Starting a construction project typically involves months of on-site activity with crews, equipment, and materials facing weather delays and site constraints. Modular construction changes this approach significantly. We construct about 60-90% of the structure in a controlled factory environment, using the same materials and adhering to the same building codes as conventional construction but with greatly reduced timelines.
At EB3 Construction, we’ve experienced how this construction methodology transforms the building process. Instead of following the linear sequence of traditional construction, we simultaneously prepare the site foundation while fabricating building modules off-site. These precisely engineered components arrive at the project location ready for final assembly and integration—a coordinated process that can reduce overall timelines by 30-50% compared to conventional methods.
The real innovation lies in maintaining quality while speeding up delivery. Each module undergoes rigorous quality control inspections during fabrication, ensuring structural integrity before it reaches the site. When assembled, these modules create buildings indistinguishable from traditionally constructed facilities but offer developers and property owners significant advantages in scheduling, cost control, and risk management.
What Are the Types of Modular Construction Methods?
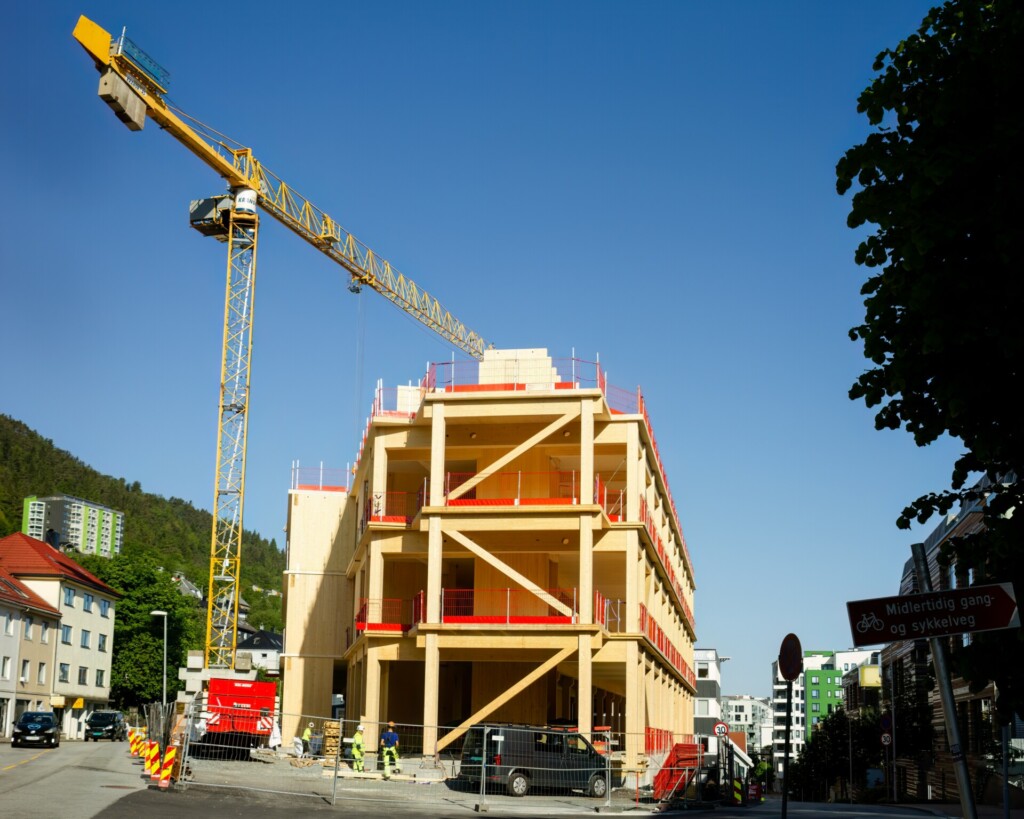
The modular construction landscape includes several distinct methodologies, each with unique applications and advantages for developers and property owners. At EB3 Construction, we implement these approaches across various projects, adapting our strategy based on client requirements, site conditions, and long-term objectives.
Permanent Modular Construction (PMC)
PMC is a well-established approach in the prefabrication spectrum. We design and construct these modules for fixed locations, manufacturing them in controlled factory environments before transporting them to the final building site. This method has gained significant traction, contributing to the projected growth of the modular market from $104.1 billion to $140.8 billion by 2029.
