In construction, walls are much more than simple vertical barriers. When building structures for our clients, we consider walls critical structural elements that provide support, division, and protection throughout a building. Our approach to wall construction emphasizes selecting the right configuration for each specific purpose within the project scope.
Walls fall into two fundamental categories that guide our construction planning. Framed walls, constructed using a system of posts, columns, or studs, transfer building loads through these vertical members to the foundation below. In contrast, mass walls rely on the inherent strength of solid materials, like concrete or brick masonry, to support structural loads through their entire mass.
When coordinating with architects and structural engineers, we evaluate each wall’s intended function within the building envelope. Load-bearing walls form part of the structural framework, carrying the weight of floors and roof systems above them. Non-load-bearing walls, typically installed after completing the primary structure, divide interior spaces without contributing to structural integrity. Both types play distinct roles in our construction methodology, with material selection and construction techniques varying substantially based on their purpose.
What Are the Primary Materials Used in Wall Construction?

When evaluating a project’s wall systems at EB3 Construction, we carefully match materials to the specific requirements of each development. The material selection directly impacts the structural integrity, energy efficiency, and long-term performance of the building envelope. Our experience shows that each wall material offers distinct advantages for different applications.
Brick and Masonry Systems
Brick remains one of the most reliable and time-tested wall materials we implement in our projects. Constructing brick walls provides developers with exceptional durability, natural fire resistance, and virtually maintenance-free exteriors. The thermal mass properties of brick also contribute to energy efficiency by slowing temperature fluctuations and reducing HVAC demands.
For projects requiring more visual variety, we often combine traditional clay bricks with concrete masonry units (CMUs) in patterns that create architectural interest while maintaining structural integrity. This approach works particularly well in mixed-use developments where aesthetic appeal must balance with practical considerations. The February 2023 shortage of certain brick types has prompted us to maintain strong supplier relationships to ensure material availability for our clients.
When reinforcing masonry walls, we embed steel bars in specified cavities at vertical junctures and lintels, which are then grouted with specialty concrete mixes. This reinforcement significantly enhances lateral force resistance, particularly important in regions with seismic activity or high wind loads.
Natural Stone Construction
Natural stone wall systems offer unparalleled strength and character for premium developments. We source various stone types based on the project’s specific requirements, knowing that each variety brings unique properties. Granite provides exceptional compressive strength for load-bearing applications, while limestone offers easier workability for detailed architectural elements.
The substantial thermal mass of stone walls creates natural temperature regulation inside buildings. During summer, these walls absorb heat during the day and slowly release it at night when temperatures drop. In winter, they retain warmth from heating systems, creating more stable indoor environments and reducing energy consumption over time.
When implementing stone in modern construction, we typically use it as a veneer over a structural backup wall rather than as a solid mass wall. This approach maintains the aesthetic benefits while improving cost-efficiency and installation timelines.
Concrete Wall Systems
For projects demanding maximum structural capacity, our concrete wall systems deliver superior performance. We implement both cast-in-place and precast concrete walls depending on project requirements. Cast-in-place offers complete design flexibility and seamless connections, while precast provides accelerated installation and factory-controlled quality.
Reinforced concrete walls require careful planning of rebar placement to maximize structural integrity. We typically use #4 to #6 bars in residential applications and larger diameter reinforcement for commercial structures. The concrete mix design varies based on exposure conditions, with water-cement ratios carefully controlled to prevent cracking and ensure long-term durability.
For projects with strict thermal performance requirements, we’ve successfully implemented insulated concrete forms (ICFs) that combine the structural benefits of concrete with continuous insulation. These systems have proven particularly effective in severe weather regions where both strength and energy efficiency are priorities.
