moisture, UV damage, and temperature fluctuations compared to earlier generations of portable structures.
Cost-Effectiveness That Improves Your Bottom Line
The financial advantages of portable buildings make them particularly attractive in today’s construction market. Portable building projects are typically completed in 30-50% less time than conventional construction, significantly reducing labor costs and allowing for faster occupancy. This accelerated timeline translates directly to improved ROI for property developers.
The assembly-line manufacturing approach minimizes material waste while maximizing efficiency. Our precise construction processes typically result in 15-20% material savings compared to traditional on-site building methods. These efficiencies extend beyond initial construction—portable buildings generally require less maintenance and offer excellent energy performance through superior insulation and modern HVAC systems.
Perhaps most valuable is the predictable pricing model. When we provide a quote for a portable building project, that price remains stable throughout construction. This eliminates the unpleasant budget surprises that frequently plague conventional construction projects, where unexpected site conditions or material price fluctuations can drive substantial cost overruns.
Sustainability Benefits and Environmental Considerations
As construction sustainability becomes increasingly important to stakeholders, portable buildings offer significant environmental advantages. These structures are built in controlled factory environments that optimize resource usage while minimizing waste. The manufacturing precision results in buildings with excellent thermal performance, reducing long-term energy consumption and associated climate impact.
The modular design philosophy grants these buildings extended usability. Rather than demolishing and disposing of traditional structures, portable buildings can be disassembled and repurposed for future projects. This approach dramatically reduces construction waste while conserving valuable materials and embedded energy.
Site impact represents another key environmental benefit. Our installation processes require minimal ground disturbance compared to traditional foundation systems. This preservation of existing site conditions is particularly valuable for environmentally sensitive areas or projects with strict site impact limitations.
For developers seeking to enhance their sustainability credentials, portable buildings offer a compelling narrative. The reduced carbon footprint, material efficiency, and adaptability align perfectly with modern environmental, social, and governance (ESG) objectives that increasingly influence development decisions.
Conclusion: Making the Right Choice for Your Portable Building Needs
Portable buildings offer exceptional versatility and value when selected with your specific requirements in mind. These structures serve countless purposes—from basic storage solutions to fully functional workspaces—while offering advantages traditional construction simply can’t match. The key lies in a deliberate assessment of your needs, space constraints, and long-term objectives. When we guide clients through this decision-making process, we emphasize that budget expectations must align with desired features, ensuring satisfaction with both immediate functionality and sustained performance.
The portable building market continues to evolve with improved materials, energy efficiency features, and customization options, making these structures increasingly practical for diverse applications. By evaluating factors like site preparation requirements, local building codes, and aesthetic considerations alongside your primary purpose and budget constraints, you position yourself to make a choice that delivers lasting value. We’ve found that the most successful portable building projects begin with this comprehensive approach to selection—balancing immediate needs with future adaptability while maintaining a focus on quality construction that withstands the test of time.
Ready to explore portable building solutions tailored to your specific requirements? Contact EB3 Construction today.