Pre-construction marks the essential planning phase before the onset of physical construction. This strategic period serves as the foundation for successful projects, transforming conceptual ideas into actionable plans complete with specific timelines, budgets, and resource allocations. Our approach to this phase is methodical, as thorough planning now prevents costly problems later.
During pre-construction, our team collaborates with project owners, architects, engineers, and other stakeholders to refine designs, select appropriate contractors, analyze potential risks, and develop comprehensive schedules. This early involvement helps us address key questions about design feasibility, resource organization, and permitting requirements before construction begins. Given the recent California drought, pre-construction water usage planning has become even more critical for projects in water-restricted areas.
The value of this pre-development stage is significant. Construction projects lacking robust pre-construction planning often face budget overruns, change orders, schedule delays, and unforeseen site condition challenges. A 2023 industry report found that projects with comprehensive pre-construction planning achieved profit margins averaging 23%, while those with inadequate planning averaged losses of 3%. Our experience shows that investing time in this phase leads to smoother project execution and better financial outcomes. Will your next project include adequate pre-construction planning?
Who Makes Up the Pre-Construction Team?
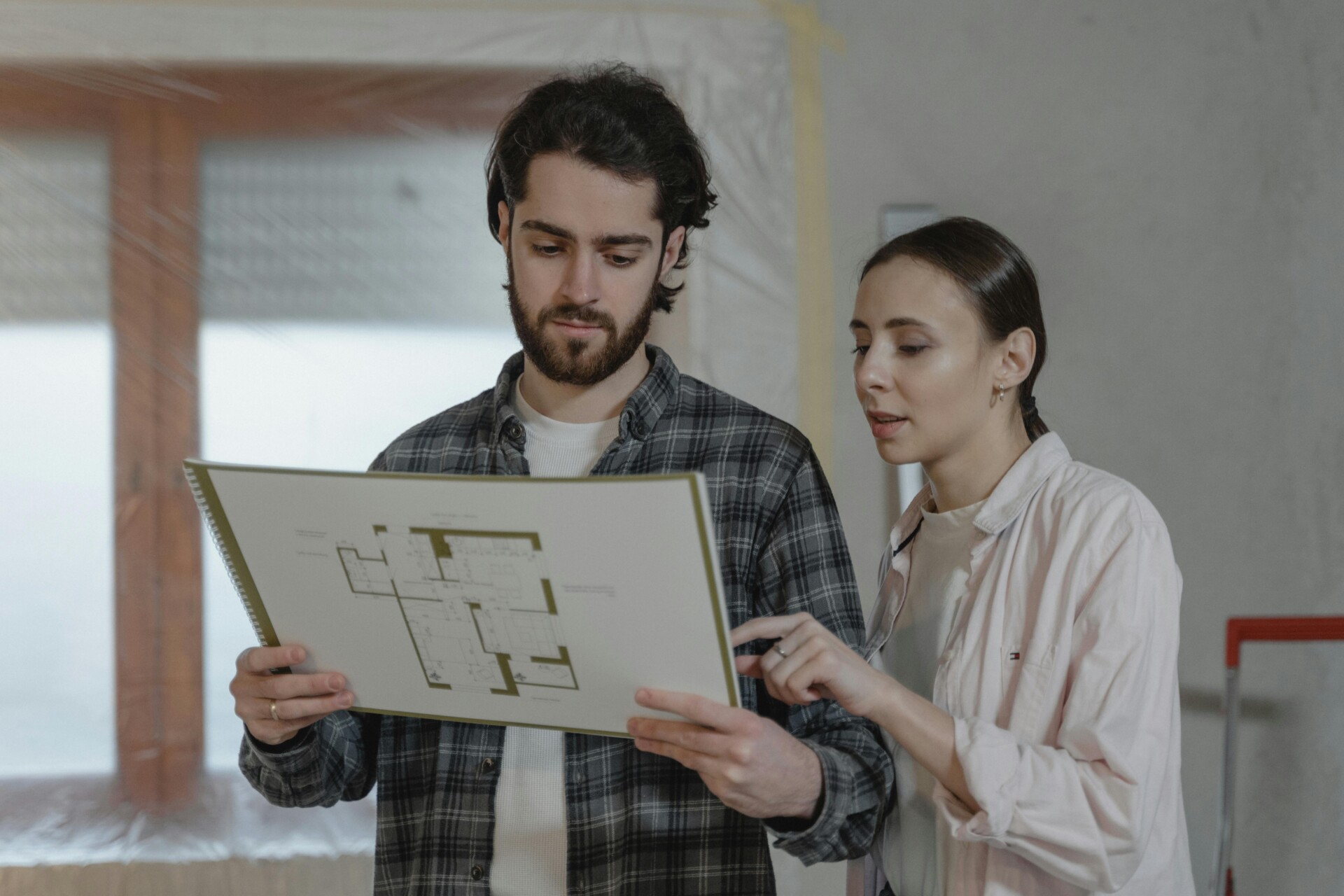
At EB3 Construction, we understand that successful project execution begins by assembling the right pre-construction team. This crucial phase sets the foundation for every development project, requiring specialized expertise across multiple disciplines to transform concepts into buildable plans. We collaborate with property owners and developers to coordinate all necessary team members based on each project’s unique requirements.
Project Owners and Developers
The project owner or developer leads the pre-construction process. As their construction partner, we work with them to establish clear objectives, budget parameters, and quality expectations. Many larger developers assign a dedicated project manager or owner’s representative to act as the primary point of contact during the pre-construction phase.
These representatives bring valuable insights to our planning meetings, ensuring that commercial viability and investment goals remain central to decision-making. During the recent surge in material costs, having the owner actively engaged in pre-construction has helped navigate budget challenges more effectively through real-time value engineering discussions.
The Design Team
The design team forms the creative and technical backbone of pre-construction planning. We regularly coordinate with architects who develop preliminary designs, translate client visions into working drawings, and provide the specifications that guide our estimating and planning processes. Architects establish the design intent that influences subsequent engineering and construction decisions.
