Commercial building construction involves the intricate process of planning, designing, and building structures specifically for business and profit-generation. These environments can host various types of commerce, including office complexes, retail centers, healthcare facilities, and industrial warehouses. The commercial construction landscape has experienced growth over the years, attracting investors despite these projects” inherent complexities.
Commercial construction projects typically differ from residential building in several ways. They generally operate on a larger scale and may require more stringent standards. These projects often involve coordinating specialized engineering teams, navigating municipal permitting processes, and implementing systems designed for higher occupancy and intensive daily use. Commercial structures are typically built to withstand greater foot traffic while meeting the functional needs of the businesses that will occupy them.
Commercial construction also emphasizes functionality, operational efficiency, and compliance with commercial building codes. While developing these spaces, construction teams aim to balance the practical needs of businesses with safety considerations, accessibility requirements, and sustainability goals. Each project typically requires coordination among developers, architects, engineers, and construction teams to create structures that fulfill their commercial purpose while supporting the goals of property owners and stakeholders.
What Are the Different Types and Scales of Commercial Construction?
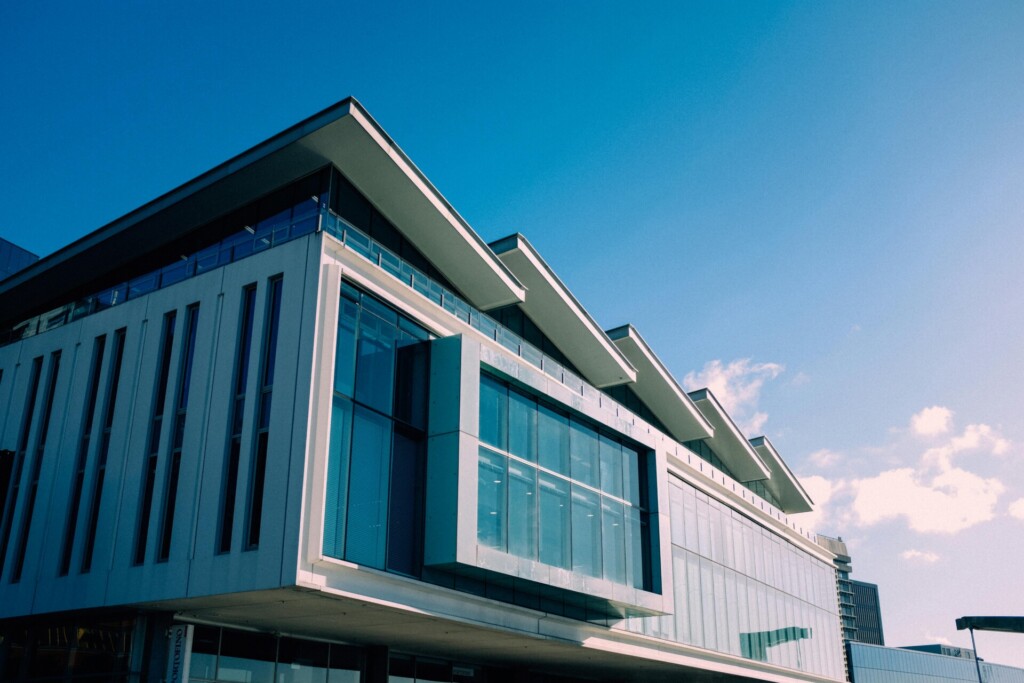
Commercial construction involves a wide array of projects designed to meet the needs of businesses and organizations across diverse industries. At EB3 Construction, we classify these projects into three main scales based on scope, complexity, and resource requirements. Understanding these levels can help align expectations with project realities and prepare effectively for commercial building endeavors.
Small-Scale Commercial Construction
Small-scale projects often entail modifications to existing structures, typically not affecting the building”s footprint or major structural elements. These projects can cover less than 5,000 square feet and may be completed within weeks or a few months. They can be managed with focused teams and efficient processes.
