When foundations are being poured on one end of your job site, we’re already preparing the steel framework that will soon rise above them. Pre-Engineered Buildings represent a significant change in commercial construction. Unlike traditional structures built piece by piece on location, PEBs use steel components manufactured off-site to precise specifications, then transported to your property for efficient assembly.
These engineered systems arrive as a complete package—columns, rafters, purlins, girts, and sheeting—all designed to work together seamlessly. The result? A structure that’s typically 30% lighter than conventional steel buildings when properly engineered, without sacrificing structural integrity. This weight reduction translates directly to cost savings in foundations and site work, particularly valuable in today’s material-constrained market.
From warehouses and manufacturing facilities to distribution centers and even architecturally striking commercial spaces, we’ve implemented this construction methodology across diverse project types. With tightening construction schedules and rising labor costs challenging every project, PEB systems offer practical advantages that developers and property owners increasingly recognize as essential, not optional.
What Components Make Up a Pre-Engineered Building?
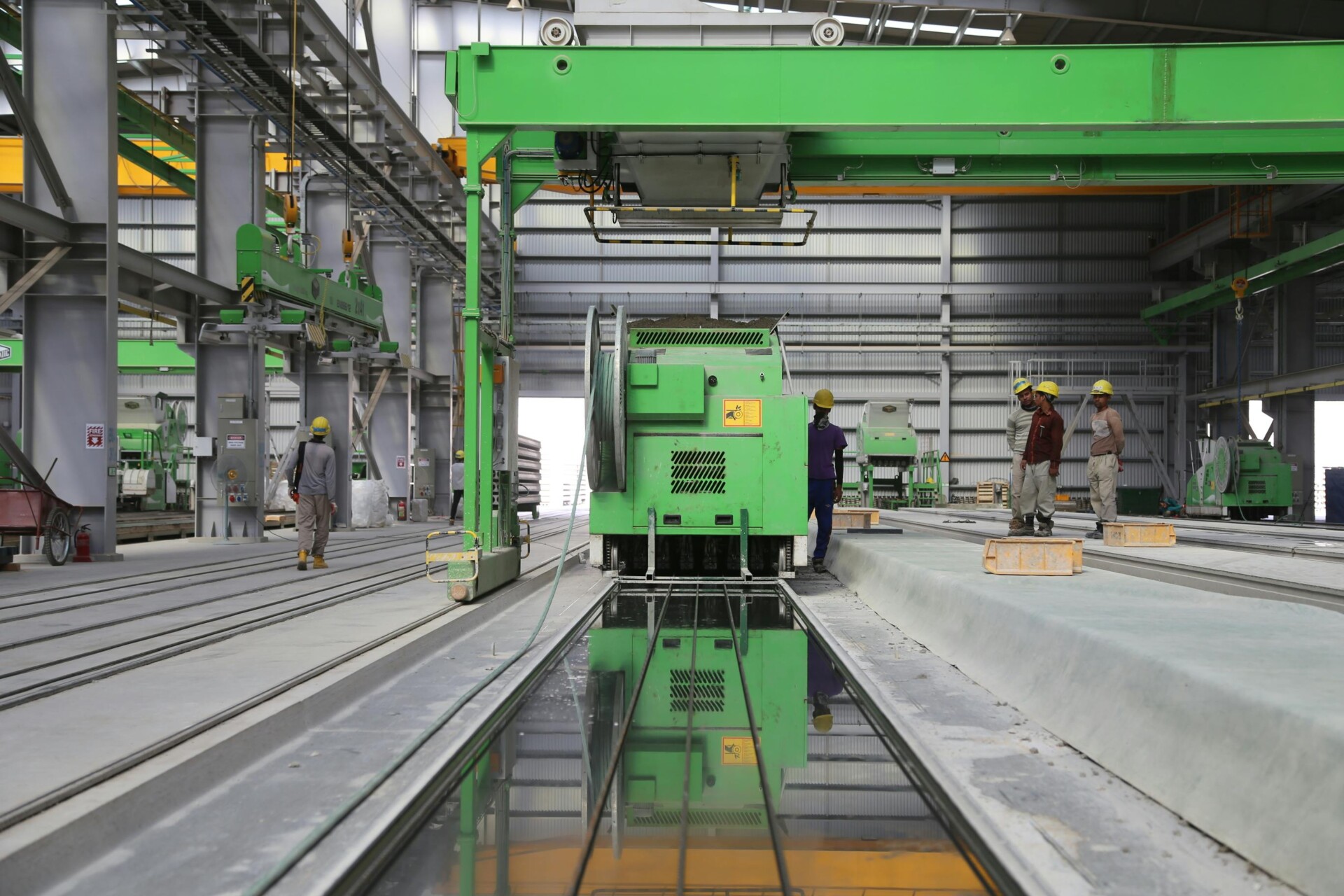
Pre-engineered buildings (PEBs) embody the peak of modern construction engineering, with every component precisely designed before reaching the site. These systems are complete building packages, where each element plays a specific role in ensuring structural integrity.
