Failed inspections can derail even the most carefully planned construction projects. When a build doesn’t meet code requirements or quality standards, the consequences ripple through every aspect of the job. Timelines stretch, budgets balloon, and reputations take a hit. For project managers and stakeholders, inspection failures create a challenging scenario of delays, cost overruns, and potential legal headaches.
We’ve seen how quickly a single failed inspection can escalate into major issues. Crews suddenly scramble to address deficiencies while other work grinds to a halt. Rework consumes valuable time and resources. With each passing day, the financial impacts compound—from idle equipment fees to liquidated damages for missed deadlines.
The effects extend far beyond the immediate project. Word travels fast in this industry. Inspection failures raise red flags for future clients and partners, potentially damaging a company’s hard-earned reputation for quality and reliability. For contractors operating on thin margins, the long-term business impacts can be severe.
This is why proactively addressing potential inspection issues is critical. By understanding common pitfalls and implementing robust quality control measures, construction teams can avoid the costly effects of failed inspections. The stakes are simply too high to leave compliance and quality to chance.
What Are the Immediate Consequences of Failed Inspections?
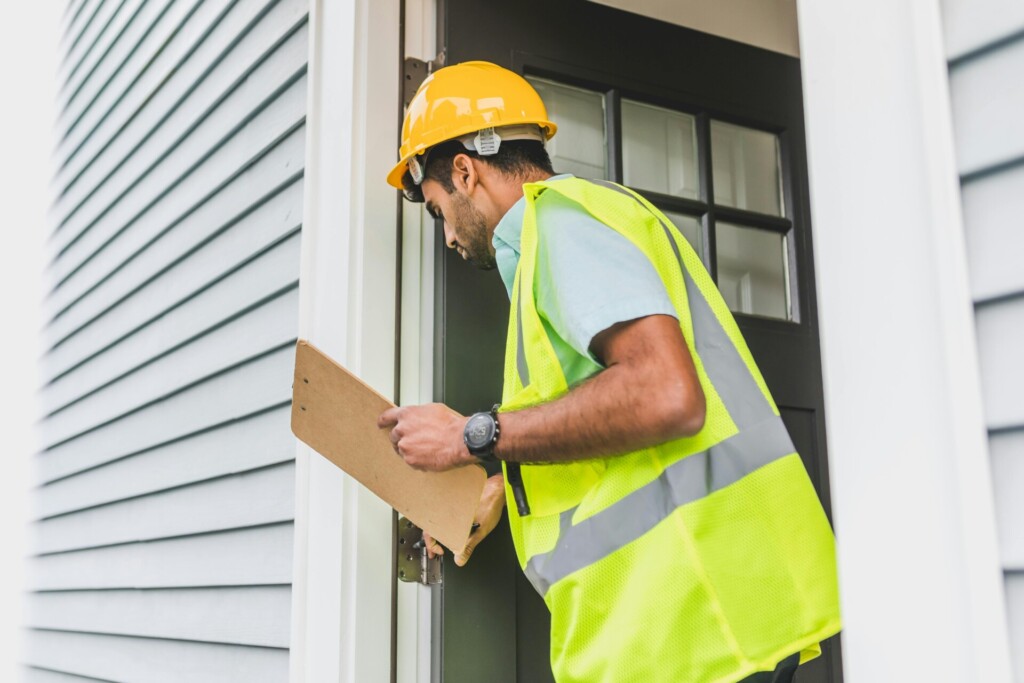
When a construction project fails inspection, the repercussions are swift and significant. As general contractors, we have experienced firsthand how a failed inspection can halt work and create a cascade of challenges. Let’s examine the immediate consequences:
Work Stoppage and Schedule Disruptions
The most immediate and visible impact is the cessation of work. Inspectors have the authority to issue stop work orders, causing all or part of the project to come to a standstill. This isn’t just an inconvenience—it’s a major disruption that can throw carefully planned schedules into disarray. We often must scramble to reallocate resources and adjust timelines, which can have ripple effects across the entire project.
Nonconformance Reports and Rework
Failed inspections typically result in detailed nonconformance reports. These documents outline exactly where our work has fallen short of regulatory requirements or project specifications. Addressing these issues isn’t just about fixing the immediate problem—it often involves extensive rework. This means dedicating additional labor hours and materials to bring everything up to code, essentially doubling our efforts in some areas.
