Construction deadlines are tightening while budgets are shrinking—a familiar pressure point for developers and property owners in today’s market.
At EB3 Construction, we have embraced Modern Methods of Construction (MMC) as pivotal solutions for meeting these challenges head-on. These innovative approaches utilize cutting-edge technology and materials to fundamentally transform how we deliver projects from concept to completion.
MMC marks a decisive shift from traditional on-site building techniques toward more efficient, factory-based production systems. We implement these methods to shorten construction timelines while maintaining—and often enhancing—build quality. The 2020 Dodge Data and Analytics report supports our experience, showing that 91% of general contractors report positive cost impacts when using modular construction techniques, with nearly half achieving cost reductions of 10% or more.
Instead of assembling everything piece by piece on-site, we coordinate substantial elements manufactured under controlled factory conditions, bringing them to your location ready for efficient installation. This approach not only accelerates project delivery but also improves precision, reduces waste, and creates more predictable outcomes for your investment.
What Are the Top Prefabrication and Modular Construction Methods?
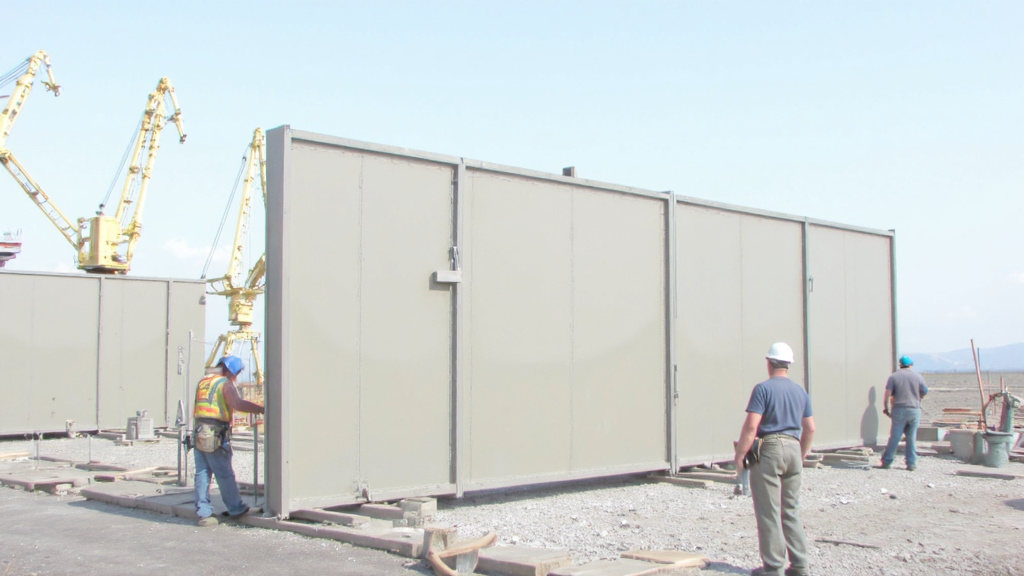
Prefabrication and modular techniques are fundamentally transforming how we deliver projects for our clients. As general contractors, we’ve seen firsthand how these methods compress schedules while maintaining—and often improving—quality standards. Let’s examine the most effective prefabrication approaches we implement on our projects.
Precast and Pre-engineered Flat Panel Systems
When we manufacture floor and wall panels in controlled factory environments, we eliminate many of the variables that traditionally slow construction progress. These flat panel systems arrive on site ready for immediate installation, with electrical conduits, insulation, and even window openings precisely pre-positioned.
The efficiency gains are substantial. Our crews can install dozens of panels daily, allowing us to enclose buildings in days rather than weeks. This approach particularly shines in multi-unit residential developments and commercial structures where repeatable elements create economies of scale.
For developers facing tight market windows, this prefabrication method offers remarkable advantages—panels manufactured simultaneously with foundation work can reduce overall project timelines by 30-40% compared to conventional methods.
3D Volumetric Construction
The most comprehensive form of prefabrication we employ is 3D volumetric construction, where entire building sections—complete with floors, walls, ceilings, and internal connections—are manufactured off-site. These three-dimensional modules arrive with MEP systems pre-installed, fixtures in place, and finishes applied. The controlled factory environment ensures consistent quality regardless of outdoor weather conditions.
