Moisture control is critical in new construction projects. If left unchecked, excess moisture can quickly lead to mold growth, compromising building integrity and occupant health. We know firsthand how devastating mold issues can be, having seen multi-million-dollar claims arise from moisture problems during construction.
Mold requires three key ingredients to thrive: heat, water, and food sources like wood or drywall. Construction sites provide the perfect environment, with ambient temperatures, exposed materials, and numerous potential moisture entry points. Water can infiltrate through obvious leaks but also via condensation, high humidity, or even capillary action drawing moisture into porous materials. The timeframe for mold growth is short — spores can begin growing in as little as 24-48 hours once materials become damp.
As general contractors, we take a proactive approach to moisture management throughout the build process. Proper material moisture control strategies are essential not just for preventing mold growth but also for ensuring overall building durability and performance. By understanding how moisture behaves on construction sites and implementing proper controls, we create healthier, longer-lasting structures for our clients.
What Are the Primary Sources of Moisture During Construction?
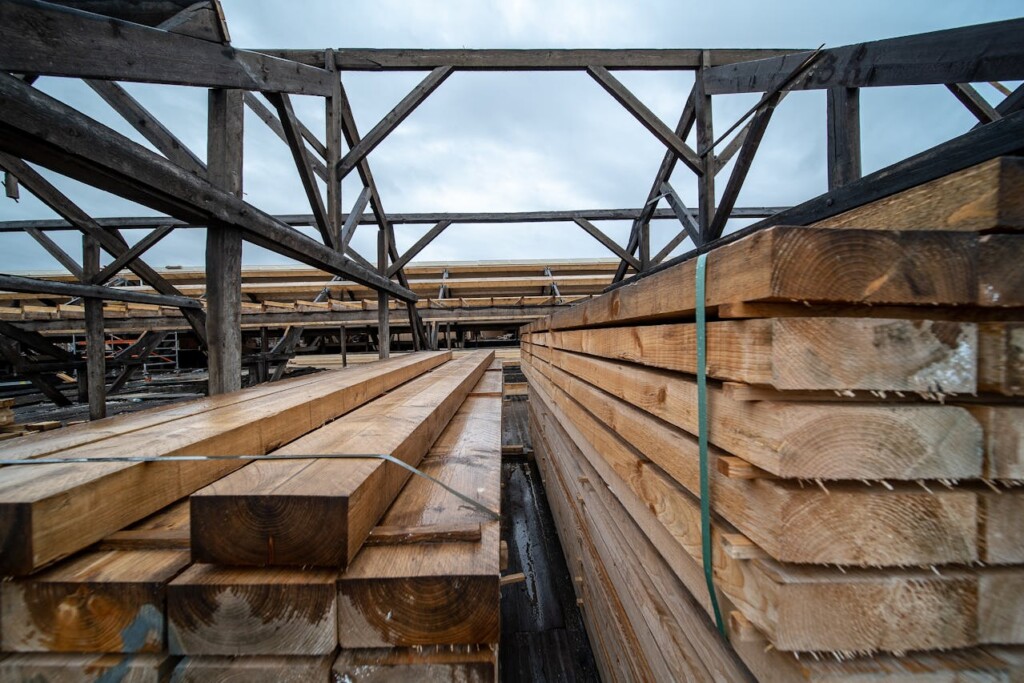
As general contractors, we encounter numerous moisture challenges on construction sites that require diligent management. Understanding and addressing these sources is crucial for preventing water damage and ensuring the long-term integrity of the structures we build. Here, we examine the key areas where moisture can become problematic during the construction process.
Site Drainage Issues
One of the foremost concerns we face is poor site drainage. When stormwater isn’t properly directed away from the building, it can lead to water accumulation around foundations and in excavated areas. This often results in saturated soil conditions that can compromise structural integrity and create ideal environments for mold growth. To mitigate these risks, we implement comprehensive drainage plans, including proper grading, installation of French drains, and strategic placement of sump pumps in basements and crawl spaces.
