As general contractors, we select concrete slab types based on project requirements, building loads, and site conditions.
Each slab system offers distinct advantages for specific applications, allowing us to optimize structural performance while managing project costs. Understanding these options helps us deliver the right solution for your development.
Choosing the Right Concrete Slab for Your Project
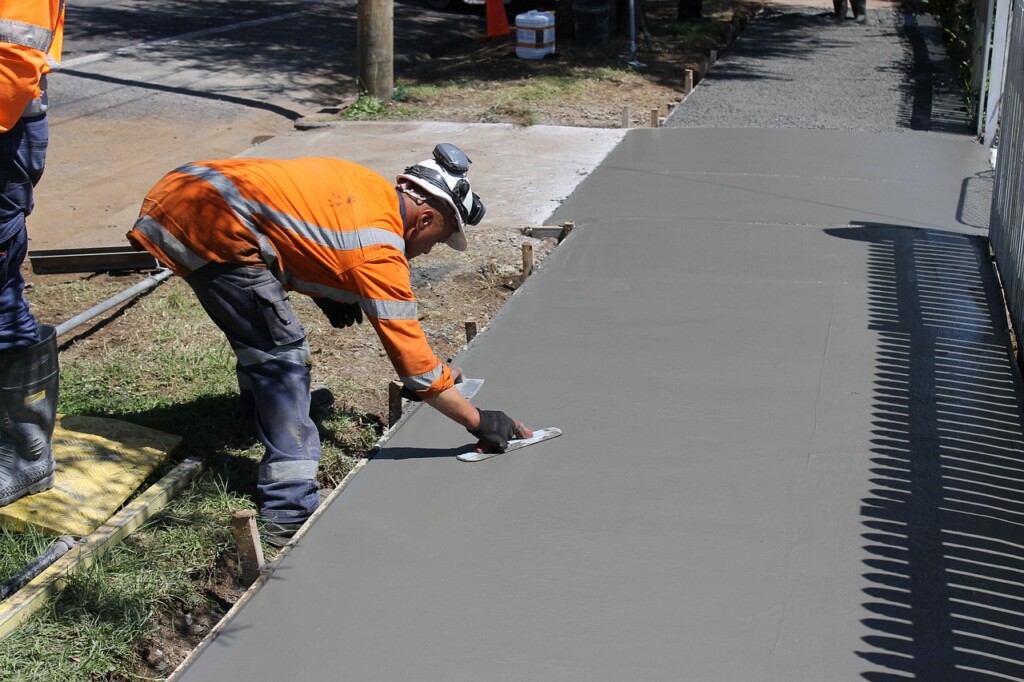
At EB3 Construction, we regularly work with the following concrete slab systems:
Basic Support Systems: One-Way and Two-Way Slabs
One-way slabs represent our most straightforward approach when structural supports are available on two parallel sides. These slabs, typically 4-6 inches thick for residential applications, distribute loads in a single direction toward the supporting beams or walls. We often implement these when the length-to-width ratio exceeds 2:1, making them ideal for rectangular spaces like corridors or residential rooms.
Two-way slabs offer greater versatility when we need to distribute loads in multiple directions. When we construct these slabs, we install reinforcement in perpendicular directions to transfer loads to supports on all four sides. This configuration creates a more robust floor system for square or nearly square areas. While requiring more complex formwork and reinforcement patterns, two-way slabs provide excellent structural integrity for commercial spaces and areas with heavy loads.
Column-Supported Systems: Flat Slabs and Flat Plates
When architectural plans call for open spaces without visible beams, we recommend flat slab systems. These slabs connect directly to columns, often using thickened portions called drop panels or column capitals at connection points to handle shear forces. We frequently implement flat slabs in office buildings and hotels where clear ceiling heights and flexible floor plans are priorities.
Flat plates offer a variation on this approach with a uniform thickness throughout. We build these simpler systems when loads are moderate and spans are shorter. The clean underside eliminates the need for complex formwork, accelerating construction schedules while providing a finished ceiling that requires minimal additional work.
Specialized Slab Systems for Enhanced Performance
Waffle slabs feature a distinctive grid pattern of ribs on the underside, resembling a waffle iron. We construct these by placing form voids in a grid pattern before pouring concrete. This approach reduces concrete volume by up to 30% while maintaining structural depth, making waffle slabs ideal for longer spans in theaters, auditoriums, and spaces where exposed ceilings can showcase their architectural appeal.
