Precast construction represents a significant change in how we build modern structures. The process involves manufacturing concrete components off-site in a factory, where elements are cast in reusable molds, cured under controlled conditions, and then transported to the project location for assembly. This systematic approach contrasts with traditional cast-in-place methods that dominate conventional jobsites.
As general contractors in the commercial and industrial sectors, we have seen how precast techniques have transformed project timelines. The controlled production environment eliminates weather-related delays and allows for concurrent site preparation while components are being manufactured—a scheduling advantage that is especially valuable in regions with unpredictable climates or compressed building seasons.
The real advantage of precast methods lies in the precision and consistency that factory production enables. Fabricating components in standardized forms achieves dimensional accuracy that is nearly impossible to replicate with field-poured concrete. This results in faster assembly, reduced material waste, and ultimately, structures that perform better throughout their lifecycle.
How Does the Precast Construction Process Work?
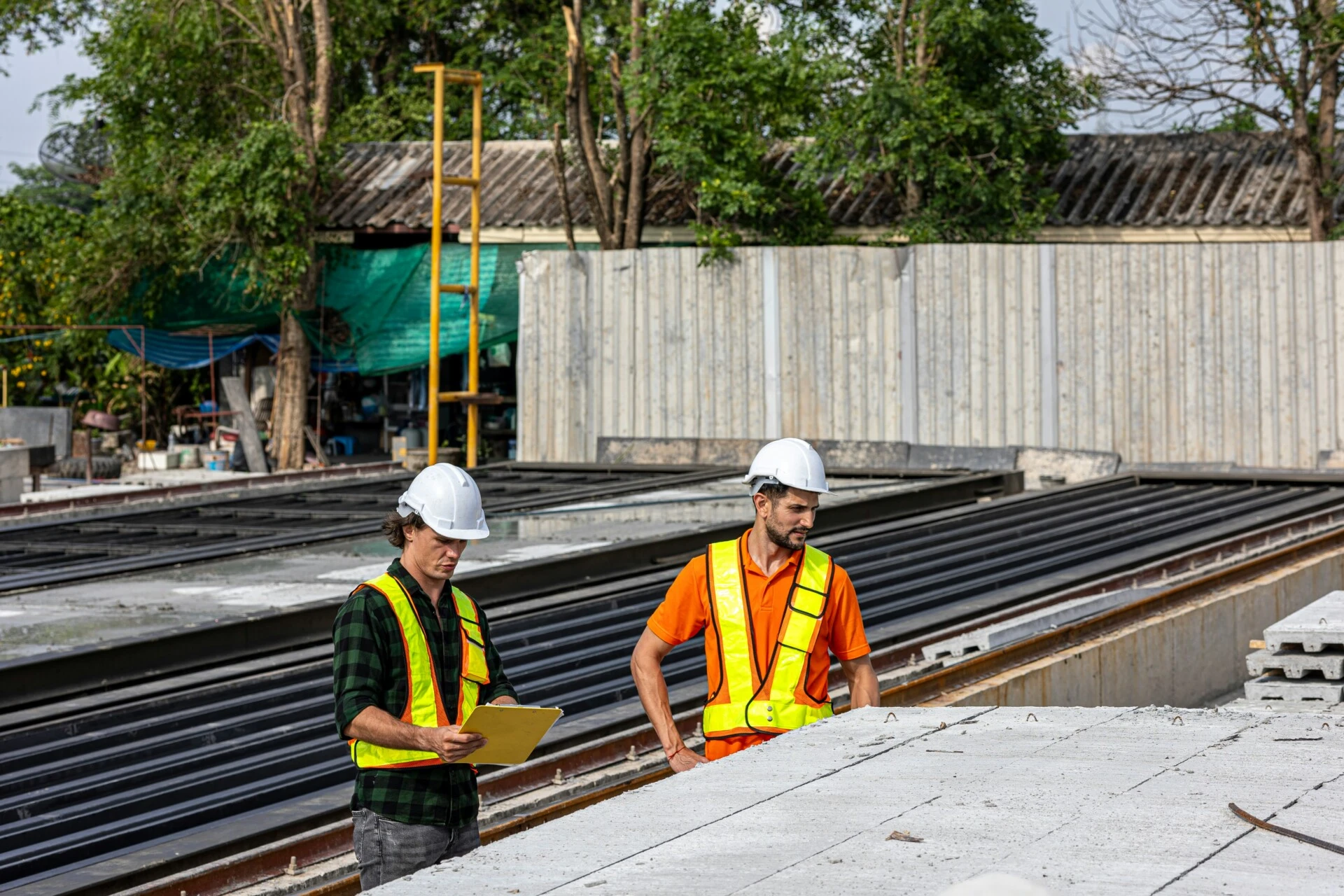
At EB3 Construction, we have refined our approach to precast concrete construction to maximize efficiency and quality. The process begins in a controlled manufacturing environment, away from the unpredictable conditions of an active job site, where we create precision-engineered components that will later form the structural backbone of the project.
