Commercial building costs are one of the most significant investments developers and property owners face when initiating a new project. At EB3 Construction, we frequently address inquiries about pricing expectations for various commercial structures. Generally, commercial building construction costs typically fall within a range of $75 to $400 per square foot, though actual costs can vary considerably based on project requirements, location, and current market conditions.
Building types can significantly impact costs. For example, small office warehouses may have different cost considerations compared to big box retail stores. Typical costs for commercial construction can range from $45 to $300 per square foot, depending on the building type and specifications. For instance, a standard 10,000 sq ft commercial building might have estimated costs between $450,000 and $3 million, subject to project specifics.
Understanding these numbers is crucial. Standard estimates typically cover the building shell, foundation, and basic construction elements. These figures do not usually include interior build-out costs, which can vary greatly depending on finishes, specialized systems, and tenant requirements. Recent supply chain fluctuations post-pandemic have also introduced pricing volatility that may necessitate careful planning and cost contingencies in current projects.
Disclaimer: Pricing figures are based on publicly available market data and are intended for general estimation purposes as of July 2025. They do not represent a formal quote from EB3 Construction. Actual costs will vary by project scope, location, labor rates, and material prices.
How Do Construction Methods Affect Commercial Building Costs?
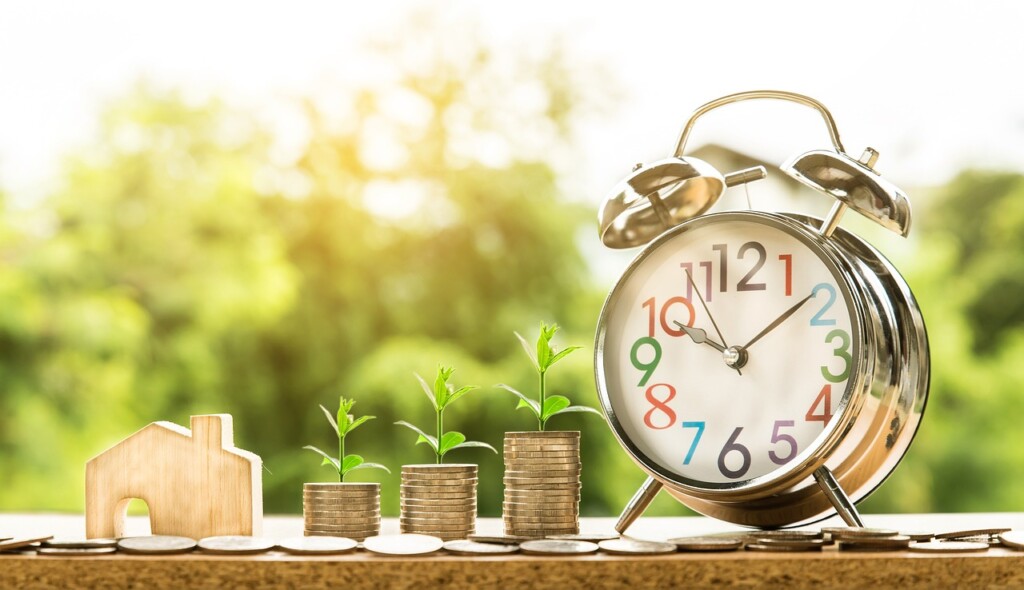
At EB3 Construction, we understand how the chosen construction method for a commercial project can affect both upfront costs and long-term value. The approach may impact your budget, construction timelines, building performance, and future maintenance needs.
Pre-Engineered Metal Buildings (PEMB)
Pre-engineered metal buildings can be a cost-effective solution for certain projects.Typical costs for PEMB structures can range from $20 to $40 per square foot for the basic structure, with total costs varying widely when finishes, MEP systems, and site work are included, depending on project specifics.
The cost efficiency often comes from factory-fabricated components that arrive ready for assembly, which can help reduce on-site labor hours and construction waste. PEMB approaches may help reduce construction schedules compared to some conventional methods, potentially resulting in savings.
Light Gauge Steel Framing
Light gauge steel framing can offer cost benefits while providing design flexibility. This method uses thin steel sheets formed into structural shapes at room temperature. The non-combustible nature of steel may contribute to reduced insurance premiums for some commercial property owners.
The material”s strength-to-weight ratio enables efficient spanning capabilities, and its dimensional stability can help prevent warping and shrinking issues sometimes encountered with wood framing. For multi-story office buildings and retail spaces, this construction method may provide value while maintaining design freedom.