The logistics are complex but manageable with proper planning. Our teams coordinate precisely timed deliveries and crane operations to position and connect modules with millimeter-level precision. The reduced on-site workforce requirements—often 40-60% fewer labor hours—prove particularly valuable in regions with construction labor shortages.
Precast Concrete Foundations
The foundation phase often represents a significant timeline vulnerability in traditional construction. We mitigate this risk by implementing precast concrete foundation systems whenever site conditions permit. These factory-produced foundation components offer superior dimensional accuracy and consistent material quality.
For our developer clients, the advantages extend beyond speed. Precast foundation elements withstand harsh weather conditions exceptionally well, making them ideal for projects in areas with extreme seasonal variations. The factory curing process results in concrete that achieves its design strength before ever reaching the site.
We’ve found these systems particularly effective when paired with helical screw piles in challenging soil conditions. This combination minimizes ground disturbance while providing laser-precise levelness—essential for subsequent modular components.
Benefits That Drive Implementation
Our implementation of these prefabrication methods consistently delivers measurable advantages for our clients’ projects. Quality control improves significantly when construction occurs in factory environments with specialized equipment and standardized processes. Weather delays become largely irrelevant to the manufacturing timeline, allowing for more predictable scheduling.
The sustainability benefits deserve particular mention. Our prefabrication partners report 60-80% less construction waste compared to traditional methods. Transportation logistics are carefully optimized to minimize environmental impact, while the inherent durability of factory-built components often extends building lifecycles.
For property owners, the accelerated timeline translates directly to earlier occupancy and faster return on investment. The precision of prefabricated components also results in tighter building envelopes with superior energy performance, reducing long-term operational costs.
What Advanced Concrete and Wall System Technologies Are Transforming Construction?
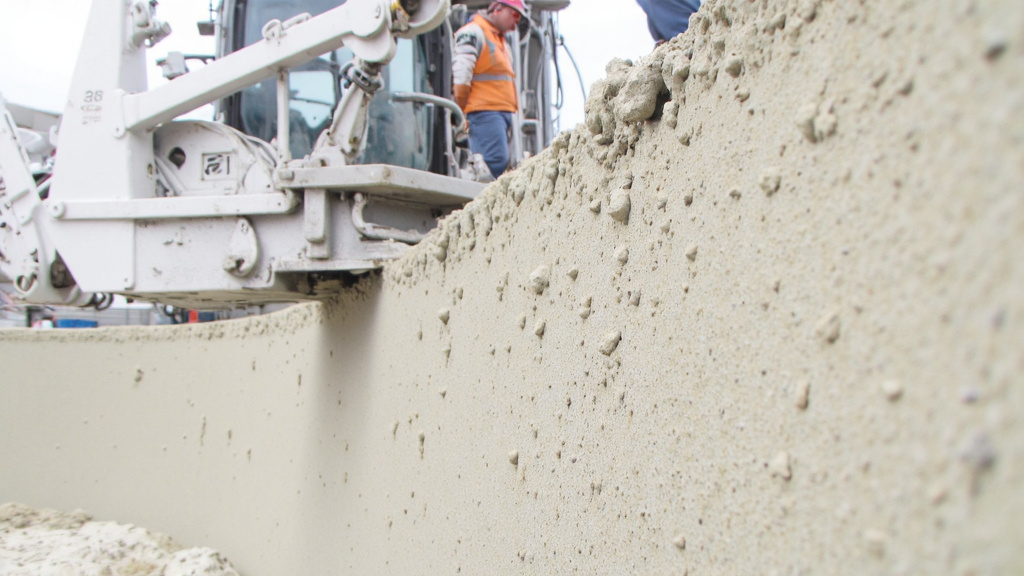
As general contractors, we’re witnessing a fundamental shift in how structures are built due to innovative concrete technologies and advanced wall systems. These methods not only improve efficiency but also create stronger, more energy-efficient buildings while reducing construction timelines for our clients’ projects.
Insulated Concrete Forms (ICF): Building Better Thermal Envelopes
When developers prioritize energy efficiency without sacrificing structural integrity, we implement ICF construction. This system uses double-walled polystyrene panels to create a permanent formwork for poured concrete, resulting in walls with exceptional thermal resistance.
