Rammed earth construction is not a new concept in the building world. This method has stood the test of time, with examples dating back thousands of years. From sections of China’s Great Wall to ancient dwellings across Africa and the Middle East, rammed earth structures continue to stand centuries after their construction. The technique’s longevity speaks to its effectiveness as a building method that we still implement today in contemporary sustainable architecture.
The construction process unfolds in carefully executed stages. We set up sturdy formwork to create the wall shape, then add the soil mixture in layers of about 10 centimeters. Each layer is thoroughly compacted—or rammed—until it reduces to about 6-7 centimeters in height.
The ramming process dramatically increases the density and strength of the material. After compaction, we move the formwork upward or laterally to continue building. This layer-by-layer approach creates the distinctive horizontal striations that give rammed earth walls their characteristic appearance, resembling natural geological formations.
How is a Rammed Earth Wall Constructed?
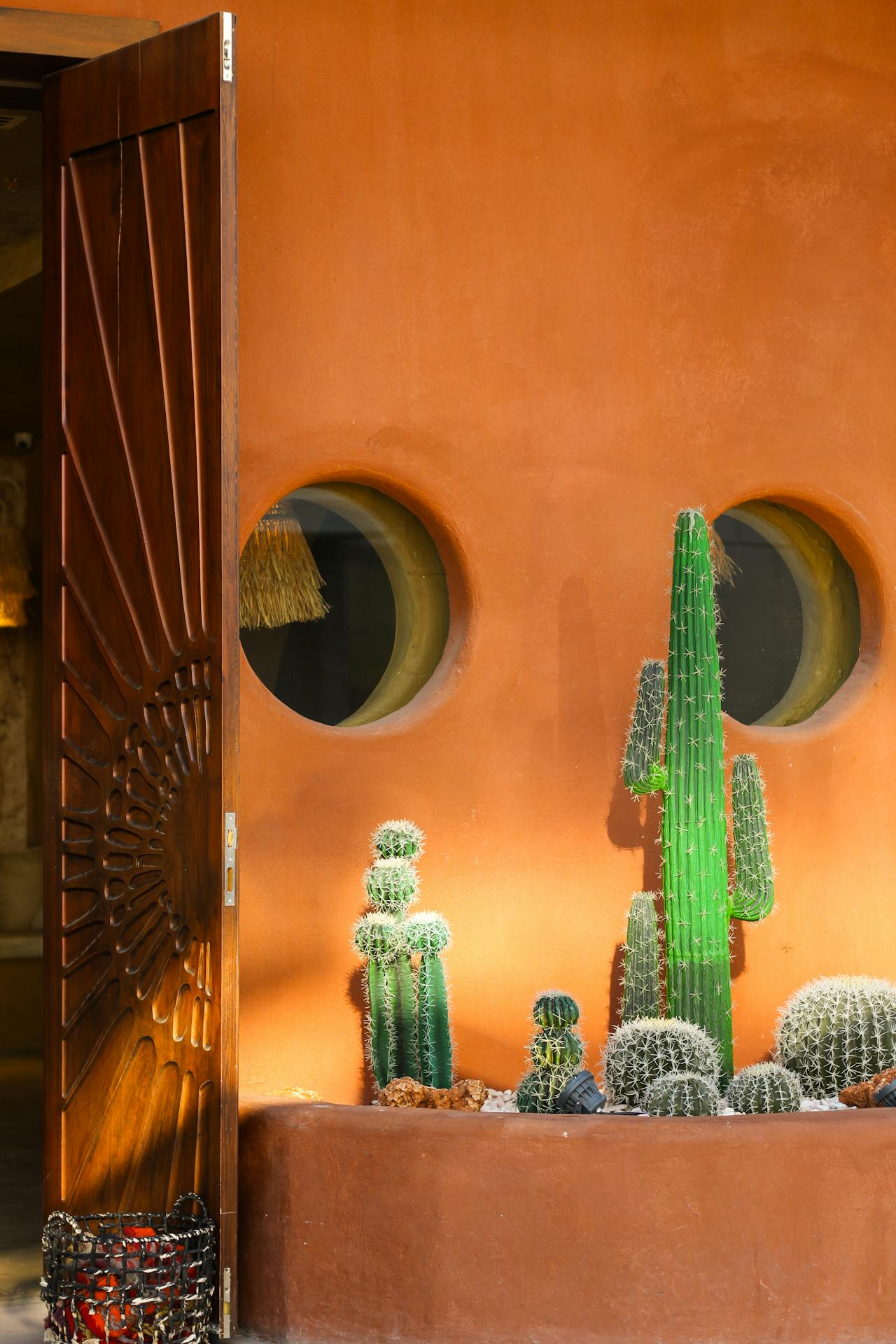
At EB3 Construction, our rammed earth process starts with careful soil selection and preparation. We source and test local materials to achieve the optimal blend for structural integrity and aesthetic appeal. While the ideal soil composition varies by region, we generally aim for a mixture containing 70-80% earth and gravel with 20-30% clay.