Structural Steel Framing
For projects requiring larger open spans or taller structures, structural steel framing is commonly used, with costs typically ranging from $150 to $250 per square foot, subject to market conditions and project specifics.
While often at a higher price point, structural steel provides strength and versatility for complex commercial projects. The speed of erection may offset some costs through reduced construction timelines. Coordination with fabricators can help ensure steel is sequenced properly for efficient installation, potentially minimizing downtime on the construction site.
Tilt-Up Concrete Construction
Tilt-up concrete construction has gained popularity for warehouses, distribution centers, and big-box retail due to its balance of cost, durability, and speed. This method involves casting concrete panels horizontally at the job site before tilting them into position.
Typical costs for tilt-up construction range from $90 to $120 per square foot, depending on project scope and complexity. The concrete panels offer thermal mass properties that may contribute to energy efficiency and durability against weather events. For some projects, tilt-up construction may help reduce building envelope costs compared to conventional masonry.
The economics of tilt-up can improve with scale—larger buildings with repeating panel designs may maximize efficiency and minimize per-square-foot costs. Proper site preparation is crucial for casting beds and crane positioning to streamline the panel-raising phase of construction.
Factors Influencing Method Selection
When considering method selection, several factors beyond initial square footage costs may be relevant. Building use, local code requirements, timeline constraints, and long-term ownership plans can all influence the optimal construction approach.
In regions with stringent seismic codes, additional reinforcement required for certain methods may impact costs. Similarly, areas with high snow loads may make some construction methods more economical than others due to structural requirements.
Supply chain considerations also play a crucial role in today”s market. The availability and lead times for structural components can vary between methods. Strong relationships with suppliers across construction types may help secure competitive pricing and reliable delivery schedules.
Through planning and early contractor involvement, we help clients navigate these decisions during the crucial pre-construction phase, when method selection may have the greatest impact on project economics. An integrated approach can help ensure that the construction method aligns with both budget constraints and performance expectations for the finished building.
What Factors Influence the Cost of Commercial Construction?
Understanding the diverse factors that influence costs helps provide accurate estimates and deliver value to clients. As a general contractor serving developers and property owners, we aim to consider how various variables can impact budgets and timelines.
Location: One of the Most Significant Cost Drivers
Geographic location is perhaps the single most influential factor in commercial construction costs. Cost disparities can vary significantly between major metropolitan areas and rural regions for essentially identical structures. In high-demand markets, factors like land values, labor costs, and regulatory requirements are typically higher.
Urban projects typically involve additional logistical challenges. Limited site access, restricted staging areas, and coordination with neighboring buildings require specialized planning and can extend project timelines. By contrast, building in rural or suburban areas may offer easier site access and fewer constraints that can help manage costs.
Local building codes and zoning requirements also vary significantly by location. In earthquake-prone regions, additional structural reinforcements are often necessary. In coastal areas, hurricane-resistant construction techniques may be implemented. These location-specific requirements can directly translate to variations in construction costs.
Building Type and Complexity
The intended use of a commercial building fundamentally shapes its construction requirements and costs. Each project type has specialized demands:
Warehouses and industrial facilities typically feature simpler designs with open floor plans and fewer mechanical systems. For these projects, the focus is often on structural integrity and operational efficiency while maintaining cost-effectiveness.
Office buildings require sophisticated HVAC systems, advanced technology infrastructure, and higher-grade finishes. These projects involve coordinating complex MEP systems while creating functional, attractive workspaces.
Healthcare facilities present unique challenges with specialized requirements for medical equipment, sterile environments, and complex mechanical systems. These projects demand precise coordination of multiple building systems to meet strict regulatory standards.
Hospitality and retail spaces emphasize custom finishes and specialized features to enhance guest experiences. The approach often balances aesthetic requirements with practical functionality and durability.
Museums and performing arts centers represent some of the most complex commercial projects, requiring specialized acoustic treatments, lighting systems, and unique architectural features. These landmark projects demand exceptional attention to detail.
Materials and Quality Standards
Material selection significantly impacts both upfront costs and long-term building performance. Clients can be guided to navigate these choices by balancing immediate budget constraints with lifecycle costs:
Structural systems can range from economical pre-engineered metal buildings to custom-designed structural steel or concrete frameworks. Each option offers different advantages in terms of construction speed, design flexibility, and cost.
Exterior envelope materials vary widely in cost, from basic metal panels to high-end curtain wall systems or natural stone facades. These choices can affect not just aesthetics but also building performance and maintenance requirements.
