Building a home in today’s market involves a significant investment. According to recent data, the national average cost to construct a house is approximately $329,000, not including land costs. This figure is just the starting point in a broad investment spectrum.
Construction costs can vary greatly based on numerous factors affecting projects. Modest builds can start around $42,000 for basic structures, while premium custom homes may exceed $900,000 for clients seeking unique designs and high-end finishes. This range highlights the highly customizable nature of home construction that we explore with our clients.
When analyzing costs per square foot, the national average is about $150. However, this figure can vary significantly by region, with metropolitan areas demanding higher rates than rural locations. For a standard 2,000-square-foot home, we typically budget between $201,000 and $310,000 for construction costs, although regional material availability, labor markets, and supply chain conditions continue to impact these numbers in real-time.
How Does House Size and Layout Affect Building Costs?
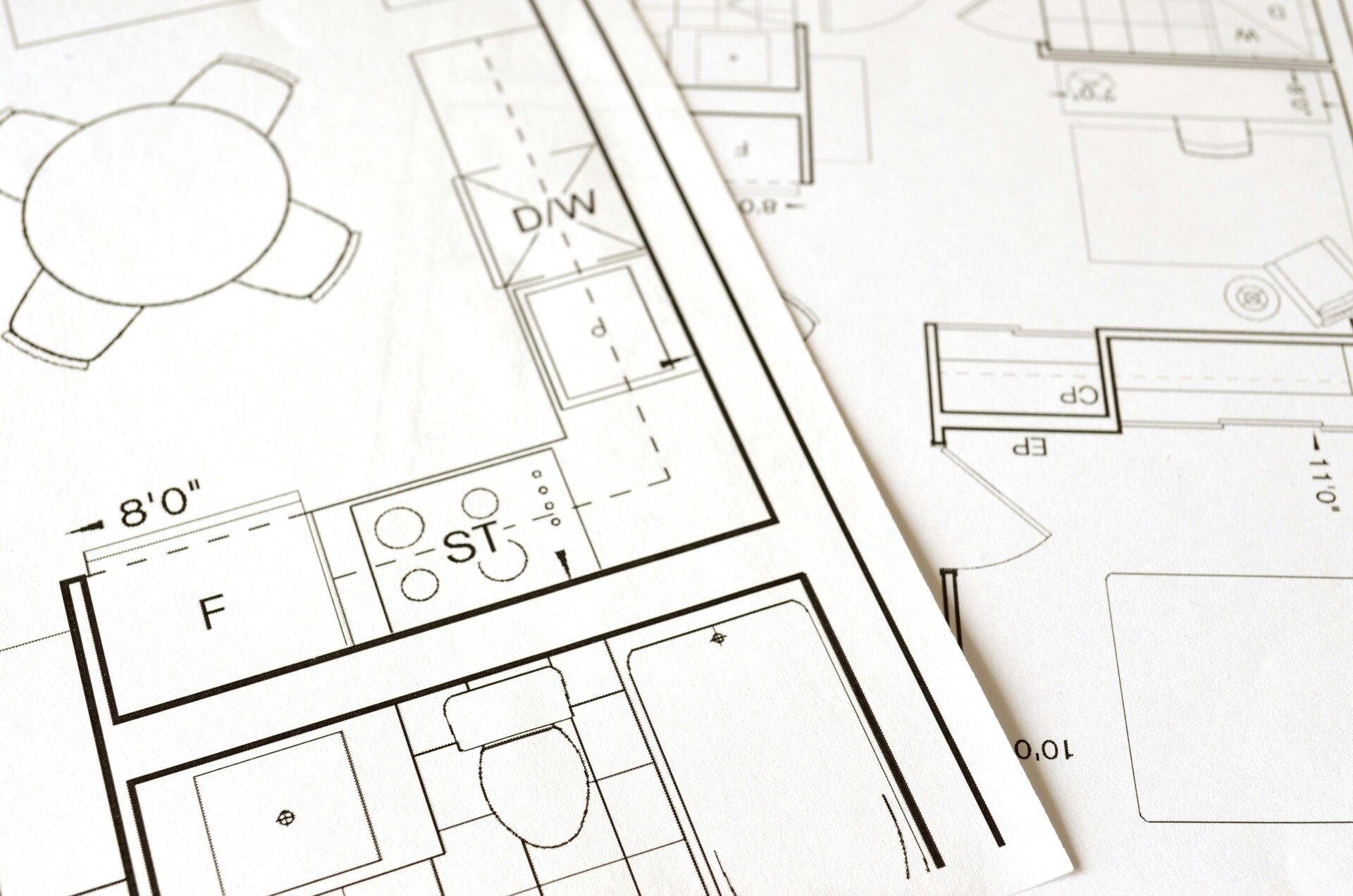
When we build homes for our clients, square footage consistently emerges as a primary cost driver. We’ve observed that every additional room in a floor plan increases the home’s overall size, directly impacting material requirements, labor hours, and ultimately, the bottom line. This relationship between space and cost follows a predictable pattern that helps our clients make informed decisions early in the development process.