Working on small-scale renovations may involve tight schedules in occupied spaces. For example, retail storefront remodels might require night shifts to minimize disruption, while restaurant kitchen upgrades must adhere to health codes throughout construction. Other common small-scale projects can include:
- Office remodeling and tenant improvements
- Interior reconfigurations to enhance workflow
- Upgrades to HVAC, electrical, or plumbing systems
- ADA compliance modifications
- Facade improvements and signage installation
These projects typically require fewer permits and less coordination than larger ones, yet demand careful attention to building codes and client requirements. Small-scale project teams aim to maintain high-quality standards throughout the build process.
Mid-Scale Commercial Construction
Mid-scale commercial construction represents an increase in complexity and resource allocation. Covering 5,000 to 50,000 square feet, these projects may involve substantial modifications to existing structures or moderately sized new builds. Timelines can extend from several months to over a year, necessitating extensive planning and coordination.
To manage mid-scale projects, specialized teams may be assembled, including project managers, superintendents, and trade specialists. The scope typically includes:
- Building expansions, such as adding new wings or floors
- Significant renovations involving multiple building systems
- Medium-sized new constructions like medical clinics or boutique hotels
- Multi-tenant commercial spaces requiring complex coordination
- Warehouse conversions or extensive retail buildouts
These projects can present unique challenges that require creative problem-solving. For instance, historic building conversions may need careful preservation of architectural elements while installing modern systems. Close coordination with local preservation authorities may be necessary, and unexpected structural issues during demolition can impact project schedules.
Large-Scale Commercial Construction
Large-scale commercial construction encapsulates complex and resource-intensive projects in the industry. These endeavors typically exceed 50,000 square feet and can span multiple years from planning to completion. They require sophisticated management systems, extensive coordination among numerous stakeholders, and carefully planned phases.
In undertaking large-scale projects, comprehensive project controls may be implemented and multidisciplinary teams with specialized expertise assembled. The logistics demand meticulous planning—from material staging and equipment coordination to workforce scheduling and safety protocols. Examples include:
- High-rise office buildings and multi-use developments
- Large-scale hospital complexes and healthcare facilities
- University campus developments and educational institutions
- Industrial manufacturing facilities and distribution centers
- Shopping malls and large retail developments
These projects often incorporate advanced construction technologies and methods. For example, Building Information Modeling (BIM) can be used to identify potential conflicts before construction begins, and lean construction principles may be applied to minimize waste and maximize efficiency. These sophisticated approaches aim to help manage complex projects effectively while addressing inherent challenges.
The scale of a commercial construction project directly impacts nearly every aspect of its execution—from initial planning and budgeting to daily site operations and final delivery. Each scale demands a tailored approach, with specialized teams, equipment, and management strategies to ensure successful outcomes.
Scale | Square Feet | Typical Duration | Examples |
---|---|---|---|
Small-Scale | < 5,000 | Weeks to a few months | Retail storefront remodel, office remodeling, HVAC upgrades |
Mid-Scale | 5,000 – 50,000 | 6 to 18 months | Building expansions, medium-sized new constructions like medical clinics |
Large-Scale | > 50,000 | 18 months to 5 years | High-rise office buildings, large-scale hospitals, shopping malls |
Regardless of scale, all commercial construction projects can benefit from early contractor involvement. By bringing expertise to the table during the planning phase, contractors may help clients avoid costly pitfalls and develop realistic budgets and timelines. Experience across all scales of commercial construction can enable guidance through the complexities of building or renovating commercial spaces with confidence and transparency.
What Are the Key Steps in the Commercial Construction Process?
The commercial construction journey demands precision, coordination, and expertise at every turn. As general contractors, we understand that successful construction typically hinges on a methodical approach to each phase. Let”s examine seven critical steps that can form the foundation of bringing commercial projects to life.
Development and Planning
Every successful commercial project typically begins with thorough development and planning. This foundational stage is where the project”s direction can be established and realistic expectations set. This may involve helping developers select an optimal location, considering factors such as accessibility, zoning regulations, soil conditions, and proximity to utilities and infrastructure.