Civil engineers conduct comprehensive site analyses to identify potential challenges and opportunities. Their expertise is especially valuable in urban infill projects, where existing infrastructure constraints and soil conditions can significantly impact construction approaches. Our team reviews their assessments to develop site logistics plans that maximize efficiency while minimizing disruption.
Structural engineers work with us to ensure designs meet structural integrity requirements while optimizing material usage. In multi-story projects, we collaborate with structural engineers early to identify economical framing systems that maintain design intent while controlling costs. Their input on foundation systems is crucial when dealing with challenging soil conditions.
Mechanical, electrical, and plumbing (MEP) engineers design the essential building systems that bring structures to life. Early coordination with MEP engineers helps identify optimal placement for building systems, reducing costly conflicts during construction. Their expertise in energy code compliance and sustainable design solutions is increasingly valuable as regulations evolve.
General Contractors and Construction Managers
As general contractors, we bring practical construction knowledge to pre-construction planning. Our team analyzes constructability issues, provides detailed budget estimates, develops realistic schedules, and recommends efficient construction methods based on current market conditions. We identify long-lead items that require early procurement and highlight potential material shortages or labor constraints that could affect project timelines.
Construction managers oversee the planning process, coordinating between design professionals, specialty contractors, and owners to ensure alignment across all aspects of project development. We leverage our field experience to anticipate challenges that might not be apparent on paper, such as site access limitations or staging requirements for materials and equipment.
The benefits of having experienced builders at the pre-construction table became particularly evident during the pandemic-related supply chain disruptions. Our knowledge of material availability and pricing volatility allowed clients to make informed decisions about alternative products and construction approaches.
Specialty Contractors and Consultants
For projects with unique or technically complex elements, we involve specialty contractors during pre-construction. Their expertise in specific building systems or construction methods helps refine designs and budgets for specialized components. For instance, when working on projects with complex curtainwall systems, we engage facade specialists early to ensure designs align with manufacturing and installation capabilities.
