At EB3 Construction, we’re observing a noteworthy revival of wood construction within our projects. This resurgence is not just a trend—it’s driven by substantial benefits that meet modern construction demands and environmental responsibilities. Wood surpasses traditional materials like concrete and steel in carbon footprint reduction, with recent industry studies indicating that timber construction can lower carbon emissions by up to 75% compared to conventional methods.
We use wood as a primary building material due to its inherent sustainability as a renewable resource. Unlike many finite construction materials, responsibly harvested timber supports a continuous cycle where replanting ensures a future supply without depleting natural resources. This approach particularly resonates with property developers who face increasing pressure to meet strict environmental standards in their building portfolios.
Technological advancements in engineered wood products have expanded the possibilities on construction sites. Cross-laminated timber (CLT) and laminated veneer lumber (LVL) enable us to construct everything from modest residential developments to multi-story commercial structures with exceptional strength-to-weight ratios. These innovations have effectively addressed historical concerns about wood’s structural limitations, opening new possibilities for architects and developers alike.
What Are the Different Types of Wood Construction Methods?
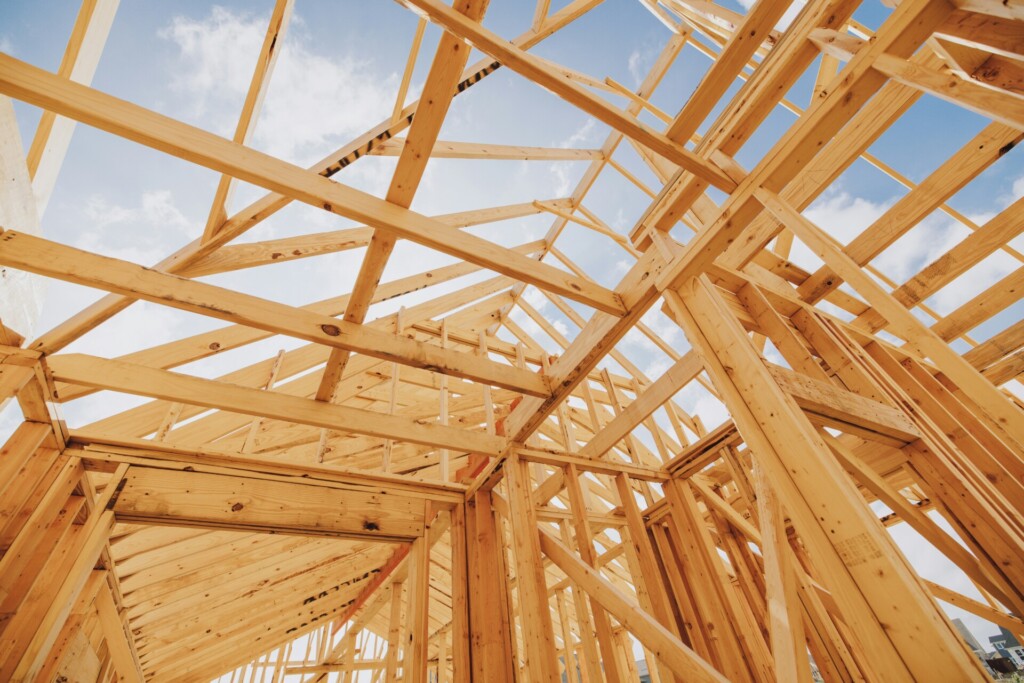
As general contractors, we employ several distinct wood construction methods, each offering unique structural and aesthetic benefits for our clients. Our expertise across traditional and modern techniques allows us to recommend the best approach based on specific project requirements, timeline, and budget considerations.
Traditional Wood Construction Methods
In our commercial and residential projects, we regularly work with time-tested wood construction approaches that have proven reliability over generations. These methods form the foundation of many of our custom builds where authentic craftsmanship is paramount.
Log construction remains one of the oldest techniques we use for certain specialty projects. This method involves horizontally stacking logs that are carefully selected for their dimensional stability and joining them at corners using specialized notching methods. When clients request this method, we source logs that have been properly seasoned to minimize settling issues, which can complicate electrical and plumbing installations.