Hollow core slabs arrive at our job sites as precast units with longitudinal voids running through them. These factory-produced elements allow us to rapidly install floor systems without extensive formwork or curing time on site. The voids reduce weight while maintaining strength, and the hollow channels provide convenient pathways for electrical and mechanical services.
Post-tensioned slabs incorporate steel tendons that we tension after the concrete has hardened. This technique allows us to build thinner slabs that span greater distances with less deflection. We often implement post-tensioning in parking structures, shopping centers, and residential foundations on expansive soils, where controlling cracking is critical to long-term performance.
Application-Specific Concrete Slabs
For industrial facilities, we typically construct thicker slabs-on-grade designed to support heavy equipment, vehicle traffic, or storage loads. These slabs range from 6 to 12 inches thick depending on the anticipated loads and often include steel fiber or rebar reinforcement and carefully designed joint patterns to control cracking.
Residential foundations usually involve monolithic slabs that combine the footing and floor slab in a single pour. This approach streamlines construction while providing a continuous barrier against moisture. When building in areas with poor soil conditions, we might recommend ribbed slabs with integral beams to provide additional stiffness and load distribution.
Slab Type | Common Applications | Span Length | Load Capacity (kN/m²) |
---|---|---|---|
One-Way Slab | Rectangular rooms, corridors | 3-6m | 3-5 kN/m² |
Two-Way Slab | Square rooms, heavy load areas | 6-9m | 3-6 kN/m² |
Flat Slab | Office buildings, hotels | 6-9m | 4-7 kN/m² |
Waffle Slab | Theaters, auditoriums | 9-15m | 4-7 kN/m² |
Hollow Core Slab | Office, retail, parking | Up to 16m | 2.5 kN/m² |
Composite Slab | Multi-story buildings | 3-4.5m | |
Precast Slab | Large warehouses, industrial sites | Up to 15m |
The recent California building code updates have influenced our approach to slab selection, particularly regarding seismic performance of flat plate systems. Additionally, advances in concrete admixtures have allowed us to place and finish slabs more efficiently in challenging weather conditions, extending the construction season while maintaining quality.
When evaluating slab options for your next project, we consider not just the initial construction cost but also long-term performance, maintenance requirements, and compatibility with other building systems. This comprehensive approach ensures that the concrete slabs we build will deliver lasting value for your development.
How is a Concrete Floor Slab Constructed?
At EB3 Construction, we approach concrete floor slab construction as a carefully orchestrated process that demands precision and expertise. The success of a floor slab hinges on properly executing four critical phases that transform raw materials into a durable, functional surface capable of withstanding years of use.
Formwork Installation: Creating the Foundation
We begin by establishing precise formwork that serves as the mold for the concrete slab. Our team constructs these forms using sturdy lumber or steel panels, securing them at the correct elevation with stakes driven at regular intervals. Proper bracing is essential—we typically place supports every two feet to prevent bulging when the concrete exerts lateral pressure during placement.
Formwork isn’t merely a container; it defines the slab’s final dimensions and elevations. We take extra care to establish correct slopes for drainage where required, typically maintaining a minimum pitch of 1/4 inch per foot in areas where water management is essential. Before proceeding, we verify all measurements and check formwork for squareness using the 3-4-5 method to ensure perfect 90-degree corners.
Reinforcement Placement: Strengthening from Within
With formwork secured, we install reinforcement to enhance the slab’s structural integrity. Depending on the load requirements, we position steel rebar in a grid pattern, typically spaced 12 to 18 inches apart in both directions. Maintaining proper concrete cover is critical—using plastic chairs or precast concrete spacers, we elevate the reinforcement approximately 2 inches from the subgrade.
For slabs that will bear significant loads, we often increase reinforcement at strategic points or incorporate additional steel around columns and at construction joints. When joining rebar sections, we overlap bars by at least 40 times their diameter and secure connections with wire ties. Throughout this stage, we carefully maintain the reinforcement’s position during subsequent operations, as displacement can compromise the slab’s long-term performance.
