On a typical construction site, dust levels can be up to 100 times higher than normal, posing serious risks for operating businesses. Managing dust and debris during construction or renovation projects is crucial for maintaining safety, reducing environmental impact, and ensuring regulatory compliance. We understand the challenges of balancing ongoing operations with construction needs.
Dust and airborne pollutants pose significant health risks to workers, customers, and nearby communities. Fine particulate matter can penetrate deep into the lungs, potentially causing respiratory issues. Beyond health concerns, uncontrolled dust can damage inventory, disrupt sensitive equipment, and create an unpleasant experience for customers. Effective dust control is essential for minimizing business disruption.
At EB3 Construction, we implement comprehensive control measures to create healthier work environments and promote sustainability. Our approach addresses both immediate safety needs and long-term air quality impacts. By proactively managing dust and debris, we help businesses maintain productivity and protect their bottom line during construction projects. Proper dust management isn’t just about compliance—it’s about safeguarding your people, property, and business continuity.
What Are the Primary Sources of Construction Dust and How Can You Control Them?
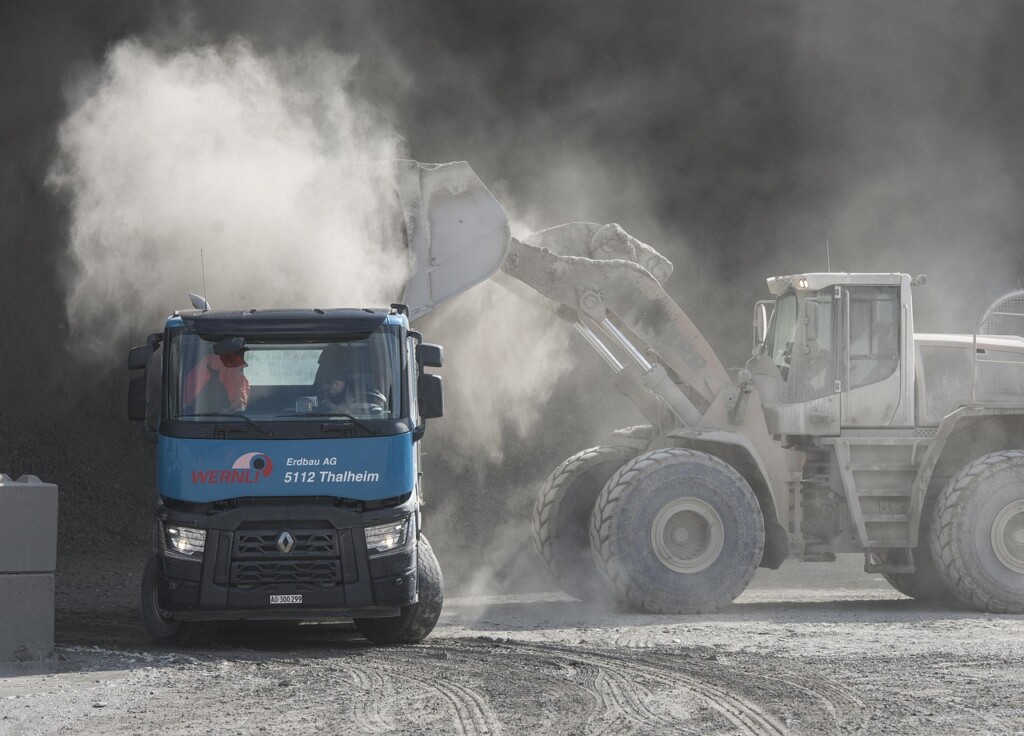
At EB3 Construction, we understand that managing dust is a critical aspect of any construction project. The first step is identifying the key sources of dust on-site. Based on our experience, the main contributors include:
- Demolition activities
- Earthmoving operations such as excavation and grading
- Vehicle and equipment movement, especially on unpaved surfaces
- Handling and storage of materials like sand, gravel, and cement
Once the dust sources are identified, we implement targeted suppression techniques. Water spraying is often our preferred method—it’s simple yet highly effective when performed correctly. For persistent dust, we frequently incorporate dust-control additives to enhance the water’s binding capability.
Covering material stockpiles is another vital strategy we use. This prevents wind from dispersing dust from sand, gravel, or other loose materials. For long-term projects, we may employ vegetative cover to stabilize exposed soil and reduce airborne dust.
Working in operational facilities requires extra caution in dust control. We use techniques such as:
- Installing physical barriers to isolate construction zones
- Placing sticky floor mats at entrances to trap dust
- Properly sealing off work areas to prevent dust migration
These methods help minimize impact on adjacent spaces that need to remain functional during construction.