The bedroom count serves as a reliable indicator of overall home size and cost. A 2-bedroom house, typically ranging between 800-1,500 square feet, costs around $122,000 for us to construct. Moving up to a 3-bedroom home (1,000-2,500 sq ft) substantially increases the price range to between $147,000 and $310,000, reflecting both the additional square footage and the complexity of accommodating more living spaces.
Impact of Layout Complexity on Construction Costs
We find that layout complexity often influences costs as significantly as raw square footage. Homes with intricate designs featuring angled walls, multiple hallways, or bay windows require more custom framing and finishing work. These design elements demand additional materials and specialized labor, driving up costs compared to simpler, more rectangular layouts.
When we develop construction plans for larger homes, we carefully consider how spatial arrangements affect budgets. Four-bedroom homes (1,900-2,600 sq ft) generally cost approximately $285,000 to build, while 5-bedroom properties (2,500-3,500 sq ft) can reach $375,000 or more. The price increase isn’t merely proportional to the added square footage—larger homes often incorporate more high-end finishes and complex mechanical systems that compound costs.
Number of Bedrooms | Typical Home Size (sq ft) | Average Cost |
---|---|---|
2 | 800 – 1,500 | $122,000 |
3 | 1,000 – 2,500 | $147,000 |
4 | 1,900 – 2,600 | $285,000 |
5 | 2,500 – 3,500 | $375,000 |
Strategic Design Approaches to Control Costs
We frequently advise our development partners that building upward instead of outward can meaningfully reduce costs. Multi-story construction decreases a home’s footprint, which directly translates to savings on foundation work, roofing materials, and land use. A smaller foundation requires less concrete, excavation, and waterproofing—all substantial line items in any construction budget.
When we optimize layout efficiency, we look beyond bedroom count to consider overall circulation space. Hallways and transitional areas add to square footage without providing livable space. By designing homes with efficient traffic patterns and multifunctional rooms, we can reduce the total square footage while maintaining the spaciousness clients desire.
Local market conditions also influence how size and layout decisions affect final costs. In high-demand areas where land values have surged (reaching up to $150,000 in some markets as of 2022), maximizing the efficiency of each square foot becomes even more critical. We help our clients balance spatial needs with budgetary constraints by presenting clear cost implications for various design choices.
What Are the Pre-Construction and Exterior Costs?
Starting a new construction project requires a significant upfront investment even before the physical building begins. At EB3 Construction, we have guided many developers and property owners through these initial phases, helping them understand and budget for both pre-construction and exterior expenses, which are crucial for any successful project.
Pre-Construction Expenses: The Critical First Steps
Pre-construction costs typically account for 1-3% of your total project budget but play a crucial role in determining project success. These preliminary expenses set the foundation for everything that follows.
Land acquisition is your most significant pre-construction investment. Plot prices vary dramatically from $3,000 to $150,000 per acre, depending on location, zoning, and development potential. Urban and suburban infill lots in high-demand markets command premium prices, while rural parcels offer more affordable entry points.
Professional services form another substantial pre-construction cost category. Architectural plans range from $500 for stock designs to over $20,000 for custom drawings that maximize site potential and meet specific usage requirements. Construction management fees typically range between $3,000 and $52,000, depending on project complexity and scope—a worthwhile investment that helps prevent costly mistakes during execution.
Regulatory compliance costs are unavoidable but necessary investments. Building permits average $1,200 to $2,000 in most municipalities, though this can increase in highly regulated markets or for specialized construction types. Impact fees, environmental assessments, and water/sewer inspections (approximately $8,400) ensure your project meets all legal requirements before breaking ground.
Proper site evaluation prevents unexpected challenges during construction. We conduct thorough boundary surveys (average $500), soil testing, environmental assessments, and utility location mapping to identify potential obstacles early. These evaluations help us develop accurate construction timelines and budgets tailored to your specific site conditions.