Additional consultants often include environmental experts who assess site conditions and regulatory requirements, code consultants who navigate complex building regulations, and legal counsel who review contracts and compliance matters. In projects with significant community impact, we may also engage with government representatives and community stakeholders to address concerns proactively.
The composition of our pre-construction team evolves based on project requirements, with each member bringing specialized knowledge to the planning process. By facilitating collaboration across disciplines, we ensure that designs are not only visually striking but also buildable, cost-effective, and aligned with client objectives. This integrated approach reduces costly mid-project changes and creates a solid foundation for successful construction execution.
How Does Design Development Impact Project Success?
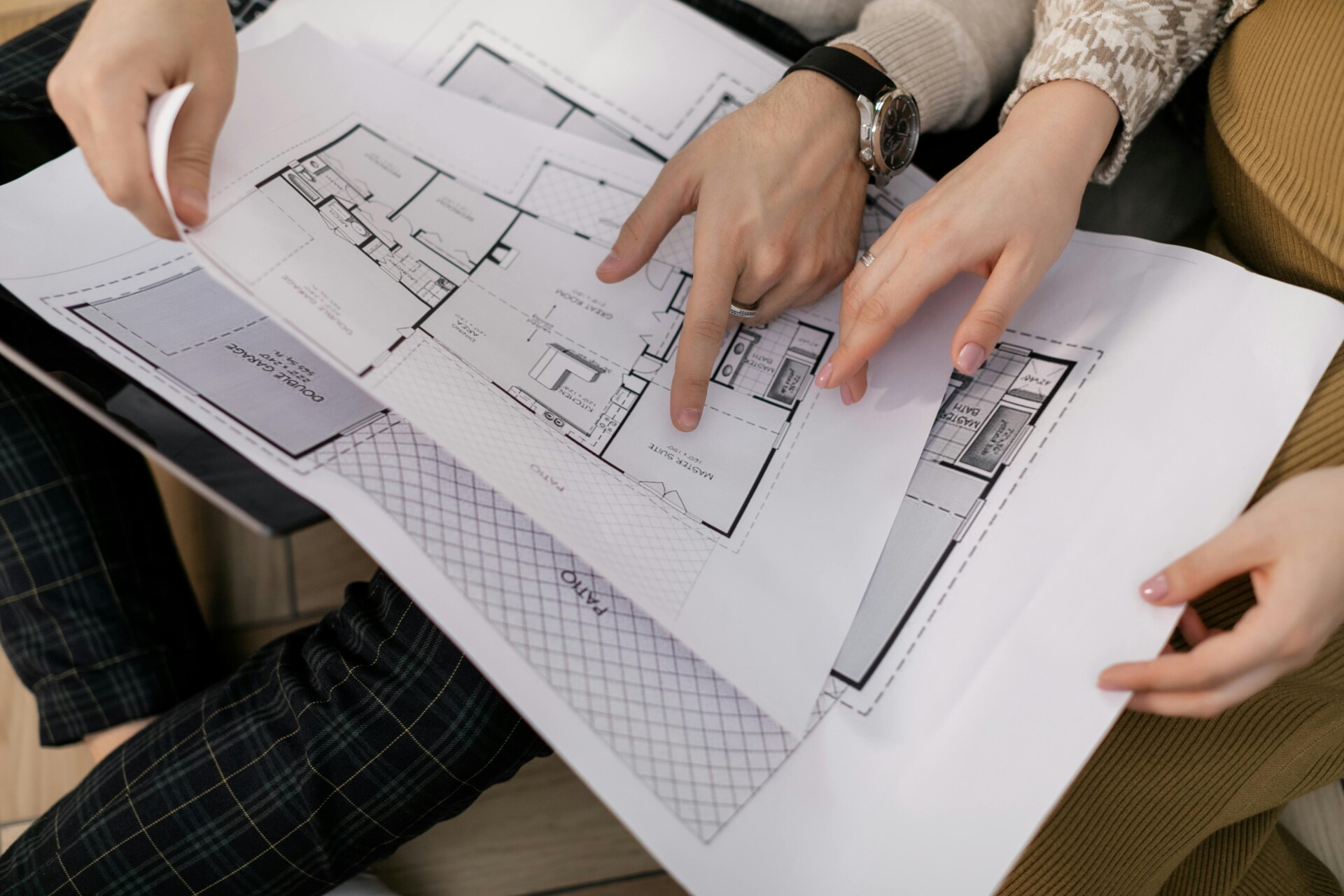
Design development is a pivotal moment in the lifecycle of any construction project. At EB3 Construction, engaging in this pre-construction phase involves translating conceptual ideas into a detailed roadmap that guides the entire building process. This transformation from abstract concepts to buildable plans is where projects truly take shape and where many potential problems can be identified and solved before they impact schedules or budgets.