Timber frame construction is another traditional approach we utilize when structural authenticity is desired. This method features exposed heavy timber beams connected through mortise and tenon joints rather than metal fasteners. We frequently coordinate with specialized timber framers to implement this method since the precision cutting and joinery require expert craftsmanship. The resulting exposed beam structure creates dramatic interior spaces that many property developers find appealing for hospitality and high-end residential applications.
Modern Framing Systems
Light wood framing, commonly referred to as stick framing, forms the backbone of most residential construction projects we manage. This method uses smaller dimensional lumber (typically 2×4 or 2×6 studs) spaced closely together to create structural walls. We then apply plywood or oriented strand board (OSB) sheathing to these frames for rigidity. The efficiency of this system allows us to maintain competitive pricing while delivering quality construction on schedule.
Our construction teams are well-versed in platform framing, a variant of stick framing, where each floor serves as a platform for building the next level. This approach simplifies the construction sequence and allows for better quality control as we progress vertically through the structure. For multi-family and commercial projects, we often employ balloon framing techniques where studs run continuously from foundation to roof, providing enhanced structural continuity.
Advanced Engineered Wood Systems
For clients seeking superior performance and sustainability metrics, we increasingly implement Cross-Laminated Timber (CLT) construction in our projects. This innovative method uses engineered wood panels manufactured by gluing layers of solid lumber boards at right angles to create exceptionally strong structural elements. The dimensional stability and prefabricated nature of CLT panels allow us to accelerate construction schedules while maintaining precise tolerances.
When working with CLT systems, we coordinate closely with suppliers during pre-construction to optimize panel dimensions and connection details, minimizing waste and streamlining installation. The inherent fire resistance and structural integrity of these panels make them particularly well-suited for mid-rise construction projects where conventional framing would be impractical.
Post and beam construction represents a hybrid approach we frequently recommend for projects requiring open floor plans and design flexibility. This method uses widely spaced vertical posts and horizontal beams to create the primary load-bearing structure, eliminating the need for closely spaced studs throughout. Our teams complement these main structural elements with non-load-bearing partition walls, allowing for future reconfiguration of interior spaces – a significant advantage for commercial and institutional clients with evolving space needs.
Construction Method | Complexity | Cost | Typical Applications |
---|---|---|---|
Log Construction | Traditional method using interlocking logs | Moderate to high | Cabins, rustic homes |
Timber Frame Construction | High craftsmanship required | High | High-end residential and commercial spaces |
Light Wood Framing (Stick Framing) | Moderate, uses standard lumber dimensions | Low to moderate | Residential buildings |
Cross-Laminated Timber (CLT) | Advanced, prefabrication involved | High | Multi-story commercial buildings |
Post and Beam Construction | Simpler design provides open spaces | Varies depending on design | Open floor plan structures |
Hybrid and Specialized Construction Methods
Beyond these standard approaches, we regularly execute projects using specialized wood construction methods tailored to specific requirements. Panelized construction systems, where we assemble wall sections off-site under controlled conditions before transporting them to the project location, have proven particularly effective for accelerating schedules during challenging weather conditions.
For properties in high wind or seismic zones, we implement advanced shear wall systems with engineered wood products and specialized fastening schedules to enhance lateral resistance. These technical considerations are vital to long-term structural performance and represent an area where our experience provides significant value to property developers and owners.
The modular timber construction method represents another innovation we’ve successfully implemented on tight-timeline projects. This approach involves constructing entire room modules off-site—complete with finishes, fixtures, and even mechanical systems—before delivering and connecting them on the building foundation. The controlled manufacturing environment results in exceptional quality control while dramatically reducing on-site construction time.
When evaluating which wood construction method best suits a particular project, we conduct comprehensive analyses of structural requirements, architectural vision, sustainability goals, and budget constraints. This consultative approach ensures that our clients receive solutions optimally aligned with their project objectives and long-term performance expectations.
How Do Hardwoods and Softwoods Differ in Construction Applications?