When implementing PMC solutions, we focus on durability and permanence. These structures adhere to the same building codes as traditional construction while offering superior quality control through the factory production process. Modules are set on permanent foundations, creating buildings indistinguishable from conventional construction but with faster completion timelines and reduced site disruption.
Relocatable Buildings (RB)
Unlike their permanent counterparts, relocatable buildings offer flexibility that many of our clients find invaluable for temporary or transitional needs. We engineer these structures for disassembly, transportation, and reuse across multiple locations, making them particularly valuable in fast-changing environments or where future relocation might be necessary.
The construction of RBs involves robust engineering that can withstand repeated transportation while maintaining structural integrity. We often deploy these solutions for clients needing swing space during renovations, temporary office facilities at construction sites, or educational spaces during campus expansions.
Volumetric Modular Construction
Volumetric construction is the most comprehensive form of modular building we offer. We fabricate complete three-dimensional room modules—including finishes, fixtures, and MEP systems—in the factory environment. These modules arrive at the job site at approximately 80-90% completion, requiring only final connections and minimal on-site work.
The primary advantage of volumetric construction is the significant acceleration of project timelines. By coordinating factory production with site preparation, we can deliver buildings 30-75% faster than traditional methods. This approach is particularly effective for repetitive layouts like hotels, multi-family housing, and healthcare facilities.
Panelized Modular Construction
In panelized construction, we produce large, flat components—walls, floors, and roof sections—in factory settings, then transport them to the site for assembly. While less complete than volumetric modules upon arrival, these panels incorporate insulation, sheathing, windows, and often interior finishes, streamlining the on-site construction process substantially.
The panelized method offers greater design flexibility than fully volumetric approaches while still providing significant efficiency gains. We employ this technique on projects where site access constraints would have made volumetric module delivery challenging or where more customized architectural expressions were required without sacrificing the benefits of prefabrication.
Modular Type | Duration of Use | Materials | Design Flexibility | Construction Duration |
---|---|---|---|---|
Permanent Modular Construction (PMC) | Long-term | Wood, steel, concrete | High | Months |
Relocatable Buildings (RB) | Short-term | Wood | Limited | Weeks |
Volumetric Modular Construction | Varies | Wood, steel | Moderate | 30-75% faster |
Panelized Modular Construction | Varies | Wood, steel | Higher than volumetric | Faster than traditional |
Hybrid Modular Approaches
The most sophisticated projects we undertake often involve hybrid approaches that combine different modular techniques with selective site-built elements. For example, we might utilize volumetric modules for repeatable elements like bathrooms and kitchens, panelized construction for the building envelope, and traditional methods for unique architectural features or complex systems.
This integration of methods allows us to optimize for efficiency without sacrificing design intent. The flexibility of hybrid approaches proves particularly valuable when working with existing structures or on sites with unusual constraints that require creative construction solutions.
By evaluating project requirements against the strengths of each modular methodology, we develop tailored strategies that maximize the benefits of offsite fabrication while meeting the specific needs of the development. The modular spectrum offers solutions ranging from fully relocatable to permanent structures, with varying degrees of prefabrication and on-site assembly—all contributing to faster schedules, improved quality control, and more predictable outcomes.
What Are the Key Benefits of Modular Construction?
In construction today, where tight schedules and budget constraints are common, modular construction has emerged as a transformative approach for developers and property owners. At EB3 Construction, we’ve seen how modular methods are revolutionizing project delivery, offering substantial advantages that traditional construction can’t match.
Accelerated Project Timelines
When NYC developers faced critical housing shortages after Superstorm Sandy, modular construction provided the solution—delivering essential housing units in half the time of conventional methods. This speed results from a fundamentally different construction approach.
We execute up to 80% of the building process in controlled factory environments while simultaneously conducting site work. This parallel processing eliminates the sequential delays inherent in traditional construction, allowing us to deliver projects 30-50% faster. For developers, this means quicker occupancy, earlier revenue streams, and reduced financing costs.
Weather delays, the bane of conventional construction, become largely irrelevant with modular methods. Our teams coordinate production schedules with precision, drastically reducing the typical waiting periods between construction phases.
