Quality control isn’t just a box to check on Texas construction projects. It’s the backbone that ensures the structural integrity, occupant safety, and long-term durability of every building we construct. At its core, quality control represents a systematic approach implemented throughout the construction process to verify that all work meets or exceeds contractual requirements and established industry standards.
In Texas’s complex and often challenging building environment, we distinguish between two critical components: construction quality control (CQC) and construction quality assurance (CQA). As general contractors, EB3 Construction executes CQC through rigorous on-site verification processes, including daily inspections, material testing, and workmanship evaluations that catch potential issues before they become costly problems.
Meanwhile, CQA involves independent monitoring and third-party inspections that confirm our compliance with comprehensive quality management plans. This is particularly important in a state where extreme weather conditions, from Gulf Coast hurricanes to North Texas tornadoes, can test structural resilience.
What Regulatory Agencies Oversee Construction Quality in Texas?
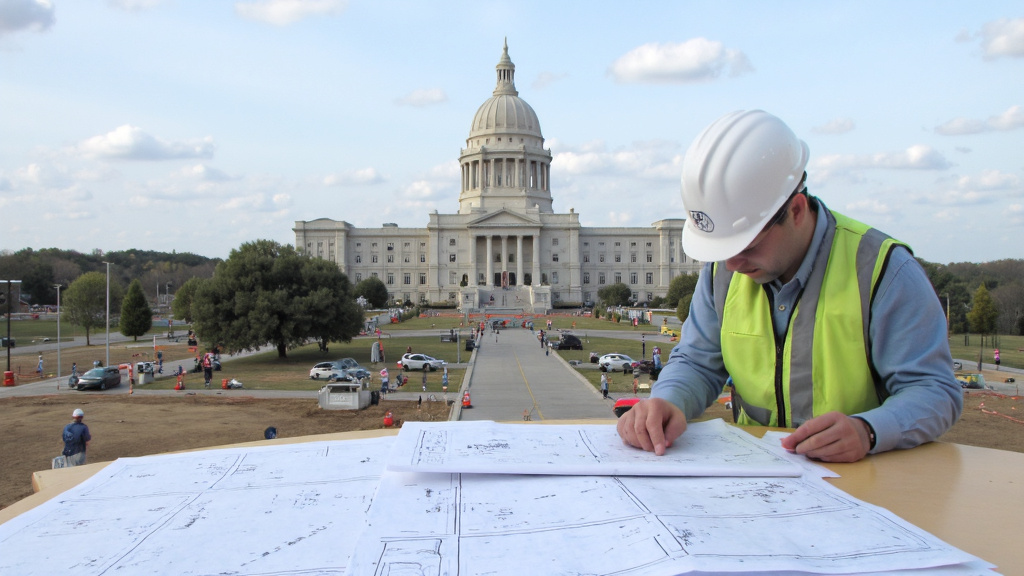
The construction industry in Texas operates under a robust regulatory framework to ensure safety, quality, and environmental compliance. As general contractors, we engage with multiple agencies that monitor different aspects of our work.
The Texas Department of Licensing and Regulation (TDLR) is a primary regulatory body for the construction industry, enforcing standards across numerous building trades. Their scope includes electrical work, accessibility compliance, and various specialty contracting areas affecting our operations and project planning.
Environmental Oversight and Compliance
The Texas Commission on Environmental Quality (TCEQ) serves as the state’s environmental guardian, focusing on water quality protection and waste management protocols at our construction sites. Their regulations significantly impact our sitework procedures, especially concerning stormwater pollution prevention plans and proper disposal of construction materials.
When developing properties near sensitive environmental areas, we implement comprehensive compliance strategies that align with TCEQ requirements. This oversight extends beyond paperwork—TCEQ field inspectors regularly visit active construction sites, particularly during earthwork phases when environmental impact risks are highest.
The Environmental Protection Agency (EPA) also maintains federal jurisdiction over certain aspects of construction, creating a dual layer of compliance requirements that we integrate into our project execution plans.