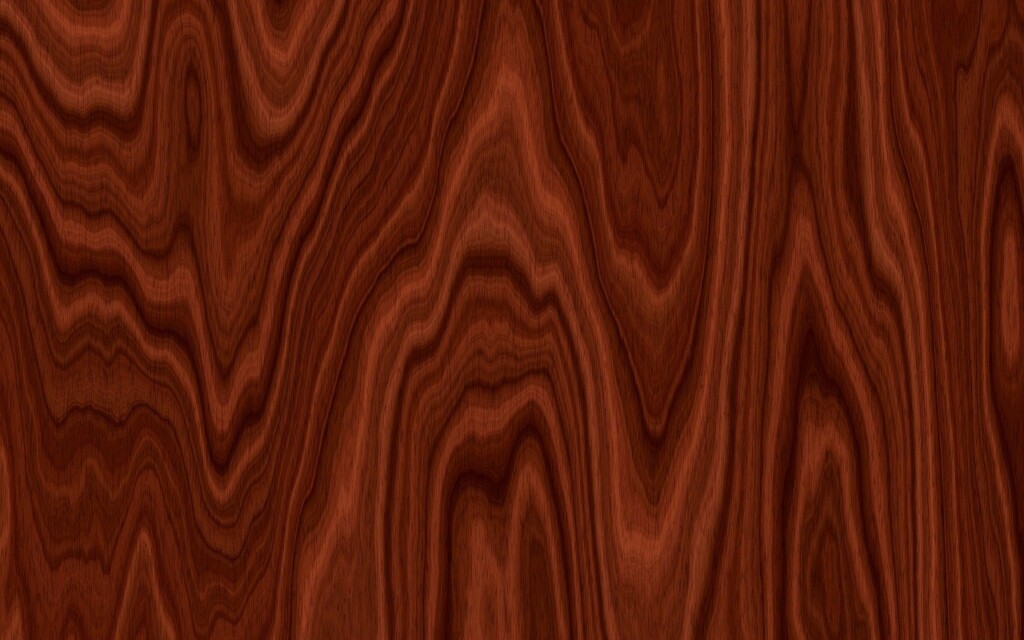
When selecting materials for construction projects, understanding the fundamental differences between hardwoods and softwoods helps us make strategic decisions that impact everything from structural integrity to aesthetic finish. These two wood categories bring distinct properties to the construction site, directly influencing how we use them.
Biological Origins and Growth Patterns
The distinction between hardwoods and softwoods starts at the source. Hardwoods come from deciduous, broad-leaved trees that shed annually, while softwoods originate from coniferous, needle-bearing evergreens. This biological difference creates varying growth patterns that affect availability and cost. Hardwoods like oak and maple can take up to 150 years to mature fully, creating naturally limited supply. In contrast, softwoods like pine and fir reach harvest maturity in about 40 years, allowing for more sustainable production cycles.
This growth difference directly impacts our material planning timelines. When projects require specific hardwood species, we need to account for potential sourcing delays, especially during high demand in the construction market. The 2021 lumber shortage was a stark reminder of how growth cycles and supply chain issues can dramatically affect building schedules.
Physical Properties and Structural Applications
In framing and structural work, the density differences between these wood types guide our engineering decisions. Hardwoods generally feature a more complex cellular structure with visible pores, creating that distinctive heavy grain and superior density. This translates to excellent compressive strength, making hardwoods like oak ideal for load-bearing elements in high-stress applications.
Softwoods like pine and spruce offer different advantages in structural applications. Their lighter weight significantly reduces dead load in wall assemblies and roof systems while still providing adequate strength for most residential and light commercial construction. When designing timber-framed structures, this weight consideration becomes crucial for foundation specifications and seismic performance.
Practical Applications in Our Projects
We consistently use softwoods for framing, sheathing, and general structural components where their workability shines. These woods accept fasteners readily without splitting, cut cleanly with minimal dulling of tools, and can be modified on-site as needed. Southern yellow pine, for example, performs exceptionally well for roof trusses, while spruce-pine-fir (SPF) remains our go-to for wall framing due to its dimensional stability.