Cost Overruns
The financial impact of a failed inspection can be substantial. We incur increased labor costs from the rework required, additional material expenses, and often face penalties for non-compliance. These unplanned costs can quickly erode our profit margins. For example, a failed electrical inspection might require us to rewire an entire floor, incurring thousands in unexpected expenses.
Regulatory Penalties and Legal Issues
Beyond the immediate project costs, failed inspections can lead to regulatory penalties. These fines can vary widely depending on the severity of the violation and local regulations. In some cases, we have seen penalties reach tens of thousands of dollars for serious infractions. Moreover, repeated failures or egregious violations can result in more severe consequences, including potential legal action or damage to our contractor license status.
Reputational Damage
While less tangible, the reputational impact of failed inspections shouldn’t be underestimated. Word travels fast in the construction industry, and a history of inspection failures can make it harder to win future contracts or maintain positive relationships with subcontractors and suppliers. We have learned that maintaining a strong track record of passing inspections is crucial for long-term success in this business.
To mitigate these risks, we have implemented rigorous quality control measures and pre-inspection checklists. By being proactive and thorough in our approach to compliance, we aim to catch and correct any issues before they become costly inspection failures. It’s an investment in time and resources upfront, but one that pays dividends in avoiding the severe consequences of failed inspections.
What Are the Long-Term Effects on Project Viability?
Failed inspections can significantly affect the overall viability of construction projects, extending beyond immediate disruptions. When critical inspections fail, they create a domino effect of delays that severely impact the entire project timeline. These delays can risk financing arrangements, causing projects to drag on longer than anticipated.
A contractor’s reputation also suffers when inspections consistently fail. News spreads quickly within the industry, making it more difficult to secure future work and maintain a sustainable business. Insurance companies also take note and often require proof of compliance with building codes before providing or continuing coverage. This can leave contractors vulnerable to significant liability gaps.
Perhaps most concerning are the potential structural issues that can arise from cutting corners or failing to meet code requirements. While these issues may not be immediately apparent, subpar work can lead to catastrophic failures months or years later. This often results in extremely costly rebuilds, puts workers and occupants at risk of injury, and in the worst cases can lead to fatalities.
We’ve seen how quickly reputation and viability can crumble in high-profile cases of major structural failures. The deadly collapse of the Champlain Towers South condo in Florida and the Berkeley balcony collapse that killed six Irish students highlight the human toll when code compliance and proper inspections are neglected. While these are extreme examples, they underscore the importance of taking a long-term view and never compromising on safety standards.
Ultimately, the compounding effects of failed inspections create a vicious cycle that threatens a contractor’s ability to stay in business. Short-term cost-cutting or rushing often leads to exponentially higher costs and risks over time. By maintaining rigorous quality control and viewing inspections as opportunities for improvement rather than obstacles, contractors can protect their long-term viability and build a sustainable future.
How Should Teams Respond to Failed Inspections?