Fire Safety and Building Standards
The Texas State Fire Marshal’s Office enforces critical fire safety standards that influence our design-build approach for commercial and public buildings. Their requirements guide our material selections, emergency egress provisions, and fire suppression systems integration.
Local municipal authorities add another layer of quality control through their building departments, which enforce locally adopted versions of the International Building Code. The variation between jurisdictions means our teams must stay current with specific local amendments that may exceed baseline state requirements.
Through years of permitting experience, we’ve developed strong working relationships with these municipal inspection teams, facilitating smoother review processes while maintaining compliance with fire code provisions.
Industry and Trade-Specific Regulation
The Texas State Board of Plumbing Examiners regulates plumbing standards, ensuring that all installations meet health and safety requirements. This oversight directly impacts our mechanical coordination and quality control procedures for all water and waste systems.
The Occupational Safety and Health Administration (OSHA) maintains strict workplace safety standards that shape our daily site operations. Their enforcement authority extends to jobsite conditions, worker training, and hazard prevention measures that we integrate into every project phase.
The Texas Association of Builders works closely with elected officials and these regulatory agencies to develop construction standards that balance safety with practicality. This collaboration helps ensure regulations remain effective without creating unnecessary obstacles to efficient building practices.
Regulatory Agency | Jurisdiction | Impact on Construction |
---|---|---|
Texas Department of Licensing and Regulation (TDLR) | State | Enforces standards for electrical work, accessibility compliance, and specialty contracting |
Texas Commission on Environmental Quality (TCEQ) | State | Focuses on water quality protection and waste management at construction sites |
Environmental Protection Agency (EPA) | Federal | Maintains jurisdiction over environmental compliance |
Texas State Fire Marshal’s Office | State | Enforces fire safety standards influencing design-build approaches |
Occupational Safety and Health Administration (OSHA) | Federal | Sets workplace safety standards affecting jobsite conditions and worker training |
While navigating these overlapping jurisdictions presents challenges, we view regulatory compliance as a cornerstone of quality construction. Each agency plays a vital role in the ecosystem that ultimately protects building occupants, workers, and the environment. The collective oversight helps maintain Texas construction standards while allowing for innovation and growth within established safety parameters.
What Are the Key Components of Texas Construction Quality Control?
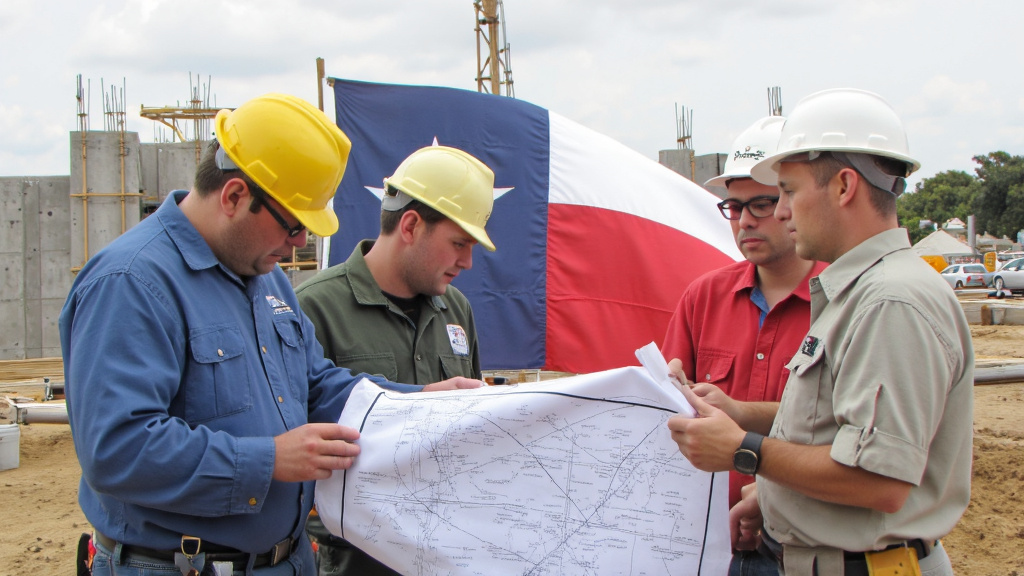
Quality control in Texas construction is the backbone of project integrity and compliance, comprising a strategic framework of inspections, material standards, and verification protocols. As experienced general contractors, we implement robust quality control measures that transform building codes from paper requirements into physical reality, ensuring every project we deliver meets or exceeds standards.