Superior Quality Through Controlled Manufacturing
The precision advantage of modular construction cannot be overstated. We build in environments where temperature, humidity, and lighting are optimized—conditions that site-built projects can only dream of. This controlled setting allows for exceptional quality control, with specialized teams focusing on specific assembly aspects.
Every module undergoes rigorous QA/QC protocols at multiple production stages, resulting in consistent quality that surpasses what’s typically achievable on-site. Precision tools and standardized processes ensure tight tolerances and proper fit between components, minimizing the rework that often plagues traditional construction.
The result? Buildings with fewer defects, better performance characteristics, and reduced warranty claims—outcomes that reflect directly on your reputation as a developer or property owner.
Significant Cost Advantages
We regularly deliver cost savings of 15-20% compared to traditional construction methods. These savings stem from shorter project durations that reduce labor costs, financing expenses, and general conditions. Material waste drops dramatically in factory settings—typically 90% less than conventional site-built projects, according to WRAP studies.
The efficiency gained through repetitive processes and specialized labor means your budget stretches further. Bulk material purchasing at the factory level provides economies of scale that individual projects rarely achieve. Additionally, the controlled environment virtually eliminates expensive weather-related damages and delays.
Even better, the predictability of modular construction means fewer change orders and greater cost certainty—a critical factor for developers navigating tight financing conditions.
Enhanced Environmental Performance
Building sustainability isn’t just good practice—it’s increasingly mandated by regulations and expected by stakeholders. Modular construction inherently supports these goals. We reduce construction waste by up to 90% through precise material ordering and efficient factory processes, diverting substantial volume from landfills.
Our factory-built components incorporate energy-efficient systems more effectively than field-constructed elements. The controlled setting allows for tighter building envelopes, more consistent insulation installation, and better overall thermal performance. Site disturbance is minimized, with fewer deliveries, reduced equipment needs, and shorter on-site construction periods.
For developers targeting green building certifications like LEED, these inherent sustainability advantages provide valuable points with minimal additional investment.
Improved Safety Protocols
Worker safety fundamentally improves when we shift 80% of construction activities to controlled factory environments. We eliminate many high-risk activities that traditionally occur at height or in challenging site conditions. The factory setting provides ergonomic workstations, proper lighting, and consistent safety protocols that significantly reduce accident rates.
This safety advantage translates directly to reduced insurance costs, fewer work stoppages, and improved project predictability. For property owners and developers, it means fewer liability concerns and a reduced risk profile for the entire project.
The reduced on-site construction presence also minimizes community disruption—a critical consideration when working in dense urban environments or occupied campus settings where stakeholder goodwill is essential.
Flexibility and Future Adaptability
We design modular systems with change in mind. Buildings constructed using modular methods can be more easily reconfigured, expanded, or repurposed as needs evolve. This adaptability provides significant long-term value for owners whose space requirements may change over time.
The standardized nature of modular components facilitates future modifications without the extensive demolition and reconstruction typically required in traditional buildings. For property owners considering a building’s full lifecycle costs, this adaptability represents substantial value beyond the initial construction phase.
What Challenges Does Modular Construction Face?
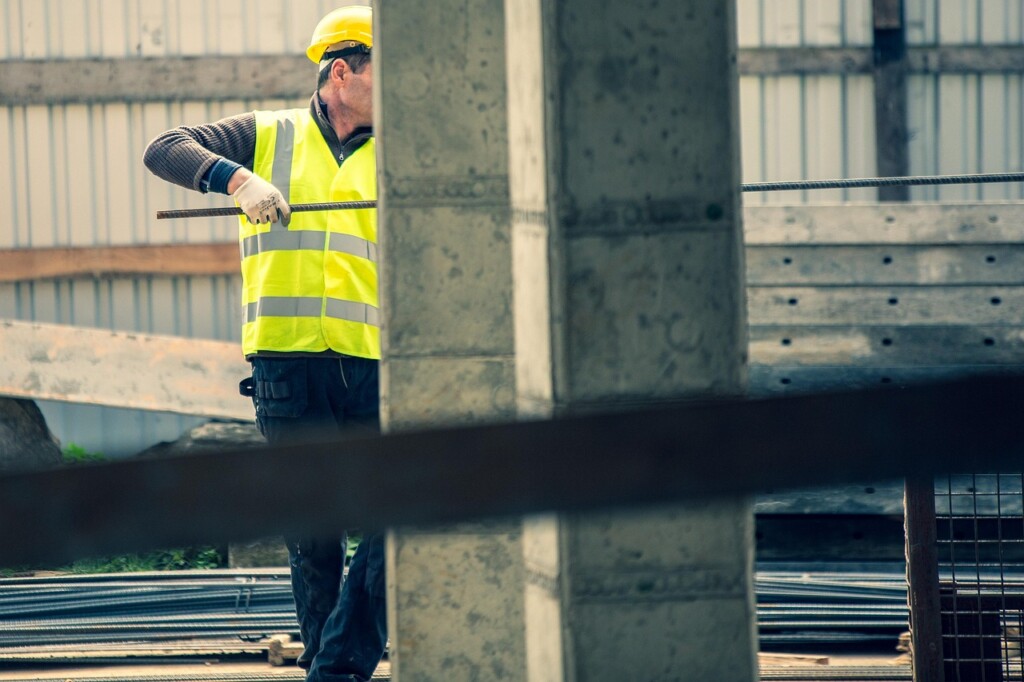
While we have established the efficiency benefits of modular construction, implementing this approach involves overcoming several significant hurdles. Our construction teams regularly face these challenges when evaluating modular solutions for our clients’ projects.