Wall Type | Material | U-value (W/m²K) | Whole-wall R-value (hft²°F/Btu) |
---|---|---|---|
Brick and Block Walls | Single Skin Brick | 3.28 | 9.6 |
Brick and Block Walls | Plastered Brick | 3.02 | |
Cavity Walls with EPS | EPS Insulated | 0.47 | |
Concrete Walls | Solid Concrete | 3.10 | |
Concrete Walls | Lightweight Concrete with Insulation | 0.45 |
Light-Frame Wall Construction
Our timber and steel framing systems offer flexibility and speed for many applications. Wood framing remains cost-effective for low-rise residential and light commercial projects, while steel studs provide improved fire resistance and dimensional stability. We typically space studs at 16 or 24 inches on-center, with modifications based on specific load requirements.
For wood-framed walls, we select lumber grades appropriate to each application, using higher grades for load-bearing elements and more economical options for non-structural partitions. The market volatility in lumber pricing since 2020 has required us to implement more precise material ordering and scheduling to maintain budget controls.
Steel framing offers significant advantages in certain applications, particularly in fire-resistant construction. We utilize galvanized steel studs ranging from 0.5mm to 0.8mm thickness depending on the wall height and loading conditions. These systems integrate seamlessly with other building components and allow efficient installation of mechanical and electrical systems.
Interior Partition Materials
Interior walls serve different functions than exterior walls, requiring materials focused on acoustic performance, ease of installation, and design flexibility. Our standard interior partition system utilizes metal studs with gypsum board facing, providing good sound attenuation and fire resistance while allowing efficient installation.
For areas requiring enhanced acoustical separation, we implement double-layer drywall systems with acoustic insulation and resilient channels. These specialized systems can achieve STC ratings above 55, creating effective sound barriers between adjacent spaces in mixed-use or multifamily developments.
Glass partition systems have become increasingly popular in commercial projects, creating visual connectivity while maintaining separate functional zones. We install frameless glass systems with minimal hardware for contemporary aesthetics, or more traditional framed glass partitions where budget considerations are paramount.
How Do Construction Techniques Differ Between Wall Types?
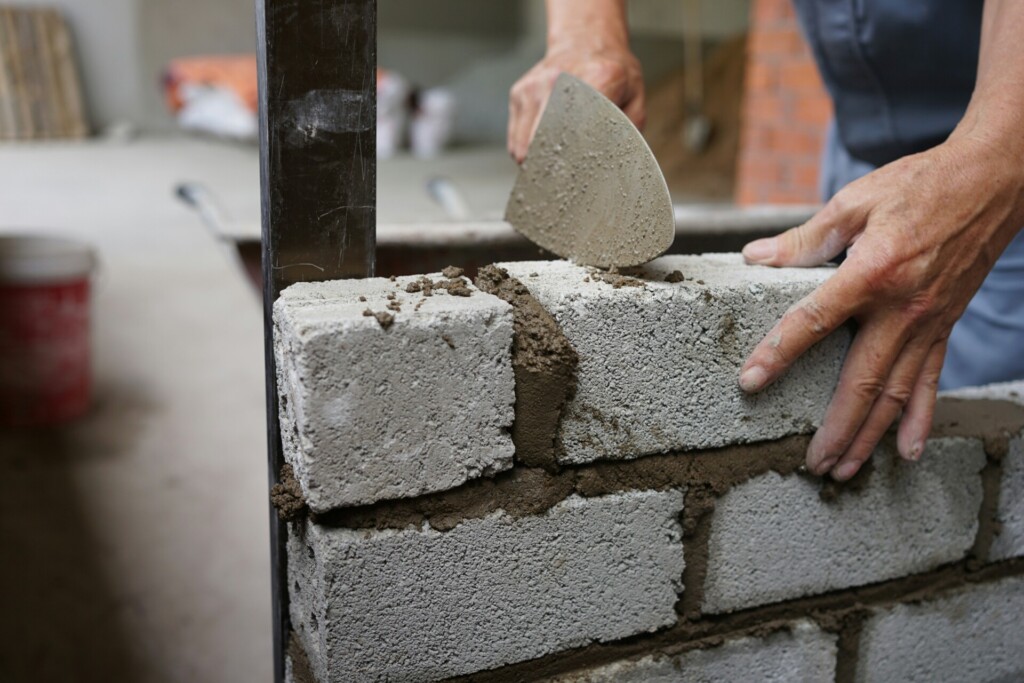
When constructing walls using different materials, the approach, techniques, and tooling requirements can vary significantly. As general contractors, we have developed specialized methods for each wall type to deliver optimal results that balance durability, cost efficiency, and aesthetic appeal for our developer clients.