The beauty of ICF lies in its dual functionality—the insulating forms remain in place after the concrete cures, creating continuous insulation that virtually eliminates thermal bridging. For property owners concerned about environmental impact, we’ve found ICF structures can reduce heating and cooling costs by up to 50% compared to traditional construction methods.
ICF particularly excels in regions with extreme weather conditions. We’ve deployed this system for everything from custom homes to commercial buildings where sound attenuation and durability are paramount concerns. The robust walls provide superior resistance to high winds, fire, and moisture intrusion—addressing multiple project requirements with a single building system.
Twin-Wall Technology: Precision and Speed Combined
For projects with aggressive timelines, we utilize twin-wall technology to maintain quality while accelerating construction schedules. This hybrid approach combines the precision of precast concrete with the continuity of cast-in-place methods.
The system consists of two precast concrete panels, typically 2-3 inches thick, connected by an integrated lattice girder system. We’ve found this method particularly valuable for multi-story structures where the panels can be rapidly installed, providing immediate stability and safety for follow-up trades.
On a recent commercial development, our switch to twin-wall technology reduced the structural construction timeline by nearly 40%. After installation, we fill the void between panels with cast-in-place concrete, creating a monolithic structure that performs like a traditionally formed wall but with significantly reduced labor hours and formwork costs.
System | Clear Wall R-value (hft²°F/Btu) | Whole Wall R-value (hft²°F/Btu) | R-value Ratio (%) |
---|---|---|---|
12-in. Two-core insul. units – concrete | 3.7 | 3.6 | 97.3 |
12-in. Two-core insul. units – wood concrete | 9.4 | 8.6 | 91.7 |
EPS block-forms poured in place | 15.2 | 15.7 | 103.3 |
2×4 wood stud wall 16-in. o.c. | 10.6 | 9.6 | 90.9 |
2×6 wood stud wall 24-in. o.c. | 16.4 | 13.7 | 83.7 |
Stress Skin Panel Wall | 24.7 | 21.6 | 87.5 |
4-in. Metal stud wall 24-in. o.c. | 14.8 | 10.9 | 73.5 |
Thin Joint Masonry: Optimizing Traditional Methods
When project specifications call for masonry construction, we employ thin joint systems to enhance both performance and productivity. Unlike conventional 10mm mortar joints, thin joint masonry uses specialized adhesive mortars at just 3mm thickness, fundamentally changing how we approach blockwork.
The reduced mortar layer yields multiple benefits for our clients. Wall strength improves significantly due to the superior bond strength of the adhesive mortar, while the reduced thickness minimizes potential weak points in the assembly. Our masonry crews can build walls faster with thin joint techniques, accelerating project schedules without compromising quality.
From a practical standpoint, thin joint masonry allows us to make buildings weather-tight sooner. This enables interior trades to begin their work earlier, creating a cascading efficiency effect throughout the construction sequence. The reduced thermal bridging through mortar joints also contributes to improved envelope performance—a critical consideration as energy codes become increasingly stringent.
Implementation Considerations
Successfully integrating these advanced concrete technologies requires careful planning and expertise. Our pre-construction teams evaluate site conditions, project requirements, and logistical factors to determine which system will deliver maximum value for each specific development.
For oceanfront properties, we often recommend ICF for its superior moisture resistance and insulating properties. Urban infill projects typically benefit from twin-wall technology due to reduced site congestion and faster erection. Low-rise commercial developments frequently use thin joint masonry for its cost-effectiveness and aesthetic versatility.
While these systems require specialized knowledge during installation, their long-term performance advantages make them increasingly popular options among forward-thinking developers and property owners focusing on building lifecycle costs rather than just initial construction expenses.
How Do Structural Framing Innovations Improve Building Projects?
