When rising material costs and tight schedules threaten project profitability, value engineering offers a proven path to deliver more for less—without cutting corners. By systematically questioning each design decision and weighing function against cost, we can uncover smarter ways to achieve the owner’s goals while safeguarding quality, performance, and sustainability.
At EB3 Construction, our approach follows a six-stage methodology that moves from data gathering through implementation and monitoring, ensuring every recommendation is grounded in real-world feasibility. The result is a project that not only meets budget but often exceeds expectations in efficiency, durability, and long-term value.
In the sections that follow, we’ll walk through each stage in detail and highlight the benefits, challenges, and best practices that turn value engineering from a buzzword into a competitive advantage on the jobsite.
What Are the Key Stages of the Value Engineering Process?
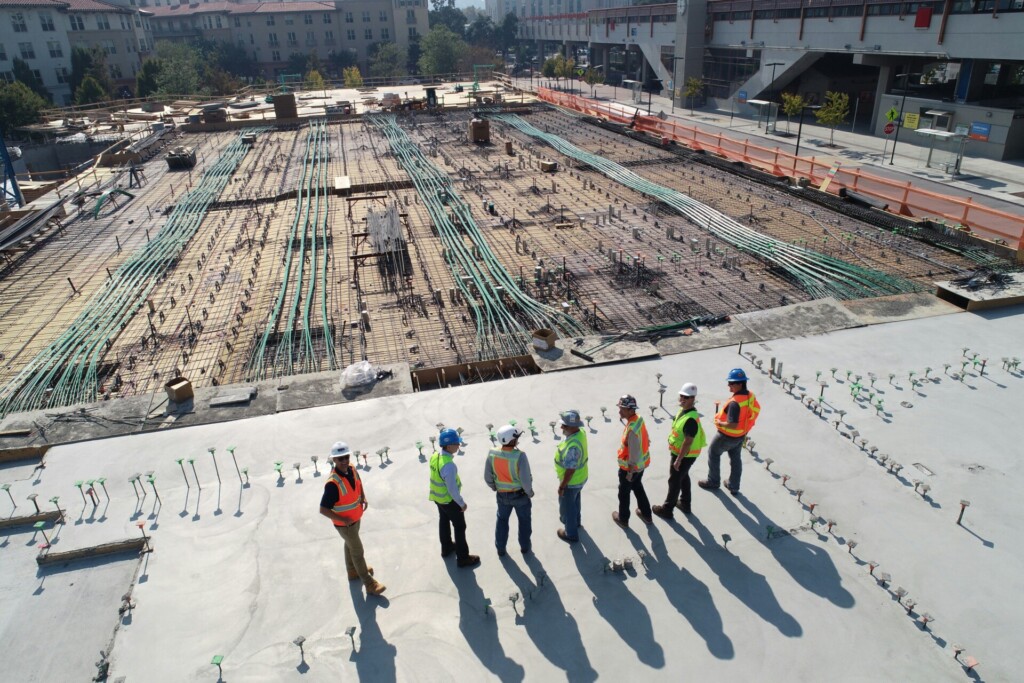
The value engineering process in construction follows a structured methodology consisting of six essential stages. This systematic approach enables project teams to thoroughly analyze and optimize a construction project’s value. Let’s examine each stage in detail:
1. Information Gathering
The process begins with a comprehensive collection of data related to the project. Teams gather information on:
- Project scope and objectives
- Budget constraints
- Design specifications
- Material and labor costs
- Regulatory requirements
This foundational stage ensures that all stakeholders have a clear understanding of the project parameters before proceeding.
2. Functional Analysis
Once information is collected, the team conducts a detailed functional analysis. This involves:
- Identifying the primary and secondary functions of each project component
- Evaluating the necessity and cost of each function
- Determining which functions offer opportunities for cost reduction or value improvement
This analytical stage helps prioritize efforts on areas with the greatest potential for value enhancement.