Brick Wall Construction
Our brick wall construction begins with careful material selection. We choose bricks for uniformity, structural integrity, and consistency in color and texture. The foundation preparation must be level and solid, as the entire structure depends on this initial stability.
The heart of brick construction lies in the bonding pattern—how we arrange individual bricks to create structural strength. Common patterns include the stretcher bond (most frequently used in modern construction), English bond, and Flemish bond. Each provides different aesthetic qualities and structural benefits. When working with architects who specify decorative patterns, we ensure our masons understand the technical requirements of these more complex designs.
Mortar mixing is critical in brick construction. We carefully control the ratio of cement, sand, and water to achieve the right consistency and strength. Too wet, and the mortar becomes unworkable; too dry, and proper bonding doesn’t occur. The thickness of mortar joints (typically 10mm) must remain consistent throughout the wall for both structural integrity and visual appeal.
Stone Wall Construction
Stone masonry requires the highest level of craftsmanship among wall types. We select stones not just for appearance but for how they will work together structurally. Unlike the uniformity of bricks, stone’s irregularity demands skilled masons who understand how to create stability from varied shapes.
In conventional stone walls, we use mortar similar to brick construction but often with different proportions to accommodate the weight and characteristics of stone. The process is more time-consuming as each stone must be individually assessed and placed. For heritage projects, we often match historical mortar compositions using lime rather than modern cement.
Dry stone walling represents a specialized technique where we construct walls without mortar. This method, often used in landscape features, relies entirely on the careful selection and placement of stones that lock together through friction and gravity. The wall tapers slightly inward as it rises, with larger stones at the base and progressively smaller ones toward the top. Despite lacking mortar, properly constructed dry stone walls can last for generations.
Concrete Wall Construction
Concrete wall construction involves significantly different processes than masonry. We begin by building formwork—temporary molds that shape the concrete as it cures. Precise formwork construction is essential as it determines the final dimensions and surface quality of the wall.
Before pouring, we install reinforcement bars (rebar) in a grid pattern within the formwork. This reinforcement provides the tensile strength that concrete naturally lacks, making the wall resistant to cracking under pressure or during seismic events. The spacing and diameter of rebar depends on structural requirements specified by engineers.
The concrete mix design and pouring technique require careful control. We vibrate freshly poured concrete to eliminate air pockets that would compromise strength. The curing process is equally important—we maintain proper moisture and temperature conditions for several days after pouring to ensure the concrete develops its full strength. This often involves covering the concrete and regular watering in dry conditions.
Material Type | Construction Technique | Key Characteristics |
---|---|---|
Brick | Laying bricks in patterns with mortar | Aesthetic appeal, good sound insulation, requires added insulation for thermal efficiency |
Stone | Dry stone walling or using mortar | Timeless beauty, strong, offers thermal mass, may require added insulation |
Concrete | Poured concrete with formwork, may use rebar | High load-bearing capacity, moisture, and pest resistance, can include integrated insulation |
Timber Framing | Wood studs with attached drywall or siding | Cost-effective, flexible, offers space for insulation |
Steel Framing | Galvanized steel studs in a skeleton structure | Fire-resistant, dimensional stability, good for integration with MEP systems |
Framed Wall Construction
When constructing framed walls, we create a skeleton structure using either wood or steel studs. This approach fundamentally differs from mass wall construction methods, as the frame itself isn’t the finished surface but rather a support system for other materials.