Component | Cost Range |
Land Acquisition | $3,000 to $150,000 per acre |
Architectural Plans | $500 to $20,000+ |
Construction Management Fees | $3,000 to $52,000 |
Building Permits | $1,200 to $2,000 |
Impact Fees, Environmental Assessments, Water/Sewer Inspections | Approximately $8,400 |
Boundary Surveys | $500 average |
Exterior Building Costs: Creating the Structural Envelope
Once pre-construction hurdles are cleared, exterior construction begins with site preparation. Excavation costs range from $1,400 to $5,400, depending on site complexity, soil conditions, and the amount of vegetation clearing required. For sites with significant tree removal or demolition needs, these costs can easily reach $15,000 or more.
Foundation work represents the project’s literal and figurative bedrock. A standard 2,000-square-foot foundation averages $8,900, though prices vary based on foundation type and soil conditions. Slab-on-grade foundations cost $5-$16 per square foot, while basement foundations run $20-$37 per square foot due to additional excavation, soil preparation, and concrete requirements.
Structural framing constitutes the largest exterior expense, typically running between $20,000 and $50,000 for a mid-sized commercial structure. This critical phase includes lumber, steel supports, roof trusses, and labor costs. Current material market conditions significantly impact these figures—we monitor commodity prices closely to help clients optimize purchases.
Building envelope components complete the exterior structure. Roofing systems average $8,500 for standard materials but can exceed $25,000 for high-performance or specialized applications. Exterior siding costs range from $2 per square foot for basic vinyl to $9+ for premium fiber cement or architectural metal panels. These envelope systems must balance aesthetic appeal with durability and weather resistance.
Site integration elements finalize the exterior costs. Driveway installation averages $4,400 for standard paved surfaces, with prices varying based on length, width, and material selection. Initial landscaping packages start around $8,200 and can represent significant value when thoughtfully integrated with stormwater management systems and building aesthetics.
Regional Variations and Market Factors
Construction costs vary significantly by region. The Pacific region typically sees costs 11% above national averages, while the East South Atlantic region runs about 5% below average. These variations reflect differences in labor costs, material availability, building code requirements, and climatic design considerations.
Market timing can substantially impact your project budget. Seasonal construction patterns, economic cycles, and global supply chain dynamics all influence material and labor pricing. We help clients navigate these variables by timing purchases strategically and locking in favorable contract terms when possible.
We approach each project by analyzing these pre-construction and exterior costs within your specific context. Rather than simply accepting industry averages, we develop detailed project-specific estimates that account for your site conditions, design requirements, and business objectives. This tailored approach helps prevent budget surprises and ensures every dollar is strategically allocated.