Primary Structural Frame
The core of any PEB is its primary frame system. These frames are constructed using tapered I-shaped steel members that optimize material use while maintaining strength. Unlike conventional steel buildings with uniform sections, our frames use variable web depths—thicker where stress is concentrated and lighter elsewhere.
Main columns transfer vertical loads directly to foundations, while rigid rafters span between columns to shape the building’s profile. These components function as moment-resisting frames handling lateral and gravity loads. At end walls, we install either rigid frames or more economical bearing frames, depending on project needs and loading conditions.
Wind bracing and high-tensile connecting bolts reinforce these primary elements, creating a cohesive structure capable of withstanding significant environmental forces. The splice connections we use allow for easier transportation and efficient field assembly, reducing crane needs and installation time.
Secondary Support Elements
Purlins are crucial secondary framing elements in PEBs. These cold-formed structural members—typically in Z, C, or sigma cross-sections—span between primary frames to support roof and wall covering systems. Their strategic placement transfers loads from cladding to the main structure, providing lateral stability.
The cold-forming process produces lightweight yet sturdy components that optimize material use. We select purlin spacing based on loading requirements, span distances, and cladding specifications. Their corrosion-resistant properties, achieved through galvanization or specialized coatings, ensure long-term performance in challenging environments.
Additional secondary elements include eave struts, which connect purlins and girts at roof-to-wall intersections, and various bracing systems that help maintain overall building geometry under load.
Component | Function | Material |
---|---|---|
Steel Frames | Primary structural support | Steel |
Roofing and Wall Panels | Protective covering and aesthetics | High-quality steel sheets |
Insulation Materials | Thermal comfort and energy efficiency | Various insulation materials |
Fasteners and Bolts | Connect structural elements | Steel |
Doors and Windows | Functionality and aesthetics | Various complementing materials |
Foundations | Stability and load-bearing | Reinforced concrete |
Ventilation Systems | Air quality and moisture control | Various systems |
Paint and Coatings | Protection and aesthetics | Various coatings |
Roof and Wall Systems
The building envelope completes the structure, offering functionality beyond weather protection. We use roll-formed steel sheets for roof panels, with specialized profiles that enhance water drainage and structural performance. These panels typically feature factory-applied finishes that resist UV degradation and chemical exposure.
Wall systems vary based on project needs—from simple single-skin metal panels to sophisticated curtain wall assemblies incorporating glass and other materials. For industrial applications requiring thermal efficiency, we often use standing seam roof systems with concealed fasteners that minimize leak points while allowing thermal expansion.
Energy considerations drive many of our envelope decisions. Specialized roofing sheets with reflective coatings reduce heat absorption, while strategically placed translucent panels harvest natural daylight without compromising structural integrity. Proper flashing details ensure weather-tight performance throughout the building’s service life.
Specialized Components and Accessories
Modern PEBs incorporate numerous specialized elements that enhance performance and functionality. Sandwich panels—three-layer composites with insulating core material between metal facings—provide superior thermal performance in a single-component installation. These factory-assembled units reduce field labor while delivering consistent quality.
We customize buildings with components like mezzanine floors to maximize usable space, skylight sheets for natural illumination, and various access systems such as cage ladders for maintenance needs. Functional elements including cable trays, ventilation ducts, and crane systems integrate directly with the primary structure through pre-engineered connection points.
PEB flexibility extends to façade treatments as well. We can incorporate masonry wainscots, decorative entrance features, and custom color schemes to achieve architectural objectives while maintaining the economic advantages of pre-engineered construction. This versatility makes PEBs suitable for applications ranging from industrial warehouses to retail facilities and office complexes.
What Are the Advantages of Pre-Engineered Buildings?