In wood framing, we typically space studs at 16 or 24 inches on center, depending on structural requirements and local building codes. Top and bottom plates distribute loads evenly, while headers span openings for doors and windows. For steel framing, we use cold-formed steel studs with similar spacing, though the connection methods differ—screws replace nails, and specialized tools are required.
One significant advantage of framed construction is the cavity created between studs, which provides space for insulation, electrical wiring, and plumbing. We install vapor barriers and sheathing to protect against moisture and provide structural rigidity. Interior surfaces typically receive drywall finishing, while exterior surfaces may receive various cladding systems—from brick veneer to fiber cement siding.
Frame construction typically proceeds much faster than masonry or concrete methods, allowing us to enclose buildings quickly and move to interior work sooner. This speed advantage makes framed construction particularly attractive to developers working with tight timelines, though the wall’s performance characteristics differ significantly from mass wall systems.
What Planning Considerations Are Essential Before Building a Wall?
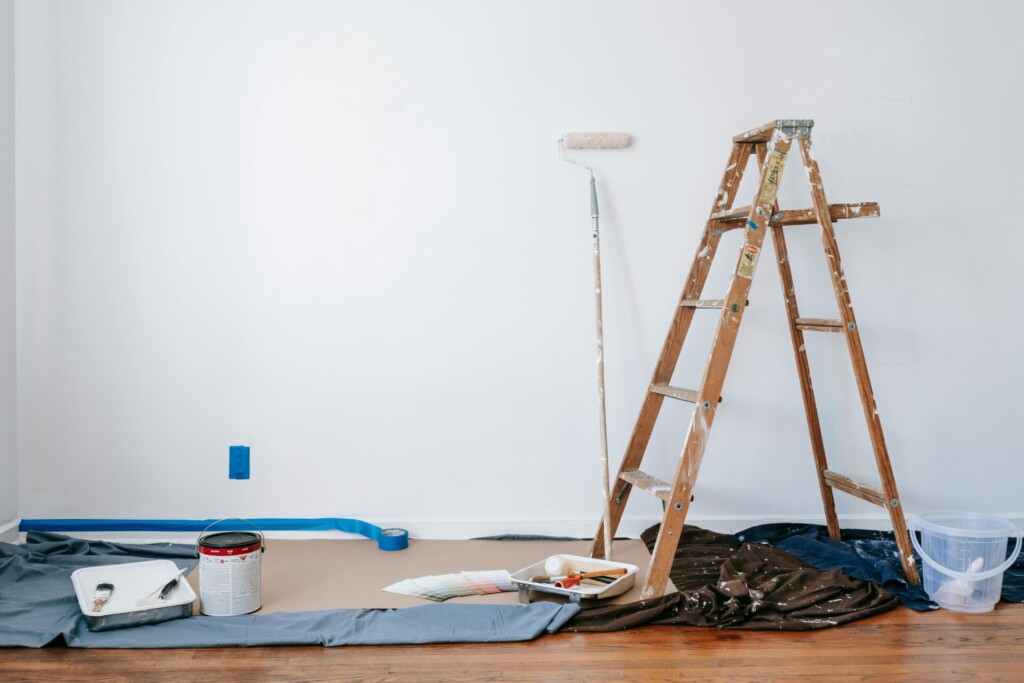
Before starting a wall construction project, proper planning is crucial for success. At EB3 Construction, we’ve found that thorough preparation prevents costly delays and structural issues. Here are the essential planning considerations to address before laying the first brick.
Determining Your Wall’s Purpose
Every successful wall construction begins with clarity about its function. We always start by asking clients what their wall needs to accomplish. Is it for structural support in a building expansion, creating privacy between properties, or offering decorative division within a space? The wall’s purpose guides every subsequent decision, from materials to design specifications.
Purpose matters because structural walls require different engineering approaches than decorative ones. For example, load-bearing walls need precise foundation work and structural reinforcement, unlike a garden privacy wall. Getting this wrong can lead to serious safety issues or wasteful overbuilding.