For finished elements and specialty applications, we turn to hardwoods. We install oak and maple flooring in high-traffic commercial spaces where durability is paramount. Cherry and walnut appear in custom millwork, cabinetry, and architectural details when clients want both structural integrity and visual distinction. The natural resistance of certain hardwoods to rot and insects makes them suitable for exterior applications like decking and siding, though properly treated softwoods can serve these purposes at a lower price point.
Durability and Weathering Considerations
Weather exposure demands careful wood selection. In exterior applications, certain hardwoods demonstrate remarkable natural resistance to decay. Ipe and teak contain natural oils and resins that ward off moisture and pests, making them excellent choices for decking and outdoor structures despite their premium cost.
On the softwood side, cedar and redwood stand out for their natural durability in exterior settings. We often specify Western Red Cedar for cladding projects because of its dimensional stability and inherent resistance to decay, even in challenging weather conditions. When budget constraints exist, pressure-treated pine provides a cost-effective alternative for exterior structural elements, though it typically requires more maintenance over time.
Cost and Budget Implications
The cost differential between hardwoods and softwoods significantly impacts our project budgeting. Premium hardwoods can cost three to five times more than construction-grade softwoods for the same volume of material. This reality often guides our material recommendations, particularly in projects with tight budget constraints.
We’ve found that strategic use of both wood types often yields the best results. Using softwoods for structural components where they will be concealed and reserving hardwoods for visible elements allows us to maximize value while maintaining quality. This hybrid approach has become increasingly important as lumber prices fluctuate in response to market conditions and supply chain challenges.
Workability and Installation Considerations
The density difference between hardwoods and softwoods directly affects how we work with them on site. Softwoods generally cut, drill, and nail with less resistance, reducing labor time and tool wear. This makes them particularly valuable in framing applications where numerous cuts and connections must be made quickly.
Hardwoods require more powerful tools, sharper blades, and often pre-drilling for fasteners to prevent splitting. While this increases installation time, the superior holding power for screws and nails often results in more secure connections. When installing hardwood flooring or crafting built-ins, we factor this additional labor time into our scheduling.
Wood Type | Density | Compressive Strength | Typical Applications | Cost |
---|---|---|---|---|
Pine | 410 kg/m³ | 4,800 PSI | Frames, Flooring | Moderate |
Oak | 700 kg/m³ | 13,800 PSI | Furniture, Cabinetry | High |
Spruce | 450 kg/m³ | 5,100 PSI | Indoor framing | Low |
Cedar | 380 kg/m³ | 6,500 PSI | Siding, Outdoor Projects | Moderate |
Teak | 650 kg/m³ | 10,000 PSI | Outdoor furniture, Marine | Very High |
Finishing Characteristics
The finishing requirements for these wood types diverge significantly. Softwoods like pine tend to absorb stains unevenly due to varying densities between early and latewood within their growth rings. To achieve consistent results, we often apply pre-stain conditioners to softwoods before finishing.
Hardwoods generally accept finishes more predictably, though their dense structure sometimes requires additional sanding between coats. The pronounced grain patterns in hardwoods like oak and ash create distinctive visual interest when finished, while softwoods like pine offer a more subdued appearance. These aesthetic differences guide our recommendations for exposed wood elements in both residential and commercial projects.
Through years of construction experience, we’ve learned that neither wood category is universally superior—each has specific applications where it excels. By understanding these differences, we select the right material for each component of our construction projects, balancing performance requirements with budget considerations and design objectives.
What Are Engineered Wood Products and Their Benefits?