By customizing our dust suppression approach to each project’s specific conditions and requirements, we maintain air quality and safety standards while ensuring work progresses efficiently. Proper dust management involves early identification of sources and applying the right combination of control measures.
Dust Source | Control Method |
---|---|
Demolition Activities | Water Spraying, Dust-Control Additives |
Earthmoving Operations (Excavation, Grading) | Water Spraying, Vegetative Cover |
Vehicle Movement on Unpaved Roads | Water Spraying, Chemical Stabilizers |
Material Handling (Sand, Gravel, Cement) | Covering Stockpiles, Dust-Control Additives |
How Should You Implement Effective Perimeter Controls and Containment Strategies?
Preventing dust and debris from escaping construction zones is crucial when working in active business environments. We implement a multi-layered approach to perimeter control and dust containment that keeps surrounding areas clean and minimizes disruption.
Outdoor Perimeter Controls
For exterior work, we establish a clear perimeter around the site with barriers. Sturdy temporary fences or windbreaks serve as the first line of defense, containing larger debris and reducing wind-driven dust. At site exits, we install wheel wash stations to prevent vehicles from tracking dirt onto public roads or clean areas of the property. This simple measure significantly reduces dust migration beyond the work zone.
We complement this with a regular schedule of street sweeping and cleaning in areas surrounding the construction site. This helps capture any dust that does manage to escape the immediate work area, keeping nearby spaces tidy and preventing the accumulation of construction debris.
Indoor Containment Strategies
When performing interior renovations or demolition, dust containment becomes even more crucial. We start by clearly demarcating construction zones with proper signage and temporary walls. Penetrations in demising walls are carefully sealed prior to any demolition work to prevent dust from migrating to occupied spaces.
One of our most effective indoor containment tools is the use of negative pressure systems. We install powerful exhaust fans that vent directly outdoors, creating negative air pressure within the work zone. This setup ensures that any airborne dust is continuously pulled out of the building rather than drifting into occupied areas.
For sensitive environments like healthcare facilities or food production areas, we may implement even more stringent controls. This may include creating negative pressure vestibules at work zone entrances or using HEPA filtration on all exhausted air.
Monitoring and Maintenance
Effective perimeter control and containment isn’t a set-it-and-forget-it proposition. We continuously monitor our control measures, performing regular inspections and maintenance to ensure they remain effective throughout the project. This vigilance allows us to quickly address any issues and maintain a clean, safe environment for both workers and building occupants.
By implementing these comprehensive perimeter controls and containment strategies, we minimize the impact of construction activities on ongoing business operations. Our approach keeps dust and debris confined to work zones, maintaining a professional appearance and healthy environment in adjacent spaces.
How Can You Develop and Execute an Effective Debris Management Plan?
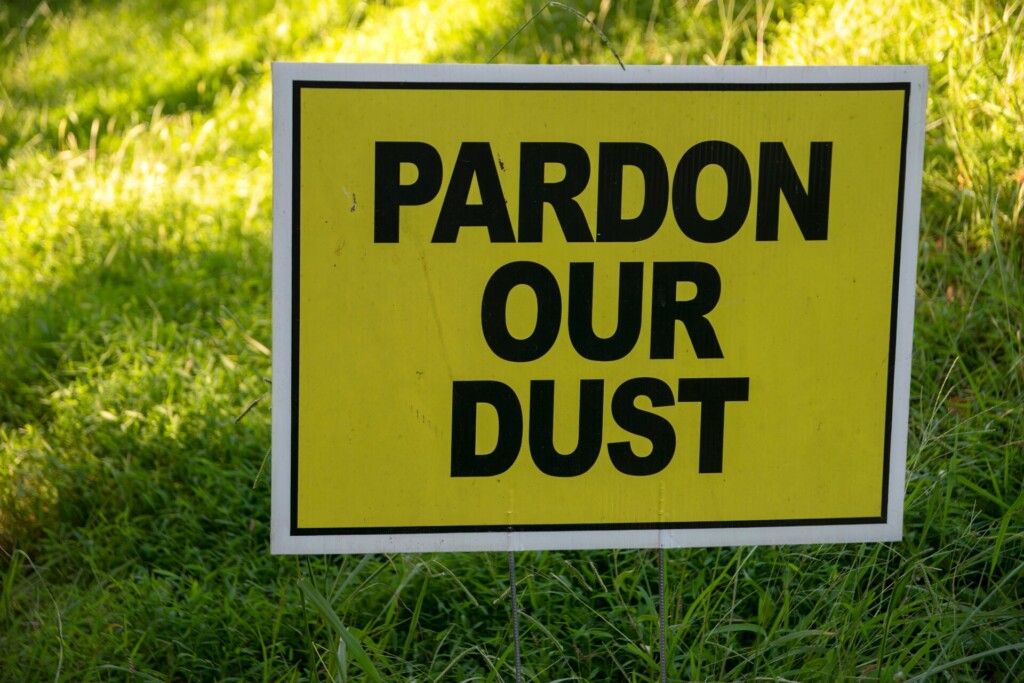
A comprehensive debris management plan is essential for streamlining the removal process and maintaining a clean, safe construction site. At EB3 Construction, we have developed a proven approach to creating and implementing effective debris management plans for our projects. Here’s how we tackle this critical task:
Developing the Plan
1. Assess debris types and volumes: We start by thoroughly evaluating the scope of work and forecasting the types and quantities of debris our project will generate. This assessment informs all subsequent planning decisions.