3. Creative Brainstorming
With a clear understanding of project functions, the team enters a creative phase to generate alternative solutions. This stage involves:
- Encouraging open and innovative thinking
- Proposing alternative materials, methods, or designs
- Considering unconventional approaches to meet functional requirements
The goal is to produce a wide range of ideas without judgment, fostering creativity and potential breakthroughs.
4. Evaluation
Following the brainstorming phase, each proposed idea undergoes rigorous evaluation. This stage includes:
- Assessing the feasibility of each alternative
- Conducting cost-benefit analyses
- Considering potential risks and long-term implications
- Ranking ideas based on their potential value improvement
This critical stage filters out impractical suggestions and identifies the most promising value engineering opportunities.
5. Development
The most viable alternatives from the evaluation stage are then further developed. This involves:
- Refining selected ideas into actionable proposals
- Creating detailed implementation plans
- Estimating costs and potential savings more accurately
- Addressing any technical or logistical challenges
This development stage transforms conceptual ideas into concrete, implementable solutions.
6. Implementation and Monitoring
The final stage involves putting the selected value engineering recommendations into action. Key activities include:
- Integrating approved changes into the project plan
- Communicating modifications to all relevant stakeholders
- Monitoring the implementation process
- Tracking actual costs and benefits against projections
- Making adjustments as necessary to ensure value improvements are realized
Proper execution and ongoing assessment are crucial to achieving the full benefits of the value engineering process.
By systematically working through these six stages, construction teams can effectively identify and implement value-enhancing changes, ultimately delivering projects with improved functionality and cost-effectiveness.
Stage | Description |
---|---|
1. Data Collection | Gathering comprehensive project data including materials, labor costs, design specifications, and timelines. |
2. Data Analysis | Conducting cost-benefit analysis to identify areas for cost savings and quality improvements. |
3. Solution Development | Transforming insights from analysis into actionable improvements, exploring alternatives to maximize value. |
4. Collaborative Planning | Stakeholders collaborate to implement solutions, ensuring alignment with project objectives. |
5. Implementation | Executing changes systematically while monitoring resources and timelines for maximum value. |
What Benefits Does Value Engineering Provide to Construction Projects?
Value engineering delivers multiple benefits to construction projects, extending far beyond merely reducing costs. While cost savings are often the most immediate and tangible advantage, the value engineering process provides numerous other benefits that improve project outcomes and enhance stakeholder satisfaction.
Cost Reduction
The most apparent benefit of value engineering is its ability to reduce overall project costs without sacrificing quality or functionality. We closely analyze every aspect of the project to identify areas where expenses can be trimmed or eliminated. This may involve substituting more cost-effective materials, streamlining construction methods, or optimizing resource allocation. For example, on a recent commercial building project, our value engineering analysis enabled us to reduce structural steel requirements by 15% through an innovative redesign, saving over $500,000 in material costs alone.
Improved Efficiency
Value engineering inherently leads to enhanced project efficiency by streamlining processes and eliminating waste. We scrutinize every element of the construction plan to identify bottlenecks, redundancies, and inefficiencies. This often results in accelerated project timelines and improved resource utilization. On a recent highway expansion project, our value-engineered approach to traffic management and construction sequencing reduced the overall project duration by 3 months.
Enhanced Performance
Rather than compromising on quality, effective value engineering actually improves long-term building performance and durability. We evaluate materials, systems, and design elements to select options that provide the best combination of initial cost, maintenance requirements, and lifecycle performance. For instance, specifying a higher-grade roofing system may increase upfront costs slightly but dramatically reduce maintenance needs and extend the roof’s functional lifespan.
Sustainable Practices
Value engineering promotes sustainability by identifying eco-friendly solutions that also reduce costs. We look for opportunities to minimize energy consumption, reduce waste, and incorporate recycled or locally-sourced materials. On a recent university dormitory project, our value engineering process led to the selection of a geothermal HVAC system that reduced energy costs by 30% compared to conventional systems while also lowering the building’s carbon footprint.
