Foundation construction is crucial for every successful building project. As the lowest load-bearing component, foundations transfer the entire weight of buildings and their contents into the underlying soil or bedrock. This critical structural element creates the interface between the above-ground structures we build and the earth that must ultimately support them.
Our approach to foundation work starts with understanding how different loads interact with site conditions. From the dead weight of structural elements to forces from occupants, wind pressures, and seismic activity, foundations must handle it all while maintaining stability. The foundation not only supports vertical loads; it also anchors the building against lateral forces and potential uplift during severe weather.
Foundation systems vary widely based on soil characteristics, structural requirements, and project specifics. We design these essential components to distribute building loads safely into the ground while protecting against moisture intrusion, settlement issues, and frost heave in colder climates. A properly engineered foundation isn’t merely the starting point of construction; it’s the enduring platform that determines a structure’s performance throughout its service life.
What Are the Main Types of Foundations in Construction?
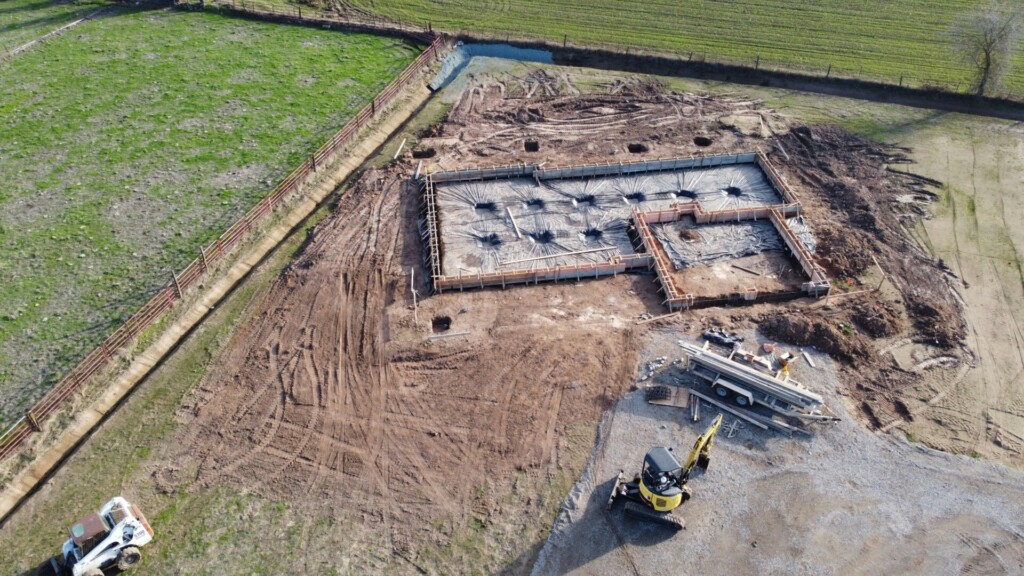
When starting any construction project, the foundation serves as a critical structural element that transfers loads from the building to the soil beneath. At EB3 Construction, we classify foundations into two primary categories based on depth and load-bearing requirements: shallow foundations and deep foundations. Each type serves different purposes depending on soil conditions, structural requirements, and project specifications.
Shallow Foundations
Shallow foundations distribute building loads across a relatively wide area near the ground surface. We typically implement these when stable soil exists within 3 meters of the ground level. Their cost-effectiveness and simpler installation make them our standard choice for many residential and light commercial projects.
For single-family homes and smaller structures, we often use isolated footings (also called pad footings) to support individual columns. These concrete pads spread the concentrated column loads to prevent excessive settlement. When soil conditions require distributing the load from multiple columns, we utilize combined footings that support two or more columns.
Strip footings serve as our solution for load-bearing walls, creating a continuous foundation strip that evenly distributes the wall load to the soil below. For projects built on softer soils or those requiring more uniform load distribution, we recommend mat or raft foundations—essentially a single concrete slab that supports the entire building footprint.
Deep Foundations
When stable soil exists only at greater depths or when structures carry substantial loads, we implement deep foundation systems. These foundations transfer loads through unstable upper soil layers to reach more competent bearing strata below.
