When starting a construction project in Texas, success begins long before the first shovel hits the ground. A pre-construction checklist serves as a foundational roadmap that guides developers and property owners through the complex requirements that must be satisfied before construction can legally commence.
These comprehensive documents vary significantly across Texas municipalities—from the detailed requirements in Grapevine to the streamlined processes in Westlake. Each checklist reflects local building codes, environmental considerations, and regulatory frameworks unique to that jurisdiction. Developers navigating multiple Texas markets must pay careful attention to these variations to ensure compliance in each locale.
Beyond regulatory compliance, these checklists represent the critical planning phase that can determine a project’s timeline, budget, and ultimate success. They consolidate essential administrative approvals, technical assessments, and documentation requirements that, when properly addressed, allow construction to proceed smoothly from conception to completion.
What Documentation Must Be Prepared Before Construction?
Starting construction in Texas involves more than just bringing equipment and materials. We manage a comprehensive documentation process that confirms project legitimacy, ensures safety compliance, and provides a construction roadmap. Each document serves a distinct purpose within the regulatory framework governing construction in Texas.
Core Documentation Requirements
Every construction project in Texas starts with proper site documentation. We file plats at the county courthouse to establish legal boundaries and property details before any work begins. These documents become permanent public records that define the project’s physical footprint and ownership status.
Site plans require thorough approval from local Development Services departments. These plans illustrate the layout design, including building placement, landscaping, parking configuration, and drainage solutions. The approval process often involves multiple reviews and potential revisions before receiving the necessary green light.
Construction plans must carry the crucial “Released for Construction” stamp to be considered valid. These technical documents typically need specific formatting and submission in multiple copies. We ensure these plans detail structural components, electrical systems, plumbing configurations, and mechanical elements with precision that satisfies local building authorities.
Safety and Traffic Management Documentation
Construction inevitably impacts surrounding areas, requiring specialized documentation for public safety. Barricade and traffic control plans detail how we manage vehicle and pedestrian flow around the construction site. These plans must comply with the Texas Manual on Uniform Traffic Control Devices, with requirements varying based on project scope and proximity to public thoroughfares.
Trench safety plans have become essential following the Texas Trench Safety Act. We develop comprehensive documentation outlining protective systems and safety protocols for any excavation exceeding five feet in depth. These plans incorporate OSHA standards and address specific soil conditions at the project site.
Conditional Documentation Requirements
Projects near state highways require Texas Department of Transportation (TXDOT) permits. The application process includes detailed explanations of how construction activities might affect state-maintained roadways. Similarly, developments impacting watershed areas require Trinity River Authority (TRA) permits to ensure proper environmental protections.
When construction impacts neighboring properties, we secure indemnification letters and offsite easement documentation. These legal instruments protect both project owners and adjacent property holders by clarifying access rights and liability limitations during the construction phase.
Properties in flood-prone areas require Federal Emergency Management Agency (FEMA) documentation. These submissions may include elevation certificates, floodproofing certificates, or No-Rise certifications depending on the specific flood designation. The recent implementation of updated FEMA flood maps across Texas has made this documentation increasingly important for new developments.
“Fill” agreements document plans for importing soil to alter site elevation, particularly crucial in areas with drainage concerns. These agreements specify the type, quantity, and source of fill material, along with compaction requirements to ensure structural stability for future building foundations.
Documentation Sequencing and Submission
The order of document submission is crucial. We typically secure plat approvals first, followed by site plan endorsements. Construction plans usually come next, with specialty permits and agreements finalized before breaking ground. This sequential approach prevents costly rework and regulatory complications.
Most Texas municipalities now offer digital submission options, streamlining the process compared to the traditional paper-based approach. However, many jurisdictions still require hard copies of final approved plans to be maintained onsite during construction for reference during inspections.
Documentation requirements can vary significantly between urban centers like Houston or Dallas and smaller municipalities. For instance, metropolitan areas typically impose more stringent traffic control documentation requirements than rural communities, reflecting their higher density and complex infrastructure.
What Site Preparation Requirements Must Be Met?