The formwork phase is crucial for successful rammed earth walls. We construct robust, reusable formwork systems using marine-grade plywood reinforced with sturdy framing. These forms must withstand significant pressure during compaction without bulging or shifting. The recent updates to the California building code concerning seismic considerations have influenced our formwork design to ensure walls meet structural requirements, even in earthquake-prone areas.
Material Preparation and Mixing
The soil mixture sets the foundation of the entire structure. We avoid using topsoil, which contains organic material that can compromise wall strength. Instead, we excavate subsoil and conduct drop tests to assess its suitability. Our experienced crews often identify proper soil composition by feel, but we rely on laboratory testing for precision on larger projects.
Water content is one of the most nuanced aspects. Too dry, and the earth won’t properly bind; too wet, and the wall may crack during curing. We aim for a mix that forms a cohesive ball when squeezed in hand, breaking into clumps when dropped from waist height. This moisture-content sweet spot enables optimal compaction and prevents future structural issues.
The Ramming Process
With secure formwork and prepared materials, we begin construction by pouring the soil mixture into the forms in layers of approximately 10-25 centimeters. Each layer undergoes thorough compaction using pneumatic tampers, reducing its volume by about 50%. This compaction transforms loose earth into a solid, stone-like material with impressive compressive strength.
For specialized aesthetic effects, we sometimes use hand tamping techniques alongside mechanical methods. While pneumatic tampers greatly improve efficiency on large sections, manual tamping allows more control for decorative patterns or tight spaces. The distinctive layered appearance of rammed earth walls naturally emerges from this process, with subtle color variations reflecting the soil’s mineral composition.
Tool Type | Application |
---|---|
Manual (Hand) Tools | Used for small-scale projects, such as tampers or rammers. Best for limited quantities but labor-intensive and time-consuming. |
Mechanical Ramming Equipment | Used for large-scale projects, featuring a large steel plate that provides consistent compaction, reducing manual effort. |
Hydraulic Press | Suitable for large industrial or commercial projects for efficient and quick ramming through hydraulic pressure. |
Pneumatic Rammers | Appropriate for smaller projects, like residential buildings. They use compressed air to drive a steel plate for compaction. |
Curing and Finishing
Unlike concrete, which requires prolonged formwork contact, rammed earth walls achieve sufficient strength to allow for immediate form removal. We carefully remove the forms while the wall is slightly damp, allowing us to address any surface imperfections. The wall then continues to cure and harden over several weeks as moisture evaporates and the material stabilizes.
During the winter, we implement protective measures to prevent freeze-thaw damage during this curing period. In colder climates, temperature monitoring and temporary shelters may be required to ensure proper strength development. While the wall achieves most of its strength within the first month, it continues to harden for years through a process similar to the natural formation of sedimentary rock.
The finished walls require minimal maintenance compared to conventional building systems. We often apply breathable sealants to enhance weather resistance while preserving the wall’s natural ability to regulate humidity. This moisture permeability is a significant advantage of rammed earth over less breathable building systems, creating healthier indoor environments and maintaining the wall’s structural integrity for decades.
What Are the Key Benefits of Rammed Earth Walls?