Concrete Placement and Finishing: Building the Surface
The actual concrete placement represents the most visible transformation in the construction process. We coordinate closely with ready-mix suppliers to ensure consistent delivery of properly proportioned concrete that meets the project’s specific strength requirements. Starting from one end of the formwork, our crews place concrete methodically, working in organized sections to maintain a consistent workflow.
Immediately after placement, we use mechanical vibrators to consolidate the concrete, eliminating air pockets that could weaken the structure. The vibration process requires skill—inserting the vibrator vertically at regular intervals without over-vibrating, which can cause aggregate segregation. Once consolidated, we strike off excess concrete using screeds pulled across the formwork edges, establishing the initial level surface.
Finishing operations follow a carefully timed sequence. After the concrete begins to stiffen and surface water disappears, we apply floating techniques to embed aggregate, close surface voids, and prepare for final finishing. Depending on the intended use of the slab, we may apply a broom finish for exterior surfaces requiring slip resistance or execute multiple passes with power trowels to create a smooth, dense surface for interior floors.
Curing and Protection: Ensuring Long-Term Durability
The final phase of concrete floor slab construction is crucial for long-term performance. Proper curing prevents rapid moisture loss that can lead to shrinkage cracks and surface dusting. We implement suitable curing methods based on project conditions, often applying liquid membrane-forming compounds that create a protective film over the fresh concrete.
For high-performance slabs, we sometimes employ wet curing techniques, maintaining moisture on the surface through periodic spraying or covering with saturated burlap. The curing period typically extends for 7 days, during which we protect the new slab from temperature extremes, premature loading, and other potential damage. Only after the concrete reaches sufficient strength do we remove formwork, typically around 24-48 hours for slab edges.
Throughout the entire construction process, we maintain comprehensive quality control procedures, including regular slump testing, concrete temperature monitoring, and verification of finishing techniques. These measures ensure the completed floor slab meets both structural requirements and aesthetic expectations.
Slab Type | Typical Thickness | Load Distribution | Key Advantages | Applications |
---|---|---|---|---|
One-Way Slabs | 4-6 inches | One-direction | Simple construction | Residential rooms, corridors |
Two-Way Slabs | Varies | Multi-direction | High structural integrity | Commercial spaces |
Flat Slabs | Varies | Multi-direction | Open spaces | Offices, hotels |
Flat Plates | Uniform thickness | Multi-direction | Minimal formwork | Buildings with moderate loads |
Waffle Slabs | Reduced concrete volume by 30% | Grid pattern | Architectural appeal | Theaters, auditoriums |
Hollow Core Slabs | Precast units | Longitudinal voids | Speedy installation | Commercial floors |
Post-Tensioned Slabs | Thinner slabs | High tension | Less deflection | Parking structures |
By following this systematic approach to concrete floor slab construction, we deliver durable, high-quality surfaces that meet the specific needs of each project. The attention to detail at each phase—from formwork erection through final curing—creates floor slabs that maintain their integrity and appearance for decades to come.
What Are the Thermal Properties of Concrete Slabs?