Pile foundations represent our most common deep foundation solution. These are driven, drilled, or cast long, slender columns into the ground until they reach bedrock or a stable soil layer. The February 2023 tower project in downtown Portland demonstrated how effectively pile foundations can support tall structures on previously unsuitable land.
For construction near water or when dealing with extremely poor soil conditions, we utilize caisson foundations. These watertight retaining structures allow excavation below the water table to create a solid foundation base. Caissons are particularly valuable for bridge piers and waterfront structures where traditional foundations would fail.
Pier foundations, which involve drilling cylindrical holes and filling them with reinforced concrete, provide another deep foundation option. We recommend these for projects requiring moderate depth support without the extensive equipment needed for pile driving.
Foundation Type | Soil Condition | Application |
---|---|---|
Shallow Foundations | Stable soils within 3 meters from the surface | Single-family homes, Light commercial projects |
Deep Foundations | Poor surface soil conditions, Requires reaching stable substrates | Tall structures, Projects near water, Areas with high groundwater levels |
Pile Foundations | Weak or loose soils | Support tall structures, Areas with high seismic activity |
Caisson Foundations | Water-saturated soils or beneath the water table | Bridge piers, Waterfront structures |
Mat or Raft Foundations | Softer soils requiring load distribution | Buildings with multiple column supports |
Basement Foundations | Structures requiring additional space or support | Buildings with basements |
Selecting the Right Foundation System
Our foundation selection process begins with thorough site investigation and soil testing. By analyzing soil bearing capacity, groundwater levels, and structural loads, we determine which foundation system will deliver optimal performance. For expansive clay soils common in parts of Texas, we often recommend deep foundations to bypass the problematic soil layer entirely.
Budget considerations inevitably influence foundation decisions. While shallow foundations typically cost less initially, site conditions sometimes necessitate deep foundations despite their higher installation expense. We carefully evaluate the long-term structural implications alongside construction costs to recommend the most appropriate foundation solution.
Climate and environmental factors also play crucial roles in our foundation selection. In coastal areas prone to erosion, we often implement deep foundations that can withstand soil instability. Similarly, in seismic zones, we design foundations specifically to resist lateral forces and ground movement during earthquakes.
How is Foundation Construction Carried Out Step-by-Step?
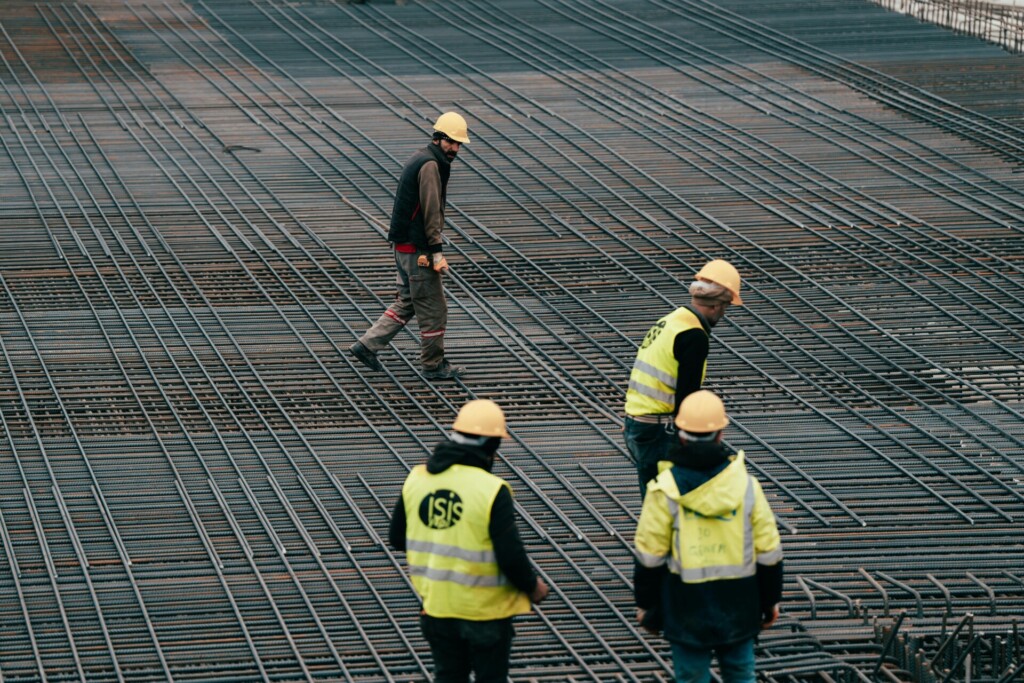
At EB3 Construction, we approach foundation work with the understanding that it forms the literal bedrock of every successful project. Our systematic process ensures each foundation we build provides reliable structural support while meeting project-specific requirements. Foundation construction is never a one-size-fits-all operation—soil conditions, building design, and local regulations all influence our approach.