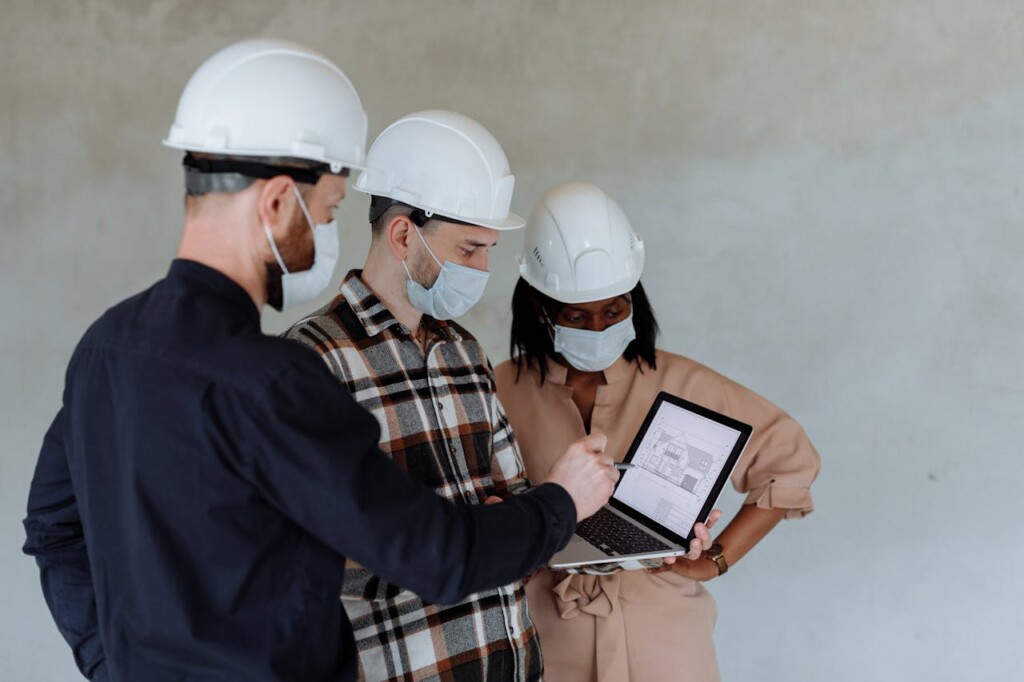
Over the past decade, structural framing methods have evolved significantly. Today’s construction environment requires solutions that provide exceptional strength and durability, address environmental concerns, and accelerate project timelines. At EB3 Construction, we implement these advanced framing techniques to deliver superior building performance for developers and property owners.
Advanced Timber Framing Solutions
The traditional art of timber framing has been transformed through modern engineering. We now work with engineered wood products like cross-laminated timber (CLT) and laminated veneer lumber (LVL) that offer consistent strength and dimensional stability beyond conventional lumber.
These engineered products allow us to span greater distances without additional support, creating more open, flexible spaces for our clients. The manufacturing process maximizes each tree’s yield, reducing waste while providing superior load-bearing capacity. When we frame with these materials, we build structures that maintain their integrity longer while reducing the project’s overall carbon footprint.
For developers concerned with both sustainability metrics and construction efficiency, our engineered wood framing solutions offer a dual advantage. The prefabricated nature of these components means we can assemble them more quickly on-site, reducing labor costs and accelerating project timelines without sacrificing quality.
Optimized Framing Techniques
We’ve adopted advanced framing approaches that strategically reduce material usage while enhancing building performance. Instead of following the conventional 16-inch on-center stud placement, we implement 24-inch spacing where structurally appropriate. This seemingly small change yields significant benefits throughout your project.
By optimizing stud placement, we create more space for insulation within walls, dramatically improving thermal performance. The reduction in thermal bridging means your building will maintain more consistent interior temperatures with less energy expenditure. For property owners, this translates directly to lower operational costs over the building’s lifetime.
Our precision in header sizing and elimination of redundant framing members further reduces material costs without compromising structural integrity. When combined with single top plates and two-stud corners in non-load-bearing applications, these techniques collectively decrease lumber usage by up to 30% compared to conventional framing methods.
Aspect | Traditional Framing | Advanced Framing |
---|---|---|
Stud Size | 2″x4″ | 2″x6″ |
Stud Spacing | 16″ apart | 24″ apart |
Material Usage | Higher | 30% less |
Insulation Space | Limited | 50% more |
Design Flexibility | Less flexible | More flexible |
Load-Bearing Walls | Required | Not always required |
Cost-Effectiveness | Higher material costs | Potential cost savings |
Energy Efficiency | Lower | Higher |
Innovative Concrete Systems
For multi-story and commercial projects, we utilize flat slab construction methods that eliminate the need for traditional beams. These thick, reinforced concrete slabs transfer loads directly to supporting columns, creating versatile open spaces with higher ceilings and unobstructed floor plans.