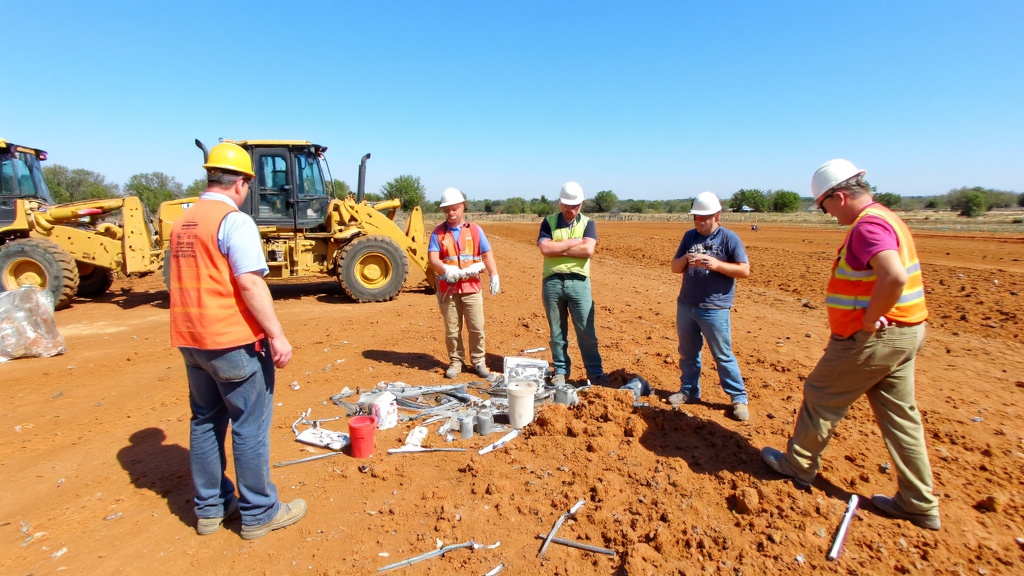
Breaking ground in Texas involves significant regulatory considerations. As a general contractor, we understand that proper site preparation not only ensures compliance but also protects the environment and prevents costly delays. Before mobilizing equipment, we must implement several critical measures to meet state and federal requirements.
Erosion Control Implementation
The cornerstone of compliant site preparation is effective erosion control. Before any soil is disturbed, we install perimeter protection, including properly trenched silt fencing that follows the site’s contours. This crucial first step prevents sediment-laden runoff from leaving the construction area and potentially contaminating nearby waterways, which would violate the Clean Water Act.
For sites larger than one acre, we develop a Stormwater Pollution Prevention Plan (SWPPP) as required by the Texas Commission on Environmental Quality (TCEQ). This plan is our roadmap for managing stormwater throughout the project lifecycle. The SWPPP documents our best management practices (BMPs), identifies potential pollution sources, and establishes our inspection and maintenance protocols.
Site entrances require stabilization with bull rock or crushed stone to create a sediment-trapping transition zone. These entrances typically extend at least 50 feet from public roads and must be maintained throughout construction to prevent tracking soil onto roadways. Proper installation reduces street cleaning requirements and minimizes complaints from neighboring properties and local authorities.
Material Management and Clean Water Act Compliance
The Clean Water Act Section 402 establishes the National Pollutant Discharge Elimination System (NPDES), administered in Texas through the TPDES Construction General Permit. This regulatory framework demands proper management of all materials on site, particularly soil stockpiles. We cover these stockpiles with geotextile fabrics or plastic sheeting when not in use, especially before anticipated rainfall.
For concrete operations, we establish designated washout areas that are properly lined and maintained. These containment systems prevent highly alkaline concrete washwater from contacting soil or stormwater, which can cause serious environmental damage. All chemical containers, fuels, and potentially hazardous materials must be stored in secondary containment with proper covers or shelters to prevent stormwater contact.
Site Identification and Permitting
Proper site identification is more than a formality—it’s a compliance requirement. We install temporary address boards in visible locations with lettering at least 4 inches high, ensuring emergency responders can easily locate the site. All required permits, including the site notice for TPDES coverage, must be displayed in weather-resistant enclosures visible from the street.
For large construction activities disturbing 5 or more acres, we submit a Notice of Intent (NOI) to TCEQ and receive authorization before beginning any work. This documentation must remain on site and accessible during inspections, along with the SWPPP and any local permits. The potential penalties for non-compliance—up to $32,500 per day per violation—make proper permitting a critical priority.
Tree Protection and Natural Resource Conservation
Before clearing begins, we identify protected trees and implement the required protection measures according to local ordinances. This typically involves installing sturdy fencing at the drip line of designated trees and clearly marking protected areas. These protection zones must remain untouched by equipment, materials, or any construction activity.
In environmentally sensitive areas or sites near waterways, additional buffer zones may be required to protect natural resources. We work closely with environmental consultants to identify these areas early in the planning process, ensuring our site preparation accounts for all necessary conservation measures.