Independent Quality Assurance Framework
The cornerstone of effective construction quality control in Texas is independence. Under Texas Government Code requirements, governmental entities must separate quality verification from the design-build team, creating essential checks and balances. This separation ensures objectivity when evaluating materials and workmanship, particularly crucial on large-scale civil projects where public safety and investment protection are paramount.
We coordinate with independent quality firms (IQF) who report to both our management team and regulatory authorities. This dual reporting relationship maintains the integrity of testing while ensuring findings are properly addressed within the construction timeline.
Comprehensive Material Testing and Standards
Material testing forms the scientific foundation of quality construction. We enforce rigorous material standards through systematic sampling and testing protocols that verify the performance characteristics of key components, including:
- Concrete mix designs and compression strength testing
- Soil compaction and density verification
- Steel reinforcement tensile strength assessment
- Asphalt mixture composition and density testing
- Structural component load capacity verification
Each material category undergoes multiple testing phases—from pre-delivery qualification to post-installation verification—creating a continuous quality assurance chain. When material testing identifies non-conforming results, we implement a structured remediation process including engineering judgment evaluations or referee testing when discrepancies arise between quality control and verification testing.
Structured Inspection Protocols
Our inspection protocols follow a methodical approach that divides projects into critical inspection points. At each milestone, trained inspectors document compliance with plan specifications and applicable codes before work proceeds. This prevents costly rework and ensures quality issues are addressed when correction is most efficient.
We implement risk-based inspection planning—a prioritization tool that concentrates verification resources on components with higher failure consequences or historical quality challenges. This approach optimizes inspection coverage while maintaining comprehensive quality oversight.
Documentation Systems
Complete and accessible documentation serves as the permanent record of quality control efforts. Our documentation systems capture:
- Daily inspection reports submitted within 48 hours of work completion
- Material test results with clear pass/fail determinations
- Non-conformance reports (NCRs) with resolution pathways
- Engineering judgment logs for materials acceptance decisions
- Monthly material certification and quantities reports
These records provide real-time quality insights during construction while creating a traceable history for future reference. Properly maintained documentation also facilitates regulatory compliance verification and supports warranty claims management.
Verification Testing and Owner Oversight
Verification testing serves as the objective confirmation that contractor quality control measures are effective. The Owner Verification Firm (OVF) independently tests materials and inspects work according to a risk-based verification plan. This creates a statistical validation system that confirms the accuracy of quality control testing.
Three levels of verification are typically employed:
- Level 1: Statistical analysis of parallel test results
- Level 2: Independent verification of critical components
- Level 3: Observational verification for lower-risk elements
This tiered approach enables comprehensive verification coverage while focusing resources where they deliver maximum quality assurance benefit.
Continuous Improvement Through Auditing
Regular audits of quality control processes provide systematic feedback that drives improvement. Audits examine both procedural compliance and effectiveness, identifying potential weaknesses before they affect construction quality. TxDOT requirements specify at least annual audits of quality control activities and semi-annual audits of verification processes.
Our quality control systems incorporate audit findings through formal corrective action processes, creating a continuously improving framework that adapts to project-specific challenges and evolving construction practices.
Personnel Qualification Requirements
Construction quality control effectiveness ultimately depends on the people implementing it. Texas construction quality standards require rigorous qualification for testing and inspection personnel, including:
- Certification in specific test methods
- Written examination verification (minimum 80% passing score)
- Performance testing of laboratory procedures
- Regular requalification (every 3-5 years)
By employing inspectors and testers who meet or exceed these qualifications, we ensure that testing follows standardized procedures and produces reliable, consistent results across projects.