Transportation Limitations
The most immediate challenge involves logistics. Module dimensions are constrained by transportation regulations—typically limited to a maximum of 16 feet wide by 75 feet long. These size restrictions directly impact design possibilities and can create complications during planning phases.
Transportation costs also represent a substantial portion of modular project budgets. When factory locations are far from the project site, these expenses can quickly erode the cost advantages gained through factory production. For urban projects, we must carefully coordinate delivery routes to account for bridges, tight turns, and traffic restrictions that could impede module transportation.
The risk of damage during transport presents another concern. Even with careful handling, modules can suffer damage that requires on-site repairs, potentially disrupting installation sequences and timelines. Our project managers develop detailed transportation plans with contingencies to minimize these risks.
Customization Constraints
Despite advancements in modular technology, we still encounter limitations when clients request highly customized designs. The manufacturing process, while efficient, favors standardization and repetition. Projects with unique architectural features or non-uniform layouts often lose some of the cost and schedule advantages that modular construction typically provides.
Front-loaded design decisions present another challenge. Unlike traditional construction, where changes can be accommodated during the building process, modular construction requires finalizing nearly all design elements before manufacturing begins. This accelerated decision timeline can be difficult for clients accustomed to making adjustments throughout construction.
For development projects requiring distinctive aesthetics or variable unit types, we carefully evaluate whether modular construction truly delivers enough advantages to offset these customization constraints.
Regulatory Hurdles
The regulatory landscape for modular construction remains complex and inconsistent. Building codes and zoning laws vary significantly between jurisdictions, with some areas having established clear guidelines for modular projects while others require extensive education and engagement with local officials.
In our experience, inspection processes can become particularly complicated. Some jurisdictions permit factory inspections that allow modules to arrive on-site with closed walls and completed finishes. Others require local inspections that make it necessary to leave systems exposed until on-site approval, reducing efficiency and increasing fieldwork.
We address these regulatory challenges through early coordination with authorities having jurisdiction, sometimes months before project commencement. This proactive approach helps establish clear expectations and requirements for module approval throughout the construction process.
Financing Complications
The financial structure of modular projects differs significantly from traditional construction, creating potential funding obstacles. Modular manufacturers typically require substantial payments earlier in the project timeline—often before any physical work appears on-site. This upfront capital requirement can create cash flow challenges for developers and property owners.
Traditional construction loans, structured around field progress and physical completion percentages, often align poorly with modular manufacturing schedules. We work closely with our clients’ financial partners to develop funding projections that account for the accelerated material purchasing and manufacturing timelines inherent in modular projects.
To prevent potential liens or work stoppages, we establish clear verification procedures for factory production progress, ensuring that funds are properly allocated to the specific modules being manufactured for our projects.
Market Perception Challenges
Despite increasing adoption, modular construction still contends with perception issues among some stakeholders. Misunderstandings about quality, durability, and design flexibility can create resistance among investors, end-users, and even some construction professionals.