First, we develop detailed shop drawings and create specialized molds or forms based on the architectural specifications. These reusable forms, typically made from steel, fiberglass, or timber, can be customized to produce almost any structural element needed, from facade panels to structural beams. Unlike traditional site-poured concrete, where formwork might be used only once, our precast forms can be reused hundreds or even thousands of times, creating significant cost efficiencies.
Next comes reinforcement preparation—a critical step that significantly impacts structural integrity. Our teams assemble reinforcement cages using steel rebar or mesh according to engineering specifications, positioning them precisely within the forms. For enhanced performance in specific applications, we may incorporate prestressing techniques, applying tension to the reinforcement before the concrete is poured to improve load-bearing capacity.
The concrete mix design is another area where the precast method excels. We utilize high-strength concrete mixes, typically with Portland Type III cement, specifically engineered for each application. Careful monitoring of aggregate quality, water-cement ratios, and admixtures ensures consistent performance across all components. The controlled batching process eliminates the variables that often plague on-site concrete work.
When we pour the concrete, we use mechanical vibration techniques to eliminate air pockets and ensure complete consolidation around the reinforcement. This creates exceptionally dense, strong components that significantly outperform site-poured alternatives. The forms are then moved to curing chambers where temperature and humidity are precisely controlled to optimize strength development.
Curing is where precast truly differentiates itself from traditional methods. While site-poured concrete is subject to weather conditions that can compromise quality, our precast elements cure in a controlled environment for a specified period, typically reaching 75% of design strength within days rather than weeks. This accelerated curing schedule allows for much faster production timelines than would be possible on-site.
After curing and quality inspection, we transport the finished components to the construction site. The logistics of this phase require careful planning, especially for large structural elements. Our site teams use cranes and specialized equipment to position each component precisely according to the installation sequence. Connection points, designed during the engineering phase, allow for rapid assembly and integration with the building’s structural system.
The entire process—from initial form preparation to final installation—operates on a streamlined timeline that dramatically reduces overall project schedules compared to conventional cast-in-place methods. While traditional concrete construction involves sequential operations that must wait for curing periods, our precast approach allows simultaneous manufacturing of components while site preparation proceeds in parallel.
This parallel workflow, combined with factory-level quality control and precision, delivers exceptional value for developers and property owners faced with tight schedules and quality requirements that grow more demanding each year. The Spring 2023 market conditions have made this efficiency even more valuable, as construction timelines face increasing pressure from supply chain challenges.
Aspect | Precast Concrete | Cast-in-Place Concrete |
---|---|---|
Production Environment | Controlled factory setting | On-site |
Curing Time | Fast, controlled curing | Extended, weather-dependent |
Quality Control | High, consistent quality | Variable, site-dependent |
Installation Speed | Rapid assembly | Slower, sequential processes |
Labor Cost | Reduced due to off-site production | Higher due to on-site labor |
Weather Dependence | Independent of weather | Dependent on weather conditions |
Construction Time | Reduced overall timeline | Longer due to curing and weather delays |
Beyond the production advantages, the installation phase showcases another benefit of precast methods. Our skilled assembly teams can install dozens of precast elements in a single day, accomplishing in hours what might take weeks with traditional forming, pouring, and curing cycles. This rapid assembly not only accelerates the schedule but also reduces site disruption—a significant advantage in congested urban environments or occupied facilities where minimizing construction impact is essential.
What Are the Key Components of Precast Construction?