Implementing these quality control components creates a comprehensive system that delivers construction excellence while maintaining regulatory compliance—the foundation of successful, durable projects that stand the test of time.
How Are Quality Control Teams Structured in Texas Construction Projects?
When we build projects throughout Texas, establishing a robust quality control team is essential for regulatory compliance and project success. We implement a hierarchical structure that allows us to monitor every aspect of construction while maintaining clear lines of accountability from the ground up.
The core of our quality control structure begins with specifically designated roles required by Texas Government Code Section 2269.3615. This regulation mandates design-build firms to formally identify the companies and personnel who will occupy key project positions. We organize our teams with clearly defined responsibilities distributed among quality management professionals, technical specialists, and field personnel.
The Quality Management Leadership Trio
At the top level of our quality control structure, we establish three distinct leadership positions that form the backbone of our quality oversight approach:
The Quality Manager serves as the central authority for all quality-related decisions and documentation. This position reports directly to project executive leadership, maintaining independence from the production team to ensure unbiased quality assessments. Our Quality Managers have the authority to stop work when necessary to address non-conformance issues before they become costly problems.
Working alongside the Quality Manager, our Quality Control Management team focuses on preventative measures. They conduct pre-activity meetings, establish inspection points, and develop testing schedules that align with both project specifications and applicable Texas building codes. This proactive approach helps us identify potential issues before they impact construction progress.
Completing the trio, our Quality Assurance Management team provides independent verification that work meets the established quality standards. Unlike the QC team, which works within the production process, our QA personnel maintain organizational separation to ensure objective oversight. This dual-layer approach creates a system of checks and balances that has proven effective across our Texas projects.
Specialized Task Leaders for Technical Disciplines
Below the management level, we assign specialized task leaders to oversee quality in their respective technical areas. Texas projects often face unique challenges related to soil conditions, environmental factors, and strict regulatory requirements. Our specialized quality leads include:
Geotechnical Quality Leaders who monitor subsurface conditions, foundation work, and soil stabilization, particularly crucial in areas with expansive clay soils common throughout Central Texas. These specialists ensure that actual site conditions match design assumptions and make appropriate adjustments when variations are encountered.
Structural Quality Leaders who focus on concrete placement, steel erection, and connections—areas where quality lapses can have severe consequences. In regions prone to high winds along the Gulf Coast, these team members pay particular attention to hurricane-resistant construction details.
Environmental and Utility Quality Leaders who coordinate with regulatory agencies and ensure compliance with TCEQ requirements. With water conservation being a critical concern in Texas, these specialists verify that stormwater management systems and erosion controls are properly implemented according to permitted plans.
For public works and government projects, we also incorporate a Compliance Specialist who ensures adherence to all applicable Texas procurement and contracting requirements, particularly important when working with local jurisdictions that may adopt different amendments to base codes.
Field Implementation and Documentation
The operational level of our quality structure includes field inspectors, testing technicians, and documentation specialists who implement the quality program daily. These team members conduct required inspections at critical construction phases as specified by local building departments.
Our field quality personnel maintain detailed records of inspections, material certifications, and testing results—documentation that becomes increasingly important for government projects. When working in unincorporated areas where county authority may be more limited, we maintain the same rigorous documentation standards used in municipalities with comprehensive building departments.
To support our field personnel, we implement digital quality management systems that allow real-time reporting and resolution tracking. This technological approach helps us maintain transparency with clients and regulatory agencies while creating an auditable trail of quality activities.
Quality Team Integration with Project Partners
The effectiveness of our quality control team depends on clear communication with all project stakeholders. We establish formal interfaces between our quality personnel and:
The project’s design professionals, ensuring that field questions receive timely resolution and that any necessary design modifications maintain the original quality intent. This link is particularly important for the engineer of record who must review and approve construction documents before release, as required under Section 2269.365 of the Texas Government Code.
Subcontractors and trade partners, who develop their own quality control plans that integrate with our master program. We require specialized trades to designate quality representatives who participate in our coordination meetings and inspection processes.