As general contractors with extensive field experience, we have witnessed firsthand how pre-engineered buildings (PEBs) transform construction timelines and project economics. The building industry continues to embrace these systems as developers and property owners recognize their substantial advantages over conventional construction methods.
Superior Quality Control
Pre-engineered components are manufactured in controlled factory environments, virtually eliminating the variables that affect traditional on-site construction. We ensure consistent quality across structural elements when components are fabricated to precise specifications under rigorous quality assurance protocols before they reach the job site.
This factory-based production approach ensures each beam, column, and connection meets exacting standards—something difficult to guarantee with field-fabricated elements exposed to weather conditions and varying labor quality. The result is buildings with superior structural integrity and fewer long-term maintenance issues.
For our clients, this translates to fewer warranty callbacks and greater confidence in the finished structure’s performance. The controlled manufacturing environment produces components with tighter tolerances and more predictable behavior under load.
Dramatically Reduced Construction Timelines
One of the most compelling advantages we deliver through PEB systems is speed to occupancy. While conventional construction methods typically require 20-26 weeks from groundbreaking to completion, we can erect pre-engineered buildings in just 6-8 weeks—a reduction of approximately 70% in construction time.
This acceleration occurs because we can conduct site preparation and foundation work simultaneously with the manufacturing of the building components. When materials arrive on site, they’re ready for immediate assembly without the delays associated with conventional framing, forming, and curing processes.
The compressed timeline directly impacts our clients’ bottom line, allowing faster return on investment through earlier occupancy and operational capability. For developers working with construction loans, this speed can significantly reduce financing costs during the construction phase.
Aspect | Pre-Engineered Buildings (PEB) | Conventional Buildings |
---|---|---|
Construction Time | 6-12 months | 12-24 months |
Cost Efficiency | Up to 30% more cost-effective | Higher material and labor costs |
Labor Requirements | Lower due to prefabrication | Higher due to on-site fabrication |
Material Usage | Optimized and minimal waste | Higher waste and inefficiencies |
Lower Long-Term Maintenance Requirements
We select PEB systems with durable, high-performance finishes that minimize maintenance needs. Advanced coating systems applied to steel components during manufacturing provide superior corrosion resistance compared to field-applied paints. Many systems feature specialized finishes with 25+ year warranties against peeling, flaking, or excessive fading.
The engineered connection details minimize water infiltration points, reducing the risk of moisture-related deterioration. For property owners, this means fewer repair cycles, lower maintenance budgets, and extended intervals between major renovations—all contributing to a lower total cost of ownership over the building’s lifespan.
Exceptional Flexibility for Future Expansion
When we design PEB projects, we’re not just building for today—we’re planning for tomorrow’s needs. Pre-engineered systems excel at accommodating future growth with expandable end walls and modular components specifically engineered for straightforward expansion.
We can extend building length by removing end wall components and adding new structural bays. Height modifications are possible through specialized connection designs that allow for vertical expansion. Width increases, while more complex, can be engineered into the initial design to accommodate future growth.
This inherent adaptability provides significant value for businesses anticipating growth or evolving operational requirements. Rather than facing the prospect of new construction or relocation, owners can modify their existing structure at a fraction of replacement cost.
Enhanced Energy Efficiency
Modern PEB systems provide excellent thermal performance through specialized insulation options. We regularly implement polyurethane insulated panels that deliver R-values up to R-42, significantly exceeding code minimums. For projects with different requirements, we also utilize fiberglass blanket systems with vapor barriers that balance performance with cost considerations.
The tight building envelope created by factory-precision components reduces air infiltration compared to conventional construction. Cool roof technologies with high solar reflectance indices (SRI) minimize heat gain in warmer climates, reducing cooling loads and operating costs.
Many of our clients have reported energy consumption reductions of 30% or more compared to conventional buildings of similar size and function. These savings continue to accumulate throughout the building’s operational life, making a substantial impact on long-term operating budgets.
Design Versatility
Today’s pre-engineered buildings bear little resemblance to the utilitarian metal boxes of decades past. We now implement diverse façade treatments, canopy systems, and architectural elements that transform these structures into visually distinctive buildings.
Metal wall panel systems come in numerous profiles, finishes, and colors. We frequently integrate these with conventional materials like glass, stone, or precast concrete to create hybrid exteriors that meet specific aesthetic requirements while maintaining the structural and economic benefits of pre-engineered construction.