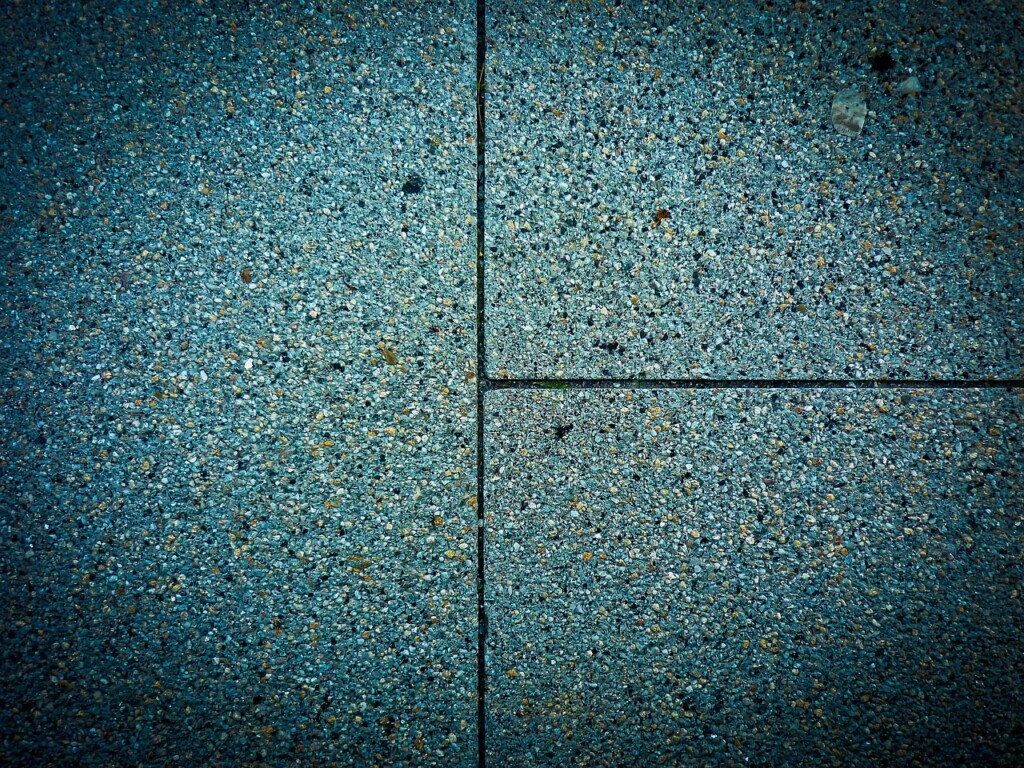
Understanding the thermal properties of concrete slabs is essential for optimizing building energy performance. In our work with developers and property owners, we have found that concrete’s thermal behavior significantly influences both construction decisions and long-term building operation costs.
Thermal Mass: Concrete’s Energy Storage Capacity
Concrete slabs possess high thermal mass, which refers to their ability to absorb, store, and later release heat. This density-derived property allows concrete to act as a thermal buffer, absorbing excess heat during warmer periods and gradually releasing it when temperatures drop.
When we design buildings with concrete slabs, we leverage this gradual temperature response to create more stable indoor environments. In locations experiencing significant day-night temperature fluctuations, properly positioned concrete slabs can reduce peak heating and cooling loads by 10-30%, depending on climate conditions and building design.
The practical benefit? Buildings stay cooler during hot days and warmer during cool nights without requiring constant mechanical system operation. For a typical commercial development, this translates to measurable energy savings and improved occupant comfort.
Thermal Conductivity and Heat Transfer
Concrete’s thermal conductivity, or how readily it conducts heat, typically ranges from 0.8 to 2.0 W m−1 K−1, which is relatively high compared to insulating materials. This means that while concrete can store considerable thermal energy, it also transfers heat efficiently when temperature differentials exist.
We have observed that concrete density significantly affects its conductivity. Standard structural concrete with a density around 2,400 kg/m³ conducts heat more readily than lightweight concrete mixtures. This relationship between density and conductivity offers us design flexibility when balancing structural requirements with thermal performance goals.
For comparison, materials like wood (0.12-0.04 W m−1 K−1) and fiberglass insulation (0.04 W m−1 K−1) have significantly lower conductivity values, while metals like steel (43 W m−1 K−1) conduct heat much more readily than concrete.
Material | Thermal Conductivity (W/m K) |
Brick, dense | 1.31 |
Concrete | 1.6 – 1.8 |
Wood | 0.12 – 0.04 |
Fiberglass | 0.04 |
Steel | 43 |
R-Value and Insulation Considerations
The R-value of a standard 4-inch concrete slab is approximately 0.4 (IP units), offering minimal thermal resistance. This is why we typically incorporate insulation systems with concrete slabs in energy-efficient construction. Without proper insulation, concrete’s relatively high thermal conductivity can lead to unwanted heat loss in winter and heat gain in summer.
When working on energy-efficient projects, we often position expanded polystyrene (EPS) or extruded polystyrene (XPS) insulation boards beneath or around concrete slabs to enhance the overall thermal resistance of the floor assembly. A typical configuration might include a vapor barrier, 2-3 inches of rigid foam insulation, and then the concrete slab—creating a system with an effective R-value between 10-15.
In cold climate zones, we often extend this insulation to create a thermal break at slab edges, preventing heat loss through thermal bridging where the slab meets foundation walls.