Building officials and third-party inspectors who conduct code-mandated inspections. Our quality team schedules these inspections strategically to prevent workflow disruptions while ensuring all required approvals are obtained at the appropriate construction phases.
Role | Responsibilities |
---|---|
Quality Manager | Primary responsibility for quality assurance; reports directly to senior management to maintain independence; develops project standards; responsible for personnel evaluation and training. |
Project Manager | Overall responsibility for the construction project; integrates quality concerns into project goals; manages personnel, subcontractors, and suppliers. |
Superintendent | First line of quality assurance; applies company standards and customer requirements daily; works closely with Quality Manager and Safety Manager. |
Beyond meeting regulatory requirements, our quality team structure supports efficient project delivery. By detecting and addressing issues early, we reduce rework, minimize schedule impacts, and control costs. The investment in a comprehensive quality structure yields returns through improved productivity and reduced post-completion warranty items.
As each project presents unique challenges, we adapt our quality team structure to match specific requirements. For complex projects with compressed schedules, we might increase our field quality staffing to provide more frequent oversight. For specialized facilities like water treatment plants or healthcare projects, we incorporate subject matter experts with specific technical backgrounds relevant to those building types.
Continuous Improvement Process
Our quality teams don’t merely enforce standards—they drive continuous improvement. We conduct regular quality audits and analyze non-conformance trends to identify systematic issues. This data informs process improvements and training initiatives for our construction teams.
At project completion, quality personnel participate in lessons-learned sessions to document successful quality approaches and identify opportunities for future projects. This institutional knowledge becomes particularly valuable when working with repeat clients who expect continuous improvement in quality performance.
By structuring our quality teams with clear roles, responsibilities, and authority, we ensure that quality isn’t just an inspection function—it’s integrated into every phase of construction from preconstruction planning through project closeout. This comprehensive approach to quality management has proven essential for successful project delivery throughout Texas.
What Permit Requirements Affect Construction Quality Control in Texas?
Every construction project in Texas relies on regulatory compliance. As experienced builders, we understand that permits are not just bureaucratic hurdles—they form the essential framework for quality control in construction. Before breaking ground, we meticulously verify local regulations to ensure our projects align with each jurisdiction’s specific requirements.
The Texas construction landscape is governed by a patchwork of building codes that vary by municipality. These codes are not arbitrary—they represent carefully developed standards designed to protect public safety and ensure construction integrity. When we secure permits for our clients’ projects, we confirm that our construction plans meet or exceed these established quality benchmarks. This verification process serves as the first formal quality control checkpoint in the construction timeline.
Permit requirements typically encompass structural integrity, fire safety provisions, accessibility standards, and environmental considerations. The Texas Commission on Environmental Quality (TCEQ) plays a significant role in regulating environmental aspects, particularly water quality and waste management during construction. Similarly, the Texas State Fire Marshal’s Office enforces critical fire safety standards in commercial and public buildings—a matter we take extremely seriously in all our construction projects.
While specific permit requirements vary between cities like Houston, Dallas, and Austin, the fundamental purpose remains consistent: establishing minimum quality standards before construction begins. For larger projects, we often navigate multiple permit types, from general building permits to specialized electrical, plumbing, and mechanical approvals. Each represents a specific quality control milestone in the pre-construction phase.
Quality Assurance Through the Permitting Process
The permit application process serves as a comprehensive quality review. When we submit construction documents for approval, local building officials conduct thorough examinations of our plans, checking for code compliance and identifying potential issues before they manifest on the jobsite. This independent verification adds an invaluable layer of quality assurance to our internal quality control processes.
For design-build projects, quality control requirements are often explicitly stated in the permit documentation. According to Texas Government Code Chapter 2269, which governs contracting procedures for construction projects, quality assurance and quality control requirements must be specified in the design criteria package. This legal framework ensures that QA/QC considerations are integrated from the earliest stages of project development.