Site Preparation and Initial Survey
We begin by clearing the construction site of all vegetation, debris, and existing structures that could compromise foundation integrity. Our crews use heavy machinery to remove obstacles while preserving any elements marked for protection in the site plan. This initial phase often reveals surprises not caught during preliminary site assessments, such as unexpected utility lines or soil composition variations.
After clearing, we conduct a thorough site survey to establish reference points and ensure proper elevation. Recent improvements in laser leveling technology have significantly enhanced our accuracy during this critical stage. We then grade the lot and test for soil compaction, adjusting our approach based on the results to prevent future settlement issues.
Excavation and Subgrade Preparation
Excavation goes beyond simply digging a hole. We carefully remove soil to the specified depth and dimensions according to engineering plans. The California residential building market has seen a shift toward deeper foundations in certain regions due to expansive soil concerns. Our excavation approach adapts to these regional variations while maintaining strict adherence to design specifications.
Once excavation is complete, we prepare the subgrade—the natural soil upon which the foundation will rest. This involves removing loose material, compacting the soil to the required density, and ensuring proper drainage. In areas with poor soil conditions, we often implement soil stabilization measures or install engineered fill to create a suitable base.
Moisture Barriers and Preliminary Treatments
With the subgrade prepared, we apply anti-termite treatments to protect the structure from potential infestation. This preventative measure has become increasingly important as climate change expands the range of termite activity across North America. We then install waterproofing measures, including drainage systems and moisture barriers, to protect against groundwater intrusion.
The placement of a vapor barrier—typically black polyethylene sheeting—is particularly critical in slab foundations. This barrier prevents ground moisture from migrating through the concrete, potentially damaging flooring and creating unhealthy indoor conditions. We ensure these barriers extend beyond foundation edges and are properly sealed at all penetrations and seams.
PCC Layer and Foundation Reinforcement
We pour a Plain Cement Concrete (PCC) layer to create a level, clean surface for the structural foundation. This “mud slab” typically ranges from 3 to 6 inches thick, depending on soil conditions and structural requirements. The PCC layer also serves as a working platform for the installation of reinforcement.
Reinforcement placement follows strict engineering specifications. We position steel rebar or wire mesh according to structural drawings, ensuring proper spacing, overlap, and concrete cover. The Winter 2023 concrete reinforcement shortage taught us to plan well ahead for material availability, particularly for specialty steel configurations required in seismic zones.
Reinforcement Technique | Description | Application |
---|---|---|
Micropiles | Small-diameter piles installed into the soil using hydraulic jacks | Suitable for unstable soils or differential settlements |
Mass Concrete Underpinning | Excavating and pouring new rebars and concrete beneath the existing foundation | Used for reinforcing structures with significant load requirements |
Resin Injection | Injecting polyurethane resins into the soil around foundations | Effective for clayey soils or areas with subsidence |
Wall Bracing and Carbon Fiber Straps | Strengthening foundation walls showing signs of bowing or cracking | Applicable in situations with wall integrity issues |
Pier and Beam Underpinning | Adding deep piers to transfer loads to stronger soil layers | Effective when the soil at shallow depths is not stable |
Jet Grouting | High-pressure injection of cementitious grout to create a new foundation base | Suitable for poorly consolidated soils |
Formwork Installation and Pre-Pour Preparation
Formwork serves as temporary molds that hold concrete in place until it hardens. Our carpenters construct these forms using materials appropriate for the project—typically wood for residential projects and steel or aluminum for larger commercial foundations. Proper bracing and support prevent form movement during concrete placement.