What Are the Interior Material and Labor Costs?
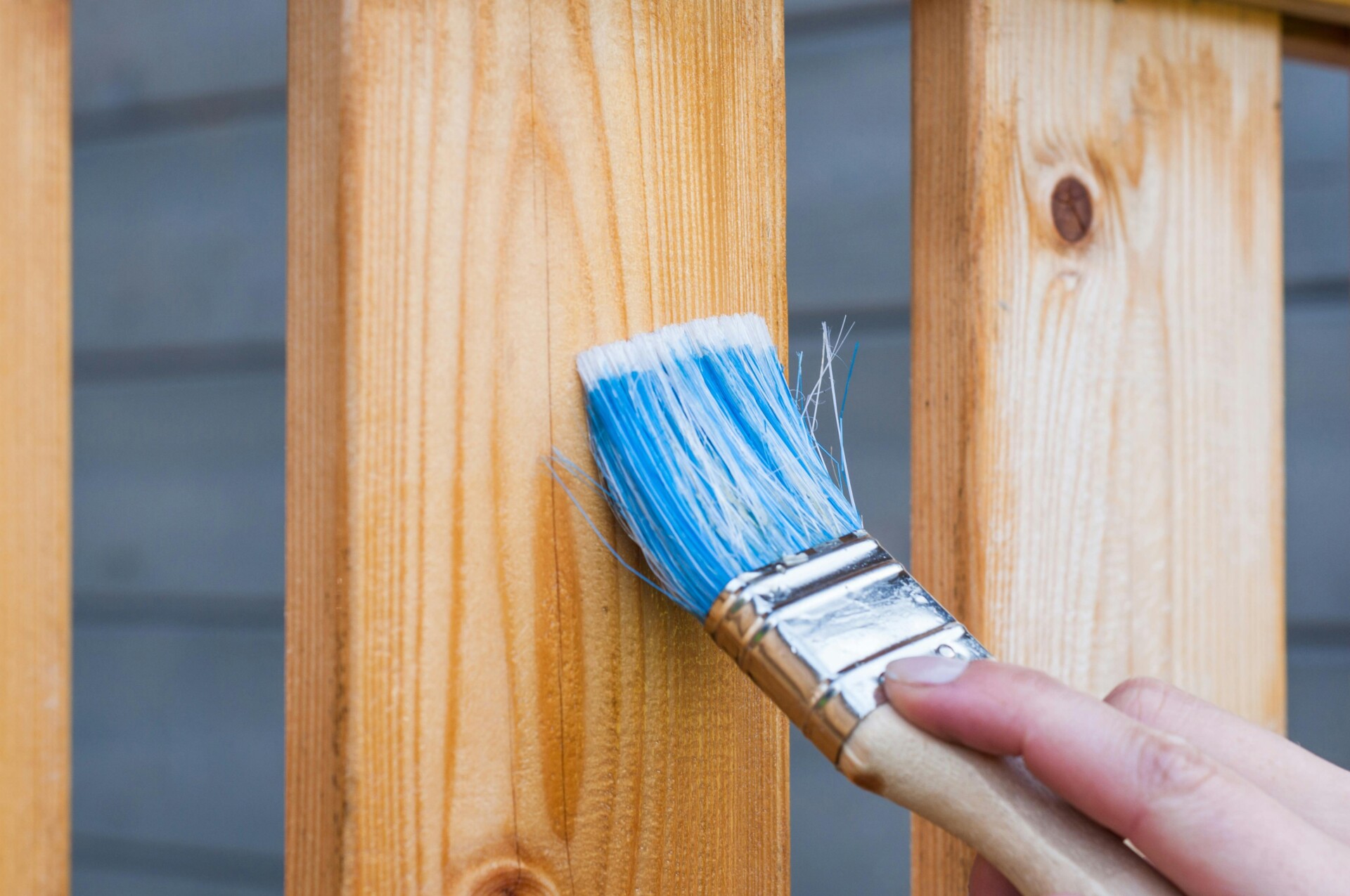
Interior systems form the backbone of a functional home, representing a substantial portion of any construction budget. As general contractors, we have observed that these elements make up nearly 40% of total construction expenses. Understanding these costs helps developers and property owners make informed decisions early in the planning process.
Major Building Systems
HVAC, plumbing, and electrical systems form the essential infrastructure of any modern building. Each system typically costs around $27,000 for new construction, with the three combined averaging $82,319 for an average new home. These systems require both specialized materials and skilled labor.
HVAC installation ranges from $5,000 for basic systems to $34,000 for high-efficiency zoned solutions. Plumbing costs vary from $1,500 for simple layouts to $17,500 for homes with multiple bathrooms or specialized fixtures. Electrical work averages between $7,000 and $13,000 depending on complexity and fixture requirements.
When coordinating these systems, we sequence installation carefully to avoid costly rework. Rough-ins must be completed before drywall installation, with each trade requiring careful coordination to prevent conflicts between ductwork, piping, and wiring paths.
Cost Category | Materials | Labor |
---|---|---|
HVAC | $5,000 – $34,000 | Specialized labor required |
Plumbing | $1,500 – $17,500 | Specialized labor required |
Electrical | $7,000 – $13,000 | Specialized labor required |
Interior Finishes | $103,391 average | Labor accounts for 39% of costs |
Interior Finishes
Interior finishes represent the most substantial portion of interior costs, averaging $103,391 for new construction. These elements include insulation, drywall, paint, flooring, cabinets, countertops, and various fixtures that transform a shell into a livable space.
Insulation costs between $3,000 and $10,000 depending on the R-value requirements and materials chosen. Drywall installation averages $15,550 for an average-sized home, while painting ranges widely from $300 for DIY applications to $28,000 for premium finishes with specialized techniques. Flooring averages $10,250 but can vary dramatically based on material selection—vinyl and carpet representing more economical options compared to hardwood or stone tile.
Cabinets and countertops represent a particularly significant expense at approximately $11,800 for standard installations, though premium custom cabinetry can push this figure much higher. In fact, cabinetry alone typically accounts for nearly $20,000 in new home construction, making it one of the largest line items in interior finishes.
Labor vs. Material Costs
Labor costs typically account for about 50% of total construction expenses—a remarkably high ratio compared to manufacturing industries where labor might represent only 10-20% of costs. This labor-intensive nature explains why construction costs have not declined significantly despite technological advances.