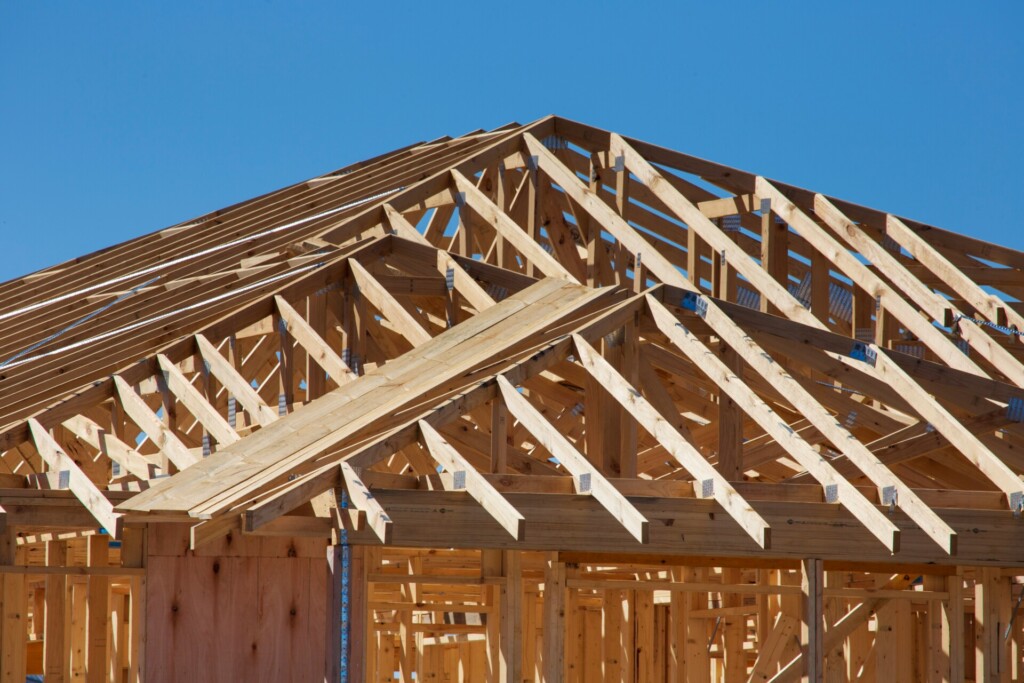
In tackling complex construction projects, traditional lumber can at times fall short of meeting modern building standards. Engineered wood products step in to meet these demands effectively. Manufactured by bonding wood strands, veneers, or fibers through controlled processes using heat and pressure, they offer remarkable performance characteristics while preserving the natural aesthetics of wood.
Types of Engineered Wood Products
Various engineered wood products are employed in construction projects, each with unique properties for specific applications. Laminated Veneer Lumber (LVL) consists of multiple layers of thin wood veneers bonded with the grain running parallel, creating structural members with exceptional strength. LVL is often specified for load-bearing beams and headers where traditional lumber would require larger dimensions.
I-joists represent another versatile engineered solution, routinely incorporated into floor and roof systems. These structural members feature flanges typically made from LVL or solid lumber connected by a vertical web of oriented strand board (OSB). Their distinctive ‘I’ shape maximizes structural efficiency while reducing weight, enabling longer spans with less material.
Cross-Laminated Timber (CLT) has transformed approaches to larger commercial and multi-family projects. These large wooden panels consist of multiple layers of dimensional lumber arranged perpendicular to each other and bonded with structural adhesives. The cross-lamination technique distributes loads in both directions, creating strong panels that can replace concrete in many applications.
Glue-laminated timber (glulam) represents yet another valuable component of our engineered wood arsenal, consisting of individual wood laminations bonded together to form large structural members. Unlike LVL, glulam can be manufactured in curved shapes, offering design flexibility for architectural features like arches and exposed beams.
Performance Advantages Over Traditional Lumber
The benefits of engineered wood products extend beyond their innovative manufacturing processes. These materials consistently outperform traditional lumber in several key ways. Their superior strength-to-weight ratio allows the spanning of greater distances without intermediate support columns, creating more open and flexible interior spaces.
Dimensional stability is another major advantage. While conventional lumber tends to warp, twist, and shrink with moisture content changes, engineered wood products maintain their shape and structural integrity over time. This results in straighter walls, flatter floors, and fewer warranty headaches like nail pops or drywall cracks.
The resistance to warping and splitting makes engineered wood especially valuable in challenging environmental conditions. These products remain stable in areas with significant humidity fluctuations throughout seasonal changes, allowing for tight construction tolerances to be met and maintained over the building’s lifetime.
Environmental and Resource Efficiency
In addition to their structural advantages, engineered wood products support resource-efficient construction practices. Their manufacturing process maximizes yield from raw timber by using younger, more abundant trees instead of relying on old-growth forests. This allows for 30-50% more usable material from the same timber harvest compared to traditional milling processes.