Before concrete placement, we install utility penetrations, anchor bolts, and other embedded items according to design specifications. These elements must be precisely located and secured to prevent movement during concrete placement. We then conduct a pre-pour inspection to verify formwork integrity, reinforcement placement, and overall readiness.
Concrete Placement and Initial Finishing
The concrete mix design is tailored to project specifications, considering factors like required strength, exposure conditions, and placement methods. We typically use concrete with a 28-day compressive strength between 3,000 and 5,000 psi for residential foundations, though commercial projects often require higher strength formulations.
During placement, we employ appropriate methods—direct chute, pumping, or conveyor systems—based on site conditions and foundation type. Our crews work methodically to ensure proper concrete consolidation, using vibrators to eliminate air pockets and ensure complete reinforcement coverage. Initial finishing operations follow immediately, creating a level, uniform surface.
Curing Process and Quality Assurance
Proper curing is essential for concrete to reach its designed strength and durability. We implement appropriate curing methods—moisture retention through water spray, curing compounds, or wet coverings—based on weather conditions and project requirements. During summer months, we pay particular attention to evaporation control to prevent surface cracking.
The curing period typically extends 7-28 days, during which we monitor conditions and protect the concrete from extreme temperatures, premature drying, and physical damage. Once curing is complete, we conduct final inspections to verify dimensional accuracy, surface quality, and overall compliance with design specifications.
Throughout the entire foundation construction process, quality control remains our focus. Regular testing and inspections ensure the finished foundation will provide stable, durable support for the structure it will carry.
What Factors Influence Foundation Selection and Design?
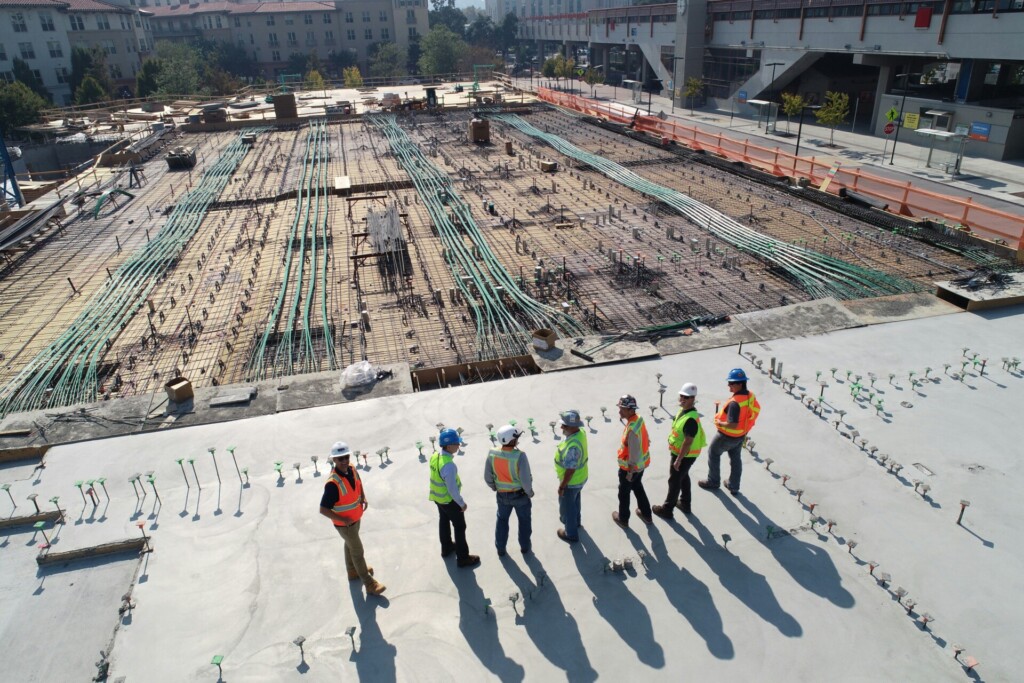
When evaluating a project site for foundation requirements, several critical factors guide our decision-making process to ensure the building’s structural integrity throughout its lifetime. Our approach is comprehensive, as foundations serve not just as structural elements but as the literal base upon which project success is built.