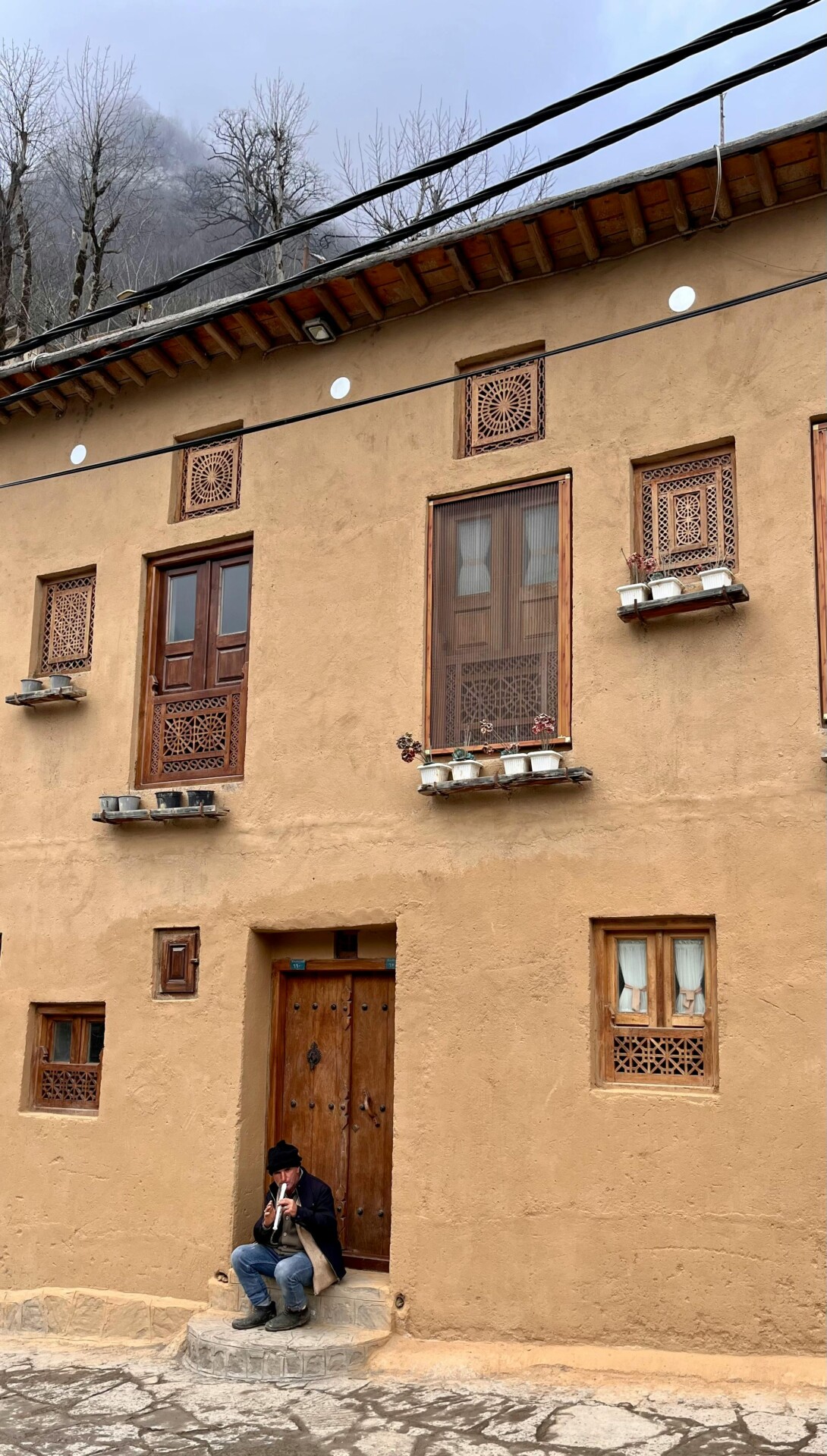
Incorporating rammed earth walls into construction projects offers a sustainable solution, leveraging an ancient building technique that provides numerous benefits. The natural properties of compacted soil help create structures that endure over time while enhancing environmental credentials.
Superior Thermal Performance
The significant thermal mass of rammed earth walls underpins their energy efficiency. In our California desert projects, these thick earthen structures have demonstrated the ability to absorb heat during the day and gradually release it at night. This natural temperature regulation substantially reduces the need for mechanical heating and cooling, resulting in more comfortable interiors and lower operational costs for building owners.
The physics behind this performance is straightforward yet effective. The density of the compacted earth creates a delayed thermal transfer, smoothing out temperature fluctuations. Practically, this means that interior spaces remain cooler during hot days and warmer during cool nights without constant HVAC cycling. A recent commercial project reported a 30% reduction in cooling costs during its first summer of operation.
Beyond temperature regulation, the thermal properties of rammed earth are ideal for passive solar design strategies. By strategically positioning windows and thermal mass, buildings can maximize solar gain in the winter and utilize shading for summer protection, aligning with nature rather than opposing it.
Exceptional Durability and Low Maintenance
The longevity of rammed earth structures often surprises even skeptical clients. Historical examples worldwide show these walls can last centuries with minimal maintenance. Our construction methodology, which involves proper compaction and stabilization, ensures structural integrity that meets modern construction demands.