Building Codes and Regulations
Local building codes aren’t just bureaucratic hurdles—they’re essential safeguards protecting property owners and the public. We thoroughly research applicable regulations before finalizing any wall construction plan. Most jurisdictions have specific requirements regarding wall height, setbacks from property lines, and necessary permits.
Building officials typically review plans for structural integrity, especially for walls exceeding certain height thresholds. For load-bearing walls, codes often specify minimum thickness, foundation requirements, and reinforcement details. Ignoring these requirements can result in stop-work orders, fines, or even forced demolition—expenses no developer wants to incur.
Strategic Material Selection
Material choice dramatically impacts a wall’s performance, longevity, and cost. We evaluate materials based on structural requirements, environmental conditions, budget constraints, and aesthetic preferences. Common options include:
Brick offers excellent durability and fire resistance but requires skilled masonry work. Concrete blocks provide structural strength economically but may need additional finishing for visual appeal. Drywall is perfect for interior partitions but unsuitable for exterior applications. Timber creates warm aesthetics but demands proper treatment against moisture and pests.
The material selection must consider local availability, as transportation costs for heavy materials like stone or concrete can significantly impact budgets. We often recommend on-site material samples to evaluate appearance under actual lighting conditions before making final decisions.
Site Evaluation and Location Factors
The wall’s physical location demands careful assessment. We conduct thorough site evaluations to identify challenges before construction begins. Property boundaries must be precisely identified—encroaching on neighboring property can lead to costly legal disputes and required modifications.
Soil conditions fundamentally affect foundation requirements. Expansive clay soils might necessitate deeper footings, while sandy soils may require wider footings for adequate load distribution. Drainage patterns need evaluation to prevent water accumulation, which could undermine structural integrity. For exterior walls, we also consider sunlight exposure, prevailing winds, and other environmental factors that might affect material performance.
Design Specifications and Structural Planning
Wall design goes beyond aesthetics to address critical structural requirements. Height and thickness calculations depend on the wall’s purpose and the loads it will bear. A retaining wall holding back soil requires substantially different engineering than a simple garden wall. For taller walls, we often incorporate structural reinforcement such as rebar or wire mesh.
We develop detailed construction drawings showing dimensions, materials, reinforcement details, and connection methods to other structures. These plans become the blueprint for construction and are often required for permit applications. Proper design planning prevents mid-construction changes that can compromise structural integrity or blow budgets.
Tool and Equipment Preparation
Having the right tools ready before construction begins prevents costly delays and quality compromises. Basic wall construction typically requires measuring tools (tape measure, level, plumb line), cutting equipment appropriate for the chosen materials, mixing equipment for mortar or concrete, and specialized tools for specific materials.
For larger walls, we coordinate heavy equipment needs such as excavators for foundation work or lifts for higher sections. Safety equipment—including personal protective gear and appropriate scaffolding—is non-negotiable. Thorough tool preparation ensures work proceeds efficiently with proper technique.
Budget and Timeline Planning
Realistic budgeting requires accounting for all potential costs. Beyond materials and labor, we include allowances for permits, equipment rental, waste disposal, and contingency funds for unexpected issues. Weather considerations affect outdoor construction timelines, and material lead times can impact scheduling.
We develop detailed construction schedules that account for curing times between phases and coordinate with other site activities. This prevents the common problem of walls being rushed to meet artificial deadlines, potentially compromising quality and safety.
For complex projects, we often phase construction to manage cash flow and allow for inspections at critical points. Proper timeline planning also helps coordinate with other trades that might need to install elements within or adjacent to the wall.
Professional Consultation
For walls with significant structural implications, professional engineering input is invaluable. Structural engineers can provide calculations for load-bearing capacity, foundation requirements, and reinforcement specifications. For walls in challenging soil conditions or seismic zones, geotechnical engineers may need to evaluate soil stability.
