Construction risk management involves a systematic approach to identifying potential threats, analyzing their likelihood and impact, and implementing practical controls to mitigate their effects.
According to the Bureau of Labor Statistics, approximately 150,000 construction site incidents occur annually in the United States, highlighting why we prioritize comprehensive risk planning from project inception through completion. This proactive stance helps us navigate Texas’s unique regulatory environment while addressing safety concerns, financial exposures, and scheduling challenges.
For property developers and owners, effective risk management directly impacts your bottom line. By implementing robust safety protocols and contingency planning, we not only protect workers but also safeguard your timeline, budget, and ultimately, your project’s success.
At EB3, our approach integrates Texas-specific considerations with industry best practices, creating a framework that anticipates challenges before they become costly problems requiring remediation.
What Are the Key Steps in the Construction Risk Management Process?
Managing risk on construction projects isn’t just good practice—it’s essential for project success and protecting both our teams and our clients’ investments. At EB3 Construction, we’ve refined our approach to risk management through years of practical experience on Texas jobsites, following a structured yet flexible framework that adapts to each project’s unique challenges.
Identifying Potential Risks
The foundation of effective risk management begins with comprehensive risk identification during the preconstruction phase. We systematically catalog potential threats across financial, safety, operational, and environmental categories, leaving no stone unturned.
Our risk identification process incorporates multiple perspectives, bringing together estimators, project managers, superintendents, and subcontractors to leverage their collective experience. This collaborative approach helps uncover risks that might otherwise remain hidden until they emerge as expensive problems during construction.
For Texas projects specifically, we pay close attention to weather-related risks like sudden thunderstorms, hurricane impacts along coastal areas, and extreme heat conditions that can affect worker safety and material installation. Our teams document these risks in a centralized system, ensuring nothing slips through the cracks.
Assessing Impact and Likelihood
Once we’ve identified potential risks, we evaluate each one based on two critical factors: the probability of occurrence and the potential severity of impact. This dual assessment helps us prioritize where to focus our mitigation efforts first.
For quantifiable risks, we assign numeric values to create a risk assessment matrix that visually maps the significance of each threat. High-impact, high-probability risks immediately move to the top of our priority list, while lower-tier risks remain on our radar but receive proportionate attention.
Historical data plays a crucial role in this phase. When evaluating a hospital construction project, for instance, we analyze performance, safety, and financial reports from similar past projects to improve the accuracy of our risk assessment. This data-driven approach replaces gut feeling with measurable insights.
Implementing Control Measures
Once risks are identified and assessed, we develop and implement specific control measures tailored to each situation. Our approach considers four possible responses: accepting manageable risks, avoiding unacceptable ones, implementing controls to reduce likelihood or impact, or transferring risk through subcontracts or insurance.
For safety risks, we institute rigorous protocols including daily toolbox talks, regular safety inspections, and ongoing training programs. These measures have demonstrably reduced incident rates on our jobsites, protecting both our workforce and our schedule commitments.
For financial risks, we implement strategic measures like progress billing, careful cash flow management, and protecting lien rights with higher-risk clients. These approaches maintain project liquidity while safeguarding against potential payment disruptions that could derail construction progress.
Supply chain disruptions represent another critical risk area, especially in today’s volatile market. We mitigate these by diversifying suppliers, pre-purchasing critical materials when feasible, and maintaining strong relationships with multiple vendors to ensure consistent material availability.
Monitoring and Reviewing Controls
The final—and ongoing—step in our risk management process involves continuous monitoring and regular review of our control measures. This vigilant approach ensures that our risk mitigation strategies remain effective throughout the project lifecycle.
Weekly project meetings include dedicated time for risk review, where teams report on existing risk controls and identify emerging concerns. This regular cadence keeps risk management at the forefront rather than treating it as a one-time exercise at project kickoff.
When losses do occur, we document them thoroughly and analyze root causes. This post-incident examination informs improvements to our risk management approach, creating an iterative cycle of continuous improvement. Each project ultimately strengthens our risk management capabilities for the next one.
Technology plays an increasingly important role in this monitoring phase. Real-time project management platforms help us track risk indicators, while digital safety reporting tools allow immediate notification of incidents or near-misses that might signal control failures.
Practical Applications on Texas Construction Sites
Our systematic risk management approach delivers tangible benefits on Texas construction sites. For example, when facing potential weather disruptions during concrete pours, we develop contingency plans that include temporary shelters, standby pumping equipment, and flexible scheduling windows to ensure quality completion despite challenging conditions.
For projects with complex regulatory compliance requirements—particularly common in healthcare and government construction—we implement specialized tracking systems to monitor permitting milestones and inspection requirements, preventing costly compliance-related delays.
On multi-phase developments, we conduct risk transfer analysis to determine optimal insurance coverage, balancing premium costs against potential exposure. This calculated approach maximizes protection while maintaining cost-effectiveness for both our company and our clients.
By faithfully executing each step of this risk management process, we transform unpredictable threats into manageable challenges, creating more reliable outcomes for our clients and protecting our own operational sustainability.