At EB3 Construction, we’ve observed how precast concrete systems transform project timelines and outcomes. The controlled manufacturing process behind precast construction ensures consistent quality unmatched by traditional cast-in-place methods. Understanding these fundamental elements helps us coordinate assembly and maximize benefits for our clients’ projects.
Precast Concrete Panels
Wall panels are among the most versatile and widely used precast components we implement. These factory-manufactured elements serve both exterior façades and interior partitions, offering superior insulation alongside their structural function. Precision manufacturing allows us to integrate window openings, architectural details, and various surface finishes during production.
When installed on-site, their ready-to-assemble nature significantly accelerates building envelope closure. A project requiring weeks of formwork, pouring, and curing with traditional methods can often be enclosed in days using precast panels. This rapid weathertightness enables our interior trade partners to start work much earlier in the construction sequence.
Beyond speed, the controlled factory environment ensures consistent concrete curing conditions, eliminating concerns of thermal cracking and improper hydration that affect poured-in-place concrete during extreme temperatures.
Structural Beams and Columns
The skeletal framework of precast buildings relies on engineered beams and columns. These load-bearing elements transfer structural forces throughout the building while supporting floors, roofs, and other components. We typically use inverted tee beams, L-beams, or rectangular beams based on specific structural requirements and clearance needs.
Precast columns, generally rectangular, support larger framing elements that carry heavier loads. During preconstruction planning, we work closely with structural engineers to determine optimal column locations that balance structural needs with the client’s interior space preferences.
The superior load-bearing capacity of precast columns and beams allows for longer spans and more flexible floor plans than many conventional systems. This structural efficiency translates directly to more usable square footage for our clients—a critical factor in commercial and institutional projects where maximizing rentable space drives ROI.
Floor and Roof Systems
Precast floor and roof systems complete the structural envelope with components like hollow-core slabs, solid slabs, and double-tee sections. These horizontal elements distribute loads across the structure while providing fire resistance and sound isolation between levels.
Hollow-core slabs, manufactured with continuous voids running their length, offer an excellent strength-to-weight ratio. This efficiency reduces the overall structural load and foundation requirements. The hollow sections also serve as convenient chases for mechanical, electrical, and plumbing systems, simplifying coordination between trades.
Double-tee sections provide longer clear spans—up to 100 feet in some applications—creating column-free spaces that maximize flexibility for our clients. These spans are particularly valuable in applications like parking structures, warehouses, and retail spaces where obstructed floor plans would compromise functionality.
Specialized Components
Beyond these primary elements, we incorporate specialized precast components to address specific project needs. Precast staircases arrive as complete units ready for immediate installation and use. Foundation elements like grade beams and pile caps accelerate below-grade work. Architectural features such as cornices, fascias, and decorative panels offer aesthetic versatility without sacrificing the speed and quality advantages of precast systems.
For infrastructure projects, we use precast components like bridge segments, retaining walls, culverts, and utility structures. These elements face harsh exposure conditions, making the enhanced durability of factory-produced precast particularly valuable for reducing long-term maintenance costs.
Component | Application |
---|---|
Precast Beams | Bridges, highways, commercial buildings |
Columns | Parking structures, bridges, commercial buildings |
Floor Panels | Residential buildings, schools, warehouses |
Stair Treads | Residential and commercial buildings |
Retaining Walls | Infrastructure projects |
Sound Walls | Urban areas to reduce noise pollution |
Culverts | Stormwater and sewage drainage |
Assembly and Connection Systems
The integration of these components relies on sophisticated connection methods that ensure structural continuity throughout the building. We employ various connector systems—from hidden corbels and column shoes to flexible loop systems and slim floor connections—that maintain structural integrity while streamlining the assembly process.
During erection, we use specialized lifting equipment to place these substantial components precisely. A typical precast panel may weigh several tons, requiring careful coordination between our crane operators and assembly crews. This orchestrated process allows us to erect multiple stories in days rather than the weeks required for conventional construction methods.
Weather independence is another significant advantage of our precast assembly approach. While traditional concrete pours often face delays during adverse conditions, our precast installation continues through light rain and moderate winds, maintaining project momentum even during challenging seasons.
What Are the Different Precast Concrete Methods?