Budget development forms another crucial component of this initial phase. Comprehensive financial frameworks may account for hard costs like materials and labor, as well as soft costs including permits, design fees, and contingencies. Recent material price volatility due to supply chain disruptions has made this planning even more critical, potentially requiring flexibility in budgets while maintaining project viability.
This is also when the core project team can be formed, bringing together key stakeholders, architects, engineers, and construction management personnel to establish clear communication channels and accountability structures. When everyone understands their role from day one, it may help minimize costly misunderstandings later.
Pre-Design Phase
Once planning is complete, the pre-design phase begins where abstract concepts can start taking concrete form. During this stage, we typically work closely with clients to define the overall scope, size, and function of different spaces within the building. This may include analyzing how the structure will connect to existing utilities and comply with local development covenants.
Thorough feasibility studies can help identify potential challenges early. This may involve examining everything from utility connection points to site access limitations that might impact construction logistics. This proactive approach allows for determining whether clients” desired amenities can be accommodated within existing parameters and budget constraints.
We may also begin creating preliminary contract documents that establish project timelines and cost breakdowns for each construction phase. This transparency can help clients understand what to expect throughout the build process and provides a framework for measuring progress as construction advances.
Design Phase
With preliminary requirements established, the design phase begins where detailed construction documents take shape. Here, architects and engineers can transform conceptual ideas into precise blueprints and specifications that construction teams will follow. This phase typically produces comprehensive drawings that govern every aspect of the build.
The design phase often involves multiple specialized professionals working in concert. Structural engineers can ensure the building”s integrity through appropriate support systems. Mechanical engineers may handle HVAC and plumbing designs that will keep the building comfortable and functional. Electrical engineers can develop power distribution systems that meet both current needs and allow for future expansion.
For commercial projects with specific requirements, additional specialists may be brought in. Civil engineers can address drainage, parking lot design, and connections to surrounding infrastructure. For taller structures, threshold inspectors may be engaged to conduct structural assessments throughout construction, providing an additional layer of quality assurance and code compliance.
Pre-Construction Phase
With designs finalized, the pre-construction phase begins, where critical administrative and preparatory work is handled before breaking ground. Obtaining building permits is typically a top priority, which often involves submitting plans to local building departments, addressing any comments or required modifications, and securing final approvals.
Securing comprehensive insurance coverage is also crucial at this stage. This typically includes builders” risk insurance to protect against property damage, commercial and contractor general liability insurance to cover potential accidents, and workers” compensation insurance to safeguard teams on site.
Simultaneously, vendor selection through competitive bidding processes and establishing the full construction team usually occurs. This may include appointing key personnel such as the project manager who oversees daily operations, the superintendent who coordinates construction activities, the contract administrator who manages documentation, and field engineers who handle technical aspects and quality control.
Procurement Phase
The procurement phase is where all necessary materials, equipment, and subcontracted services required for construction are secured. This stage is particularly crucial in today”s market where material availability and lead times can significantly impact project schedules.
Established supplier relationships and purchasing power can be leveraged to obtain materials that meet both quality standards and budget parameters. For specialized components with extended manufacturing times, orders may be placed well in advance to prevent delays in the construction schedule. Throughout this process, detailed inventory tracking systems can ensure materials arrive on site exactly when needed.
For larger projects, strategic procurement approaches may be implemented, dividing responsibilities among subcontractors for certain portions of the work while maintaining overall coordination. This approach can optimize efficiency while ensuring consistent quality standards across all aspects of the project.
Phase | Description | Duration |
---|---|---|
Design and Planning | Conceptualization, design development, securing permits | 2-6 Months |
Pre-Construction | Preparation and site evaluations | 1-4 Months |
Construction | Structural development, interior, and exterior works | 3-12 Months |
Completion and Handover | Final touches, inspections, and project closeout | 2-4 Weeks |
Post-Construction | Ongoing support and maintenance | Ongoing |
Construction Phase
The construction phase transforms plans into physical reality through a carefully orchestrated sequence of activities. This typically begins with thorough site preparation, implementing proper drainage systems, excavating the site, laying utilities, and establishing temporary facilities. This groundwork sets the stage for successful construction and may include initial inspections to verify compliance with building codes.