The Foundation of Successful Construction
Design development builds on schematic drawings to create comprehensive construction documentation. At EB3, we view this phase as the bridge connecting creative vision with practical execution. By working alongside architects, engineers, and designers, we help refine preliminary concepts into detailed specifications that address both aesthetic and functional requirements.
The collaborative nature of design development creates a feedback loop that strengthens the project. When our construction experts join the discussion early, we identify constructability issues that might otherwise go unnoticed until they become costly problems during the build phase. This early coordination between design and construction teams is especially valuable in today’s challenging material procurement environment, where identifying and ordering long-lead items well before construction begins is crucial.
Architectural Design: Refining the Vision
During architectural design refinement, we partner with architects to translate conceptual sketches into detailed construction drawings. Together, we establish the precise dimensions, materials, and construction details needed to bring the project to life. This includes finalizing room layouts, ceiling heights, wall types, door and window placements, and material selections for both interior and exterior finishes.
The level of detail generated during this phase directly impacts construction efficiency. Well-defined architectural plans reduce requests for information (RFIs) during construction and minimize costly field adjustments. For instance, a recent commercial project required specialized acoustical requirements for conference spaces. By addressing these needs during design development, we avoided disruptive rework that would have occurred if these specifications had been overlooked.
Engineering Design: Building Performance and Compliance
Engineering design runs parallel to architectural refinement, focusing on the systems that make buildings function safely and efficiently. We coordinate closely with structural, mechanical, electrical, and plumbing engineers to ensure these systems integrate seamlessly with the architectural vision.
Structural engineering defines the building’s skeleton, determining column placements, beam sizes, and foundation requirements. MEP systems (mechanical, electrical, and plumbing) require careful coordination to avoid conflicts when installed. Recent code changes regarding energy efficiency have made this coordination increasingly complex, with systems needing to meet stricter performance standards while remaining within budget constraints.
Fire protection systems, accessibility requirements, and sustainability features are also refined during this phase. Each engineering discipline contributes specialized knowledge that ensures the completed building will meet both regulatory requirements and owner expectations for performance.
Design Reviews: Collective Problem-Solving
Design reviews are structured sessions where stakeholders evaluate developing plans to identify improvements and resolve conflicts. We facilitate these critical meetings, bringing together owners, architects, engineers, and key subcontractors to examine designs from multiple perspectives.
Effective design reviews follow a systematic approach. First, we establish clear objectives for each review session. Next, we ensure all participants receive documentation with sufficient time for thorough review. During the meeting, we methodically address each system and space, documenting decisions and action items. Follow-up ensures that identified issues are resolved and incorporated into updated documents.
These collaborative sessions often yield substantial improvements. In a recent healthcare project, a design review identified opportunities to standardize room layouts, which improved operational efficiency for the client and streamlined construction through repetitive elements, saving both time and money.
Value Engineering: Optimizing Cost and Quality
Value engineering is often misunderstood as simple cost-cutting, but true value engineering balances cost reduction with maintained or improved functionality. We approach this process by examining the purpose of each building element and exploring alternative methods to achieve the same goals more efficiently.
This process works best when integrated throughout design development rather than applied after designs are complete. By continuously evaluating cost implications of design decisions, we help keep projects within budget while preserving their essential qualities. Alternative materials, simplified construction methods, and standardized components often emerge as solutions that maintain design intent while improving constructability.
