Concrete building represents the backbone of commercial development. As property owners and developers navigate the complexities of bringing architectural visions to reality, concrete structures form the literal foundation upon which successful projects stand. This essential building material defines the skyline and infrastructure throughout the metroplex, offering both structural integrity and design versatility.
At EB3 Construction, we transform raw commercial spaces into functional environments tailored to precise operational requirements. Our team coordinates every aspect of concrete construction from initial site preparation through final finishing, managing the intricate dance of formwork, reinforcement, and pour scheduling that concrete building demands.
Recently, rising material costs and supply chain fluctuations have made our expertise in procurement scheduling and value engineering particularly valuable to developers watching bottom lines.
Innovation and Evolution in Dallas Residential Construction
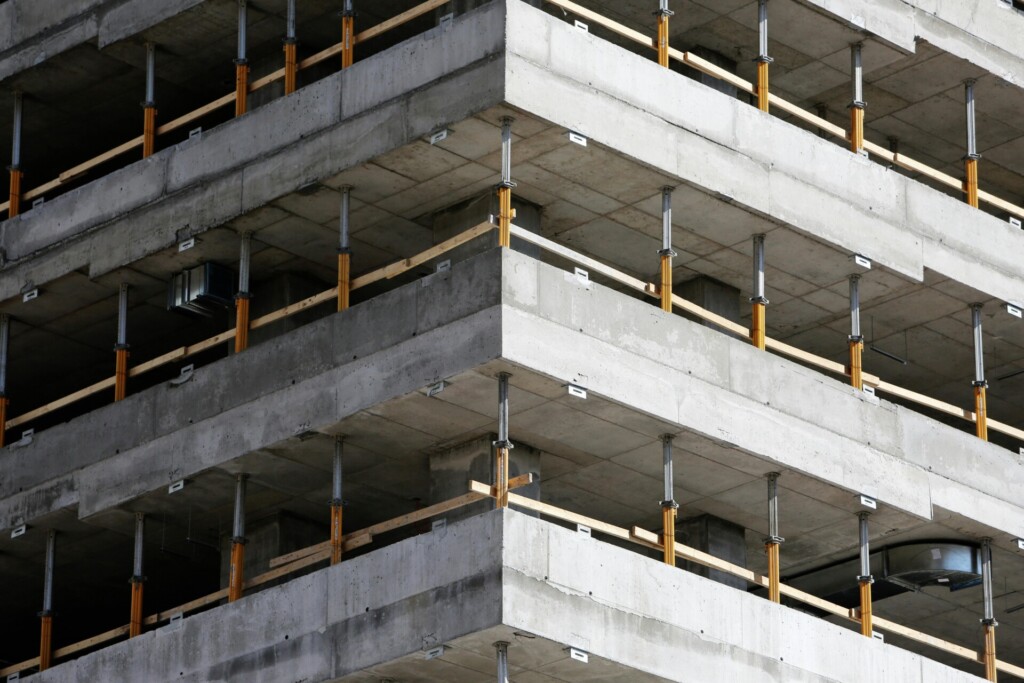
Our concrete portfolio in Dallas spans from intimate residential structures to large-scale commercial developments, showcasing our versatility in handling projects of all sizes. The unique Dallas climate, with its extreme temperature fluctuations and clay-heavy soils, presents specific challenges for concrete construction that we’ve mastered through years of local experience.
Our comprehensive approach encompasses everything from initial concrete formwork to final finishing, ensuring structural integrity and aesthetic appeal.
Residential Concrete Excellence
Residential concrete work demands precision beyond just structural considerations. We coordinate every aspect of the concrete process—from securing proper concrete mix designs that withstand Dallas’s freeze-thaw cycles to scheduling pours around optimal weather conditions. The finished product delivers both the structural durability and aesthetic finish that homeowners expect from premium residential construction.
Urban homes present unique concrete challenges, particularly in Dallas neighborhoods where space constraints require creative solutions. Our residential concrete expertise includes foundation systems, decorative concrete features, driveways, and specialty applications like concrete retaining walls that maximize usable space on sloped lots. Each project benefits from our meticulous attention to concrete curing procedures, critical for preventing the cracking and deterioration common in North Texas conditions.