Interior finishes can account for a significant portion of construction costs, with options ranging from standard commercial-grade materials to custom, high-end finishes. Prioritizing these investments based on visibility and impact can be beneficial.
Site Conditions and Preparation
Site characteristics can impact construction costs, often in ways that aren”t immediately apparent until site work begins. Pre-construction services typically include thorough site investigation to identify potential challenges:
Soil conditions determine foundation requirements and can necessitate additional engineering solutions like deep foundations or soil remediation. Poor soil conditions can potentially add to overall project costs.
Topography affects earthwork requirements, with sloped sites necessitating significant grading or retaining walls. These site adjustments can represent substantial costs before vertical construction even begins.
Existing utilities may need relocation or upgrading to support new development. Coordinating with utility companies early in the process can help identify and budget for these requirements.
Environmental factors such as wetlands, protected species, or contamination can trigger additional permitting requirements and mitigation measures. Navigating these complex scenarios requires experience to minimize delays and cost overruns.
Regulatory and Permitting Requirements
The regulatory landscape significantly influences project costs through permitting fees, impact fees, and compliance requirements. Managing these processes proactively can help minimize delays:
Building permit costs typically range from 0.5% to 2% of total construction costs, varying widely between jurisdictions. Familiarity with local requirements can help streamline these processes.
Development impact fees assessed by municipalities to offset infrastructure impacts can add substantial costs, particularly for larger developments. Accounting for these expenses during initial budgeting is important.
Code compliance with increasingly stringent energy, accessibility, and safety standards influences design decisions and material selections. Ensuring compliance while managing cost implications requires expertise.
Project Timeline and Schedule
Construction scheduling directly affects project costs through several mechanisms:
Accelerated schedules often require additional labor, extended work hours, or expedited material deliveries, all of which can increase costs. Evaluating whether accelerating the schedule is justifiable by the premium costs can be helpful for clients.
Seasonal considerations affect certain construction activities. Winter construction in cold climates may require temporary heating or weather protection. Developing schedules that optimize construction sequencing based on seasonal factors can be beneficial.
Market conditions during construction can impact material and labor availability. Strong subcontractor relationships and strategic procurement approaches can help mitigate these risks.
Professional Services and Project Management
The professional team assembled for a project influences both costs and outcomes:
Architectural and engineering fees typically range from 8% to 15% of construction costs, depending on project complexity. Quality design can yield significant returns through more efficient construction and building operation.
Construction management approaches range from traditional design-bid-build to integrated design-build delivery. Various delivery methods can be tailored to project needs and client preferences.
Specialized consultants for acoustics, lighting, sustainability, or other disciplines add expertise but also increase soft costs. Evaluating where specialized input will provide the greatest value can be helpful for clients.
Economic Conditions and Market Factors
Broader economic conditions significantly influence construction costs:
Supply chain dynamics affect material availability and pricing, as highlighted during recent global disruptions. Procurement strategies may include early material purchasing and consideration of alternative materials where advantageous.
Labor availability varies by region and economic cycle, affecting both costs and scheduling. Established subcontractor relationships can help ensure access to quality trades even during labor shortages.
Interest rates impact financing costs for development projects. While outside direct control, working with clients to optimize construction schedules can help minimize financing costs.
By thoroughly analyzing these factors during pre-construction, comprehensive budgets that account for project-specific variables can be developed. Experience across diverse project types and locations enables anticipation of cost impacts and development of appropriate contingency plans, to help support successful project delivery for clients.
How Do Regional Variations Affect Commercial Construction Costs?