Foundation work usually follows, creating the stable base upon which the entire structure will rest. Framing then establishes the building”s structural skeleton. As construction progresses, roofing and siding can enclose the structure, followed by HVAC systems that will control the interior environment.
Interior and exterior finishing work brings the building closer to completion, with attention to detail becoming increasingly important. Throughout construction, rigorous quality control measures with regular inspections are typically maintained. Project managers and superintendents coordinate the complex choreography of trades working simultaneously to maintain efficiency without compromising quality.
Post-Construction Phase
The post-construction phase ensures that the completed building meets all specifications and is ready for occupancy. This often involves thorough testing of all building systems to verify proper functionality. The project owner, design team, and construction management staff may perform a comprehensive walkthrough to identify any items requiring attention before final acceptance.
During this inspection, a detailed punch list documenting any incomplete tasks or components needing adjustment may be developed. These items are systematically addressed to ensure every aspect of the building meets expectations. This meticulous approach can lead to substantial completion certification, signifying the project is ready for its intended use.
Finally, the deactivation of temporary construction assets, return of rental equipment, site cleanup, and waste management are typically overseen. A building official usually conducts the final inspection to verify code compliance before issuing occupancy certification. Comprehensive documentation, including warranties, operating manuals, and as-built drawings to support future facility management, may also be provided.
By methodically working through these seven phases, commercial buildings can be delivered that meet clients” needs while adhering to quality standards, budget parameters, and timeline commitments. Each phase builds upon the previous one, creating a seamless progression from concept to completion that aims to maximize efficiency while minimizing potential disruptions.
What Factors Should You Consider When Building a Commercial Property?
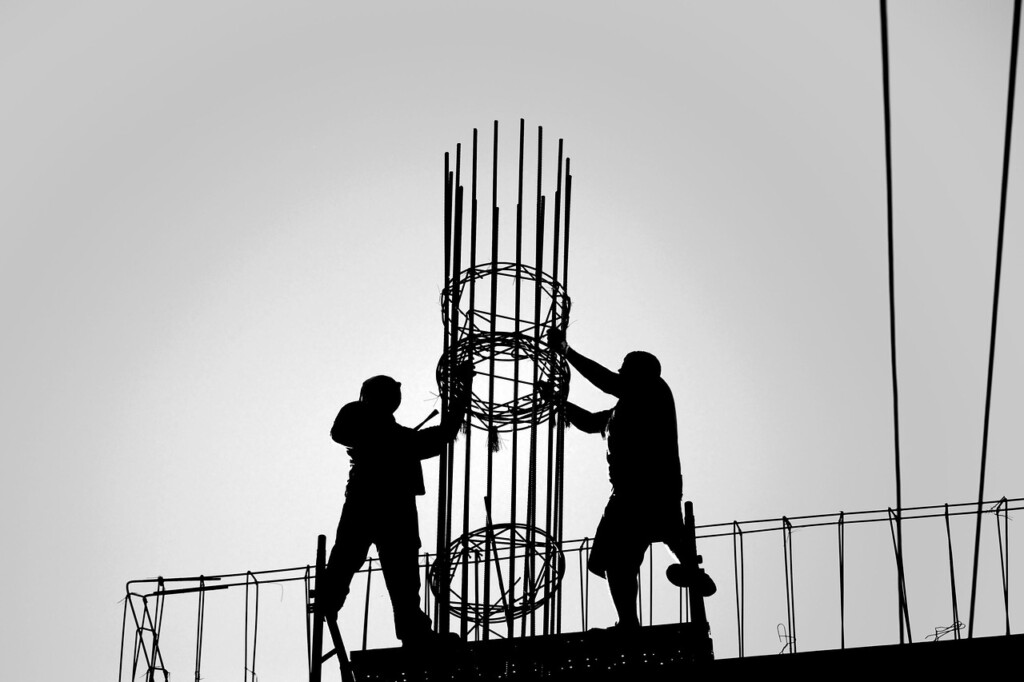
Building a commercial property requires careful planning and consideration of various factors that can influence not only the construction process but also the long-term success of your investment. At EB3 Construction, we approach each commercial project with a comprehensive analysis of these critical elements before breaking ground.