Commercial and Multifamily Concrete Construction
Commercial concrete construction requires sophisticated planning and execution. We manage the logistics of large-scale concrete deliveries in congested urban environments, coordinate complex concrete pours that must often occur during overnight hours to minimize disruption, and implement rigorous quality control procedures to verify concrete strength and durability. This comprehensive approach ensures our commercial structures meet both current needs and long-term performance requirements.
Multifamily projects bring additional concrete considerations beyond scale. We incorporate sound attenuation between units, design concrete structures that accommodate complex mechanical systems, and implement waterproofing measures for below-grade concrete elements. These technical aspects of concrete construction often go unseen but represent critical components of successful multifamily developments. The coordination between structural concrete requirements and architectural design intent remains a particular strength in our multifamily portfolio.
Concrete Specialties and Techniques
Beyond basic structural applications, we’ve developed expertise in specialized concrete techniques that add value to Dallas properties. Post-tensioned concrete slabs provide superior performance on the region’s expansive soils, while exposed aggregate finishes deliver distinctive aesthetic appeal for exterior concrete surfaces. Our concrete craftsmen execute detailed architectural concrete features that serve both functional and design purposes across our projects.
Winter construction in Dallas presents unique challenges for concrete work. When the temperature drops below 50°F, we implement concrete warming techniques—including heated enclosures and concrete additives—to ensure proper curing despite cold conditions. Conversely, summer concrete pours require careful timing and specialized concrete mixes to prevent rapid evaporation and strength loss during Dallas’s intense heat.
The evolution of concrete technology continues to enhance our project capabilities. We regularly incorporate fiber-reinforced concrete for improved crack resistance, self-consolidating concrete for complex formwork applications, and high-early-strength concrete when accelerated construction schedules demand rapid strength development. These advanced concrete solutions allow us to overcome site-specific challenges while maintaining quality standards.
From foundation to finish, our concrete expertise enables us to deliver exceptional results across diverse project types. Whether addressing the unique requirements of a custom residence or managing the complex concrete components of commercial development, we bring the same commitment to quality craftsmanship and technical precision. This consistent approach has established our reputation for concrete excellence throughout the Dallas construction market.
What Construction Methods and Standards are Used for Concrete Buildings?
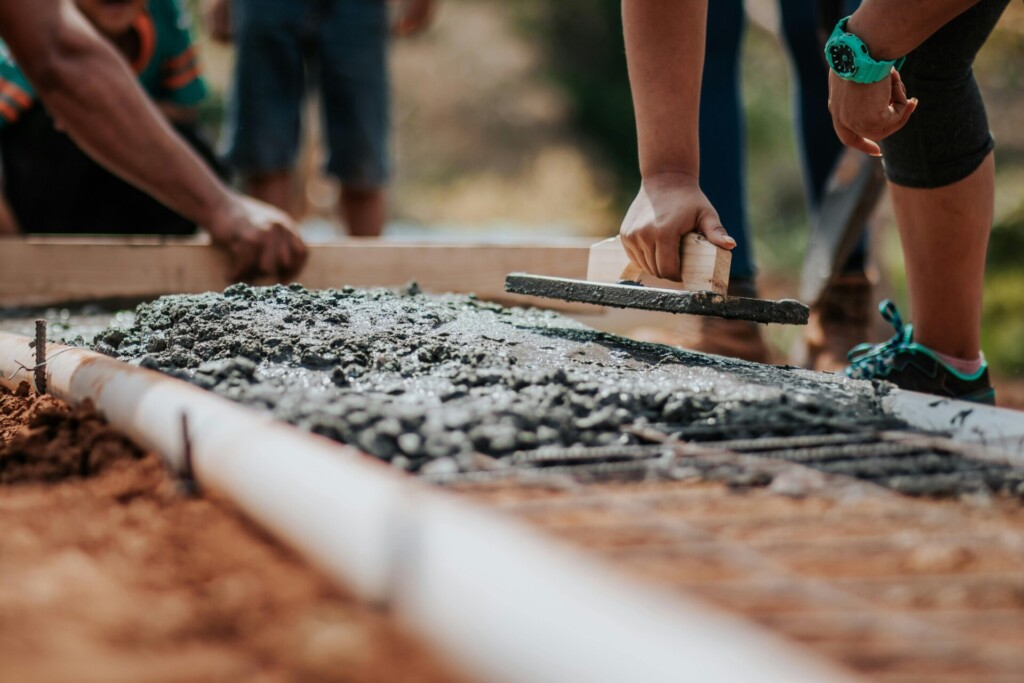
At EB3 Construction, we implement rigorous concrete building standards across our Dallas projects, ensuring each structure we deliver combines durability, safety, and precision. Our concrete construction methods are grounded in Type VA construction specifications, which establish the framework for fire-resistant properties while maximizing structural integrity. This classification requires specific wall assemblies, floor systems, and material compositions that our teams meticulously follow through every phase of construction.