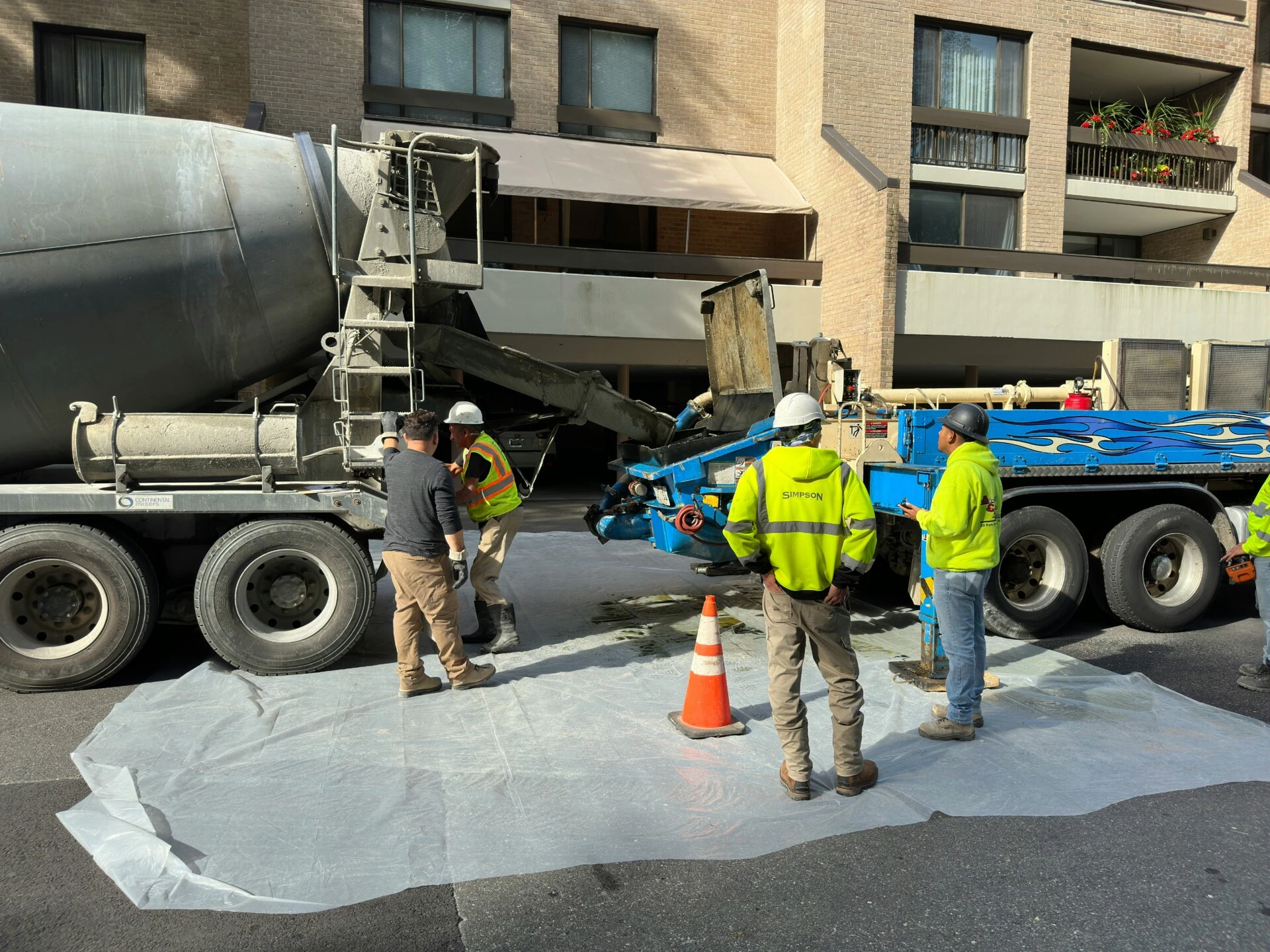
When construction demands precision and efficiency, precast concrete is our material of choice. We employ several production methods at EB3 Construction, each offering distinct advantages for specific project requirements. Understanding these differences helps us select the optimal approach for your development needs.