2. Plan for material segregation: Based on our assessment, we establish protocols for separating recyclable materials, hazardous waste, and general debris. This segregation is crucial for regulatory compliance and maximizing recycling opportunities.
3. Create a removal schedule: To prevent debris build-up, we develop a regular removal schedule tailored to the project’s pace and space constraints. This might involve daily pickups for high-volume phases or weekly removals for slower periods.
4. Designate a Waste Manager: We appoint a dedicated team member to oversee all aspects of debris management. This individual coordinates with subcontractors, monitors compliance, and adjusts the plan as needed.
5. Establish documentation procedures: Our plans include specific requirements for tracking debris types, volumes, and disposal methods. This documentation is critical for regulatory compliance and project cost management.
Executing the Plan
1. Communicate clearly: We ensure all team members and subcontractors are thoroughly briefed on the debris management plan. Key points are prominently displayed in work areas and included in all relevant contracts.
2. Conduct regular inspections: Our Waste Manager performs frequent site walk-throughs to verify proper debris handling and identify potential issues before they become problems.
3. Maintain flexibility: Construction projects are dynamic, so we build adaptability into our plans. Regular reviews allow us to adjust our approach based on changing site conditions or project requirements.
4. Prioritize safety: All debris management activities are integrated into our overall site safety plan. This includes proper personal protective equipment for debris handling and clear protocols for managing hazardous materials.
5. Leverage technology: We use digital tools to streamline documentation, track removals, and analyze our debris management performance over time.
Key Considerations for Businesses
When developing a debris management plan for active business sites, we take special care to minimize disruptions:
- Coordinate removal times to avoid peak business hours
- Establish clear pathways for customer and employee access
- Use dust control measures to maintain a clean environment
- Consider noise reduction strategies for debris handling
- Clearly communicate the plan to all affected parties, including customers
By following these best practices, we ensure our debris management plans not only meet regulatory requirements but also support efficient project execution and minimize impact on ongoing business operations.
Debris Type | Examples | Best Practices |
---|---|---|
Construction Debris | Bricks, shingles, metal | Segregate, recycle, reuse |
Natural Debris | Trees, branches, vegetation | Composting, mulching |
Hazardous Waste | Chemicals, asbestos | Special handling and disposal |
Personal Property Debris | Furniture, electronics | Donate or recycle |
Effective debris management is a cornerstone of responsible construction practices. By developing and executing a well-thought-out plan, we can significantly reduce environmental impact, improve site safety, and enhance overall project efficiency.
What Sustainability Practices Should You Incorporate in Debris Management?
At EB3 Construction, we recognize that sustainability is not just an environmental imperative but also a smart business practice. By incorporating sustainability into our debris management approach, we contribute to a greener future while often realizing cost savings and enhancing our reputation in the industry.
Recycling and Material Recovery
We prioritize recycling and material recovery whenever possible. This includes:
- Separating and recycling scrap metal, which can often be sold to generate additional revenue
- Grinding untreated wood for use as mulch or biomass fuel
- Crushing and reusing concrete as aggregate for new projects or road base
- Recycling cardboard, paper, and other packaging materials
By diverting these materials from landfills, we reduce our environmental footprint while potentially lowering disposal costs.
Donations
When we have surplus materials that are still usable, we explore opportunities to donate them to local charities or building material reuse centers. This not only keeps materials out of the waste stream but also supports our local communities.
LEED-Certified Disposal Services
We partner with haulers who offer LEED-certified disposal services. These providers ensure that materials are properly sorted and diverted to appropriate recycling or reuse streams, helping projects earn points toward LEED certification.