The design flexibility extends to interiors as well, with clear-span capabilities up to 300 feet that create uninterrupted spaces for maximum operational flexibility. High bay configurations easily accommodate overhead cranes, mezzanines, or specialized equipment while maintaining efficient space utilization.
For developers and property owners seeking the optimal balance between performance, economics, and aesthetics, pre-engineered building systems represent one of the most compelling construction approaches available in today’s market. Their combination of quality, speed, and long-term value continues to drive their growing adoption across virtually every building sector.
How Do Pre-Engineered Buildings Compare to Conventional Steel Construction?
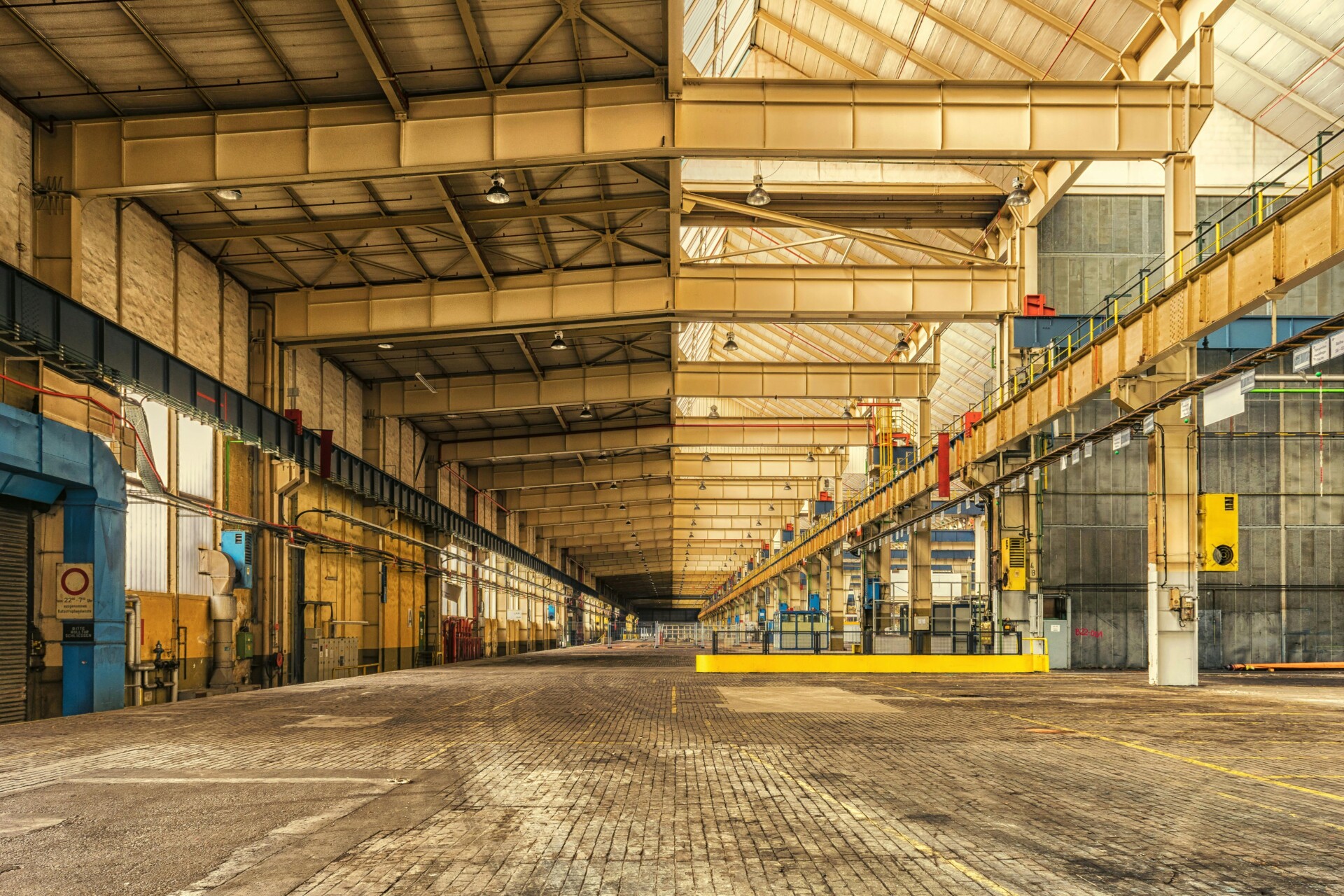
When developers consult us about their projects, one of the most common questions concerns building methods. Choosing between pre-engineered buildings (PEBs) and conventional steel construction is a fundamental decision impacting everything from timeline to budget. Having managed both types of construction for our clients, we’ve observed firsthand how these approaches differ in practice.