The ability to create larger structural elements from smaller wood components is a sustainable approach to timber resource management. Engineered wood allows the use of fast-growing plantation timber, achieving superior structural performance without the need for large-dimension old-growth trees. This supports responsible forestry practices that help maintain healthy forest ecosystems.
Controlled manufacturing environments ensure consistent quality and predictable performance. Unlike natural wood, which varies based on growth conditions and species characteristics, engineered wood offers uniform properties throughout each structural member. This consistency enables more precise engineering calculations and optimized material usage.
Engineered Wood Product | Characteristics | Common Applications |
---|---|---|
Plywood | Made by bonding layers of wood veneers | Furniture, flooring, wall panels |
Medium-Density Fiberboard (MDF) | Smooth, easy to work with | Cabinetry, furniture, paneling |
Particleboard | Made from wood chips and resin | Low-cost furniture, cabinetry |
Oriented Strand Board (OSB) | Strong, wood strands arranged in layers | Roofing, wall sheathing, flooring |
Laminated Veneer Lumber (LVL) | Thin wood veneers bonded together | Load-bearing beams and headers |
I-Joists | Typically LVL or lumber flanges with OSB web | Floor and roof joists |
Design Flexibility and Construction Efficiency
Engineered wood products significantly expand design possibilities while streamlining the construction process. Custom sizes and lengths can be created, optimizing each structural member for its application rather than being limited by standard lumber dimensions, reducing material waste, and improving structural efficiency.
The lightweight nature of many engineered wood products, particularly I-joists, simplifies handling and installation on-site. Crews can maneuver these materials without heavy equipment, reducing labor costs and improving safety. Precision manufacturing means fewer field adjustments, allowing for faster assembly and tighter construction schedules.
Crucially, engineered wood enables architectural expression difficult or impossible with conventional lumber. From dramatic curved glulam beams to massive exposed CLT panels, these materials enable striking design features while maintaining structural integrity. This blend of form and function has made engineered wood increasingly popular in signature commercial and institutional projects where structure becomes part of the architectural statement.
Incorporating engineered wood products, we deliver buildings that merge modern performance standards with the warmth and character of natural wood. As these materials evolve, we remain committed to leveraging their benefits to create exceptional spaces.
What Makes Mass Timber Construction Revolutionary?
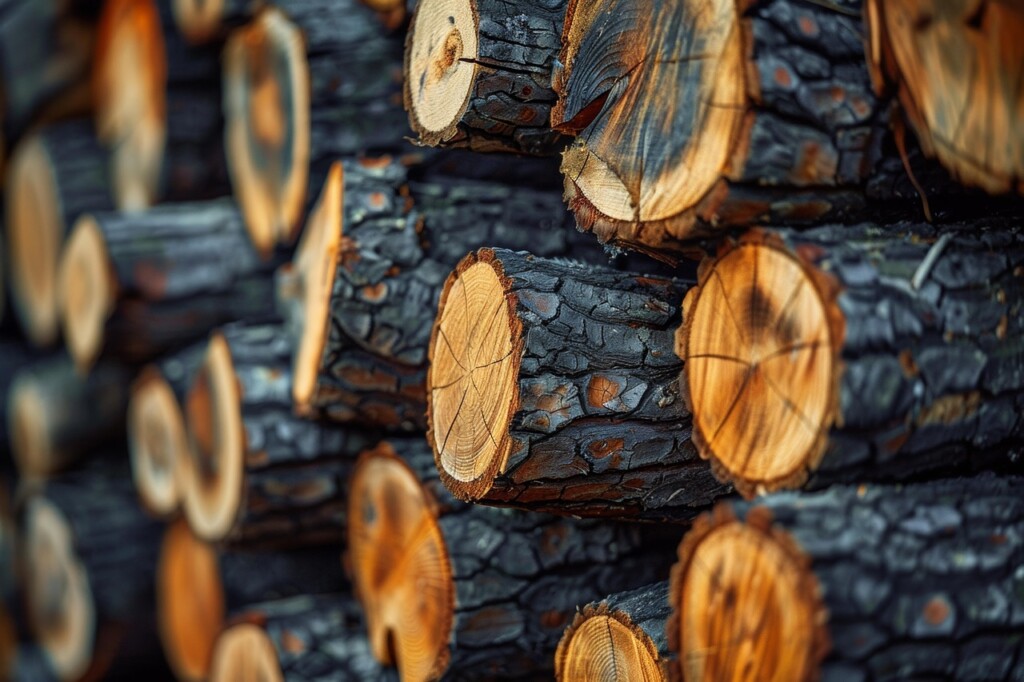
When undertaking a new construction project with mass timber, we employ a fundamentally different building methodology than traditional approaches. Instead of assembling smaller wooden components on-site, we use substantial engineered wood elements that arrive precisely manufactured and ready for assembly. This factory-based prefabrication signifies a major shift in how timber construction projects are planned and executed.