What Safety Management Practices Are Essential for Texas Construction Sites?
Managing safety on Texas construction sites involves more than just meeting regulatory requirements—it requires a comprehensive approach that protects workers while ensuring project continuity.
We’ve seen firsthand how robust safety protocols not only prevent injuries but also lay the foundation for project success. The construction boom across Dallas, Houston, and Austin has heightened the need for stringent safety practices tailored to Texas’s unique environment and regulatory landscape.
Personal Protective Equipment Requirements
We begin every project by ensuring proper PPE compliance. Hard hats, safety glasses, high-visibility clothing, and appropriate footwear form the frontline defense against common construction hazards. For specialized work like concrete pours during Texas summers, we implement additional measures including cooling vests and scheduled hydration breaks to prevent heat-related illness.
Beyond standard protection, we assess task-specific PPE requirements daily. When coordinating steel erection in San Antonio last year, we implemented specialized fall protection protocols that exceeded OSHA’s minimum standards, recognizing that Texas’s high winds created additional risks for our ironworkers.
Each worker receives their equipment during orientation with clear instructions on proper usage and maintenance. This investment in quality PPE has proven invaluable—during a recent project near the Gulf Coast, our team’s proper eye protection prevented several potential eye injuries when an unexpected dust storm swept through the worksite.
Texas-Specific Regulatory Compliance
While OSHA regulations provide the foundation for construction safety, we navigate additional Texas-specific requirements that often have different enforcement mechanisms and priorities. Understanding these nuances allows us to develop more effective site-specific safety plans that satisfy both federal and state requirements.
Our safety coordinators maintain current knowledge of Texas construction regulations through ongoing education and industry partnerships. This proactive approach helped us identify and address potential compliance issues on a recent multifamily project in Austin before they became problems during inspection.
Documentation plays a critical role in our regulatory compliance strategy. We maintain comprehensive records of safety meetings, training certifications, and incident reports—all organized to demonstrate compliance during OSHA inspections. When the Occupational Safety and Health Administration conducted 24,000 inspections nationwide in 2023 with fines totaling over $75 million for violations, our sites were consistently prepared with proper documentation.
Violation | Details | Prevention Strategy |
---|---|---|
Fall Protection | Most common OSHA violation in Texas construction sites. | Implement comprehensive fall protection systems. |
Scaffolding | Inadequate scaffolding practices leading to collapses. | Ensure scaffolding is properly erected with reinforced joints and stable bases. |
Hazard Communication | Failures in hazard communication standards. | Maintain clear labeling and documentation of hazardous materials. |
Ladder Safety | Unsafe use of ladders causing falls. | Follow regulations for safe ladder use and conduct regular inspections. |
Personal Protective Equipment (PPE) | Non-compliance with PPE requirements. | Ensure proper PPE is available and used by all workers. |
Safety Training and Communication
Regular safety training forms the cornerstone of our risk management approach. New workers complete a comprehensive orientation before stepping onto the jobsite, covering general safety protocols and site-specific hazards. This initial training is reinforced through weekly toolbox talks that address current site conditions and emerging concerns.
Open communication channels between workers and management have prevented numerous potential incidents. When a team member on our Dallas commercial project identified unstable scaffolding, the immediate reporting and swift corrective action prevented what could have become a serious accident. This culture of speaking up about safety concerns creates a protective environment where everyone takes responsibility for site safety.
Hazard Identification and Risk Management
Proactive hazard identification requires a systematic approach. We conduct comprehensive site assessments before breaking ground, identifying potential risks associated with the specific environment, task requirements, and equipment needs. Daily job hazard analyses before each shift help us address changing conditions and evolving risks.
Our risk management strategy employs a hierarchy of controls, prioritizing the elimination of hazards when possible, followed by engineering controls, administrative measures, and finally PPE when other methods can’t fully mitigate risks. For excavation work—particularly challenging in Texas’s varied soil conditions—we implement extensive shoring and daily trench inspections to prevent collapses.
Incident reporting and investigation procedures provide valuable learning opportunities. When a near-miss occurred during crane operation at our Houston industrial site, the thorough investigation allowed us to identify and address a mechanical issue before it caused an accident. These lessons become part of our continuous improvement process, strengthening our safety protocols with each project.
Emergency Preparedness and Response
Texas construction sites face unique emergency risks, from severe thunderstorms and flash floods to extreme heat events. Our emergency response plans account for these regional hazards with clearly defined evacuation routes, shelter locations, and communication protocols.
Each project includes designated emergency response team members trained in first aid, CPR, and basic disaster response. Emergency equipment—including first aid kits, AEDs, and emergency communication devices—is strategically positioned throughout our sites for immediate access when needed.
Regular emergency drills ensure everyone knows their responsibilities during a crisis. Following a severe storm warning near our Austin project last summer, our team executed the emergency protocol flawlessly, securing loose materials and moving personnel to designated shelter areas within minutes—this preparation prevented injuries and minimized property damage when the storm hit.
How Do Texas Construction Companies Manage Financial Risks?