When approaching concrete work, we begin with comprehensive soil analysis to determine the appropriate foundation system. Dallas’s varied terrain presents unique challenges, from expansive clay soils in northern areas to limestone formations in western sectors. These geological factors influence our decisions on foundation depth, reinforcement configuration, and concrete mix specifications. Rather than applying one-size-fits-all solutions, we customize our approach to each site’s specific conditions.
Concrete Production and Quality Control
We carefully select concrete production methods based on project requirements and structural demands. For components requiring exceptional surface finish and architectural detail, we utilize wet-cast methods that allow for complex shapes and smooth surfaces. When durability and immediate stripping are priorities, we employ dry-cast techniques that create exceptionally dense concrete with superior compressive strength. This methodical selection process ensures the right application of materials for each project element.
Quality control remains central to our concrete operations. Unlike traditional on-site pouring that can be compromised by weather variables, we implement rigorous inspection protocols throughout concrete preparation and placement. Our teams monitor concrete temperature during pouring—a critical factor in Dallas’s climate where summer heat can accelerate setting time and affect strength development. We also maintain strict water-cement ratios to achieve specified compressive strengths that typically range from 3,000 to 5,000 PSI depending on structural requirements.
Code Compliance and Safety Standards
Our concrete structures comply with all Dallas building regulations, which have adopted the International Building Code with local amendments. We work directly with the Dallas Building Inspection Division at key project milestones to verify compliance with structural standards. This close coordination with regulatory authorities ensures that our concrete installations meet or exceed all local requirements for structural integrity, fire resistance, and occupant safety.
Fire safety forms an integral component of our concrete building systems. Depending on building size, occupancy classification, and usage requirements, we incorporate NFPA13 or NFPA13R sprinkler systems throughout our structures. These systems complement the inherent fire-resistant properties of concrete construction to create comprehensive protection for building occupants. Our concrete floor assemblies typically achieve fire ratings between one and two hours, providing crucial time for evacuation during emergency situations.
Innovative Techniques and Sustainable Practices
Beyond standard practices, we’ve adopted innovative concrete construction techniques that enhance building performance. For projects requiring accelerated schedules, we utilize precast concrete elements manufactured off-site under controlled conditions. This approach allows for parallel workflows where site preparation progresses while concrete components are simultaneously being produced, reducing overall project timelines by up to 20-30% compared to traditional methods.
Sustainability guides our concrete practices as well. We incorporate recycled materials where structurally appropriate and implement specialized concrete mixes that reduce environmental impact without sacrificing performance. The precision of our production methods substantially reduces material waste—typically lowering concrete consumption by 5-10% compared to field-poured methods through optimized design and forming systems.
When implementing prestressed concrete methods, we create components with enhanced load-bearing capacity ideal for spanning long distances or handling heavy loads. This specialized technique involves stretching high-strength steel tendons within concrete forms before casting, creating built-in compression forces that significantly improve structural performance. The result is longer spans with less material—an efficiency that benefits both project economics and architectural flexibility.
Quality Assurance Through Expert Coordination
Our trade partner prequalification process ensures we work with concrete specialists who meet our exacting standards. We evaluate subcontractors based on their financial stability, safety records, quality standards, and Dallas-specific experience. This rigorous vetting creates a team aligned with our commitment to excellence in concrete construction.