Site Management and Waste Control
Effective waste management begins with the first day of site preparation. We establish designated areas for material storage, equipment staging, and waste collection that minimize environmental impact. Each site must have appropriate waste containers with secure lids to prevent wind-blown debris and contaminated runoff.
Portable sanitation facilities are installed in locations that minimize the risk of spillage while providing necessary access for service vehicles. These facilities are secured to prevent tipping during high winds and are regularly maintained throughout the project.
Regular site inspections—typically every 14 days and within 24 hours after rainfall events of 0.5 inches or greater—are conducted to verify that all controls remain effective. We document these inspections as required by the SWPPP, making necessary repairs or modifications promptly to maintain compliance.
The careful orchestration of these site preparation requirements creates the foundation for a smooth-running, compliant construction project. By addressing these measures before breaking ground, we protect not only the environment but also the project schedule and budget from the significant disruptions that can result from regulatory violations.
What Inspections and Fees Are Required?
Construction projects in Texas require navigating a complex landscape of inspections and fees to ensure compliance with state regulations. As general contractors, we coordinate these requirements daily, serving as the crucial interface between regulatory demands and project execution. Understanding when inspections occur and how fees are structured helps prevent costly project delays and budget surprises.
Required Inspections
When managing Texas construction projects, we coordinate multiple inspection phases that verify code compliance throughout the building process. Outside municipal jurisdictions, builders must contract with approved third-party inspectors, while projects within city limits follow local inspection protocols.
For projects outside municipal boundaries, we typically coordinate three mandatory inspection phases:
- Foundation Inspection – Occurs after forms are constructed and reinforcement is installed, but before concrete is poured
- Set Inspection – Performed when modules are connected and fastened to the foundation
- Final Inspection – Conducted when utility services are connected and all required tests are performed
The Texas Department of Licensing and Regulation (TDLR) requires that foundation inspections be documented thoroughly. When building outside city limits, we engage Texas-registered third-party inspectors or licensed engineers to verify compliance. Each inspection must be completed within prescribed timeframes, with the final inspection typically required within 180 days of construction start.
Common Construction Fees
Fee structures vary across Texas municipalities, but several categories remain consistent. We factor these into our project planning to ensure appropriate budgeting:
Plan Review and Permit Fees: These costs vary by construction value. For projects under $50,000, we typically budget approximately $515 for plan review and an additional $515 for inspection fees. For mid-sized projects between $50,000-$200,000, these fees increase to about $695 each. Larger projects between $200,000-$500,000 generally require about $745 per review or inspection.
Beyond basic permit costs, we also account for specialized fees that affect the project budget:
- TDLR Project Filing Fees – Currently $175 due at the time of plan review
- Mileage/Travel Fees – Typically calculated at $0.65 per mile for inspector travel
- Preliminary Site Inspection Fees – Variable based on project complexity
- Variance Application Fees – $175 per variance request
Remedial Actions and Additional Costs
When construction doesn’t meet initial inspection requirements, we manage remediation processes that involve additional inspections and documentation. Compliance failures regarding foundation requirements typically require engaging a Texas-licensed engineer to evaluate and inspect the foundation system, preparing a detailed report with specific recommendations.
These remedial actions include specific documentation components we must coordinate:
- Engineer’s name, Texas license number, and seal
- Complete builder information including registration numbers
- Detailed installation address information
- Serial numbers and identification details for all modules
- Comprehensive description of existing conditions
- Professional recommendations for compliance measures
Missing inspections or failing to address remedial requirements can result in administrative penalties up to $5,000 per violation per day, significantly impacting project economics.
Municipal vs. Non-Municipal Requirements
The fee and inspection structure differs significantly between municipal and non-municipal jurisdictions. Within city limits, we work directly with local building officials who enforce municipal requirements. Projects outside municipal boundaries follow TDLR protocols requiring third-party inspectors.
For residential construction, Texas law mandates permanent foundations and specific inspection protocols. We’ve found this particularly important when coordinating industrialized (modular) housing projects, which must meet the same inspection standards as traditional site-built construction despite their different manufacturing process.
Understanding these nuanced requirements allows us to streamline the construction process and deliver compliant, high-quality structures that meet both regulatory standards and client expectations.
What On-Site Requirements Must Be Maintained During Construction?
Managing a compliant construction site in Texas demands meticulous attention to documentation and safety protocols. As the general contractor, we maintain continuous oversight of these requirements throughout the project lifecycle to ensure smooth inspections and avoid costly delays.