Building with rammed earth results in walls that naturally resist fire, making them valuable in wildfire-prone areas. The dense, earthen material doesn’t burn. Additionally, these walls provide no entry points or food sources for termites and pests common in conventional wood construction, eliminating the need for toxic chemical treatments.
Minimal maintenance is required throughout a building’s lifecycle. Unlike conventional materials needing regular painting or treatment, rammed earth walls maintain their appearance and integrity with little intervention, translating to significant long-term cost savings for property owners.
Natural Humidity Regulation
The hygroscopic properties of rammed earth walls offer significant benefits for indoor air quality. When clay portions are exposed to interior spaces, they naturally regulate humidity levels within the ideal range of 40-60% relative humidity. This moisture-buffering ability enhances indoor air quality and comfort.
In a recent multi-unit residential project, this natural humidity regulation removed the need for additional humidification/dehumidification systems in several areas. The walls absorb excess moisture in humid conditions and release it in dry periods, fostering a stable indoor environment with fewer mechanical interventions.
This capability also helps prevent mold growth and reduces respiratory issues associated with overly dry or damp settings. In healthcare and wellness facilities using rammed earth, occupants have consistently reported improved comfort and air quality.
Aesthetic Appeal and Design Flexibility
Besides their performance benefits, rammed earth possesses distinctive aesthetic qualities appealing to many architects and clients. The natural layering and earth tones create visual interest that conventional materials cannot replicate. In construction feasibility assessments, we emphasize how these walls serve as architectural features, negating the need for extra finishes.
Different soil types and pigments can achieve specific color palettes that align with the landscape and architectural vision. The formwork process allows precise control over wall dimensions and openings, supporting both traditional and contemporary designs.
The versatility of rammed earth extends across various building types. We have successfully used these walls in residential, commercial, and institutional settings. Their mass offers excellent acoustic properties, creating quieter interiors—a valued feature in multi-family housing and hospitality projects where sound transmission is a concern.
Wall System | Material Type | R-Value per Inch | Total R-Value (Average) | Considerations |
---|---|---|---|---|
Rammed Earth | Natural | 0.25 – 0.75 | 22 – 30 | Requires insulation in cold climates; excellent thermal mass |
Wood Frame | Conventional | Varies | ~18 (effective) | 18% framing factor reduces thermal efficiency |
Steel Stud | Conventional | Varies | ~7 | Thermal bridging significantly reduces effectiveness |
Concrete | Conventional | Varies | Comparably less without insulation | High thermal conductivity; requires external insulation |
Straw Bale | Alternative | Varies greatly | 45 – 55 | Best thermal performance; direction-dependent conductivity |
Hempcrete | Alternative | 2.2 – 2.5 | Varies | Moderate thermal mass; suitable for single-story |
Light Straw Clay | Alternative | Varies | 20 – 25.4 | Requires breathable lime plaster; high carbon sequestration |
Environmental Sustainability
The environmental benefits of rammed earth construction align with the growing interest in sustainable building practices. Using soil often directly from the building site minimizes transportation impacts and associated carbon emissions. The minimal processing involved results in much lower embodied energy compared to materials like concrete or steel.
Our code compliance expertise supports the integration of these natural systems. Properly designed and constructed, rammed earth walls can meet or exceed modern building codes, ensuring a significantly reduced environmental impact. Many jurisdictions now recognize rammed earth as an approved construction method, though we work closely with building officials to ensure full compliance.
For developers aiming for certifications like LEED or the Living Building Challenge, rammed earth contributes valuable points in materials and resources. Its natural, non-toxic composition also supports healthy indoor air quality, creating environments better for both the planet and its inhabitants.
What Challenges Come with Rammed Earth Construction?
While we’re passionate about the sustainability and aesthetic appeal of rammed earth construction, we approach each project with a clear understanding of the challenges involved. As experienced general contractors, we’ve developed strategies to address these challenges effectively, ensuring successful outcomes for our clients’ projects.
Water Management Concerns
Rammed earth’s greatest vulnerability is its susceptibility to water damage. Without proper protection, prolonged moisture exposure can compromise structural integrity. We address this through comprehensive drainage systems and specialized waterproofing techniques to protect your investment.
In our projects, we often incorporate water-based silicone admixtures like plasticure during the mixing process to enhance water resistance. Additionally, we design extended roof overhangs and proper foundation details to direct water away from walls, significantly reducing moisture risks in wetter climates.