Improved Stakeholder Relationships
The collaborative nature of value engineering fosters better communication and relationships between project stakeholders. By bringing together designers, contractors, suppliers, and owners early in the process, we create a shared vision for project success. This alignment of goals and expectations leads to fewer conflicts and change orders during construction. The transparent process also builds trust, as stakeholders see how decisions impact costs and project outcomes.
Better Decision-Making
Value engineering provides a structured framework for evaluating options and making informed decisions. We utilize data-driven analysis to compare alternatives based on cost, performance, and long-term value. This systematic approach ensures that project teams select the best solutions rather than defaulting to familiar but potentially suboptimal choices. The process also creates a clear record of decision rationale, which is valuable for future reference.
Risk Mitigation
By thoroughly analyzing project elements early in the design phase, value engineering helps identify and mitigate potential risks. We develop contingency plans for likely issues and build flexibility into designs to accommodate unforeseen challenges. This proactive approach reduces the likelihood of costly surprises during construction and improves the project’s ability to adapt to changing conditions.
Ultimately, while cost reduction is often the primary driver for implementing value engineering, the process delivers a wide range of benefits that enhance project success in multiple dimensions. By improving efficiency, performance, sustainability, and stakeholder satisfaction, value engineering creates lasting value that extends far beyond the initial construction phase.
When Is the Optimal Time to Implement Value Engineering?
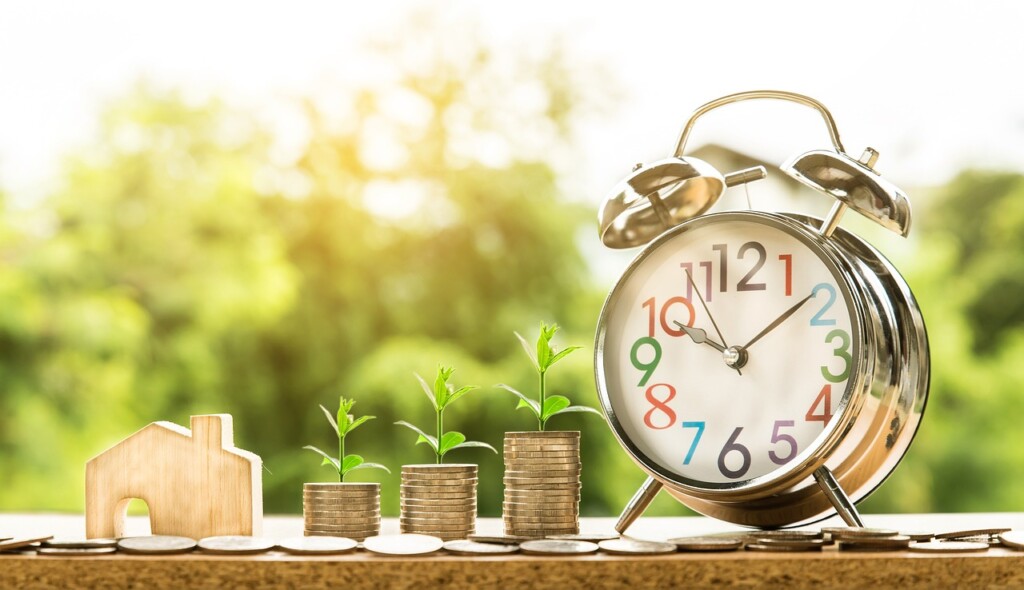
Value engineering (VE) delivers the greatest impact when implemented during the early planning and design phases of a construction project. By integrating VE principles from the start, critical decisions and adjustments can be made without disrupting schedules or incurring substantial additional costs. This aligns with industry best practices, as illustrated by the widely-referenced cost impact graph, which demonstrates how early decisions in a project lifecycle have greater potential for generating savings.
While value engineering techniques can be applied during active construction, this is typically a reactive measure in response to unexpected issues. Unfortunately, VE changes made mid-construction often lead to delays and may compromise the project’s original design intent, underscoring the importance of a proactive VE approach from pre-construction.