For example, when working on a recent multi-family residential project, we suggested slightly adjusting the building’s footprint to align with standard material dimensions, reducing waste and cutting framing costs substantially without compromising the living spaces.
Building Information Modeling (BIM): Digital Coordination
Building Information Modeling has transformed design development by creating digital 3D representations of projects before construction begins. This technology allows our team to detect clashes between building systems, verify spatial requirements, and visualize the finished project with remarkable accuracy.
When we implement BIM during design development, we are essentially building the project twice: first virtually, then physically. The virtual construction reveals issues that might otherwise remain hidden until discovered in the field. For instance, identifying that a structural beam conflicts with ductwork is much less expensive when caught during design development than when crews are standing idle on site waiting for a solution.
Beyond clash detection, BIM enhances communication by providing clients with realistic visualizations of spaces before they’re built. This improves decision-making and reduces changes during construction. The model also serves as a valuable resource during construction, providing detailed information about components and systems to field personnel.
Balancing Creativity with Constructability
The most valuable aspect of our involvement in design development is balancing creative vision with practical constructability. We work with design teams to identify constructability challenges early when adjustments can be made without compromising design intent. Sometimes, small modifications to details make construction significantly more efficient without noticeable impact on appearance or function. In other instances, understanding construction constraints inspires creative solutions that enhance the original concept.
Construction sequencing also influences design decisions. Understanding how various building elements must be installed in relation to each other helps prevent details that would be impossible to execute. This practical knowledge, when applied during design development, prevents frustration and compromises during construction.
The Path to Project Success
Design development directly impacts every aspect of project success. Thorough, coordinated documentation reduces construction delays and change orders. Careful material selection and detailing improve building quality and performance. Early identification of long-lead items prevents schedule disruptions. Collaborative problem-solving builds team cohesion that carries through to construction.
When design development is rushed or incomplete, construction inevitably suffers. Ambiguous details lead to requests for information that delay progress. Uncoordinated systems create conflicts in the field that require expensive rework. Incomplete specifications result in budget surprises when actual materials must be selected.