Throughout concrete placement, our site teams maintain constant vigilance on critical factors that affect quality. We utilize mechanical vibration techniques to eliminate air pockets and ensure complete consolidation around reinforcement. This creates exceptionally dense, strong components that significantly outperform alternatives with inconsistent consolidation. After placement, we implement proper curing protocols that protect concrete during its critical early strength development period.
From foundation to finish, our concrete building methods reflect a commitment to construction excellence that stands the test of time. By combining industry best practices, innovative techniques, and strict quality control, we deliver concrete structures that provide decades of reliable service while meeting the evolving needs of Dallas property owners and developers.
How Does EB3 Construction’s Business Structure Support Concrete Building Projects?
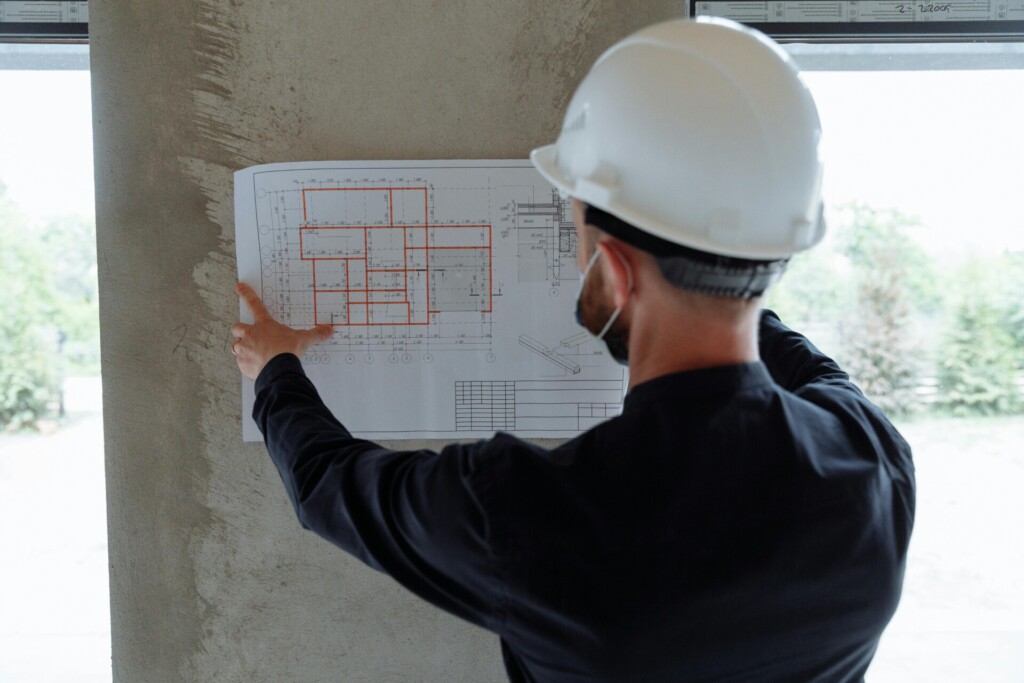
We’ve structured our business specifically to excel at concrete construction projects throughout Dallas. As a special trade contractor operating under 3939 Investment Group DBA EB3 Construction, our focused size and specialized expertise allow us to deliver exceptional results across diverse concrete building projects. Our team maintains the agility to respond quickly while having sufficient capacity to handle substantial commercial and residential concrete work.
Our business model centers on maintaining a core team of 5-10 construction professionals who bring specialized concrete expertise to every project. This right-sized approach means clients receive personalized attention from experienced builders rather than being lost in the shuffle of a massive corporate structure. Each project benefits from direct oversight by our leadership team, including owner Eldad Block, ensuring quality control throughout the construction process.
When managing concrete formwork on commercial projects, we leverage our established network of trade partners who specialize in structural applications. These strategic relationships, developed over years in the Dallas construction market, enable us to scale our concrete capabilities without sacrificing quality or exceeding budget constraints. We carefully prequalify these partners through a rigorous vetting process that evaluates their financial stability, safety records, and Dallas-specific experience.