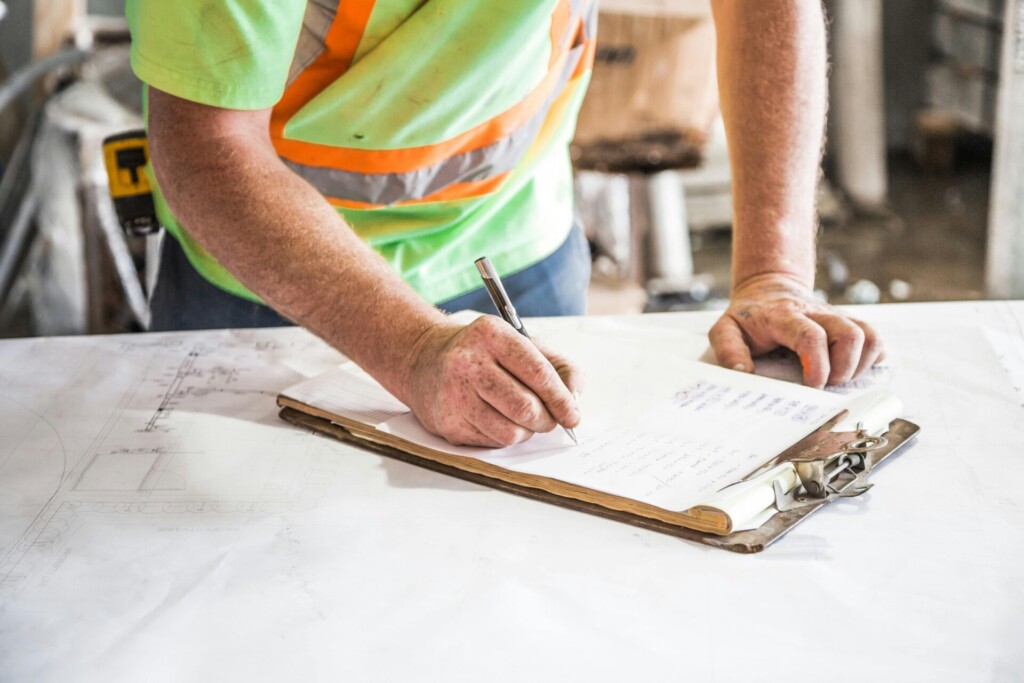
When a construction project fails inspection, a swift and strategic response is essential. At EB3 Construction, we’ve developed a systematic approach to address inspection failures and get projects back on track quickly.
Review and Analyze
We begin by thoroughly reviewing the inspection report to identify all non-compliant items. Our project managers carefully analyze each point of failure, consulting with relevant team members to understand the root causes. This detailed examination allows us to develop a comprehensive understanding of the issues at hand.
Develop a Detailed Correction Plan
Armed with a clear picture of the problems, we create a detailed correction plan. This plan outlines specific remediation steps, assigns clear responsibilities to team members, and establishes realistic timelines for completing each task. We prioritize critical issues that may impact safety or project timelines.
Communicate Transparently with Stakeholders
Open communication is crucial during this process. We promptly inform all relevant stakeholders – including clients, subcontractors, and regulatory bodies – about the situation. Our project managers provide regular updates on the correction plan and progress, ensuring everyone remains aligned and informed throughout the remediation process.
Document All Corrective Actions
Meticulous documentation is a cornerstone of our approach. As we implement corrective measures, we carefully record all actions taken, including photographic evidence where appropriate. This comprehensive record-keeping not only demonstrates our commitment to quality but also provides valuable reference for future inspections and quality control efforts.
Schedule Re-inspection Promptly
Once corrections are complete, we move quickly to schedule a re-inspection. Our goal is to minimize project delays while ensuring all issues have been fully addressed. Before the re-inspection, we conduct our own internal review to verify compliance and identify any potential oversights.
Implement Additional Quality Control Measures
Learning from inspection failures is crucial for ongoing improvement. We use these experiences to refine and enhance our quality control processes. This may involve additional training for team members, implementing new checklists or inspection protocols, or increasing the frequency of internal quality checks to prevent similar issues in the future.
By following this structured approach, we at EB3 Construction ensure that inspection failures are addressed promptly and thoroughly, minimizing disruptions to project momentum and upholding our commitment to quality and safety standards.
Responding effectively to failed inspections requires a balance of swift action and careful planning. By following a systematic approach, construction teams can turn these challenges into opportunities for improvement, ultimately delivering higher quality projects and building stronger relationships with clients and regulatory bodies.
How Can Construction Teams Prevent Inspection Failures?
Preventing inspection failures begins with proactive quality control measures. Construction teams should thoroughly review plans and specifications before beginning work to understand compliance requirements. Conducting regular self-inspections throughout the construction process can identify issues before official inspections occur, allowing teams to address problems early and avoid costly rework and delays.
Investing in proper training for all workers is crucial to ensure everyone understands code requirements and quality standards. Well-trained crews are more likely to execute work correctly the first time. Specific training on common inspection failure points is particularly valuable. For example, a framing crew could receive targeted instruction on proper nailing patterns and load-bearing wall requirements.
Digital inspection tools can streamline compliance tracking and documentation. Mobile apps enable field personnel to easily record inspection results, attach photos, and flag issues in real-time. This creates a clear audit trail and helps teams stay on top of open items. Some platforms even integrate with building information modeling (BIM) software to link inspection data directly to 3D models.