During the California rainy season last February, several traditionally built rammed earth structures experienced deterioration while properly waterproofed walls remained intact. This real-world performance difference underscores why we prioritize moisture protection in every project.
Budget and Timeline Realities
Rammed earth construction requires substantial investment. Current market costs range from $50-$225 per square foot compared to conventional concrete’s $4-$8. This price difference reflects the specialized formwork, higher labor requirements, and technical expertise needed for quality results.
The construction process is inherently time-intensive. Each wall section requires careful preparation, precise mixture ratios, layer-by-layer ramming, and proper curing time. For a typical residential project, the wall construction phase may extend several weeks longer than conventional methods. We’ve found that transparent discussions about these factors during planning help clients develop realistic budgets and timelines.
Insulation Requirements
Despite excellent thermal mass properties, rammed earth provides minimal insulation with an R-value of approximately 0.4 per inch. In most climate zones, additional insulation is necessary to meet energy codes and ensure comfort, adding another layer of complexity and cost to the construction process.
We typically incorporate either exterior insulation systems or construct double-wythe walls with insulation between them. The latter approach maintains the aesthetic appeal of rammed earth on both interior and exterior surfaces while significantly improving thermal performance. This integrated insulation strategy helped one of our recent projects achieve 40% better energy performance than required by code.
Regulatory Hurdles
Perhaps the most frustrating challenge is navigating building codes and permits. Many jurisdictions lack specific provisions for rammed earth construction, creating uncertainty for building officials and potential delays in project approval. Our team works closely with local authorities, providing engineering data and precedent examples to secure necessary approvals.
Insurance can also present obstacles, as some providers are unfamiliar with rammed earth’s performance characteristics. We’ve developed relationships with insurers who understand and appreciate the durability and fire-resistance of properly constructed rammed earth buildings, helping smooth this potential roadblock.
While conducting a recent project in northern California, we encountered initial resistance from local building officials unfamiliar with rammed earth techniques. By organizing a site visit to a completed project and providing technical documentation from similar jurisdictions, we successfully demonstrated compliance with structural and safety requirements.
Despite these challenges, the growing interest in sustainable construction is gradually improving the regulatory landscape. Each successful project helps establish precedents that make future approvals easier to obtain. Our experience navigating these complexities allows us to guide clients through the process efficiently, transforming potential obstacles into manageable steps toward their vision.
How Does Rammed Earth Compare to Conventional Building Materials?
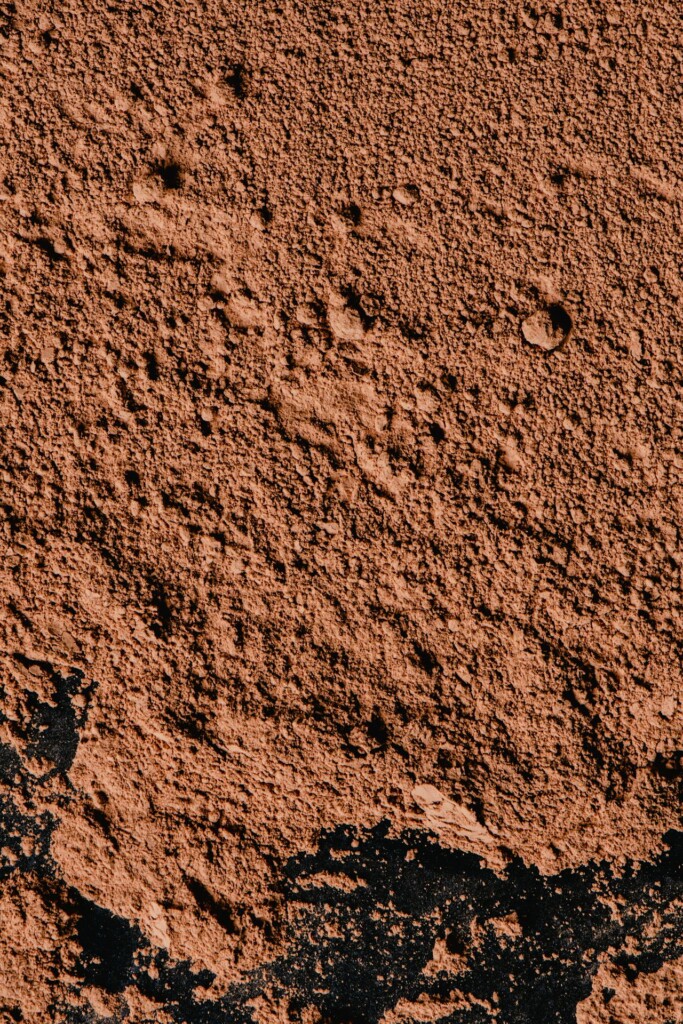
As general contractors working with diverse building materials, we have witnessed firsthand how rammed earth construction creates distinctive structures with environmental advantages that concrete simply can’t match. When implementing rammed earth techniques, we utilize materials with substantially lower embodied carbon—approximately 48 kg per cubic meter compared to concrete’s 635 kg. This significant difference is one of the reasons developers increasingly request this alternative in sustainability-focused projects.