Waste Metrics Tracking
We implement systems to track our waste metrics, including types and quantities of materials recycled, reused, or disposed of. This data allows us to:
- Set and monitor waste reduction goals
- Identify areas for improvement in our waste management practices
- Provide transparent reporting to clients and stakeholders
- Demonstrate our commitment to sustainability in bids and proposals
Use of Recycled Materials
Where possible, we incorporate recycled materials into our projects. This can include:
- Recycled-content insulation
- Reclaimed wood for flooring
- Recycled glass aggregates in concrete
Using these materials not only reduces demand for virgin resources but can also decrease dust-generating processes during construction.
Prefabrication and Off-Site Construction
We utilize prefabrication and off-site construction techniques when appropriate. By manufacturing components in controlled factory settings, we can:
- Minimize material waste through precise cutting and assembly
- Reduce on-site dust and emissions
- Decrease overall project debris at the job site
By integrating these sustainability practices into our debris management approach, we not only reduce our environmental impact but also position ourselves as responsible industry leaders. This commitment to sustainable construction practices often translates to improved project outcomes, cost savings, and a competitive edge in the increasingly environmentally conscious market.
Implementing sustainable debris management practices requires ongoing education and engagement of our team members and subcontractors. However, the long-term benefits to our business, our clients, and the environment make it a worthwhile investment in the future of construction.
Conclusion: Balancing Construction Progress with Business Operations
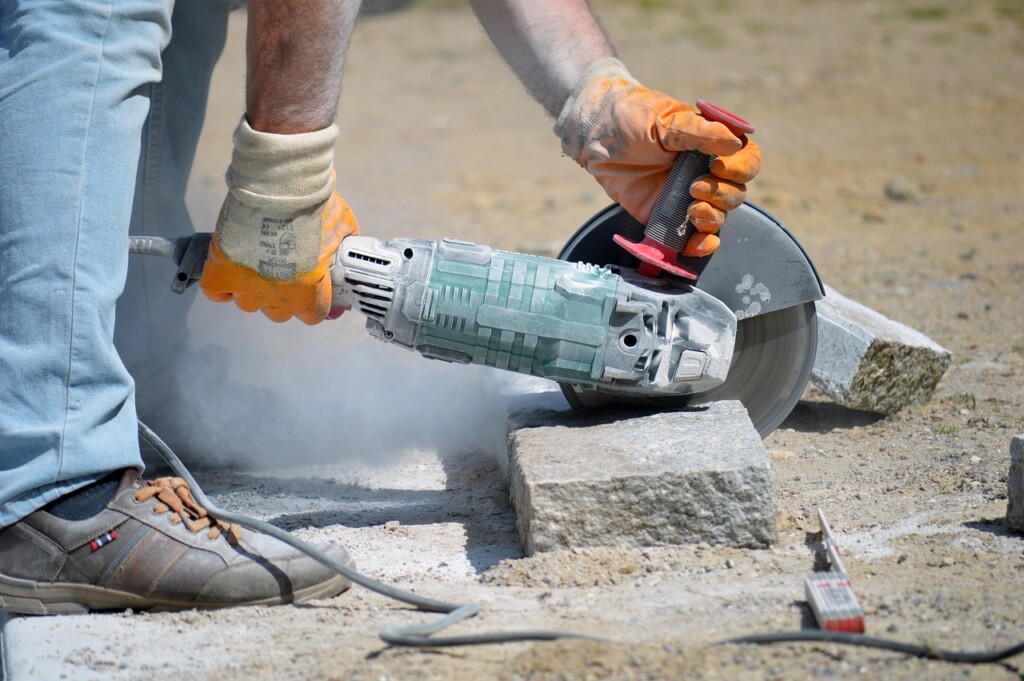
Effectively managing construction dust and debris is crucial for safeguarding the health of workers and customers, ensuring regulatory compliance, and maintaining business operations during construction projects. At EB3 Construction, we understand that adopting best practices such as dust suppression, proper debris management, perimeter controls, and sustainability initiatives leads to safer, more efficient work environments while minimizing disruption to ongoing business activities.
Our experience shows that investing in proper planning, comprehensive worker training, and effective containment measures not only improves safety outcomes but also enhances business continuity and customer satisfaction throughout the construction process. We take a proactive approach to dust management, employing advanced suppression techniques and coordinating closely with facility managers to develop customized plans that balance progress with minimal operational impact.
By prioritizing efficient dust and debris control strategies, construction professionals can deliver projects more swiftly while demonstrating environmental responsibility and a commitment to stakeholder wellbeing. We encourage developers and property owners to partner with experienced contractors who recognize the critical importance of dust management in today’s regulatory landscape.
To learn more about how EB3 Construction can help you implement top-notch dust control measures on your next project, contact our team today.