Inadequate Building Protection
During the early stages of construction, when the building envelope is not yet complete, protecting the structure from the elements becomes critical. We employ a variety of temporary measures, such as tarps, plastic sheeting, and temporary roofing systems, to shield unfinished areas from rain and snow. However, these protective measures are not foolproof, and vigilant monitoring is necessary to ensure their effectiveness throughout the construction timeline.
Material Moisture Absorption
Wood framing and subflooring materials are particularly susceptible to moisture absorption. When exposed to rain or high humidity, these materials can soak up significant amounts of water, leading to warping, swelling, and even mold growth if not properly addressed. We carefully monitor the moisture content of wood materials using moisture meters and implement drying strategies, such as dehumidification and increased ventilation, to bring moisture levels down to acceptable ranges before enclosing walls or installing finishes.
Construction Processes Introducing Moisture
Certain construction activities inherently introduce moisture into the building. For example:
- Concrete pouring and curing
- Application of water-based adhesives and coatings
- Drywall mudding and taping
- Pressure washing of surfaces
We carefully schedule these activities to allow for adequate drying time and use moisture monitoring tools to ensure that affected areas are sufficiently dry before proceeding with subsequent construction phases.
Design Flaws and Construction Defects
Perhaps the most insidious sources of moisture problems are those stemming from design flaws or construction defects. These can include improperly detailed roof-to-wall transitions, inadequate flashing around windows and doors, or gaps in the building envelope that allow water intrusion. Our quality control processes involve rigorous inspections at key stages of construction to identify and address potential issues before they become hidden behind finishes.
When we do encounter design or construction-related moisture problems, we document them thoroughly and work closely with architects and subcontractors to develop effective solutions. This might involve redesigning problematic details, implementing additional waterproofing measures, or in some cases, removing and replacing affected components.
Managing Moisture for Project Success
Effectively managing moisture during construction requires a multifaceted approach. We combine proactive planning, ongoing monitoring, and swift corrective action to minimize the risk of moisture-related issues. By addressing these primary sources of construction moisture head-on, we help ensure that the buildings we deliver are dry, durable, and ready to serve their intended purpose for years to come.
As construction professionals, our role extends beyond simply building structures—we must also act as guardians against the destructive force of unwanted moisture. Through vigilance and expertise, we transform potential moisture challenges into opportunities to demonstrate our commitment to quality and long-term value for our clients.
How Can Builders Implement Effective Moisture Control Strategies?
Effective moisture control is critical for ensuring the long-term integrity of any construction project. At EB3 Construction, we understand the importance of implementing comprehensive strategies to manage moisture throughout the building process. Our approach focuses on sealing the building envelope, monitoring moisture levels, and utilizing proper ventilation techniques.
Sealing the Building Envelope
One of our top priorities is sealing the building envelope as early as possible in the construction process. We install building papers and glazing promptly to create a barrier against moisture intrusion. This early intervention helps protect interior elements and allows interior work to proceed without exposure to excess moisture.
Air sealing is another crucial step we take before installing insulation. By meticulously sealing potential air leaks, we prevent moisture-laden air from entering wall cavities where it could condense and cause damage. This practice not only enhances moisture control but also improves the overall energy efficiency of the building.
Monitoring and Managing Moisture Levels
Throughout the construction process, we closely monitor wood moisture content using specialized meters. Our target is to maintain wood moisture levels below 15%, never exceeding 19%. This vigilance is essential for preventing mold growth and ensuring the structural integrity of wooden components.
To actively manage moisture levels, we employ dehumidifiers and ventilators during the construction phase. These tools help us maintain relative humidity below 70%, creating an environment that’s inhospitable to mold and mildew. This proactive approach to moisture management is particularly crucial in regions like the Pacific Northwest, where high humidity levels can be challenging.
Developing Comprehensive Strategies
At EB3, we develop tailored moisture control strategies for each project. These strategies include proactive steps to prevent moisture issues before they occur. We consider factors such as local climate conditions, building design, and material choices to create a holistic approach to moisture management.
Our moisture control plans also include response protocols for water events. We ensure that water removal equipment is readily available on-site, allowing for quick action if unexpected moisture issues arise. This preparedness can make the difference between a minor inconvenience and a major setback in the construction timeline.