In reality, modular buildings must meet the same codes and standards as traditionally constructed facilities. The controlled factory environment can actually enhance quality control compared to site-built structures. According to recent studies by the U.S. Department of Energy, modular buildings have demonstrated better energy efficiency when accounting for higher occupant density and have shown improved installation quality in building envelope components.
We address these perception challenges through education and by showcasing successful modular projects that demonstrate durability, aesthetic appeal, and long-term performance.
Aspect | Modular Construction | Traditional Construction |
---|---|---|
Time Efficiency | 30-75% faster due to parallel site preparation and module creation | Prone to weather setbacks, sequential processes |
Cost Efficiency | Potential cost savings from reduced labor, material waste, and faster timelines | Higher costs due to extended timelines and potential weather-related damages |
Quality Control | High due to controlled factory environment | Variable due to on-site conditions |
Design Flexibility | Limited by standardization | High adaptability for unique and custom designs |
Environmental Impact | Lower due to reduced waste and emissions | Higher due to on-site waste and emissions |
Regulatory Compliance | Complex regulations for modular-specific codes | Established codes but may have fewer hurdles |
Transportation | Challenges with module size and potential damage during transport | Not applicable |
For developers and property owners considering modular construction, understanding these challenges is essential for making informed decisions. While the benefits of shortened schedules and potential cost savings remain compelling, we approach each project with a comprehensive analysis of how these challenges might impact the specific circumstances and requirements of the development.
By acknowledging and planning for these hurdles early in the process, we can determine whether modular construction truly represents the optimal approach for achieving your project goals.
What Markets and Applications Are Ideal for Modular Construction?
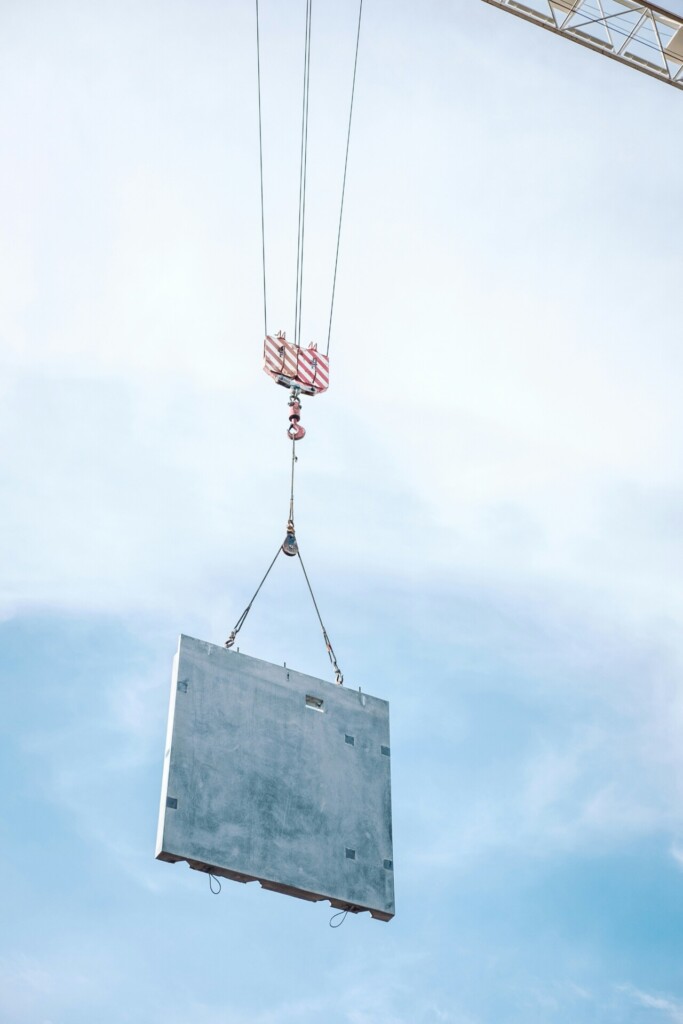
Modular construction has gained significant traction in key markets where its advantages address specific industry challenges. As general contractors, we’ve seen how different sectors can maximize the benefits of prefabrication to overcome traditional construction limitations.
Educational Facilities Lead Adoption
Educational institutions represent a promising application for modular construction, comprising about 15% of the market. Schools and universities face timing constraints—construction often needs to occur without disrupting academic calendars. We can deploy modular classrooms, administrative buildings, and student housing during breaks, minimizing the impact on educational operations.