Location Assessment
Location is a cornerstone of any commercial property. Multiple criteria can be evaluated to ensure a site aligns with business objectives. Accessibility is crucial; factors such as traffic patterns, proximity to major thoroughfares, and public transportation options can affect how easily customers and employees reach the property.
Apart from accessibility, the surrounding business ecosystem may be worth analyzing. The presence of complementary businesses can potentially create synergistic relationships that drive foot traffic, while an abundance of similar businesses might indicate market challenges. Population density, demographic profiles, and income levels are factors that can help determine if a location may support an intended commercial use.
Infrastructure availability also plays a role in site selection. It”s important to verify that a location has adequate utility connections, including water, sewer, electrical capacity, and high-speed internet infrastructure. Insufficient utilities can lead to upgrades that may impact your budget.
Zoning Laws and Regulatory Compliance
Navigating zoning regulations is one of the most challenging aspects of commercial construction. It”s crucial to research local zoning ordinances to determine permitted uses, height restrictions, setback requirements, and parking regulations that may govern a project. In some cases, variances or conditional use permits might be necessary if a vision doesn’t align perfectly with existing codes.
Building in a zone with incompatible uses can result in operational limitations or even prevent a business from operating. Staying current with local zoning changes and development regulations can help identify potential issues before they become expensive problems.
For example, changes in many urban areas have created mixed-use zoning designations that allow for combinations of retail, office, and residential spaces, potentially creating new opportunities for flexible commercial development.
Project Complexity | Typical Permit Approval Time | Description |
---|---|---|
Simple Projects | 3 days to 3 weeks | Approval can often be quick due to less complexity; some are approved over-the-counter or within a few days online. |
Moderate Projects | 2 to 8 weeks | Typical commercial modifications or upgrades take several weeks; precise timelines can vary based on jurisdiction and project specifics. |
Complex/Large Projects | 3 months to 2 years | Large scale projects that require thorough reviews can extend timelines significantly due to exhaustive compliance and multiple jurisdictional checks. |
Variable Factors | Dependent on location & scope | Timelines depend on city, county regulations, and specific project demands like environmental impact or public hearings. |
Permitting Process
The permitting journey can be lengthy and complex, with requirements varying significantly between municipalities. Coordination of necessary permits may include building permits, environmental permits, signage permits, and special use authorizations. Established relationships with local building departments can help streamline this process.
Timing is particularly critical in the permitting phase. Some jurisdictions may take weeks or even months to process permits, and failing to account for this timeline can affect a project schedule. Building realistic permitting timelines into project plans, accounting for potential review cycles and revision requests from regulatory authorities, is advisable.
Environmental considerations also factor heavily into the permitting process. Thorough environmental assessments can identify potential issues like soil contamination, wetland impacts, or endangered species habitats that could trigger additional permitting requirements or mitigation measures.
Design and Construction Planning
Translating a commercial vision into a functional, code-compliant structure requires thoughtful design and construction planning. Working closely with architects to develop plans that maximize the functionality of a space while meeting all regulatory requirements is essential. This includes considerations for ADA accessibility, fire safety systems, and energy efficiency standards.
Future adaptability is another key consideration to incorporate into design planning. Commercial needs evolve over time, and buildings that can be readily modified for different uses may maintain their value better than highly specialized structures. Flexible design elements that allow for reconfiguration as business needs change can be beneficial.
Material selection balances aesthetic considerations with durability, maintenance requirements, and budget constraints. Sourcing materials that provide the right combination of visual appeal, performance, and value can help maximize return on investment.
Budget and Financial Planning
Realistic budget planning can help prevent financial stress during construction. Developing comprehensive budgets that account for direct construction costs, permit fees, utility connection charges, and contingency funds for unforeseen circumstances is advisable. Cost transparency allows for informed decisions throughout the project.