By investing appropriate time and expertise in design development, we help ensure that when construction begins, the team has a clear, comprehensive roadmap to follow. This foundation of thorough preparation allows us to deliver projects that meet both creative visions and practical requirements.
Why is Risk Analysis Essential in Pre Construction?
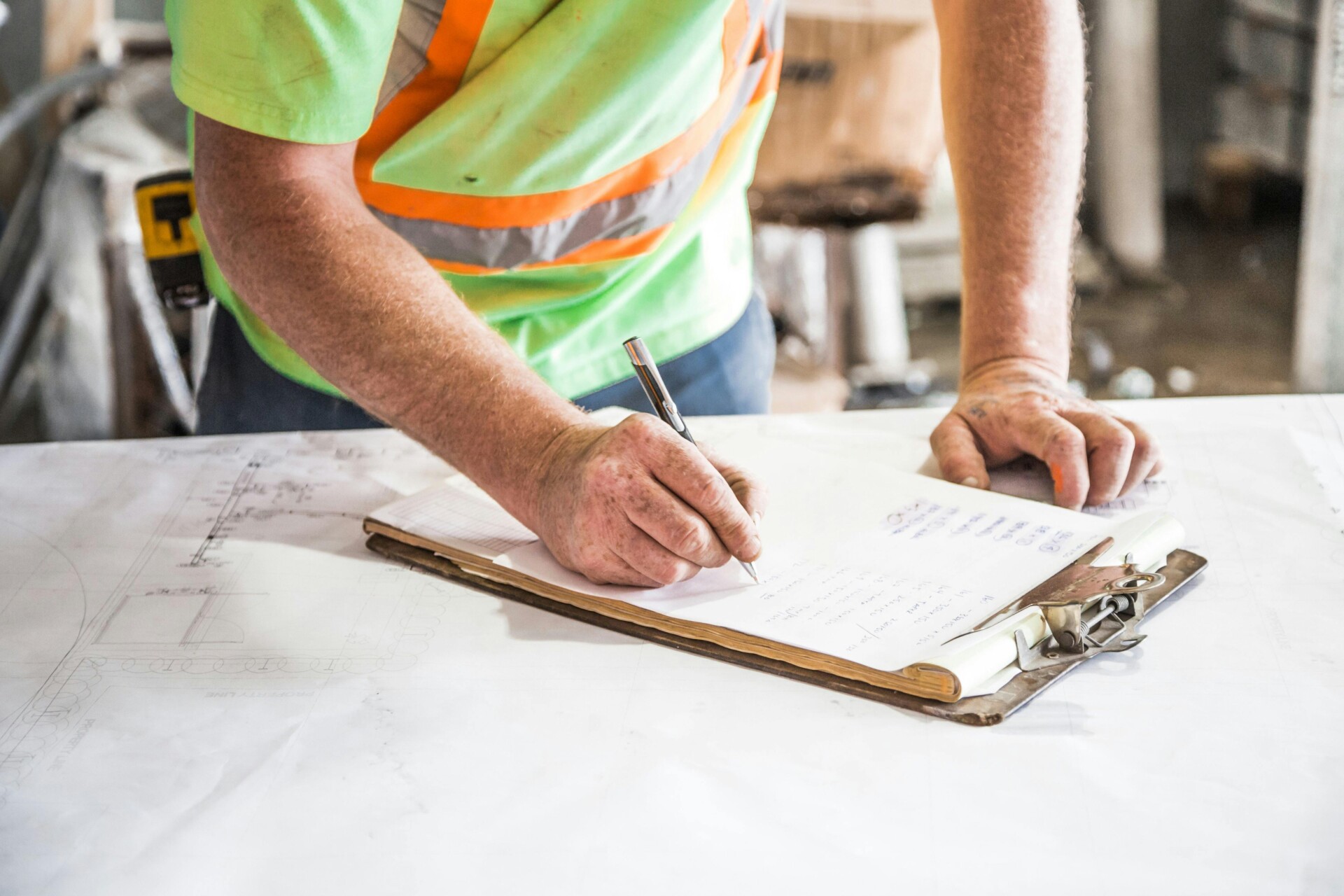
At EB3 Construction, we’ve learned that thorough risk analysis during pre-construction is fundamental to project success. By identifying potential challenges before breaking ground, we create a strategic roadmap that safeguards budgets, timelines, and ultimately, client satisfaction. This proactive approach turns unknowns into manageable variables, significantly reducing the likelihood of costly surprises during construction.
Systematic Risk Identification and Assessment
We begin our risk analysis process by conducting comprehensive assessments across multiple fronts. Our team methodically evaluates budget constraints, schedule feasibility, design complexities, and regulatory requirements specific to each project. This initial analysis often reveals hidden connections between seemingly separate risk factors that might exacerbate if unaddressed.
For financial risks, we examine material cost volatility, labor availability, and potential economic shifts that could impact the project’s bottom line. Our experience shows that construction projects face a high probability of budget challenges when these elements aren’t properly assessed early. By quantifying these risks during pre-construction, we establish realistic contingencies instead of arbitrary percentage-based buffers.
Regulatory compliance is another critical risk category that we evaluate thoroughly. Local building codes, environmental regulations, and permitting requirements vary significantly between jurisdictions and project types. We’ve found that early engagement with authorities having jurisdiction often reveals compliance nuances that, when identified during pre-construction, prevent costly mid-project adjustments.
Cost Control Planning
After identifying financial risks, we develop robust cost control strategies tailored to each project’s unique challenges. These strategies include establishing clear forecasting mechanisms to track expenditures against budgeted amounts in real-time. Our variance analysis protocols detect spending anomalies early, allowing for immediate corrective action before minor overruns become major financial issues.
Change control procedures form a critical component of our cost management approach. We implement structured processes for evaluating, approving, and documenting all project changes, ensuring that scope creep doesn’t undermine the initial budget framework. This disciplined approach maintains financial transparency throughout the project lifecycle and builds client trust through predictable outcomes.