Specialized Expertise in Concrete Applications
Our team excels in coordinating the complex requirements of concrete building projects from foundation to finish. We understand how Dallas’s variable soil conditions affect foundation design, requiring specialized knowledge of everything from pier-and-beam systems to monolithic slabs. This expertise proves particularly valuable when managing concrete pours during Texas’s extreme temperature fluctuations, where timing and technique directly impact structural integrity.
The technical demands of concrete construction require both practical experience and engineering knowledge. Our project managers collaborate closely with structural engineers to ensure concrete specifications are met precisely, whether managing standard foundations or complex tilt-wall commercial applications. This integrated approach prevents the costly miscommunications that often plague concrete projects where engineering intent doesn’t translate to field execution.
With annual sales between $5-10 million, we maintain the financial stability necessary to procure materials efficiently and manage cash flow throughout lengthy concrete projects. This financial foundation allows us to secure favorable pricing on concrete and rebar through established supplier relationships, ultimately delivering better value to our clients without compromising on material quality.
Scalable Project Management for Diverse Concrete Applications
Our business structure supports concrete projects ranging from custom residential foundations to large-scale commercial developments. We implement a systematic project management approach that scales appropriately to each project’s scope while maintaining consistent quality standards across all work. This flexibility allows us to serve diverse clients from individual property owners to commercial developers with equal attention to detail.
Communication remains central to our project management system. For concrete projects, which often involve critical sequencing and timing, we establish clear channels from estimating through completion. This transparent approach allows clients to understand exactly how their concrete elements are progressing, from reinforcement installation through finishing techniques that determine both structural integrity and aesthetic quality.
We’ve developed specialized internal processes to manage the unique challenges of concrete construction in Dallas. Our quality control protocols include extensive pre-pour checklists, regular strength testing, and dedicated inspections at critical phases. These systems ensure that each concrete element meets both structural requirements and client expectations before proceeding to subsequent construction phases.
Balancing Efficiency and Quality in Concrete Construction
Our focused business structure creates natural advantages when managing concrete projects. Unlike massive contractors that might prioritize volume over precision, our team size allows us to maintain meticulous oversight throughout concrete operations. This attention to detail proves particularly valuable during critical concrete pours where timing, temperature, and technique directly impact structural outcomes.
Resource allocation represents another strength of our business model. With a specialized team focused specifically on construction coordination, we efficiently deploy personnel and equipment to maintain momentum on concrete projects. This targeted approach eliminates the overhead inefficiencies common in larger organizations while ensuring concrete elements receive the expert attention they require at each phase.
Through strategic trade partner relationships, we maintain access to specialized concrete equipment without the capital burden of ownership. This approach allows us to deploy the right tools for each concrete application—from high-volume pumping systems for commercial slabs to specialized finishing equipment for decorative applications—while maintaining competitive pricing for our clients.
Our business structure reflects the practical realities of concrete construction in Dallas, where quality execution depends on both technical knowledge and hands-on experience. By maintaining a focused team with deep concrete expertise, we deliver exceptional results across diverse building projects throughout the region.
Conclusion: Choosing EB3 Construction for Concrete Building Projects in Dallas
When selecting a concrete building partner in Dallas, the decision ultimately comes down to finding a team that combines technical expertise with practical execution. At EB3 Construction, we’ve built our reputation on delivering concrete structures that stand the test of time while maintaining the schedule and budget discipline that developers and property owners demand. Our approach to concrete construction balances engineering precision with real-world constructability, ensuring that your vision translates seamlessly from concept to completion.
The Dallas construction landscape presents unique challenges – from the region’s clay soils requiring specialized foundation solutions to the competitive material sourcing environment that affects project timelines. Our team navigates these complexities by implementing comprehensive pre-construction planning, establishing clear communication protocols, and leveraging our established relationships with concrete suppliers and specialty subcontractors throughout the metroplex. This integrated approach allows us to manage the variables that often derail concrete projects, particularly during critical phases like large-scale pours where timing and coordination are paramount.
Ready to break ground on your next Dallas concrete building project? Contact EB3 Construction to discuss how our concrete construction expertise can transform your building vision into reality.