Cash flow management is equally important. Structuring payment schedules that align with construction milestones can help ensure that funds are available when needed without placing undue financial strain on a business. This approach may help prevent delays due to funding issues that can cascade into significant timeline problems.
Identifying potential tax incentives, grants, or special financing options that might be available for a commercial project can be beneficial. Many municipalities offer economic development incentives for commercial construction that creates jobs or revitalizes specific areas.
Construction Team Selection
The quality of a construction team can impact the success of a commercial project. Selecting experienced contractors with specific expertise in the type of commercial construction being undertaken is important. Previous project portfolios and client references can provide valuable insights into their capabilities and reliability.
Establishing communication protocols early can help ensure all stakeholders remain informed throughout the construction process. Regular meetings, detailed progress reports, and clear channels for addressing concerns can help prevent misunderstandings and keep the project moving forward.
Implementing robust quality control processes, including regular inspections and testing, can help ensure that all work meets or exceeds applicable building codes and industry standards. This attention to quality can help prevent costly rework and contribute to the longevity of a commercial property.
By carefully considering each of these factors, commercial construction projects can proceed more smoothly from concept to completion. A systematic approach can help minimize risks and maximize the potential for a successful, profitable commercial property investment.
How Can You Optimize Commercial Construction Management?
Commercial construction management thrives on a foundation of teamwork and clear communication. At EB3 Construction, we understand that the success of a project relies not only on technical expertise but also on effective collaboration throughout the construction process. The industry”s recent shift toward more integrated project delivery models has underscored what construction professionals have long understood: communication breakdowns can lead to delays and mistakes.
Building Your Construction Management Foundation
Each project typically begins with assembling a team tailored to specific needs. This may involve bringing together architects who understand the design vision, project managers experienced in the building type, and specialized contractors who provide expertise at each phase. A California Building Industry Association survey on construction delays in 2023 found that a significant portion of schedule disruptions arose from coordination issues rather than technical problems. Schedule disruptions often arise from coordination issues rather than technical problems, highlighting the importance of effective team management.
Once a team is assembled, we aim to establish clear roles and responsibilities. Each member needs to understand not only their individual tasks but also how their work integrates with others. Our superintendents typically maintain a single chain of command on-site, which can help prevent conflicting directives and ensure workers receive consistent information about project specifications and timelines.
On large commercial projects, we may implement a structured communication protocol with regular briefings between key stakeholders. These meetings can serve as checkpoints where progress is documented, challenges are identified, and solutions are collaboratively developed. This approach allows us to anticipate potential roadblocks before they impact the schedule or budget.
Leveraging Technology for Enhanced Communication
Technology has transformed how communication can be managed in construction. We typically use cloud-based construction management software as a centralized repository, aiming to ensure that everyone, from project managers to subcontractors, has access to the most current plans, specifications, and schedules. This can help reduce the risk of teams working from outdated information, a common source of errors and rework.
Building Information Modeling (BIM) is a vital tool in our workflow. This 3D modeling technology can provide stakeholders with a virtual project representation, allowing us to identify potential conflicts between building systems before construction begins. By enabling the mechanical, electrical, and plumbing teams to visualize how their work intersects, we aim to avoid on-site conflicts and redesigns.
Our field teams typically use mobile applications to document progress, flag issues, and communicate in real-time with office staff. This feedback loop can keep projects moving forward without waiting for traditional reporting cycles to identify problems. Photos, videos, and annotated drawings can be shared quickly, offering clarity that may be difficult through verbal descriptions alone.
Creating a Culture of Collaborative Problem-Solving
Beyond formal structures and technologies, we aim to promote a culture where open communication is valued. Our field supervisors are trained to encourage input from all team members, recognizing that valuable insights often come from those closest to the work. This collaborative approach allows us to leverage the collective expertise of everyone involved in a project.
When challenges arise, we typically bring together the relevant stakeholders for focused problem-solving sessions. Rather than allowing issues to multiply, we aim to address them promptly with the right expertise at the table. This might involve consulting with the architect about a design clarification, working with the structural engineer on a site condition, or coordinating with the mechanical contractor on equipment placement.