The practical advantages of this approach extend beyond aesthetics. Implementing flat slab systems dramatically simplifies the installation of mechanical, electrical, and plumbing services. Without beams interrupting the ceiling plane, ductwork and utilities can be routed more efficiently, reducing coordination challenges and potential conflicts during construction.
This method also provides greater architectural flexibility, allowing for more creative space utilization and adaptive reuse potential. As market demands change, buildings framed with these systems can be reconfigured with relative ease, extending their useful life and improving their long-term value proposition for property owners.
Integration of Modern Steel Framing
We’ve expanded our framing capabilities to include cold-formed steel systems that offer exceptional strength-to-weight ratios. These lightweight yet robust frames resist warping, cracking, and pest damage while providing superior fire resistance compared to traditional materials.
Steel framing enables us to create precise, consistent structures with minimal dimensional variation. The material’s uniform quality eliminates many common framing challenges, such as shrinkage and settling, resulting in smoother finishing surfaces and fewer warranty callbacks for cosmetic issues.
For projects with aggressive timelines, steel framing components can be fabricated off-site to exact specifications, allowing for rapid assembly once delivered. This prefabrication approach reduces waste at the jobsite while enabling tighter construction schedules and more predictable outcomes—critical factors for developers working within strict financial parameters.
What Are the Economic and Environmental Benefits of Modern Construction Methods?
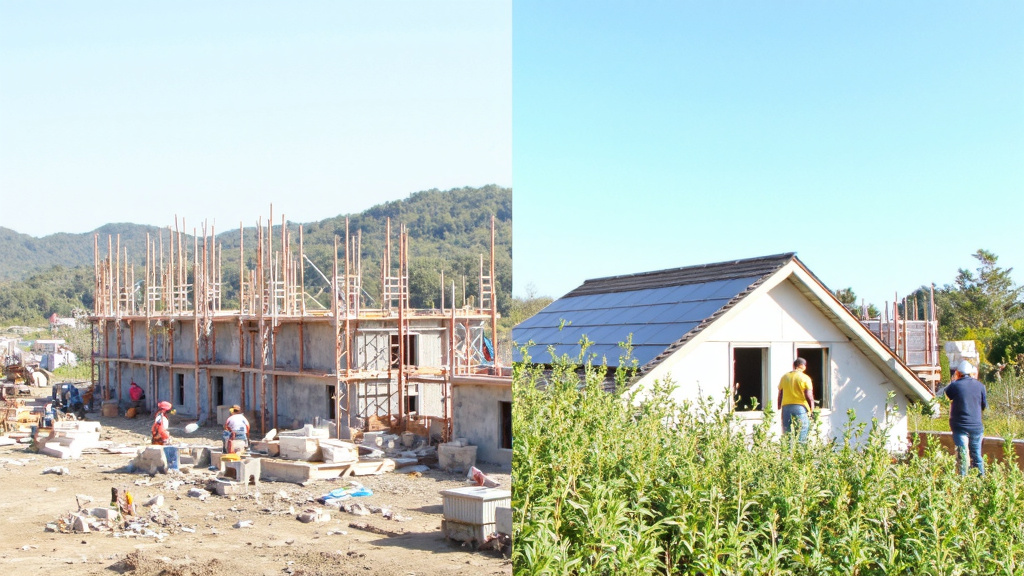
As general contractors serving developers and property owners, we have witnessed firsthand how modern construction methods are transforming the industry—not only in terms of efficiency but also through substantial economic and environmental advantages that benefit all project stakeholders.
Economic Advantages That Improve Your Bottom Line
While traditional construction approaches might appear less expensive initially, the comprehensive financial benefits of modern methods typically outweigh these upfront costs considerably. We consistently see projects using advanced techniques finish 20-30% faster than conventional builds, dramatically reducing labor costs and accelerating revenue generation.
When we implement modern construction methods like prefabrication and modular building, we eliminate many of the variables that traditionally cause budget overruns. Weather delays become significantly less impactful when major components are assembled in controlled factory environments rather than on-site. This predictability translates directly into more accurate cost projections and fewer expensive mid-project adjustments.