Soil Conditions and Bearing Capacity
Soil conditions are crucial in our foundation selection process. The soil’s bearing capacity—its ability to support load without excessive settlement—directly influences the foundation type we recommend. Recent advances in soil testing have enhanced our ability to accurately assess these conditions before construction begins.
Different soil profiles require specific foundation solutions. For instance, when we encounter hard rock, we typically use isolated shallow foundations that leverage natural stability. Clayey soils, prone to expansion and contraction with moisture changes, often necessitate raft foundations to evenly distribute structural loads and minimize differential settlement.
Sandy soils, particularly loose types, may require pile foundations to reach deeper, more stable soil layers. The February 2023 earthquake in Turkey highlighted the catastrophic consequences of improper foundation selection in areas with liquefiable sandy soils. In problematic black cotton soils, known for extreme volume changes, we use under-reamed pile foundations to anchor structures below the active zone.
Load Distribution Requirements
The magnitude and distribution of structural loads significantly impact our foundation design approach. For high-rise buildings with concentrated column loads, we might recommend deep foundations even in otherwise suitable soil conditions. Conversely, for structures with evenly distributed loads, shallow foundations often provide adequate support while optimizing construction costs.
We factor in total load combinations, including dead loads, live loads, wind forces, and potential seismic events. The foundation must distribute these forces safely into the supporting soil without exceeding allowable bearing pressures or causing undue settlement. Each project presents unique load considerations that influence our foundation selection process.
Foundation Type | Suitable Soil Conditions | Load Requirements | Applications |
---|---|---|---|
Isolated Footings | Stable soils within 3 meters | Light loads from single columns | Single-family homes, light commercial structures |
Combined Footings | Stable soils with uniform characteristics | Support multiple columns | Multi-column structures where individual footings are not feasible |
Strip Footings | Stable soil conditions | Support load-bearing walls | Load-bearing wall foundations in residential and light commercial projects |
Mat/Raft Foundations | Softer or expansive soils | Uniformly distribute loads over larger areas | Structures requiring more uniform load distribution, such as on expansive soils |
Pile Foundations | Weak or unstable upper soils, reaching stable strata | Substantial loads | Tall structures, infrastructure in poor soil conditions |
Caisson Foundations | Wet and unstable soils, water table conditions | Support extensive loads | Bridges, waterfront structures |
Pier Foundations | Moderate depth stability requirements | Moderate loads | Additional support in areas with moderately poor soil conditions |
Groundwater Conditions
The presence and level of groundwater significantly affect both foundation design and construction methodology. In areas with high water tables, we must consider hydrostatic pressure, potential soil erosion, and the risk of uplift forces. These conditions often require specialized waterproofing measures and drainage systems to maintain the foundation’s structural integrity.
Groundwater also influences construction techniques. Deep excavations below the water table require dewatering systems or specialized methods like slurry walls to sustain stable working conditions. The additional costs and technical challenges of building in high water table areas are part of our foundation recommendations and construction planning.
Seismic Considerations
In seismically active regions, foundations play a crucial role in transferring lateral and inertial forces safely into the ground. Our foundation designs in these areas include additional lateral support elements and often utilize specialized connection details between the superstructure and foundation to absorb seismic energy.
The 2019 update to seismic design provisions in the International Building Code prompted us to reevaluate traditional approaches to foundation design in earthquake-prone areas. We now implement more robust foundation solutions that can withstand ground motion while maintaining structural integrity. These measures include additional reinforcement, increased depth requirements, and sometimes base isolation systems for crucial facilities.
Construction Considerations
Practical construction factors also influence our foundation selection. Site access constraints may limit equipment options, affecting our ability to install certain foundation types. Adjacent structures require protection from potential excavation damage, which sometimes necessitates specialized shoring systems or underpinning of existing foundations.