While this represents an upfront cost, professional consultation prevents the far greater expense of structural failures or code compliance issues. Even relatively simple walls benefit from experienced construction guidance to ensure proper techniques and material usage.
Thoughtful planning transforms wall construction from a potentially risky undertaking into a predictable, successful project. By addressing these essential considerations before construction begins, we ensure walls that perform their intended function safely, durably, and economically. The small investment in thorough planning pays dividends throughout the construction process and the lifetime of the structure.
What Are Effective Insulation Options for Different Wall Types?
At EB3 Construction, we recognize that proper wall insulation represents one of the most impactful investments in building performance. When we execute insulation installations, we carefully match solutions to specific wall structures to maximize thermal efficiency while maintaining structural integrity. Each wall type demands a tailored approach to achieve optimal results.
Solid Wall Insulation Solutions
When addressing solid brick, stone, or concrete walls, we typically recommend one of two proven approaches. External wall insulation (EWI) involves securing high-performance materials like expanded polystyrene (EPS) or mineral wool to the exterior surface, followed by a protective render or cladding system. This method not only preserves valuable interior space but also effectively wraps the building in a continuous thermal blanket.
For properties where exterior modifications aren’t feasible due to historic preservation requirements or space constraints, we implement internal wall insulation (IWI) strategies. This approach involves attaching insulation boards to interior surfaces and finishing with plasterboard. While this slightly reduces room dimensions, it substantially improves the wall’s thermal resistance and creates a more comfortable indoor environment.
For clients seeking innovative solutions, we often integrate insulated plaster systems that combine thermal materials with finishing compounds. These specialized systems offer excellent thermal performance without sacrificing aesthetic appeal, particularly valuable in renovation projects where maintaining interior character is essential.
Cavity Wall Insulation Techniques
Modern cavity walls present different insulation opportunities than their solid counterparts. We regularly retrofit existing cavity walls by introducing loose-fill materials such as mineral wool, rigid foam boards, or expanding foam. This process involves drilling small access holes and injecting or inserting insulation to fill the void between wall layers.
The insulation choice depends on several factors, including cavity width and condition. Rigid foam board insulation provides exceptional R-values ranging from 3.6 to 6.5 per inch of thickness, making it particularly effective in narrower cavities. For wider cavities with irregular dimensions, we often utilize spray foam, which expands to fill voids completely and creates an effective air seal.
During our pre-installation assessments, we carefully examine wall conditions for moisture issues, ensuring the selected insulation won’t contribute to dampness problems. Proper moisture management remains critical when insulating any cavity wall system, as trapped moisture can compromise both insulation performance and structural integrity.
Integrated Systems for New Construction
For new construction projects, we implement advanced integrated wall systems that combine structural elements with insulation. Insulated concrete forms (ICFs) represent one of our most effective solutions, using hollow foam blocks as permanent formwork for poured concrete. This creates walls with built-in insulation on both interior and exterior faces, delivering exceptional thermal performance and structural strength.
Structural insulated panels (SIPs) offer another high-performance option, sandwiching rigid foam between structural boards to create prefabricated wall sections. We frequently use SIPs in commercial applications where construction speed and energy efficiency are priorities. These panels significantly reduce thermal bridging compared to conventional framing while accelerating the construction timeline.
When working with traditional framing, we often upgrade performance by combining various insulation layers. This might include spray foam between studs to eliminate air leakage, followed by continuous rigid insulation over the entire wall surface to minimize thermal bridging through framing members. This comprehensive approach delivers superior thermal performance even in conventional construction methods.
Performance Considerations for All Wall Types
Beyond simply filling wall cavities, we address critical performance details that significantly impact overall effectiveness. Thermal bridging occurs when heat bypasses insulation through structural elements, drastically reducing efficiency. We mitigate this through careful detailing around window openings, floor junctions, and other penetrations.