Design Efficiency and Process
The design phase sets the tone for the entire project lifecycle. With PEBs, we use an integrated framing system that creates a cohesive structural unit. Our design teams employ specialized software to generate detailed plans, estimates, and structural calculations much faster than conventional methods.
Conventional steel buildings require a more labor-intensive design process. Each component must be individually engineered, fabricated, and assembled on-site, extending the design timeline and introducing more variables that require coordination, increasing the potential for errors or miscommunications.
When designing PEBs, we adhere to internationally recognized codes such as AISC, AISI, and MBMA, ensuring global standards are met. Conventional steel buildings often rely on traditional, sometimes outdated IS codes that may not incorporate the latest engineering advances.
Construction Timeline and Scheduling
For developers facing market pressures or investors demanding quick returns, timeline considerations become paramount. We consistently deliver PEB projects significantly faster than conventional steel structures. A 500-ton pre-engineered building typically takes us 6-8 weeks to complete after design finalization, while an equivalent conventional structure requires 20-26 weeks.
This time difference arises from several factors: PEBs arrive on-site as ready-to-assemble components, connections are primarily bolted rather than welded, and the lightweight members are easier to handle. For time-sensitive projects—like distribution centers that need to be operational before peak season or manufacturing facilities with production deadlines—this acceleration can translate directly to revenue.
The standardization of PEB components also enables more accurate scheduling, with fewer weather-related delays and less on-site fabrication uncertainty. This predictability allows for better coordination with mechanical, electrical, and finishing trades.
Foundation Requirements and Structural Weight
The foundation is a critical element in any construction project, and significant differences exist between the two approaches. PEBs utilize tapered built-up sections that are 10-20% lighter than conventional hot-rolled sections. This weight reduction simplifies the design and construction of more cost-effective foundations.
Conventional steel buildings require heavier structural members, necessitating more robust foundations, increasing excavation work, concrete volume, and reinforcement requirements. This adds both cost and time to the early project phases. The increased foundation complexity also introduces more variables that must be managed and coordinated.
Beyond direct material savings, the lighter PEB foundations often mean less site disruption and reduced earthwork, valuable in environmentally sensitive areas or sites with challenging soil conditions.
Seismic Performance and Safety
In regions with seismic activity, structural performance during earthquakes is critical. We find that PEBs offer superior resistance to seismic forces due to their lightweight, flexible nature, effectively absorbing and dissipating energy during an earthquake.
Conventional steel structures, with heavier, more rigid frames, often struggle with seismic forces. Their greater mass generates larger inertial forces during ground acceleration, potentially leading to more significant structural stresses. In many cases, additional seismic reinforcement is necessary in conventional designs, further increasing costs and complexity.
This performance difference is especially important in areas along fault lines or with histories of seismic activity. While both systems can be engineered for earthquake resistance, PEBs often achieve this more efficiently and economically.
Cost Efficiency and Value Engineering
Perhaps the most compelling advantage from our clients’ perspective is the overall cost difference. We consistently find that PEBs cost approximately 30% less per square meter than conventional steel buildings. This cost advantage stems from multiple sources: reduced material usage, faster construction, simplified foundations, and streamlined design processes.
Labor costs also factor significantly into the equation. When erecting PEBs, the simplified construction process requires fewer specialized workers and less heavy equipment. Conventional steel structures demand more extensive on-site fabrication, welding, and assembly, driving up labor costs and equipment requirements.
Beyond the initial construction expense, PEBs typically offer lower lifecycle costs through reduced maintenance requirements and greater energy efficiency when properly insulated. For commercial developers calculating long-term returns or owner-operators concerned with total cost of ownership, these ongoing savings compound the initial advantage.
Flexibility for Future Expansion
Business needs evolve, and buildings must sometimes grow accordingly. When designing PEBs, we incorporate simple connection details facilitating future expansion. Adding bays or extending the structure becomes a straightforward process that minimizes disruption to existing operations.
Expanding conventional steel buildings presents greater challenges. The welded connections and customized components make seamless additions more complex and costly. Expanding conventional structures often requires more extensive structural analysis and potential reinforcement of existing elements.