Wet-Cast Method: Versatility and Smooth Finishes
The wet-cast method is central to our precast operations. We fill specially designed molds with flowable concrete mixtures that can be poured from mixers or trucks. This method allows for the creation of complex shapes with smooth, finished surfaces that require minimal post-production work.
The process starts with preparing a properly designed mold, followed by introducing a concrete mixture with sufficient water content for workability. We use internal vibration techniques to eliminate air pockets and ensure proper consolidation within the form. The resulting products showcase excellent surface detail and can incorporate various aesthetic finishes.
Wet-cast components typically require longer curing periods compared to other methods, but the versatility in design and appearance makes this trade-off worthwhile for many architectural applications. We routinely use this technique for producing decorative panels, complex structural elements, and components where surface finish quality is paramount.
Dry-Cast Method: Strength and Immediate Stripping
For projects demanding high durability and rapid production, we use the dry-cast method, also known as zero-slump concrete production. This approach utilizes a stiffer concrete mix with just enough moisture to ensure complete cement hydration without excess water. The concrete consistency resembles damp soil rather than the flowing mixture used in wet casting.
Instead of internal vibration, we apply intense external vibration combined with pressure to compress the mixture into molds. This creates exceptionally dense concrete with superior compressive strength and durability characteristics. The immediate advantage is evident in production efficiency – forms can often be stripped immediately after casting, allowing for rapid reuse of molds and accelerated manufacturing cycles.
Dry-cast products typically feature a rougher texture than their wet-cast counterparts, making them ideal for utilitarian applications where function trumps aesthetics. We commonly employ this method for manufacturing pipe, manholes, catch basins, and retaining wall systems where structural integrity is the primary consideration.
Aspect | Wet-Cast | Dry-Cast |
---|---|---|
Water-to-Cement Ratio | 0.4 or higher | 0.30 to 0.36 |
Mix Consistency | More fluid | Stiffer |
Production Process | Poured into forms and cured | Compressed with high pressure and cured |
Curing Time | Longer curing period | Shorter curing time |
Appearance | Smooth, detailed textures | Rougher texture |
Durability | Lower porosity, better for freeze-thaw cycles | Higher compressive strength and density |
Applications | Complex shapes, decorative panels | Pipes, manholes, structural elements |
Prestressed Precast: Enhanced Structural Performance
When spanning long distances or handling heavy loads, we turn to prestressed precast concrete methods. This specialized technique involves stretching high-strength steel tendons or cables within the concrete form before casting. After the concrete cures and achieves sufficient strength, we release the tension, creating built-in compression forces that significantly enhance the concrete’s load-bearing capacity.
This compression counteracts the tensile forces that typically limit concrete’s structural performance, allowing us to create longer spans with less material. The prestressing process requires precision engineering and specialized equipment but delivers remarkable structural efficiency. We implement this method for bridge components, floor and roof systems, and large structural elements where minimizing weight while maximizing strength offers substantial project benefits.
The prestressing operation demands exacting quality control, as proper tension levels and concrete consolidation directly impact performance. Our production facilities maintain strict protocols to ensure these critical components meet or exceed design specifications, providing the confidence developers need when pushing structural boundaries.
Specialized Methods for Specific Applications
Beyond these mainstream approaches, we employ several specialized precast methods to address unique project requirements. Autoclaved Aerated Concrete (AAC) production creates lightweight, highly insulating panels by introducing aluminum powder to create tiny air bubbles throughout the matrix. After initial setting, these panels undergo high-pressure steam curing in autoclaves, producing building components with exceptional thermal and acoustic properties.
For maximum density and strength, vacuum concrete methods extract excess water from freshly placed concrete through specialized formwork. This technique accelerates strength development and reduces shrinkage potential. We might recommend this approach for water-retaining structures or components exposed to aggressive environmental conditions where permeability concerns exist.
Glass-fiber reinforced concrete (GFRC) techniques allow us to create remarkably thin, lightweight panels with outstanding tensile strength. By integrating alkali-resistant glass fibers throughout the matrix, we produce architectural elements that would be impossible using traditional reinforcement methods. This approach proves particularly valuable for creating dramatic façade elements or complex architectural features where weight restrictions apply.
What Are the Benefits of Precast Concrete Construction?
When building structures that demand reliability, efficiency, and precision, precast concrete has become our preferred solution at construction sites across the region. Unlike traditional cast-in-place methods, precast elements arrive ready for installation, fundamentally transforming how we approach projects for our clients.