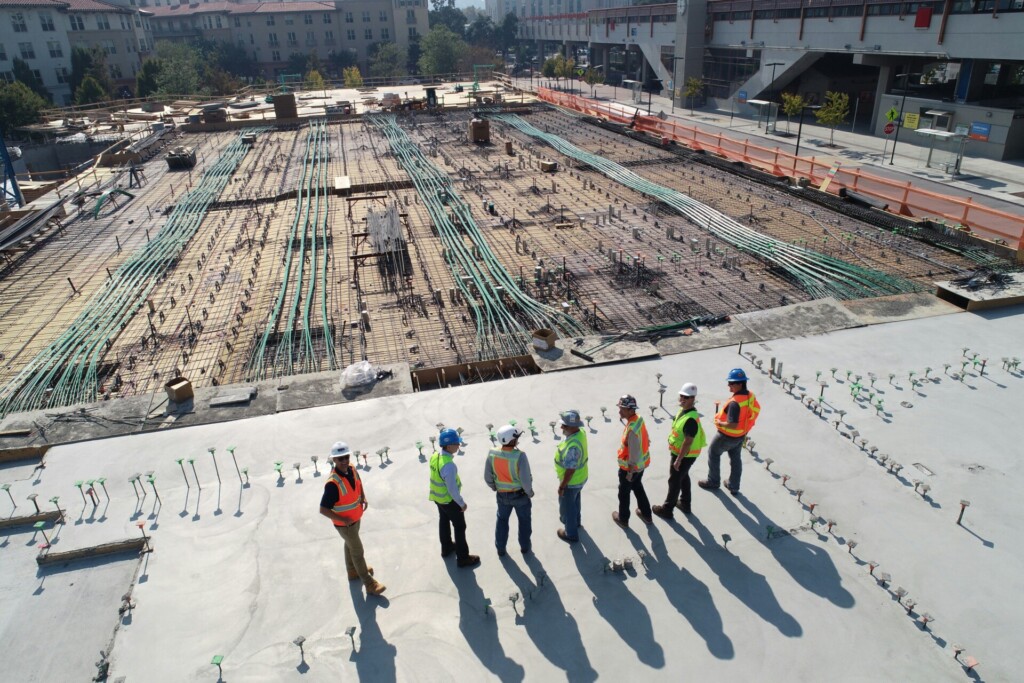
Geography can significantly influence price variations in commercial construction budgets across different regions. The cost disparities between regions can represent substantial differences, potentially impacting overall project viability. Understanding regional cost factors is crucial when assessing potential sites or considering expansion into new territories.
West Coast Construction Economics
On the West Coast, particularly in California, Oregon, and Washington, commercial projects may have higher budgets. Factors such as seismic requirements, limited urban space, and labor market conditions can influence costs. The local regulatory environment also plays a role—California”s Title 24 energy efficiency standards and local green building ordinances may add compliance costs that should be considered in budgets.
Material transportation costs can be higher along the West Coast, especially in areas with limited access or challenging terrain. Skilled trade costs in these markets typically reflect both the local cost of living and the specialized knowledge required for complex urban construction in seismic zones.
East Coast Market Conditions
Building along the Eastern Seaboard may require different budget considerations. Factors like labor requirements, logistics for material delivery in congested areas, and building codes can influence costs. Cities like New York, Boston, and Washington D.C. may have their own unique cost pressures.
East Coast projects may require additional considerations for interactions with older infrastructures, historic district requirements, and, in coastal areas, hurricane-resistant design elements. The density of urban centers can create logistical challenges that impact scheduling and costs—construction staging areas may be limited, and coordination with neighboring structures could require careful planning and additional protective measures.
Midwest Construction Considerations
The Midwest may offer different cost conditions for commercial construction. This region can benefit from factors such as land costs, permitting processes, and wage scales. Chicago may be an exception, with costs potentially more comparable to coastal cities due to its dense urban environment and labor market.
The Midwest can be advantageous for projects like distribution centers and manufacturing facilities where large footprints and good transportation access are essential. The region”s central location may reduce material transportation costs, and the availability of skilled labor without the extreme competition found in coastal markets can help manage staffing costs.
Southern States Cost Considerations
The Southern United States may offer a cost-effective construction environment. States like Texas, Florida, Georgia, and the Carolinas can benefit from year-round construction seasons and labor market conditions that may contribute to cost efficiency.
Building in Southern states can capitalize on extended construction seasons that may minimize weather delays. The warmer climate allows for continuous work throughout the year, potentially reducing inefficiencies that affect colder regions. This climate advantage could translate to shortened schedules and reduced general condition costs, providing a potential benefit for project owners concerned with time-to-market.
What Drives These Regional Cost Differences?
Several fundamental factors can contribute to geographic cost variations. Labor availability and wage rates may show regional differences, with metropolitan areas often commanding higher wages due to living costs. Material costs may vary less dramatically, but transportation expenses to remote locations can affect delivered prices.
Local building codes and regulatory requirements are important cost variables. States and municipalities with more stringent energy codes, accessibility requirements, or specialty inspections may add complexity and costs. Climate considerations are also important—approaches may need to be adjusted based on requirements for hurricane resistance in Florida, seismic resilience in California, or snow loads in the Northeast.
Competition among contractors and subcontractors can also influence pricing. Markets with fewer qualified builders may command premium prices, while areas with robust construction sectors may benefit from competitive bidding environments.