Practical Applications for Energy Efficiency
We approach concrete slab thermal design differently based on building use and local climate. In passive solar applications, we might specify darker-colored concrete floors in south-facing spaces to maximize solar heat gain in winter. For commercial buildings with high cooling loads, night cooling strategies may be employed, allowing the slab’s thermal mass to absorb excess heat during occupied hours and release it overnight.
Modern construction methods like insulated concrete forms (ICFs) allow us to combine concrete’s structural strength with enhanced insulation values. For radiant floor heating systems, concrete’s thermal conductivity becomes advantageous, efficiently transferring heat from embedded tubing to interior spaces.
The slow thermal response of concrete is particularly valuable in climates with significant diurnal temperature swings, where the mass can moderate temperature extremes and reduce HVAC system cycling. In more consistent climates, we focus more on insulation strategies to complement the concrete’s inherent properties.
Conclusion: Choosing the Right Slab for Your Construction Project
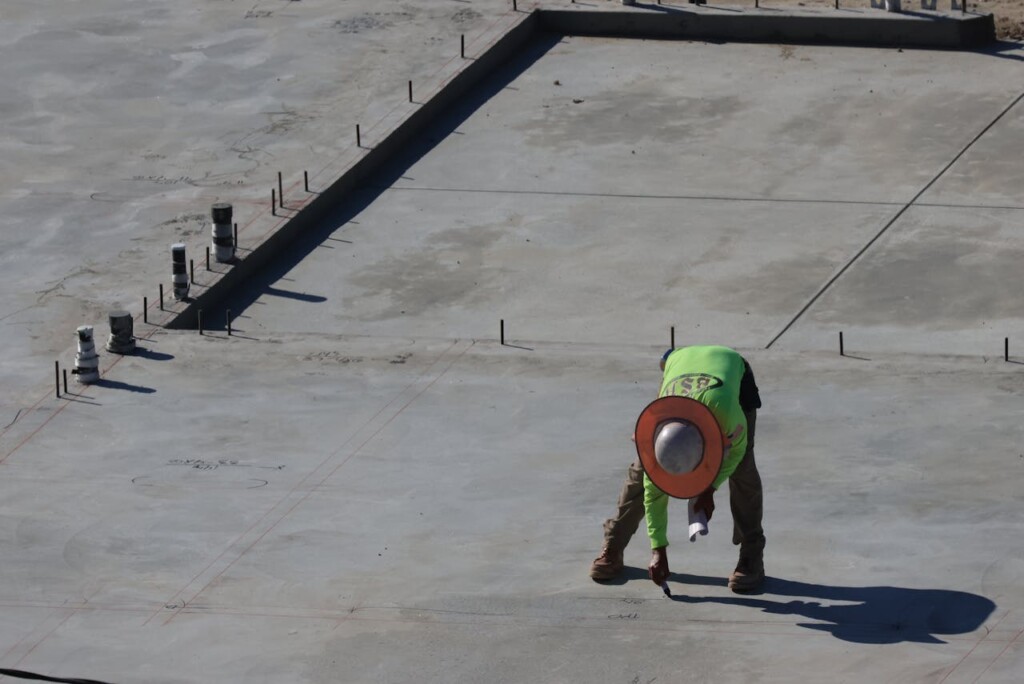
Selecting the ideal concrete slab is one of the most critical decisions in our clients’ construction projects. At EB3 Construction, we approach slab selection with a methodical evaluation of each project’s unique needs, avoiding default reliance on familiar solutions. The structural integrity, budget considerations, and long-term performance all depend on this essential foundation element.
When advising developers and property owners on slab choices, we focus on several key factors. We start by analyzing span requirements and anticipated load conditions, especially for multi-story structures or buildings with specialized equipment. Construction timeline constraints may influence our recommendations, as some slab types require extended curing times or specialized formwork. Additionally, we assess soil stability through appropriate testing; clay-rich or expansive soils require different approaches than stable sandy or rocky sites. For projects with specific thermal performance needs, we might suggest insulated slab systems that enhance energy efficiency while meeting structural requirements.
Ready to ensure your next project has the right foundation from the outset? Contact our team for a consultation on selecting the optimal concrete slab solution for your construction needs.