The speed of modular construction is valuable in areas experiencing rapid population growth, where new educational infrastructure must be delivered quickly. In these situations, we can complete projects in approximately half the time of conventional methods, allowing institutions to meet enrollment demands within constrained timeframes.
Healthcare Facilities Benefit from Precision and Speed
Healthcare construction represents about 6% of the modular market but shows strong growth potential. The sector demands exceptional precision, cleanliness, and quality control—all strengths of the modular approach. By fabricating critical components in controlled environments, we ensure consistent quality while significantly reducing construction timeframes.
The COVID-19 pandemic highlighted the value of modular healthcare construction when rapid deployment of facilities became essential. Healthcare providers increasingly turn to prefabrication, recognizing that reduced construction time translates to faster delivery of patient care.
Commercial Applications Driving Growth
The commercial sector is experiencing growth in modular construction adoption, with significant demand for offices, showrooms, and hotels. As the global economy recovers in key markets like the UK, US, and Asia, we see increased commercial building activities leveraging modular techniques. The approach is valuable for hospitality projects, where faster completion means quicker revenue generation.
From portable commercial buildings to modular retail stores, we deliver solutions that conform to the International Building Code (IBC) while reducing construction timelines. The versatility of modular construction makes it ideal across different commercial applications including offices, public facilities, restaurants, and retail establishments.
Multi-Family and Residential Housing
With growing housing shortages in urban centers worldwide, multi-family residential development is a critical application for modular construction. The residential segment accounts for about 53% of the market and continues to expand. Rising global population and urbanization have heightened the need for housing, especially in crowded metropolitan areas.
We leverage modular construction to provide efficient, cost-effective housing solutions with reduced build times and expenses. Our approach allows us to create customizable residential designs that meet diverse housing needs and preferences in rapidly growing cities. This makes modular construction valuable in addressing affordable housing challenges.
Geographic Hotspots for Modular Construction
Certain regions are especially suitable for modular construction adoption. Areas experiencing skilled labor shortages combined with high housing demand present ideal markets for our modular solutions. Notable hotspots include:
- Australia’s East Coast metropolitan areas, where urbanization pressures and construction workforce limitations create perfect conditions for modular approaches
- Germany’s growing cities, where offsite construction helps overcome labor constraints while meeting sustainability requirements
- The UK’s southern region, where government housing initiatives actively promote modular solutions to address severe housing shortages
- The US West Coast, particularly California, where high land costs and housing demand make efficient construction methods essential
In these regions, we help developers overcome local construction challenges while delivering high-quality projects in reduced timeframes.
Industrial and Workforce Accommodations
Industrial workforce housing is another significant application, particularly in regions with active energy sectors requiring temporary accommodations in remote locations. In Canada, for example, the modular industry provides critical temporary workforce housing solutions in remote areas where energy development is occurring.
These projects often require rapid deployment of high-quality living spaces in challenging environments—precisely where modular construction excels. We deliver comfortable, code-compliant accommodations on accelerated schedules, helping industrial clients maintain their operational timelines.
As modular construction technology advances, we anticipate further expansion into these key markets. The growing recognition of modular construction’s benefits—from faster project delivery and reduced site disruption to improved quality control and sustainability—makes it an increasingly attractive option across multiple sectors facing construction challenges.
Conclusion: The Future of Modular Construction
The shift from traditional site-built construction to manufacturing-style production is not just a temporary trend; it is reshaping how we approach building projects entirely. As general contractors experienced in both conventional and modular methodologies, we are witnessing firsthand how this evolution is transforming construction efficiency. With market projections indicating potential growth to $162.42 billion by 2030 at a CAGR of 7.9%, modular construction represents a significant opportunity for developers and property owners seeking more predictable timelines and budgets.
The momentum behind modular is not merely financial. While challenges remain in perception and regulatory standardization, technological advancements in BIM, improved manufacturing processes, and growing environmental pressures are creating a more favorable landscape for off-site construction than previous attempts. The ability to reduce construction schedules, minimize site disruption, and maintain consistent quality control makes modular particularly attractive for multi-family residential, healthcare, and commercial applications where speed-to-market creates tangible competitive advantages.
Ready to explore if modular construction methods might benefit your next development project? Contact EB3 Construction for a consultation on modern building approaches.