This expansion flexibility represents a significant advantage for growing businesses or phased developments where future spatial needs may not be fully defined at initial construction.
While both construction methodologies have their place in the market, pre-engineered buildings offer compelling advantages in speed, cost, seismic performance, and flexibility. By understanding these differences, we help our clients make informed decisions aligned with their project objectives, timeline constraints, and budget parameters.
What Challenges Do Pre-Engineered Buildings Present?
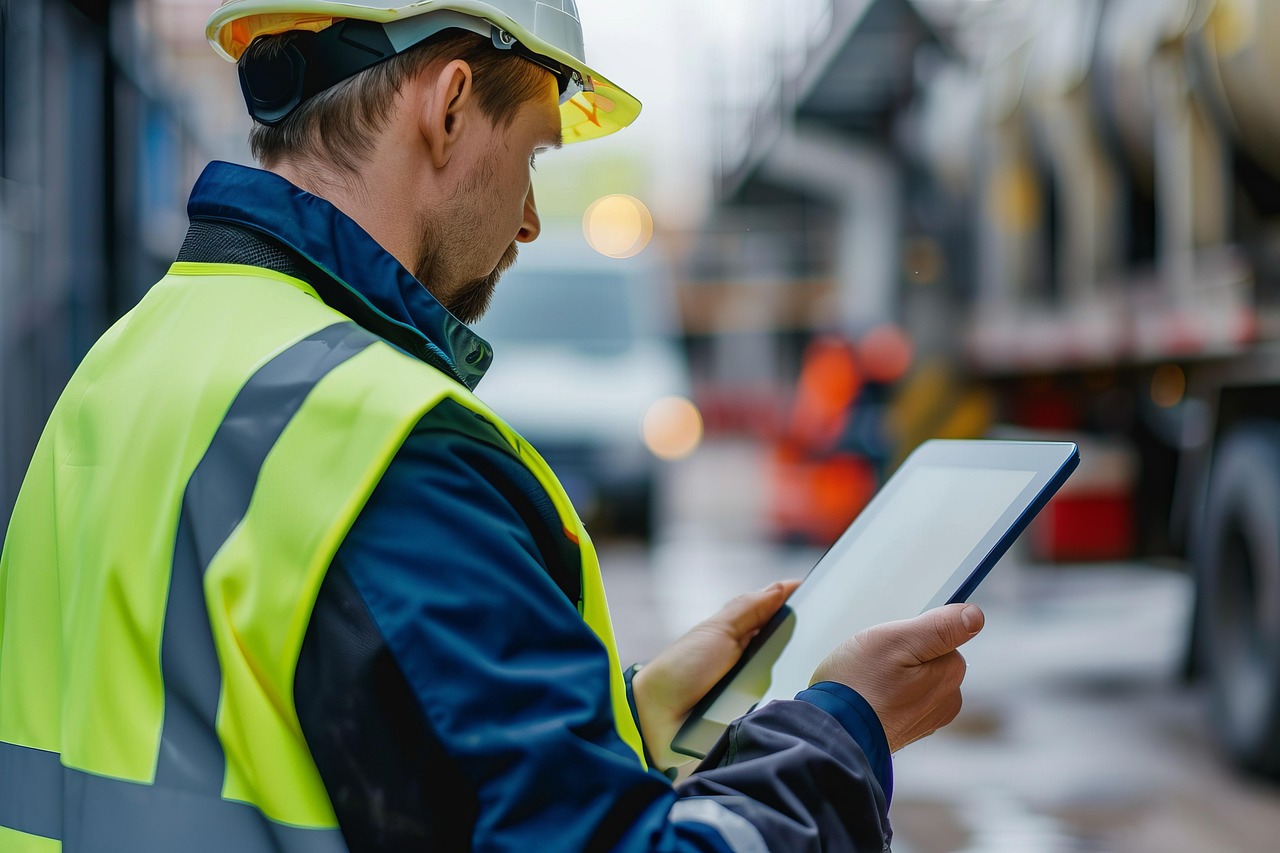
Managing pre-engineered building projects involves addressing several inherent challenges that require thoughtful solutions. These limitations don’t reduce the value PEBs offer, but they do require careful consideration during planning and construction.
Insulation Considerations and Costs
Steel’s excellent thermal conductivity is a double-edged sword for pre-engineered buildings. Without proper insulation, these structures readily transfer heat—making them uncomfortable in both summer and winter while dramatically increasing energy costs.