Maintaining open communication with inspectors and regulatory agencies helps to clarify expectations and address potential issues early. Proactively reaching out to discuss complex design elements or unusual construction methods can prevent misunderstandings. Some jurisdictions offer pre-construction meetings to review plans and inspection protocols—taking advantage of these opportunities demonstrates a commitment to compliance.
Finally, establishing a culture of quality is key for long-term inspection success. Empowering workers at all levels to speak up about potential issues and rewarding attention to detail are essential. When quality is seen as everyone’s responsibility—not just management’s—inspection readiness becomes ingrained in daily operations.
By implementing these proactive strategies, construction teams can significantly reduce the risk of inspection failures. The upfront investment in training, technology, and communication pays off through smoother project execution and improved relationships with regulatory bodies. Ultimately, a prevention-focused approach leads to higher-quality buildings and infrastructure for end users.
Conclusion: Turning Inspection Failures into Opportunities
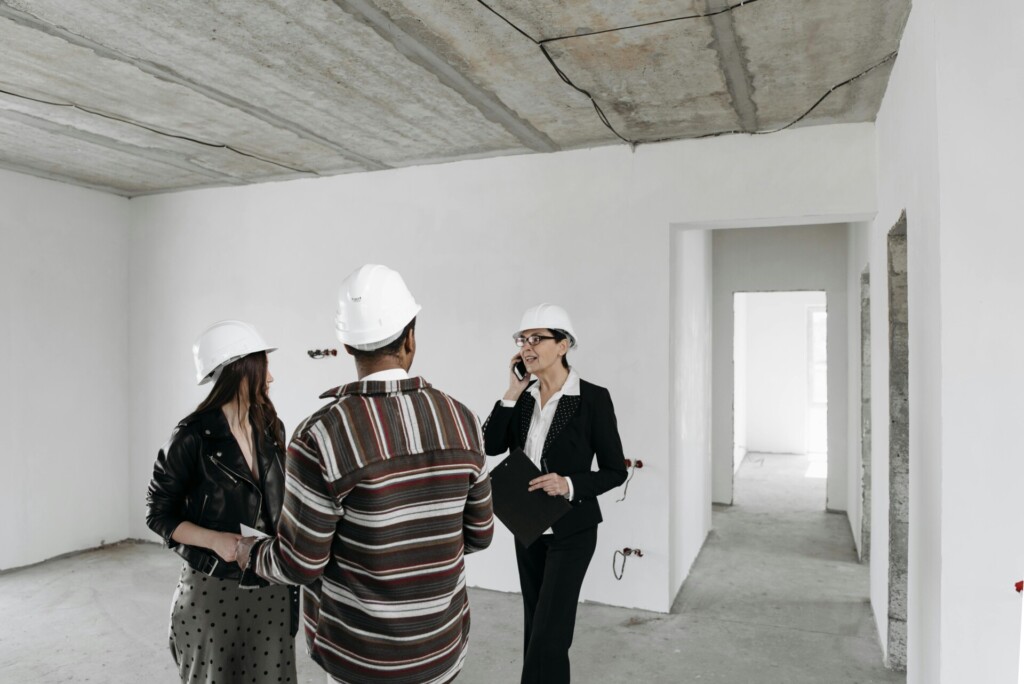
While construction inspection failures present significant challenges, they also offer opportunities for improvement. By understanding the potential consequences and implementing proactive measures, we can reduce the risk of failed inspections. When failures occur, responding strategically allows us to limit damage and strengthen processes for future projects.
At EB3 Construction, we view inspection failures as catalysts for continuous improvement. Each setback provides valuable insights that we use to refine our quality control procedures, enhance communication protocols, and elevate our overall standards of excellence. By cultivating a culture of compliance and embracing lessons learned, we transform challenges into stepping stones toward construction excellence.
With proper planning, robust quality control systems, and open lines of communication, we effectively meet inspection requirements and consistently deliver safer, more compliant structures. Our commitment to turning inspection failures into opportunities for growth ensures that each project brings us closer to our goal of setting new industry benchmarks for quality and reliability.
To learn more about how EB3 Construction can help ensure your next project meets and exceeds all inspection requirements, contact our team today.