Strategic Approaches to Regional Cost Management
When working across regions, implementing strategies to manage cost variations is important. Early planning is essential—understanding the local regulatory landscape and building jurisdiction requirements can help prevent expensive surprises later. Assembling region-specific teams familiar with local conditions, codes, and subcontractor markets can be beneficial.
Material sourcing strategies may also vary by region. In some markets, locally sourced materials might reduce transportation costs and lead times, while in others, national supply agreements could offer better pricing. Value engineering may take on different characteristics in different regions; what makes financial sense in one state might not be optimal in another.
Understanding these regional variations allows for informed decisions about project location, scope, and timing. Incorporating this geographic knowledge into preconstruction services can help support owners in optimizing their investment regardless of where they choose to build.
What Strategies Can Reduce Commercial Construction Costs?
As general contractors, we understand the pressures of rising material prices and labor costs on development budgets. In today”s challenging market, several proven strategies can help reduce commercial construction costs without compromising quality or building performance. The right approach can help achieve substantial savings while maintaining project integrity and timelines.
Design-Build Integration
Implementing a design-build approach offers significant opportunities for cost reduction. By involving design and construction teams from the very beginning, communication gaps can be minimized and costly change orders often seen in traditional design-bid-build projects may be reduced. Integrated teams can identify potential constructability issues during the design phase when modifications are typically less costly compared to during construction.
This collaborative environment can foster innovation as architects, engineers, and construction managers work together to address design challenges with budget-conscious solutions. A streamlined process may reduce overall project timelines, potentially translating to labor savings and earlier revenue generation for property owners.
Coordinating these teams under one contract can establish clear accountability and create a unified approach to value engineering. With all parties aligned on the budget from the start, scenarios where impractical designs need costly redesigns after bids come in over budget may be avoided.
Leveraging Prefabrication and Modular Construction
Prefabrication has transformed approaches to commercial construction, offering the potential for consistent quality while reducing on-site labor costs. Prefabricated components like wall panels, bathroom pods, and MEP systems are often used. These elements are typically manufactured in controlled factory environments, which can help mitigate weather delays and reduce material waste.
The cost advantages can be substantial. By shifting work off-site, the number of trade workers needed on-site may be reduced, potentially minimizing scheduling conflicts and accelerating project timelines.
Beyond immediate savings, prefabrication can enhance quality control. Standardized production processes may result in fewer defects, potentially reducing punch list items and warranty issues that could impact the bottom line after project completion. The precision of factory-built components may also improve building envelope performance, potentially contributing to long-term operational savings.
Value Engineering Without Compromising Quality
Value engineering involves a systematic analysis to maximize function while minimizing unnecessary expenses. The process typically begins with a thorough examination of project specifications to identify opportunities where alternative materials or methods can deliver equivalent performance at lower costs.
Building systems can be evaluated holistically, recognizing that initial investments may yield savings elsewhere. For instance, upgrading the building envelope might allow for the downsizing of HVAC equipment, potentially resulting in net savings. Similarly, careful analysis of structural systems may reveal opportunities to optimize steel quantities without compromising integrity.
Material substitution is another valuable strategy. Relationships with suppliers can allow for recommendations of alternative products that meet performance requirements while potentially reducing costs. This might include substituting certain interior finishes or selecting equivalent mechanical equipment from different manufacturers.
Strategic Material Procurement
A material procurement strategy can focus on timing and volume. Market conditions can be monitored to identify potentially favorable purchasing windows for commodities like steel, concrete, and lumber, which may fluctuate significantly in price. For projects with flexible timelines, accelerating or delaying purchases to capitalize on market conditions may be considered.
Bulk purchasing agreements may generate savings, especially for projects with multiple phases or for owners with concurrent projects. Supplier relationships can be leveraged to negotiate volume discounts. For materials with long lead times, early procurement may help secure pricing and ensure availability, potentially protecting against inflation and supply chain disruptions.
Local sourcing can further reduce costs by minimizing transportation expenses and supporting quicker delivery timelines. A network of regional suppliers and fabricators may allow for efficient material sourcing while supporting the local economy.
Energy-Efficient Systems and Long-Term Savings
While energy-efficient building systems often have higher upfront costs, considering the total cost of ownership perspective can be beneficial. High-efficiency HVAC systems, enhanced insulation, and intelligent building controls may offer operational savings over time, potentially continuing to generate returns throughout the building”s lifecycle.