We typically recommend high-quality insulated metal panels (IMPs) or spray foam solutions, which provide superior thermal performance with R-values that minimize heat transfer. However, these comprehensive insulation systems represent a significant initial investment. For large-scale commercial or industrial projects, this addition can increase initial budgets by 15-20%, though long-term energy savings often justify the expenditure.
When coordinating insulation work, we focus on eliminating thermal bridges where metal framing creates pathways for heat loss. This detailed approach ensures climate control remains consistent throughout the structure, avoiding the uncomfortable temperature fluctuations that poorly insulated metal buildings often experience.
Insulation Type | R-Value (per inch) | Cost per Square Foot | Advantages | Disadvantages |
---|---|---|---|---|
Fiberglass | R-3 to R-4 | $0.5 – $1.5 | Low cost, easy to install, fire resistant | Thermal bridging, moisture prone |
Spray Foam | R-6 to R-7 | $1.5 – $2.5 | Seals gaps, high thermal resistance | High cost, requires professional installation |
Insulated Panels | R-6 to R-8 | $5 – $10 | High insulating quality, quick installation | High cost, requires expertise |
Aesthetic Limitations
The industrial appearance of pre-engineered buildings presents a consistent challenge, particularly for client-facing facilities or structures in design-sensitive areas. The utilitarian look of exposed steel may conflict with brand identity or neighborhood aesthetics in retail or upscale commercial environments.
We address these concerns through several approaches. Modern façade systems using composite panels, decorative cladding, or architectural accents can significantly transform a building’s exterior appearance. For interiors, we implement suspended ceilings, wall finishes, and strategic lighting to create environments indistinguishable from conventional construction.
These aesthetic enhancements require careful coordination between architectural design and structural engineering teams to ensure modifications don’t compromise the building’s structural integrity. The additional design complexity and materials naturally increase costs, requiring us to balance visual appeal with budget constraints.
Corrosion Risks and Protective Measures
As general contractors regularly working with steel structures, we’re acutely aware that corrosion is a significant long-term threat to pre-engineered buildings. This is particularly problematic in coastal areas, facilities with high humidity, or buildings housing processes that generate corrosive chemicals.
To mitigate these risks, we implement multi-layered protection strategies. This begins with selecting appropriate coatings—galvanized steel provides basic protection, while high-performance paint systems offer additional barriers. For severe environments, we may recommend stainless steel components for critical structural elements most vulnerable to corrosion.
Beyond material selection, our construction process includes careful detailing around joints, fasteners, and penetrations to prevent water intrusion. We also develop comprehensive maintenance protocols for building owners, as ongoing inspection and addressing early signs of corrosion are essential for maximizing a structure’s lifespan.
Sound Management Challenges
The acoustic properties of metal structures create another limitation we regularly address. The inherent reflectivity of steel panels can create significant noise issues, especially in manufacturing facilities, gymnasiums, or buildings with high occupancy levels.
Our approach to sound management includes integrating acoustic insulation between structural elements, installing perforated ceiling panels with sound-absorbing backing, and strategically placing acoustic barriers around equipment or areas where noise generation is concentrated.
For particularly sensitive environments like recording studios or medical facilities, we often recommend hybrid construction approaches where conventional materials are used for interior partitions while maintaining the pre-engineered structure for the building envelope.
Conclusion: The Future of Pre-Engineered Building Construction
Pre-engineered buildings have become a cornerstone of modern construction methodology. Their popularity is not merely a trend but a response to real market demands for efficiency, cost control, and structural reliability. Through our coordination of numerous PEB projects, we have seen these structures deliver approximately 30% in cost savings while reducing construction timelines by up to 50% compared to conventional methods.
The construction landscape continues to evolve, especially as material costs fluctuate and labor challenges persist. In this context, pre-engineered solutions offer developers and property owners a predictable path forward. Factory-manufactured components eliminate much of the on-site variability that can disrupt project schedules and budgets. While considerations around insulation requirements, aesthetic customization, and corrosion protection in coastal environments must be addressed during planning, proper engineering and material selection can effectively mitigate these challenges. We approach each project by carefully weighing these factors against the substantial benefits of rapid assembly, significant weight reduction, and long-term structural performance.
Interested in exploring how pre-engineered building solutions might benefit your next development project? Contact our team at EB3 Construction to discuss your specific needs.