Resource optimization represents another substantial economic advantage. By precisely calculating material needs through digital modeling and prefabricated components, we can reduce material waste by 30-40% compared to traditional methods. These savings compound across the project lifecycle, from purchasing to disposal costs, while simultaneously addressing increasingly stringent waste management regulations.
Environmental Benefits That Matter
The construction sector currently accounts for approximately 38% of global carbon emissions. By implementing modern methods, we actively reduce this environmental burden through several key mechanisms. Factory-controlled assembly environments enable precise material usage, minimizing waste that would otherwise end up in landfills. Our prefabricated and modular approaches typically generate 60% less waste than traditional construction methods.
Energy efficiency represents another critical environmental benefit. Modern construction techniques like Insulated Concrete Forms (ICF) and Structural Insulated Panels (SIPs) create thermal envelopes that significantly outperform conventional construction. Buildings constructed using these methods routinely achieve 50-60% reductions in ongoing energy consumption, drastically reducing operational carbon footprints while delivering substantial utility cost savings to owners.
Material selection within modern construction systems further enhances environmental performance. We prioritize renewable and recycled resources whenever possible, from sustainably harvested timber frames to concrete alternatives with reduced cement content. These choices reduce embodied carbon while often improving structural performance and building longevity. Crucially, many modern systems also enable easier disassembly and material recovery at the end of a building’s life, supporting circular economy principles.
The Intersection of Economic and Environmental Benefits
The most compelling aspect of modern construction methods is how economic and environmental benefits frequently reinforce each other. Faster construction timelines reduce not only labor costs but also the environmental impacts associated with extended site activities—from generator emissions to erosion concerns. Similarly, enhanced building performance delivers both reduced operating expenses and smaller carbon footprints.
This alignment extends to regulatory compliance as well. As environmental standards become increasingly stringent, buildings constructed with modern methods are typically better positioned to meet or exceed requirements with minimal retrofitting. This forward-compatibility protects property values while avoiding costly compliance upgrades that often plague conventionally constructed buildings as regulations evolve.
Resource efficiency represents perhaps the clearest example of this economic-environmental synergy. When we reduce material waste through digital modeling and precision manufacturing, we simultaneously lower project costs and environmental impact. These efficiencies extend beyond construction into operations, where high-performance building envelopes and systems reduce both utility bills and carbon emissions for the life of the structure.
Real-World Implementation Considerations
While the benefits are compelling, successfully implementing modern construction methods requires careful planning and expertise. Effective integration begins in the earliest design phases, where decisions about structural systems and assembly approaches profoundly impact both economics and environmental performance. This underscores the importance of engaging experienced contractors like ourselves who understand these methodologies thoroughly.
Site conditions and project requirements always influence which modern methods will deliver optimal results. For urban infill projects with limited staging areas, for instance, we might recommend highly prefabricated solutions to minimize on-site disruption. For projects with aggressive sustainability targets, we might prioritize techniques offering exceptional thermal performance and reduced embodied carbon. The key lies in selecting the right approach for each specific project context.
Workforce considerations also impact implementation strategy. Modern construction methods often require specialized knowledge and different skill sets than traditional approaches. We maintain dedicated teams trained in advanced construction techniques, ensuring smooth execution regardless of which methods best suit your project. This expertise allows us to maximize both the economic and environmental benefits while maintaining strict quality control throughout the construction process.
Conclusion: Embracing Innovation in Construction
Modern construction methods have transformed our industry landscape. We have witnessed firsthand how prefabrication, modular construction, and advanced concrete technologies streamline project timelines while maintaining—and often improving—quality standards.
At EB3 Construction, we find these methods consistently deliver faster completion times compared to traditional approaches, allowing us to serve developers and property owners with unprecedented efficiency.
The construction industry is at a pivotal moment where technology adoption is essential for survival. Between 2020 and 2022, investment in AEC technology increased by 85% to approximately $50 billion, according to McKinsey & Company. We are committed to integrating these innovations into our processes because they address our industry’s most pressing challenges: labor shortages, sustainability requirements, and cost control. By incorporating Building Information Modeling, 3D printing capabilities, and prefabrication techniques into our workflow, we deliver projects that meet today’s demanding schedules while preparing for tomorrow’s construction landscape.
Ready to explore how innovative construction methods can benefit your next development project? Contact our team at EB3 Construction today.