We find that municipalities increasingly require detailed quality control plans as part of the permit application, especially for complex or high-value projects. These plans typically detail inspection schedules, testing procedures, and verification methodologies—essentially documenting how we’ll maintain quality throughout the construction process. By developing these plans during permitting, we establish clear quality benchmarks that guide our entire construction approach.
The permitting process also necessitates the designation of qualified personnel for key quality control functions. For design-build contracts, Texas law allows governmental entities to require the identification of specific team members who will fulfill quality control and quality assurance management roles. This requirement ensures that qualified professionals oversee critical quality functions throughout construction.
City | Quality Control Requirement | Description |
---|---|---|
San Antonio | Construction Verification | Rigorous on-site verification processes including daily inspections and material testing |
Dallas | Air Quality Regulation | Subject to intensified federal oversight due to air quality concerns |
Houston | Mid-Shift Quality Control | Quality control roles require physical activities and lifting requirements |
Compliance Consequences and Quality Implications
Failing to obtain proper permits carries significant consequences beyond potential fines and stop-work orders. When construction proceeds without permits, it bypasses the essential quality verification steps embedded in the permitting process. We’ve witnessed firsthand how unpermitted work frequently results in costly corrections, delays, and even complete rebuilds when discovered by authorities.
More concerning are the long-term quality implications. Unpermitted construction lacks the independent verification that helps identify potential defects or code violations. These issues may remain hidden for years, potentially leading to structural problems, safety hazards, or system failures down the line. For property owners, unpermitted work can create significant liability exposure and complications during future property transfers.
Beyond the initial permits, ongoing inspections form the backbone of construction quality control. These inspections—typically occurring at foundation, framing, mechanical/electrical/plumbing rough-in, and final stages—provide independent verification that the constructed work matches the permitted plans and meets code requirements. We coordinate closely with local building officials to schedule these inspections at optimal points in the construction sequence.
The relationship between permits and quality control extends throughout the construction process. Each inspection milestone serves as a quality checkpoint, providing opportunities to identify and address issues before they’re covered by subsequent work. This progressive verification approach helps us maintain quality standards while moving efficiently toward project completion.
Permit Requirements for Specialized Construction
Specialized construction types often carry additional permit requirements that directly impact quality control practices. For healthcare facilities, Texas requires specific permits addressing infection control, life safety, and medical gas systems. Similarly, educational facilities must meet stringent requirements related to occupant safety and emergency systems. We navigate these specialized requirements regularly, incorporating their quality standards into our comprehensive construction approach.
For renovation projects involving existing structures, permit requirements often address lead, asbestos, and other hazardous materials—matters directly related to construction quality and safety. Our permit planning includes thorough assessment of these considerations, ensuring that remediation and abatement procedures meet or exceed regulatory standards.
Energy code compliance represents another increasingly significant permit requirement affecting construction quality. Texas has adopted energy conservation codes that mandate specific performance standards for building envelopes, HVAC systems, and lighting. These requirements necessarily influence material selections, installation methods, and quality control procedures during construction.
Recent updates to Texas building codes have placed increased emphasis on resilience to extreme weather events, particularly in coastal regions. These heightened standards translate to more robust construction methods and enhanced quality control procedures for structural elements, roof systems, and building envelopes. As builders, we welcome these standards as they align with our commitment to delivering durable, high-performance structures.
Conclusion: Effective Quality Control for Texas Construction Success
As construction methods and materials continue to evolve, so must our quality control practices. Forward-thinking contractors are increasingly implementing digital documentation systems that create real-time verification trails and establishing comprehensive material tracking protocols to ensure regulatory compliance from source to installation.
These innovations help us not only meet current standards but prepare for the increasingly stringent requirements that will shape Texas construction in the years ahead.
At its core, quality control represents the most fundamental promise we make to our clients and communities—that the structures we build will perform as designed, protecting lives and property for decades to come. By investing in thorough quality verification systems today, we deliver buildings and infrastructure that will stand as testaments to construction excellence long into the future.
For your next Texas construction project, contact EB3 Construction to discuss how our quality-first approach can deliver lasting value for your development.