Quality Control Advantages
The controlled factory environment where precast components are produced provides a significant quality advantage over site-cast concrete. Temperature, humidity, and curing conditions remain optimal throughout production, eliminating the weather variability that often compromises on-site pouring.
This controlled setting allows our teams to implement rigorous inspection protocols during manufacturing. We have found that precast components consistently achieve higher strength ratings and dimensional accuracy than their cast-in-place counterparts, resulting in structures that meet or exceed engineering specifications from day one.
The precision possible in precast facilities enables complex shapes and architectural details that would be prohibitively expensive or technically challenging with traditional methods. This quality consistency reduces costly rework and remediation that commonly affect conventional concrete construction.
Accelerated Construction Timeline
Perhaps the most compelling advantage of precast concrete is the significant compression of project schedules. While site preparation progresses on location, our precast elements are simultaneously being manufactured off-site, creating parallel workflows impossible with traditional methods.
This simultaneous production approach can reduce overall project timelines by up to 20-30% compared to cast-in-place concrete. For developers with construction loans, this acceleration directly translates to earlier revenue generation and reduced financing costs.
Weather-related delays become substantially less impactful with precast methods. A rainy season that might halt traditional concrete pouring for weeks affects only the installation phase of precast components, not their production, allowing us to maintain momentum even during challenging conditions.
Construction Method | Timeframe |
Precast Concrete | 56 days |
Cast-in-Place Concrete | 266 days |
Cost and Labor Efficiencies
The shift of labor-intensive work from job sites to manufacturing facilities creates significant economic advantages. Precast production leverages specialized equipment and optimized workflows that dramatically improve labor productivity compared to field operations.
This manufacturing approach reduces the number of skilled workers needed on-site during construction. With current skilled labor shortages affecting the industry, this reduction in on-site staffing requirements helps us deliver projects despite tight labor markets.
The predictable production environment also minimizes expensive overtime and rush charges that frequently impact conventional concrete work. We can accurately forecast labor needs, material quantities, and production schedules, eliminating the costly surprises that plague traditional methods.
Sustainability and Environmental Benefits
Precast concrete offers significant environmental advantages throughout the construction lifecycle. The precision of factory production substantially reduces material waste—typically lowering concrete consumption by 5-10% compared to field-poured methods through optimized design and forming systems.
The durability of precast structures extends building lifespans, reducing the embodied carbon impact over time. Many precast facilities now incorporate recycled materials and specialized concrete mixes that further reduce environmental impact without sacrificing performance.
The thermal mass properties of precast concrete provide passive energy management benefits, reducing HVAC demands in completed buildings. When combined with integrated insulation systems, precast wall panels deliver superior energy performance compared to many alternative building envelope systems.
Structural Performance and Safety
The factory production of precast elements allows for precise reinforcement placement and concrete consolidation, creating components with superior structural integrity. This consistency is particularly valuable in structures requiring specific performance characteristics like seismic or blast resistance.
Precast systems can be engineered to meet exact load requirements, optimizing material use while maintaining structural integrity. This performance predictability is invaluable when designing for specific conditions or compliance requirements.
The reduced on-site construction activity associated with precast installation significantly improves job site safety metrics. Fewer worker hours on scaffolding and less time spent in vulnerable construction phases translate directly to improved safety performance, protecting both our teams and our project timelines.