For interior work specifically, labor accounts for approximately 39% of costs, averaging about $34 per square foot. In a typical 2,776-square-foot home, this translates to around $68,000 in labor expenses. The ratio of labor to materials varies significantly by trade—painting and framing have labor components as high as 60-70%, while factory-made items like appliances and fixtures require only 10-20% labor for installation.
Interestingly, despite the evolution of power tools over the decades, the proportional cost of labor has not changed dramatically since the 1940s. While modern tools have increased worker productivity, rising labor rates have largely offset these efficiency gains, keeping the overall labor fraction relatively stable over time.
Managing Cost Variables
Several factors influence interior costs beyond the basic calculations. Regional labor rates create significant variations—metropolitan areas with strong unions typically command higher wages than rural locations. Material quality and availability also impact pricing, with supply chain disruptions potentially causing substantial price fluctuations.
When developing project budgets, we establish allowances for finish materials that balance quality with cost objectives. We have found that clearly defining these allowances early helps prevent budget overruns when selections are made. For developers building spec homes, understanding the target market’s expectations regarding finish quality is essential for right-sizing these allowances.
Finding the optimal balance between upfront investments and long-term performance often yields the best results. High-quality mechanical systems may cost more initially but reduce maintenance costs and improve building performance over time. Similarly, durable interior finishes can reduce replacement cycles and maintain property value more effectively than budget alternatives.
How Can You Save Money When Building a House?
Building a new home represents a significant financial investment. At EB3 Construction, we have guided many developers and property owners through maximizing their construction budgets without compromising quality. The current lumber market volatility following pandemic-era price swings has increased the need for strategic cost management.
Opt for Stock House Plans Over Custom Designs
We frequently recommend stock house plans as a straightforward way to reduce expenses. These pre-designed blueprints typically cost around $500, compared to custom architectural services that can range from $10,000 to $30,000. The math speaks for itself—why reinvent the wheel?
Stock plans don’t mean cookie-cutter results. Many offer limited customization options for an additional fee, allowing us to adapt the design to meet your specific requirements while maintaining cost efficiency. The U.S. Department of Housing and Urban Development notes that using stock plans can reduce the design phase from months to weeks—saving both time and money.
With stock plans, the initial design costs are distributed across multiple buyers rather than a single client. We can help select plans featuring standard-sized windows and doors to avoid costly customization premiums during construction.
Consider Prefabricated and Modular Options
Prefabricated and modular construction offers 25-35% savings compared to traditional builds. These factory-built components arrive ready for assembly, reducing on-site labor hours and material waste. We have successfully integrated these methods for clients seeking both efficiency and sustainability.
The controlled manufacturing environment eliminates weather delays and ensures consistent quality control. When we implement modular construction, we effectively compress the building schedule, which directly translates to lower carrying costs for financing, site supervision, and temporary utilities.
For multi-unit developments especially, the repeatable nature of prefab components creates economies of scale that conventional construction methods cannot match. We coordinate delivery schedules precisely with site preparation to minimize storage requirements and protect materials from exposure.
Build Smart and Vertical
We advise clients to build upward rather than outward whenever possible. Two-story designs require less foundation work and roofing—two substantial cost centers in any construction project. The reduced footprint also means less sitework, fewer utility runs, and more economical foundation systems.
When we develop construction strategies, we analyze the cost-per-square-foot implications of different layouts. Compact, efficient floor plans minimize hallways and circulation space while maximizing usable square footage. Simple rectangular footprints require fewer complex corners and connections than elaborate shapes with multiple bump-outs.
For foundations specifically, we evaluate whether pier systems might be more cost-effective than full perimeter foundations depending on soil conditions and structural requirements. These decisions made early in the planning process yield significant savings throughout construction.
Plan for Contingencies and Smart Purchasing
Our experience in construction management has taught us the importance of budgeting at least 20% extra for unexpected expenses. Supply chain disruptions, material price fluctuations, and unforeseen site conditions are realities we help clients anticipate and navigate.
We leverage our industry relationships and buying power for material procurement advantages. For substantial purchases like appliances, fixtures, and flooring, we track sales cycles and inventory closeouts. Comparison shopping and timing purchases strategically can yield significant savings on big-ticket items.
When managing timelines, we sequence trades to minimize downtime and avoid rush charges. Creating detailed schedules and communicating clearly with all subcontractors prevents costly mistakes and rework. These project management efficiencies might seem small individually, but collectively they can substantially reduce overall construction costs.