The timing and application of value engineering can also vary based on the type of contract structure. For projects with a guaranteed maximum price (GMP) model, VE is an ongoing, iterative process throughout design development and construction. In contrast, in lump sum contracts, most value engineering efforts occur during the competitive bidding phase to optimize the proposal.
Regardless of the contract type, our experience shows that integrating value engineering early in the project workflow provides more flexibility to explore innovative, cost-effective solutions that align with the owner’s vision and budget. Prioritizing VE from day one maximizes opportunities to enhance value while minimizing potential disruptions.
Stage | Description | Potential Cost Impact | Challenges |
---|---|---|---|
Information Gathering | Collection of comprehensive project data | Provides foundation for informed decisions, enabling early cost-effectiveness | Ensuring data accuracy and detail |
Functional Analysis | Identification and assessment of project functions | Substantial cost reduction through prioritized optimization | Balancing quality with reduced cost |
Creative Brainstorming | Generation of alternative solutions | Opens avenues for breakthrough solutions and cost reductions | Cultivating open-minded and creative thinking |
Evaluation | Assessment of proposed ideas for feasibility and value | Identifies most cost-effective solutions | Comprehensive cost-benefit analysis and risk assessment |
Development | Refinement of viable ideas into actionable plans | Detailed planning maximizes potential savings | Addressing technical or logistical challenges |
Implementation and Monitoring | Execution and tracking of approved changes | Ensures realization of predicted value improvements | Maintaining effective communication and adjustments |
What Are the Challenges and Best Practices in Value Engineering?
Value engineering offers significant benefits, but it also comes with challenges that require careful management. As we approach construction projects, we often face the task of balancing cost reduction with quality maintenance, working within tight timelines, overcoming resistance to change, and leveraging specialized expertise. Let’s explore these challenges and the best practices we employ to address them.
Key Challenges in Value Engineering
One of our primary challenges is maintaining quality while reducing costs. We must carefully evaluate every proposed change to ensure it doesn’t compromise the project’s integrity or long-term performance. For example, when considering alternative materials, we analyze not just the upfront savings, but also factors like durability, maintenance requirements, and lifecycle costs.
Time constraints can also pose difficulties. Value engineering is most effective when implemented early in the design process, but project schedules don’t always allow for extensive analysis. We often need to work efficiently to identify and evaluate cost-saving opportunities without delaying the overall project timeline.
Resistance to change from stakeholders is another hurdle we frequently encounter. Designers may be attached to certain aesthetic elements, while owners might be skeptical of deviations from the original plan. Overcoming this resistance requires clear communication and compelling evidence of the benefits of proposed changes.
Lastly, effective value engineering requires specialized knowledge across various construction disciplines. We need to understand not just costs, but also building codes, construction methods, and material properties to make informed recommendations.
Best Practices for Successful Value Engineering
To address these challenges, we’ve developed several best practices that help us maximize the benefits of value engineering:
1. Stay organized with updated budgets and plans: We maintain detailed, up-to-date project documentation to quickly identify areas where value engineering can have the most impact. This organization allows us to respond nimbly to changing project conditions.
2. Consult with specialty contractors: We leverage the expertise of trade specialists to gain insights into potential cost savings and innovative solutions within their specific domains. Their on-the-ground experience often reveals opportunities we might otherwise overlook.
3. Maintain positive relationships with design teams: We foster open, collaborative relationships with architects and engineers. By involving them early in the value engineering process, we can align our cost-saving efforts with their design intent and minimize resistance to changes.
4. Conduct thorough research before presenting alternatives: When proposing changes, we come prepared with comprehensive data on costs, performance, and long-term implications. This thorough approach builds credibility and helps stakeholders make informed decisions.
5. Avoid overwhelming stakeholders with too many options: We carefully curate our value engineering proposals, presenting a focused set of high-impact alternatives rather than an exhaustive list of possibilities. This approach makes decision-making more manageable for project owners and design teams.