Documentation and Plan Accessibility
We keep stamped, approved construction plans accessible on-site at all times, not just as a regulatory checkbox but as a critical reference point for our field teams and inspectors. When design modifications become necessary, we coordinate formal approvals before implementation to avoid violations from unauthorized field changes.
Building permits remain prominently displayed until final occupancy is granted. This simple requirement serves multiple purposes: validating our authorization to work, identifying the scope of approved construction, and providing inspectors with necessary reference information when they arrive on site.
Daily logs and inspection records are maintained in weatherproof containers at designated locations, creating an accessible history of the project for both our team and regulatory officials. Clear job site addressing visible from the street ensures emergency responders can quickly locate the site when needed.
Safety and Emergency Access Provisions
Construction safety extends well beyond OSHA compliance. We strategically position materials and equipment to maintain mandated clearances around fire safety infrastructure. This includes maintaining unobstructed access to fire hydrants (minimum 3-foot clearance), standpipes, and fire department connections.
Emergency vehicle access routes remain navigable throughout construction, with temporary measures implemented when permanent access is disrupted. According to Texas Department of Licensing and Regulation standards, we maintain minimum clearances of 10 feet from overhead power lines for all equipment operations, preventing potentially catastrophic accidents.
Our site safety officers conduct daily inspections of temporary guardrails, floor opening protections, and other fall prevention measures as required by Texas safety regulations. These proactive assessments help us maintain compliance while preventing worker injuries that could delay project timelines.
Requirement | Description |
---|---|
Overhead Power Line Clearance | Maintain at least 10-foot clearance from overhead power lines for equipment operations. |
Fire Safety Infrastructure | Maintain unobstructed access to fire hydrants (minimum 3-foot clearance), standpipes, and fire department connections. |
Emergency Vehicle Access | Keep emergency vehicle access routes navigable throughout construction. |
Safety Inspections | Conduct daily inspections of temporary guardrails, floor opening protections, and other fall prevention measures. |
Code Compliance for Accessibility Features
We maintain strict adherence to Texas Accessibility Standards (TAS) throughout the construction process. Temporary pathways are constructed with appropriate slopes, stable surfaces, and adequate width to accommodate equipment while meeting accessibility requirements.
Particular attention is given to critical dimensions for accessibility features like ramps (1:12 maximum slope), door clearances (minimum 32 inches), and level landing areas (minimum 60 inches). These measurements are verified regularly against the approved plans to ensure accuracy during construction.
Where construction activities might temporarily impact accessibility, we implement alternative routes that maintain compliance. This comprehensive approach to accessibility during construction addresses both current regulatory requirements and the practical needs of all site visitors.
Environmental Controls and Neighborhood Considerations
Our erosion control measures are inspected daily and after significant rainfall, with repairs made immediately to maintain compliance with Texas Commission on Environmental Quality (TCEQ) standards. Proper installation and maintenance of silt fencing, inlet protection, and stabilized construction entrances prevent regulatory violations while demonstrating our commitment to responsible site management.
Construction noise is restricted to permitted hours as established by local ordinances, typically between 7 AM and 7 PM on weekdays in most Texas municipalities. We monitor and adjust work schedules accordingly, particularly in sensitive areas near hospitals, schools, or residential neighborhoods.
Dust control measures, including site watering and wind screens, are implemented based on current conditions to minimize particulate generation. This proactive approach reduces air quality concerns while maintaining visibility for safe equipment operations on larger sites.
Conclusion: Navigating Texas Pre-Construction Requirements Successfully
Successfully managing the intricate web of Texas pre-construction requirements requires meticulous attention to detail and thorough preparation. We have observed that comprehensive upfront planning prevents costly disruptions during active construction phases. Our approach focuses on understanding specific municipal checklists for documentation, coordinating site preparation logistics, scheduling timely inspections, budgeting for variable fees, and implementing proper on-site compliance measures—critical components for efficiently transitioning your project from planning to breaking ground.
While requirements vary across Texas municipalities depending on jurisdiction, project scope, and zoning classifications, the fundamental principle remains consistent: early engagement with regulatory frameworks saves time and resources.
We understand that each development project faces unique challenges, which is why we emphasize building relationships with local authorities, maintaining extensive documentation throughout the permitting process, and staying current with evolving building codes. When these pre-construction requirements are properly addressed, your project gains momentum from a solid foundation of regulatory compliance and operational readiness.
Ready to tackle the complexities of Texas construction requirements with confidence? Contact EB3 Construction to ensure your next project starts on solid regulatory ground.