Conclusion: Balancing Budget and Vision When Building Your Home
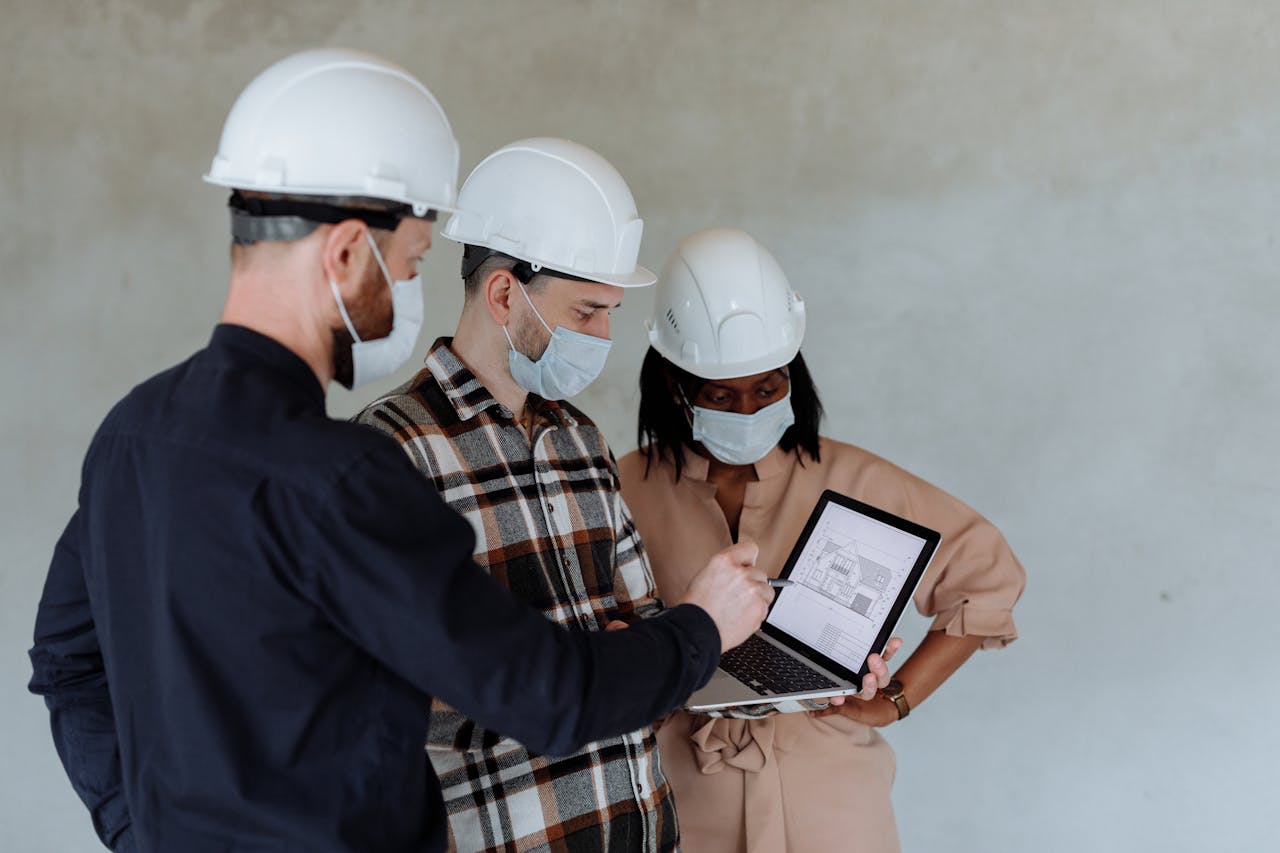
Throughout a construction project, the tension between aspiration and financial reality is constant. We’ve seen many clients grapple with this challenge—aligning their desires with their budget. The good news? With proper planning and realistic expectations, this balance is entirely achievable.
When collaborating with developers and property owners, we emphasize that successful projects aren’t about unlimited budgets but strategic allocation. Setting clear priorities from the start, establishing a comprehensive contingency fund (we typically recommend 20% for new builds), and conducting regular budget reviews create a framework for controlled execution. The national average cost of $329,000 for home construction provides a starting point, but we always prepare clients for variables such as location premiums, material selections, and scope decisions that affect final costs. The most successful projects we manage aren’t necessarily those with the highest budgets, but those with the most thoughtful resource distribution aligned with clear priorities.
Ready to transform your construction vision into reality while maintaining financial discipline? Contact EB3 Construction to discuss your project goals.