Innovative Approaches to Moisture Control
We stay abreast of the latest advancements in construction technology. For instance, we’ve begun incorporating smart sensors in some of our projects to monitor real-time humidity levels. These sensors can alert our team to potential moisture issues before they become visible, allowing for swift intervention.
Additionally, we’re exploring the use of innovative building materials that offer superior moisture resistance. Materials like self-healing concrete and hydrophobic coatings show promise in enhancing long-term moisture control in structures.
Humidity of the in-use location | EMC of the in-use location | Corresponding MC the wood will attain at this location |
19-25% | 5% | 5% |
26-32% | 6% | 6% |
33-39% | 7% | 7% |
40-46% | 8% | 8% |
47-52% | 9% | 9% |
By implementing these strategies, we at EB3 Construction ensure that moisture control is an integral part of our building process, not an afterthought. Our comprehensive approach helps protect the investments of developers and property owners by creating structures that are resilient to moisture-related issues from the ground up.
Effective moisture control is an ongoing process that extends beyond the construction phase. We educate our clients on the importance of continued monitoring and maintenance to ensure the long-term integrity of their buildings. This commitment to quality and durability is what sets EB3 Construction apart in the industry.
What Building Design Elements Help Prevent Moisture Problems?
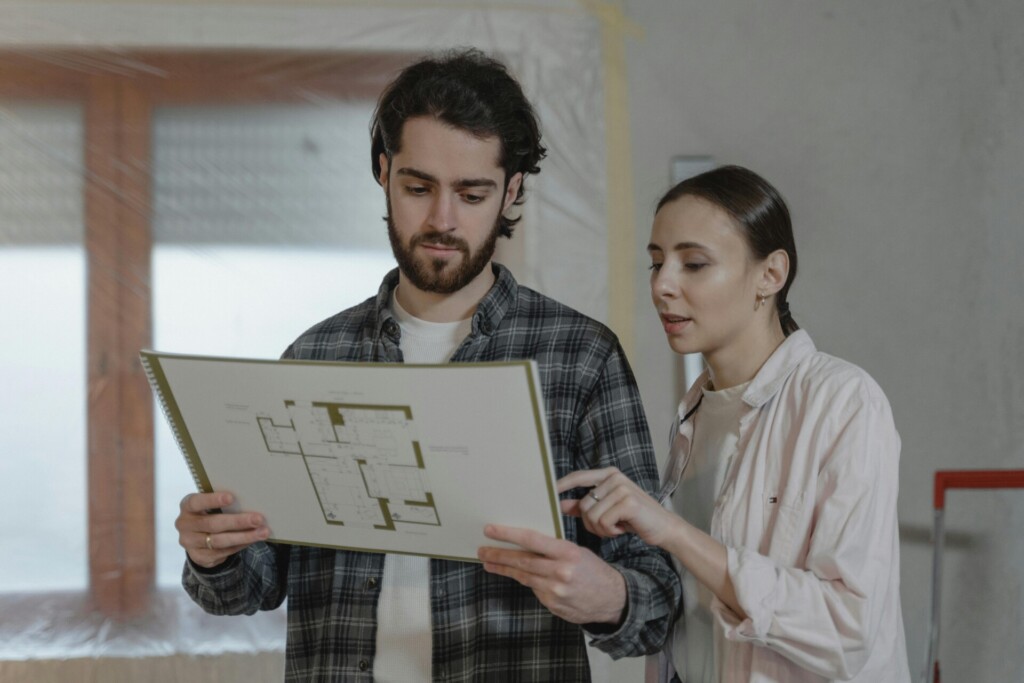
As general contractors, we know that proper building design plays a critical role in moisture prevention. Our experience has shown that implementing key elements during construction can significantly reduce moisture problems and help keep structures dry and problem-free. Let’s explore some of the most important design features we focus on:
Site Drainage and Foundation
We always ensure finished floor levels are at least 12 inches above flood plains. This provides a crucial buffer against potential water intrusion. Additionally, we grade the surrounding landscape to slope away from the building, typically aiming for a 6-inch drop over 10 feet. This directs water away from the structure, preventing pooling near the foundation.