These systems can be evaluated using life-cycle cost analysis rather than focusing solely on initial investment. This approach may show how options with higher initial costs can prove more economical when maintenance, energy consumption, and longevity are considered. For developers planning to hold properties long-term, these savings may impact NOI and property valuation.
Apart from economics, energy-efficient buildings may command premium rents and experience lower vacancy rates. Tenants increasingly value sustainability features, and buildings with strong environmental credentials may enjoy competitive advantages.
Simplified Design Approaches
Simplifying building geometry can yield cost savings. Complex shapes with numerous corners, curves, or non-standard angles may increase material waste, require more labor, and often need custom fabrication. Rectilinear designs with standardized dimensions can optimize material usage and accelerate construction.
Standardizing elements like window sizes, door types, and fixture selections throughout a building creates opportunities for volume purchasing while simplifying installation. Limiting the variety of finishes and materials may not only reduce initial costs but also simplify maintenance and future replacements.
Utilizing these strategic approaches to commercial construction can help deliver projects that meet budget requirements without sacrificing quality or functionality. Thoughtful planning and integrated problem-solving may yield greater savings than arbitrary cost-cutting, aiming to ensure that buildings perform as intended while respecting financial constraints.
Conclusion: Planning Your Commercial Building Budget
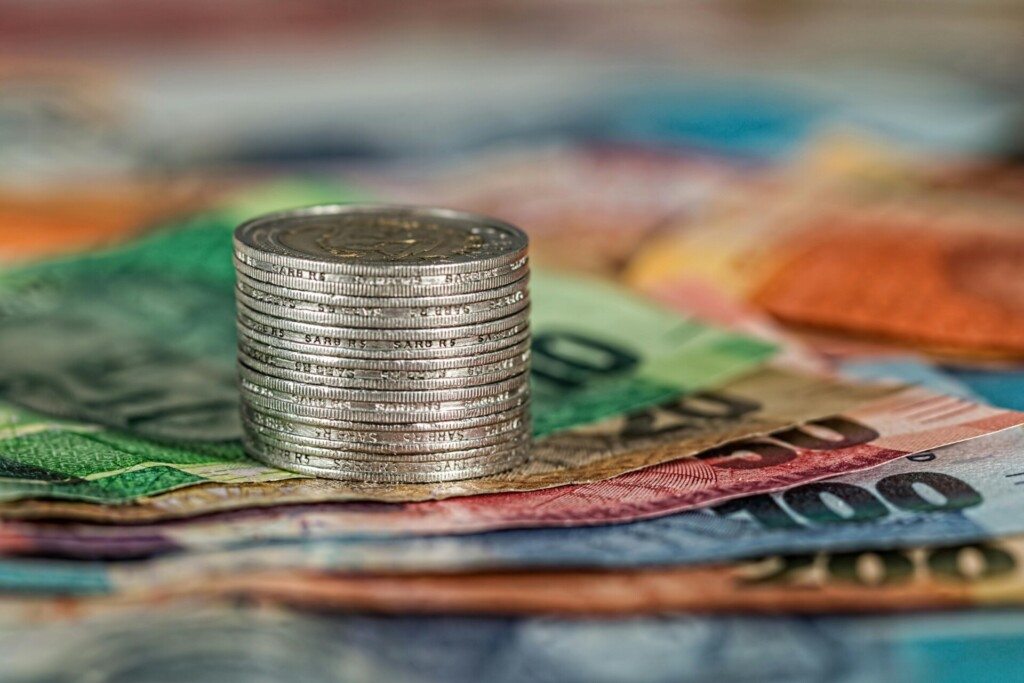
Planning a commercial building budget requires a thoughtful, multi-faceted approach grounded in market realities. A skilled general contractor can help clients understand the complexities of construction costs, which can vary widely depending on numerous factors. This substantial variance highlights the importance of early collaboration with an experienced professional familiar with the nuances of commercial construction economics.
Regional considerations often play a decisive role in budget planning. Projects in different areas of the country may face varying construction rates, with some regions potentially offering more affordable options while others command premium rates. The type of building also influences costs significantly. Basic warehouse projects may have lower price points, while healthcare facilities and museums, requiring specialized infrastructure, can involve higher costs. An effective approach involves open discussions of these variables from the outset, along with practical cost management strategies like value engineering, phased construction planning, and sustainable material selection that may deliver long-term operational savings.
Ready to develop a realistic commercial building budget that aligns with your project goals? Contact EB3 Construction to start the conversation.