Conclusion: The Future of Precast Construction
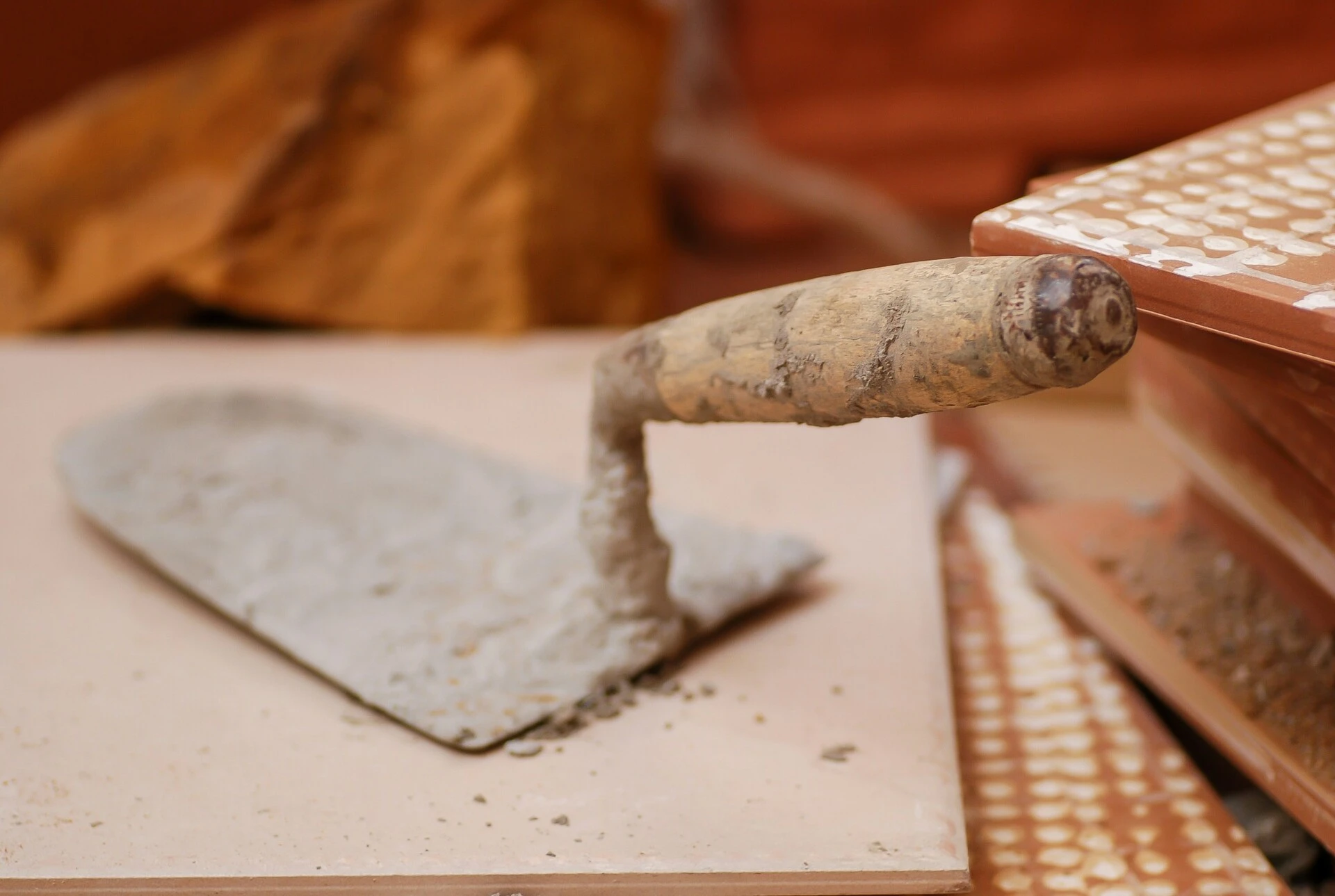
The emergence of precast concrete as a cornerstone of modern construction is not just a trend—it is reshaping how we approach building projects from foundation to finish. In commercial developments, multi-unit residential complexes, and infrastructure projects, precast methods have dramatically compressed schedules while delivering consistent quality that site-cast methods often struggle to match. As general contractors, we understand that construction feasibility often depends on these time and quality advantages, especially when weather constraints or tight urban sites present challenges.
Looking ahead, our industry stands at an exciting crossroads where advanced manufacturing techniques, sustainable materials science, and digital coordination are converging to enhance precast solutions. Ultra-high-performance concrete (UHPC), embedded sensor technologies, and 3D-printing innovations are transforming possibilities in precast fabrication. These advancements allow us to create structures that are not only more efficient to build but also more resilient, sustainable, and adaptable to changing environmental conditions. We are particularly observing how modular precast systems continue to evolve, enabling rapid deployment of complex structures with minimal on-site labor requirements—a critical advantage amid ongoing workforce challenges in our industry.
Ready to explore how precast construction solutions can benefit your next development project? Connect with our team to discuss your specific needs and timeline.