Construction schedule and budget constraints significantly affect foundation selection as well. While deep foundations might offer optimal technical performance in some cases, the associated time and cost implications might lead us to recommend alternative solutions that meet performance requirements while better aligning with project parameters.
By carefully evaluating these interconnected factors, we develop foundation designs that appropriately balance technical performance, construction feasibility, and project economics. This holistic approach ensures our clients receive foundations that will support their structures safely and efficiently throughout their intended service lives.
Conclusion: Ensuring Successful Foundation Construction
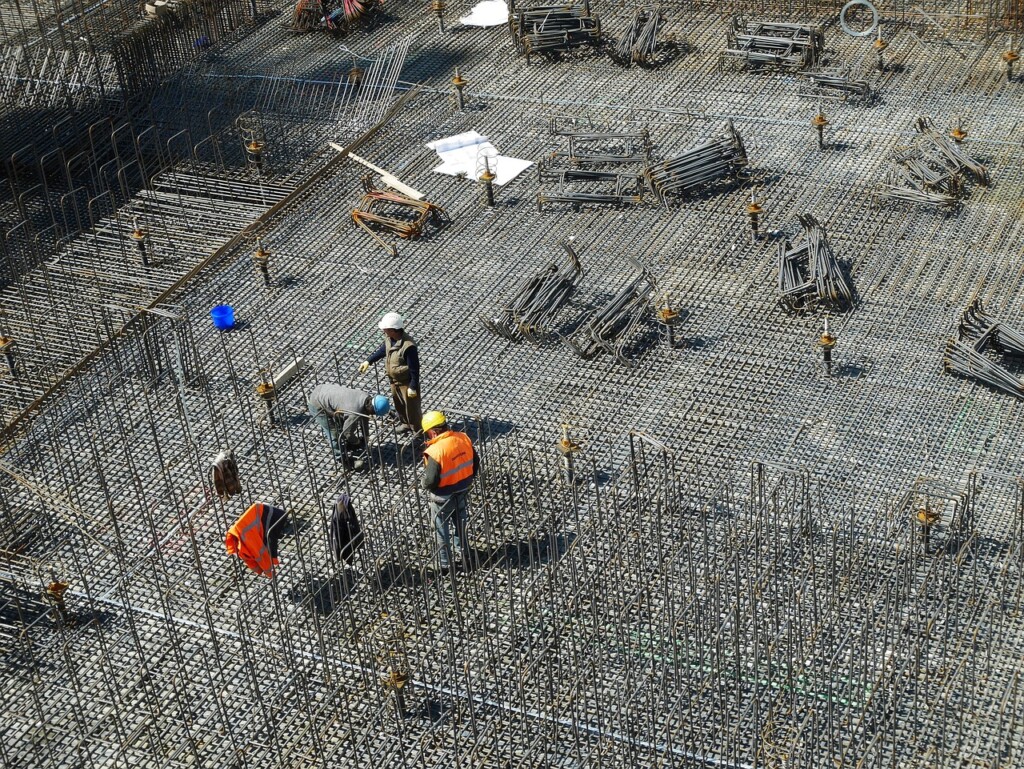
A well-constructed foundation is fundamental not just as the starting point of construction, but as a critical element that ensures a structure’s integrity for many years. In each project, our team sees how foundation decisions made in the planning stages impact the entire building lifecycle. The synergy between soil composition, load distribution, and construction techniques can either pave the way for success or lead to costly structural issues.
Quality foundation construction involves more than merely adhering to building codes. It’s about applying engineering principles that consider site-specific challenges and future conditions. We emphasize thorough soil analysis, suitable foundation selection, and precise execution because we know that shortcuts in foundation work lead to significant problems later. Investment in proper waterproofing, reinforcement, and drainage leads to reduced maintenance costs and greater building longevity. Successful projects consistently show that time dedicated to foundation quality control directly impacts structural performance and stability.
Ready to build on solid ground? Contact EB3 Construction to discuss your foundation needs.