Roof Design
The roof is your building’s first line of defense against moisture, so we pay special attention to its design. We implement a minimum 3-in-12 pitch to ensure adequate water runoff. Eave overhangs of at least 18 inches are standard in our builds, as they shield walls from direct rainfall and reduce splash-back. Proper downspouts that discharge at least 3 feet away from the building foundation are also crucial components we never overlook.
Wall Protection
Walls require multiple moisture prevention strategies. We always install capillary breaks between foundations and framing to stop moisture wicking up from the ground. Sealing all top plate penetrations is another critical step we take to prevent air and moisture infiltration. Maintaining proper clearance (typically 6 inches) between exterior cladding and grade is another best practice we follow to avoid water splashing onto siding.
Interior Moisture Management
Managing interior moisture is just as important as keeping external water out. We install effective bathroom and kitchen ventilation systems that vent directly to the exterior, not into attic spaces. These systems remove moisture at its source, preventing it from spreading throughout the building.
By implementing these design elements, we create a comprehensive moisture management strategy that protects the building from foundation to roof. Our approach not only prevents immediate water intrusion but also safeguards against long-term moisture-related issues like mold growth and structural damage.
Component | Moisture Prevention Design Elements |
Site Drainage | Proper grading, installation of French drains, placement of sump pumps |
Building Protection | Use of tarps, plastic sheeting, temporary roofing |
Material Management | Monitor moisture content, implement drying strategies |
Construction Process | Schedule for adequate drying, use of moisture monitoring tools |
Design and Construction Quality | Rigorous inspections, redesign problematic details, additional waterproofing measures |
While these design elements form the foundation of moisture control, it’s important to note that every building is unique. We always consider local climate conditions, building use, and specific site characteristics when fine-tuning our moisture prevention strategies. Our goal is to create a tailored plan that not only meets code requirements but also provides long-lasting protection against moisture-related problems.
How Should Construction Materials Be Managed to Prevent Moisture Problems?
At EB3 Construction, we recognize that effective material management is crucial for preventing moisture issues in construction projects. Our approach prioritizes protecting materials, especially porous items like drywall and wood, by implementing strict storage protocols in dry, controlled environments.
We carefully check the moisture content of wood, ensuring it remains below the critical 15% threshold before installation. This practice is essential to prevent warping, mold growth, and structural issues in the future. For materials exposed to moisture, we apply thorough drying procedures, allowing ample time for equilibration before incorporating them into building assemblies.
Our proactive stance includes our supply chain management. We’ve established robust contractual arrangements with lumber suppliers, specifying acceptable moisture content levels and outlining clear procedures for handling materials showing early signs of mold or water damage. This upstream quality control significantly reduces the risk of moisture-related issues at our job sites.
Strategies for Weather Events and Construction Delays
Construction timelines can be unpredictable, and we’re prepared for scenarios where work might be temporarily halted. In such cases, our teams implement comprehensive measures to dry out and seal off materials, effectively preventing mold development during inactive periods. This level of care ensures that work can resume smoothly without compromising the integrity of the building materials.
Weather events pose a significant challenge in material management. We employ a range of protective measures, from temporary shelters to specialized coverings, safeguarding materials from rain, snow, and high humidity. Our site managers are skilled at anticipating weather patterns and taking preemptive action by moving sensitive materials to protected areas when adverse conditions are forecasted.
Reintroducing materials after weather events is a critical phase. We conduct thorough moisture assessments using both visual inspections and moisture meters to ensure that no compromised materials enter the final structure. This vigilance is crucial for maintaining the long-term health and durability of the buildings we construct.
On-Site Moisture Testing and Control
To maintain consistent quality control, we’ve implemented simple yet effective on-site moisture testing protocols. Our construction teams are equipped with pinless moisture meters, allowing for quick, non-invasive checks of the moisture content in various materials. For wood, specifically, we use pin-type moisture meters to get precise readings at different depths, ensuring that moisture levels are acceptable throughout the material, not just on the surface.