Our pre-construction services may include communication planning, alongside traditional budgeting and scheduling. We aim to identify potential communication bottlenecks and establish protocols before breaking ground, helping to prevent the information silos that can develop between design teams, construction managers, and subcontractors on complex projects.
Measuring and Improving Communication Effectiveness
Effective construction management requires ongoing assessment of communication practices. We may track key performance indicators related to information flow, such as response times to RFIs (requests for information), the number of change orders, and the efficiency of decision-making processes. These metrics can help us continually refine our project communication approach.
Regular stakeholder feedback sessions enable us to evaluate our communication strategies” effectiveness from multiple perspectives. We aim to adjust our methods based on what works and what requires improvement, recognizing that different projects and teams may need tailored approaches. This flexibility helps ensure communication remains a strength in your project.
By investing in comprehensive communication planning, adopting suitable technologies, and nurturing a collaborative culture, we aim to help transform potential project challenges into advantages. Our goal is to support smoother project execution, fewer conflicts, and ultimately better results for your commercial construction investment.
Conclusion: Building Your Commercial Construction Success
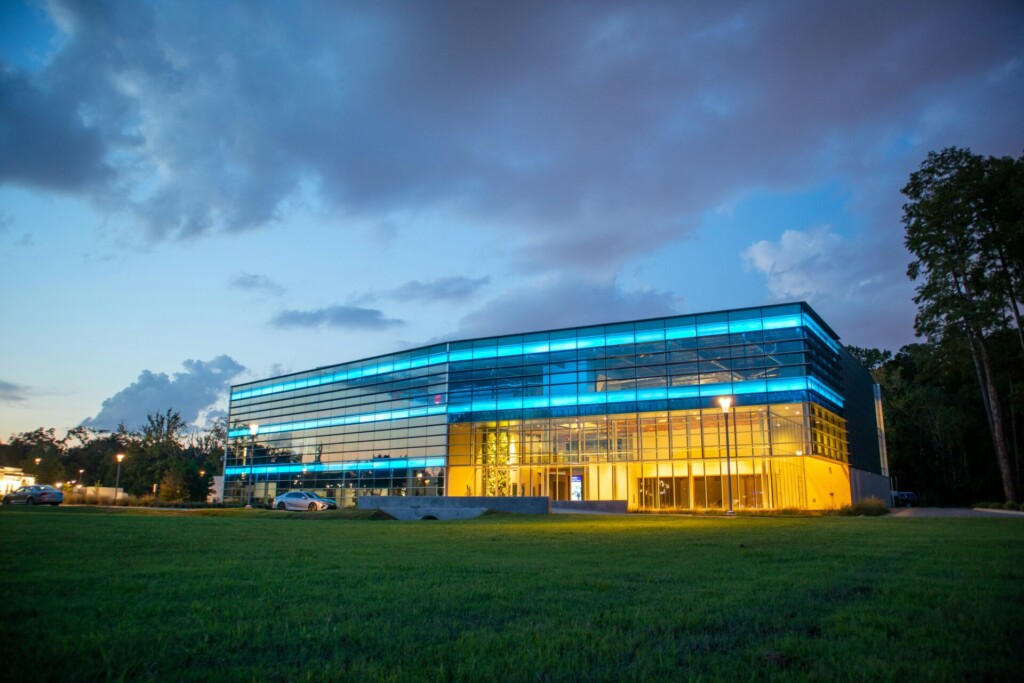
The journey of commercial construction demands strategic planning, precise execution, and dedicated partnership at every stage. Successful commercial projects can create lasting value when built on solid fundamentals. Throughout the development process, clear objectives, realistic budgets, coordination of specialized teams, and management of regulatory requirements are all crucial elements.
What truly distinguishes exceptional commercial construction projects is attention to the complete lifecycle. From initial conception through pre-construction planning, procurement, construction execution, and final delivery, constant communication and quality control can help prevent setbacks. Investments in thorough planning may pay dividends through reduced delays, controlled costs, and finished structures that serve their intended purpose for years to come.
Ready to transform your commercial construction vision into reality? Connect with our experienced team to discuss your project needs.