Advanced Manufacturing and Assembly
The process begins in the manufacturing facility, where large wood panels and structural components are created through techniques like cross-lamination or glue-lamination. These components arrive at the job site cut to exact specifications with predetermined connection points. This precision eliminates many variables that typically slow down traditional construction, allowing crews to work with remarkable efficiency.
Once materials reach the site, the assembly process progresses quickly. With proper planning and coordination, structural elements can be erected about 25% faster than comparable steel or concrete structures. This acceleration not only saves time but also reduces labor costs, minimizes site disruption, and allows for earlier project completion and occupancy.
Innovative Structural Systems
As general contractors, we employ several distinct mass timber structural approaches based on project requirements. Platform systems allow the construction of each floor as a complete horizontal plane before adding the next level. For taller structures, balloon systems are used, where vertical timbers span multiple stories with floors attached to these continuous supports. Panel wall systems use solid timber walls as load-bearing elements, while post and beam configurations create expansive, column-free interior spaces offering maximum flexibility.
These structural systems provide tremendous versatility. The University of Arkansas showcased this potential with America’s largest mass timber building—a 202,027-square-foot structure demonstrating the material’s capacity to support significant scale and complexity. We now see mass timber used in projects once unimaginable for wood construction a decade ago.
Engineering and Performance Benefits
Specifying mass timber for a project means choosing a material with an impressive strength-to-weight ratio. Engineered wood products can rival or exceed the structural performance of concrete and steel in many applications while weighing significantly less. This reduced weight means smaller foundation requirements and potentially lower seismic loads, leading to cost savings throughout the project.
Beyond structural advantages, mass timber creates spaces with unique character. Exposed wood surfaces bring warmth and natural texture that resonate with occupants. When clients visit our mass timber projects, they immediately notice the difference—a biophilic connection absent in conventional commercial construction. This aesthetic quality adds significant value, particularly for developers focused on creating premium environments for tenants or residents.
Mass timber construction’s revolutionary nature lies in its combination of ancient building materials with cutting-edge manufacturing and engineering to create a system meeting modern efficiency, sustainability, and performance demands. As more building codes recognize and accommodate these systems, we expect to see mass timber continue its trajectory from a novel alternative to a mainstream construction method.
Conclusion: The Future of Wood in Modern Construction
The construction industry stands at a crucial juncture where tradition intersects with innovation. Wood construction has transformed significantly, evolving from traditional uses to advanced building solutions that meet current sustainability needs. Advancements in engineered wood products have changed how we approach structural design, allowing us to build taller, stronger, and more efficiently than before.
Wood is particularly valuable in today’s construction environment due to its environmental benefits. Unlike steel or concrete, wood stores carbon throughout its lifecycle, retaining the carbon absorbed during tree growth even when used in buildings. Our projects increasingly utilize this natural advantage, with many clients specifically requesting wood for its sustainability benefits, warm aesthetics, and positive impact on occupant well-being. As we continue refining prefabrication techniques and expanding the applications of mass timber, the versatility and performance of wood construction are set to grow, providing developers with cost-effective solutions that meet environmental and regulatory demands.
Contact EB3 Construction to explore how wood construction can benefit your next project.