In addition to testing, we’ve developed a systematic approach to material rotation on job sites. This ‘first in, first out’ system minimizes the time materials spend in storage, reducing their exposure to potential moisture sources. We also maintain strict guidelines for material elevation, ensuring that all stored items are kept off the ground on pallets or risers, promoting air circulation and preventing ground moisture absorption.
By integrating these comprehensive material management strategies, we at EB3 Construction ensure that moisture problems are prevented at every stage of the construction process. Our meticulous approach not only protects the immediate integrity of the materials but also contributes significantly to the long-term durability and health of the structures we build.
Common Material | Acceptable Moisture Content (%) |
---|---|
Wood | 15% |
Drywall | 1% |
Concrete (RH) | 75% |
Insulation | Should be dry (no significant moisture) |
Conclusion: Creating a Comprehensive Moisture Prevention Plan
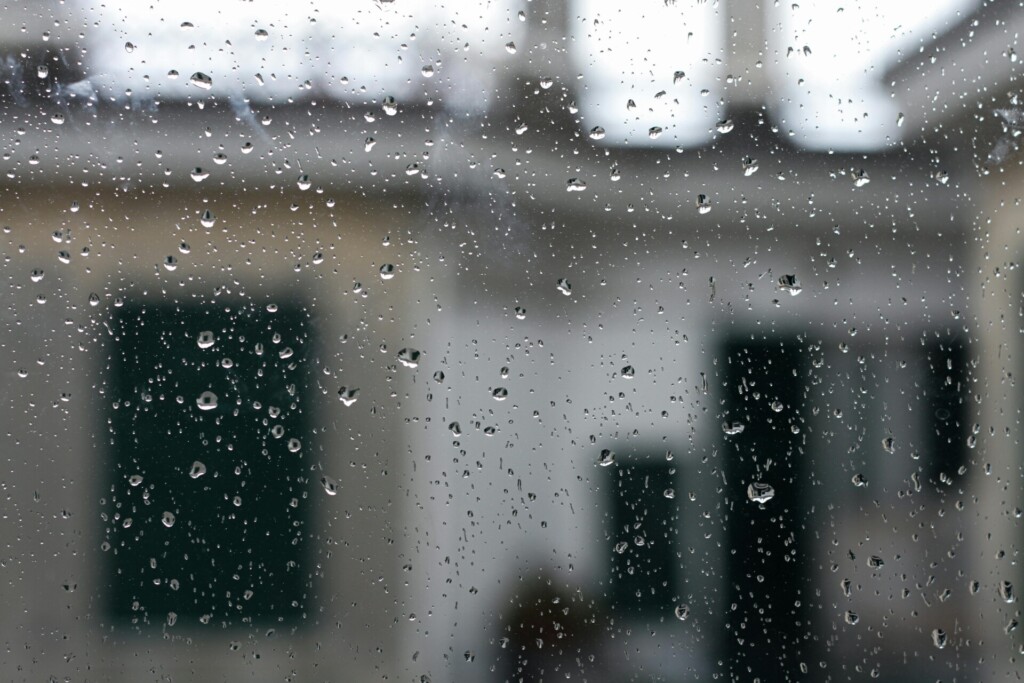
While completely eliminating moisture during construction presents challenges, implementing a comprehensive moisture prevention strategy significantly reduces the risk of mold and improves building durability. We prioritize sealing the building envelope quickly, closely monitoring material moisture content, strategically deploying dehumidifiers when needed, and adhering to proper design and construction best practices throughout the project lifecycle.
When moisture issues are discovered, our teams take immediate action, recognizing that mold can develop within just 24-48 hours. By maintaining vigilant moisture control from start to finish, we protect our clients’ investments, mitigate potential liability concerns, and ultimately deliver healthier, longer-lasting buildings.
Through diligent planning and execution, effective moisture prevention is an achievable goal that enhances building performance and occupant well-being. The strategies outlined—from material protection to rapid response protocols—work in concert to create resilient structures. By championing moisture control, we are not just avoiding mold but laying the foundation for superior buildings that stand the test of time.
To learn more about how EB3 Construction implements comprehensive moisture prevention on our projects, contact our team today.