By implementing these practices, we strike a careful balance between innovation and practicality. We maintain clear communication channels with all project stakeholders, ensuring that everyone understands the rationale behind proposed changes and their potential impacts.
Value engineering is not without its challenges, but with the right approach, it remains a powerful tool for optimizing project outcomes. By staying organized, leveraging expertise, fostering collaboration, and presenting well-researched alternatives, we can navigate the complexities of construction projects and deliver substantial value to our clients.
Conclusion: Maximizing Project Value Through Strategic Engineering
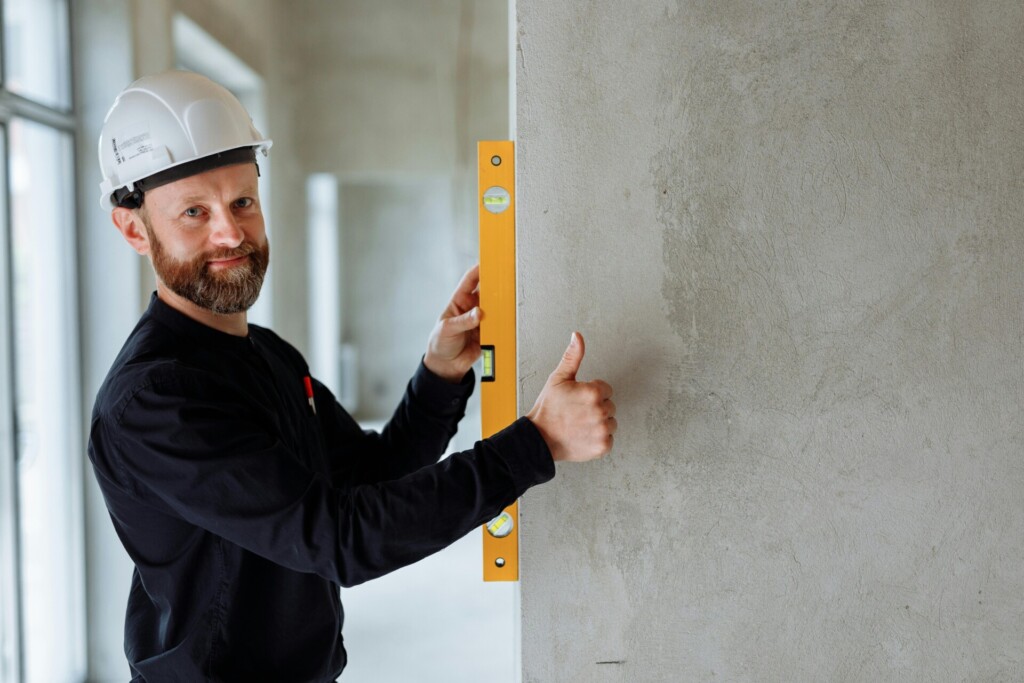
Value engineering in construction serves as a robust approach for enhancing project outcomes through strategic analysis and innovative problem-solving. By systematically evaluating function, cost, and performance, projects can meet or exceed client expectations while improving profitability and efficiency. The most effective value engineering efforts occur early in the project lifecycle, engaging all stakeholders collaboratively and maintaining a focus on long-term value rather than merely reducing costs.
As material procurement challenges and budget constraints continue to affect our industry, mastering value engineering techniques is increasingly crucial for construction professionals aiming to stay competitive and deliver outstanding results. The strategic use of value engineering principles enables us to discover creative solutions, streamline processes, and enhance the value we provide to clients.
Looking ahead, value engineering is expected to play an even more pivotal role as sustainability concerns, technological advancements, and evolving client needs reshape construction practices. By adopting a value-driven mindset and continually refining our approach, we can position ourselves at the forefront of industry innovation and ensure our projects offer enduring value for years to come.
To learn more about how EB3 Construction incorporates value engineering to optimize project outcomes, contact our team today.