The construction process for rammed earth demands specialized knowledge that our teams have refined through practical application. We build these walls significantly thicker than conventional alternatives—typically 6-24 inches depending on structural requirements—creating robust structures with exceptional sound attenuation properties. During our California projects last summer, clients were particularly impressed by how the thermal mass characteristics moderated interior temperatures, absorbing daytime heat and releasing it gradually overnight.
Cost and Construction Considerations
When discussing budgets with developers, we’re transparent about the financial implications. Rammed earth construction is more labor-intensive than pouring concrete, with costs ranging between $50-225 per square foot compared to concrete’s $4-8 per square foot. This substantial difference reflects the specialized formwork systems required and the meticulous layering and compaction process our crews perform.
The construction timeline also extends beyond typical concrete installations. Our teams must carefully mix, ram, and shape aggregates into formwork—a process that can’t be rushed without compromising structural integrity. Unlike the standardized approaches used with concrete, rammed earth demands adaptability and specialized expertise throughout the building process.
Environmental Impact Factors
We tailor the environmental performance of rammed earth walls to specific project requirements. The sustainability profile varies significantly depending on whether we’re working with raw earth or stabilized mixtures. When local regulations or structural demands require enhanced performance, we incorporate cement stabilizers (typically 5-8% of the mixture), which improve durability but increase the carbon footprint.
For context, our calculations show that a 300mm rammed earth wall with 5% cement content produces slightly more emissions than a 100mm concrete wall—an important consideration when evaluating the total environmental impact. However, we frequently source materials locally, significantly reducing transportation emissions compared to traditional concrete production, which often requires long-distance hauling of sand and aggregate.
While working with property developers in moisture-prone regions, we often recommend stabilized rammed earth to enhance weather resistance. These walls perform exceptionally well but represent a middle ground between raw earth (most environmentally friendly) and concrete (least environmentally friendly) in terms of carbon footprint.
Incorporating alternative binders like lime or pozzolans can further reduce environmental impact. On recent projects, we’ve successfully substituted up to half the cement content with these alternatives, maintaining structural integrity while substantially lowering carbon emissions. This approach allows us to balance code compliance requirements with sustainability goals, creating durable structures that align with modern environmental standards.
Conclusion: Is Rammed Earth Right for Your Construction Project?
When we assess sustainable building techniques for our clients’ projects, rammed earth construction consistently stands out for its unique blend of environmental benefits and structural performance. This centuries-old method has found renewed relevance in today’s climate-conscious construction environment. Deciding if it’s suitable for your specific project requires careful evaluation.
During our construction planning process, we help developers consider several critical factors. The exceptional thermal mass of rammed earth walls allows for natural temperature regulation, which can significantly reduce long-term energy costs. Its distinctive aesthetic—with layered earth tones and organic texture—creates spaces that connect occupants with the natural environment in ways conventional materials cannot. With proper construction techniques, these structures can last for generations with minimal maintenance.
However, we acknowledge the practical challenges of rammed earth projects. The specialized construction process typically extends build timelines compared to conventional methods. Labor costs are higher due to the skilled craftsmanship required. Additionally, current building codes in many areas lack standardized specifications for rammed earth, potentially complicating permitting. These factors must be balanced against the compelling sustainability profile and durability advantages.
The recent California wildfires have prompted many developers to reconsider traditional building materials, with rammed earth gaining traction for its fire-resistant properties. This trend reflects a growing awareness that initial construction investments can yield substantial long-term returns through operational savings and enhanced resilience to climate extremes.
As your construction partner, we bring specialized expertise in sustainable building techniques while maintaining realistic expectations about project timelines and budgets. By evaluating your specific site conditions, design aspirations, regulatory environment, and performance requirements, we can help determine if rammed earth aligns with your development goals and deliver a structure that balances innovation with practicality.
Contact EB3 Construction to discuss whether rammed earth is the right choice for your next sustainable building project.