Material procurement planning during pre-construction also helps us mitigate financial risks. By analyzing supply chain vulnerabilities and material availability, we can lock in pricing for volatile commodities or identify suitable alternatives when necessary. This strategic procurement approach has proven especially valuable during periods of market instability and supply constraints.
Site-Specific Safety Planning
Safety risk assessment is a fundamental aspect of our pre-construction process. We conduct thorough site evaluations to identify potential hazards specific to each project’s location, conditions, and scope. This detailed analysis informs our customized safety protocols, which go beyond standard requirements to address unique project characteristics.
Our safety plans include comprehensive equipment operation guidelines tailored to the specific machinery needed for each project. We develop detailed procedures for handling hazardous materials that workers might encounter, incorporating the latest best practices and regulatory requirements. Emergency response protocols are crafted with site-specific considerations in mind, including access points, evacuation routes, and coordination with local emergency services.
Training requirements receive particular attention during our safety planning process. We identify specialized skills needed for unique project elements and establish verification procedures to ensure all personnel possess the necessary qualifications. This proactive approach to competency management has demonstrably reduced incident rates on our projects while enhancing overall productivity.
Quality Control Planning
Quality risks can significantly impact project timelines and budgets if addressed reactively rather than proactively. During pre-construction, we establish clear quality standards aligned with project requirements, industry best practices, and client expectations. These standards create objective benchmarks against which all work can be measured consistently.
Our inspection procedures outline specific verification points throughout the construction process, preventing defects from being concealed by subsequent work. We develop systematic approaches for documenting inspections, tracking non-conformances, and implementing corrective actions. This structured quality management framework ensures that issues are identified and resolved promptly, minimizing their impact on project outcomes.
Material and workmanship specifications receive careful consideration during quality planning. We clearly define acceptance criteria for critical elements and establish verification methods appropriate for each. By setting these parameters during pre-construction, we avoid ambiguity during execution and create shared expectations among all project stakeholders.
Risk Response Planning
For each identified risk, we develop specific response strategies based on its potential impact and probability. Some risks warrant avoidance strategies, where we modify project approaches to eliminate the threat entirely. Others are better addressed through transfer mechanisms, such as insurance coverage or contractual provisions that assign responsibility to the party best positioned to manage the risk.
Mitigation strategies represent our most common approach to risk management. These involve specific actions that reduce either the likelihood of a risk occurring or its potential impact if it does materialize. Our contingency planning establishes predetermined responses to specific risk triggers, enabling quick action when warning signs appear.
For risks that cannot be avoided, transferred, or significantly mitigated, we develop acceptance strategies with appropriate contingency reserves. This transparent approach to residual risk ensures that all stakeholders understand the project’s risk profile and are prepared for potential outcomes. By formalizing these response plans during pre-construction, we create a framework for consistent risk management throughout the project lifecycle.
Conclusion: The Foundation of Construction Success
At EB3 Construction, we understand that pre-construction planning is the critical foundation upon which successful construction projects are built. This strategic phase transforms conceptual ideas into executable construction plans that drive project success. Our pre-construction approach integrates thorough design development, careful contractor selection, proactive risk assessment, and detailed scheduling to enhance project efficiency while controlling costs.
The construction industry increasingly recognizes that the quality of pre-construction planning directly correlates with successful outcomes. We’ve witnessed firsthand how investing time and resources in this foundational phase allows us to anticipate challenges, identify cost-saving opportunities, and establish clear expectations with our clients before breaking ground. By developing comprehensive site logistics plans and procurement strategies during pre-construction, we minimize potential disruptions during the active construction phase.
Our most successful projects maintain seamless continuity between pre-construction planning and construction execution. We utilize sophisticated construction management software to create a single source of truth that carries accurate budgets, realistic schedules, detailed specifications, and other critical information throughout the project lifecycle. This digital continuity ensures everyone works from the same information and allows us to adapt quickly when field conditions change. Contact EB3 Construction today to discuss how our proven pre-construction approach can set your next project up for success.