Air leakage represents another major efficiency challenge. When insulating any wall type, we implement comprehensive air sealing strategies to prevent conditioned air from escaping through gaps and cracks. This attention to air barrier continuity often delivers energy savings comparable to or exceeding the insulation itself.
For buildings in humid climates, we integrate vapor management strategies appropriate to the specific wall assembly. This might involve vapor retarders, ventilated rain screens, or moisture-resistant insulation materials, depending on the wall construction and local climate conditions.
By taking this comprehensive approach to wall insulation, we deliver buildings that maintain comfortable interior temperatures with minimal energy input, regardless of exterior conditions. The result is not just lower utility bills but also improved occupant comfort, reduced HVAC system wear, and enhanced building durability.
Conclusion: Building Long-Lasting and Efficient Walls
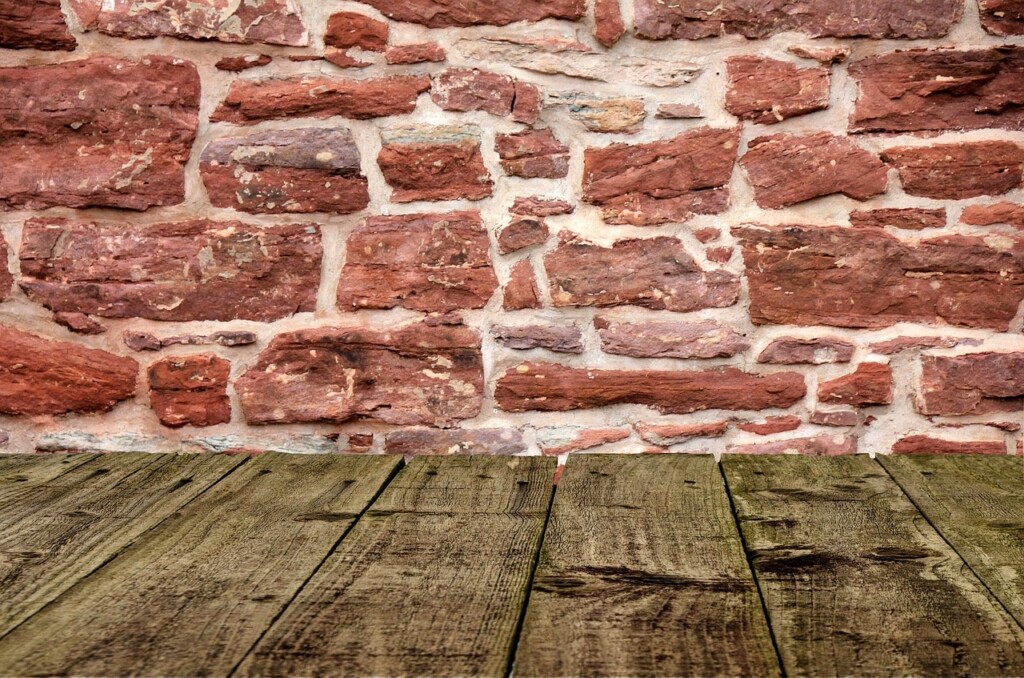
At EB3 Construction, we believe that the key to successful wall construction lies in mastering the basics: a comprehensive understanding of wall systems, careful material selection, and precise execution. The recent supply chain challenges have underscored the importance of this expertise, requiring us to be resourceful in sourcing materials that meet both performance and budget criteria.
When constructing walls for your project, we are not just assembling components — we are creating integrated systems that will impact your building’s performance for decades. Our approach blends time-tested construction methods with innovative insulation strategies to meet today’s energy demands. For developers aiming to maximize ROI, a modest initial investment in high-performance wall assemblies can lead to substantial returns through reduced operational costs, enhanced tenant satisfaction, and improved building durability. Especially in Florida’s challenging climate, where moisture management is critical, we have developed techniques that protect wall integrity against humidity while maintaining optimal thermal performance.
Ready to build walls that stand the test of time and deliver exceptional energy performance? Contact EB3 Construction to discuss your project requirements.