The Lone Star State’s construction sector faces unique challenges—from sudden material price spikes following Gulf Coast hurricanes to labor shortages in rapidly growing metropolitan areas like Austin and Dallas-Fort Worth.
These regional factors demand specialized risk management strategies beyond standard industry practices.
Identifying Financial Risks in Texas Construction
Before implementing mitigation strategies, we conduct thorough risk assessments to identify potential financial threats. Our process begins with categorizing risks specific to Texas projects: market fluctuations, credit exposure, operational inefficiencies, and liquidity challenges. This classification allows us to develop targeted responses rather than applying one-size-fits-all solutions.
The construction boom across Texas cities creates both opportunities and risks. With Austin permitting new commercial construction at record rates and the DFW metroplex expanding rapidly, we’re seeing intensified competition for materials and labor that drives cost volatility. This market-specific condition requires constant vigilance and adaptive financial strategies.
Weather-related risks also play a significant role in our financial planning. Texas’s unpredictable climate—from flooding along the coast to drought conditions in western regions—can trigger substantial project delays and unplanned expenses. We build weather contingencies into our financial models, particularly during hurricane season when material supply chains often face disruption.
Financial Risk Category | Mitigation Strategy |
---|---|
Budget Overruns | Implementing controls like progress billing and careful cash flow management |
Unexpected Costs | Creating contingency budgets and conducting thorough risk assessments |
Fluctuating Material Prices | Strategic procurement timing and early procurement |
Market Volatility | Securing comprehensive insurance and contractual risk allocation |
Proactive Risk Management Strategies
We implement a five-step risk management process that serves as our foundation: identification, assessment, mitigation, monitoring, and review. This systematic approach enables us to address financial threats before they impact project timelines or budgets. Rather than reactive crisis management, we prioritize preventive measures that maintain project momentum.
Insurance coverage forms our first line of defense. We secure comprehensive builders risk policies tailored to Texas construction requirements, covering potential losses from unforeseen circumstances like property damage and natural disasters. These policies typically include coverage for cleanup, debris removal, and material replacements—essential protections in Texas’s severe weather environment.
Contractual risk allocation represents another critical strategy for Texas contractors. We negotiate clauses that fairly distribute financial risks between project stakeholders while protecting our interests. Price escalation provisions have become particularly important during recent material cost volatility, allowing for adjustments when material costs exceed predetermined thresholds.
Material Price Fluctuation Management
Material cost volatility presents one of the most significant financial risks in Texas construction. We employ several approaches to mitigate these fluctuations, beginning with strategic procurement timing. By analyzing market trends and maintaining relationships with multiple suppliers, we can optimize purchasing decisions and secure favorable pricing.
Early procurement represents another effective strategy when feasible. For materials with projected price increases, we may purchase and securely store items ahead of schedule, locking in current rates. This approach requires additional storage considerations but often yields substantial cost savings on large-scale projects.
We also incorporate contingency budgeting specifically for material price fluctuations. Instead of generic project contingencies, we allocate funds directly tied to materials with historically volatile pricing. This targeted approach ensures we have financial resources available precisely where market uncertainties may impact our projects.
Cash Flow and Liquidity Management
Maintaining positive cash flow remains essential to our financial stability. We implement rigorous cash flow forecasting that accounts for Texas’s construction payment practices and typical project timelines. These projections help us anticipate potential liquidity challenges and adjust our financial strategy accordingly.
Effective billing and collection procedures form the cornerstone of our cash flow management. We establish clear payment terms with clients and maintain consistent invoicing schedules. When payment delays occur—particularly common in multi-tier projects—we have established protocols for follow-up and resolution to minimize impacts on our operational liquidity.
Credit risk assessment also plays a vital role in our financial management approach. Before committing to new projects, we evaluate the financial stability of project owners and general contractors. This due diligence helps us avoid payment issues that could compromise our cash position and overall financial health.
Technology in Financial Risk Management
Technology integration enhances our financial risk management capabilities. Construction management software provides real-time data on project expenses, allowing us to identify potential budget variances early and implement corrective measures. These digital tools have transformed how we monitor financial performance across multiple Texas projects simultaneously.
Data analytics capabilities enable us to leverage historical project information for more accurate risk assessment. By analyzing past performance data from similar Texas projects, we can better anticipate financial risks and develop more effective mitigation strategies for current and future work.
Loss Recovery Strategies
Despite our best prevention efforts, financial losses occasionally occur. When they do, we implement structured recovery approaches to minimize their impact. Our insurance claims process begins immediately following covered incidents, with thorough documentation to support timely claim resolution.
We understand Texas mechanics lien laws and utilize them when necessary to secure payment for completed work. This legal tool provides leverage in payment disputes and helps protect our financial interests when traditional collection methods prove insufficient.
For persistent payment issues, we may pursue collections or legal action as a final resort. While we prefer collaborative resolution, we maintain relationships with construction law specialists who understand Texas’s unique legal landscape and can effectively advocate for our financial interests when required.
What Tools and Technologies Support Risk Management in Texas Construction?
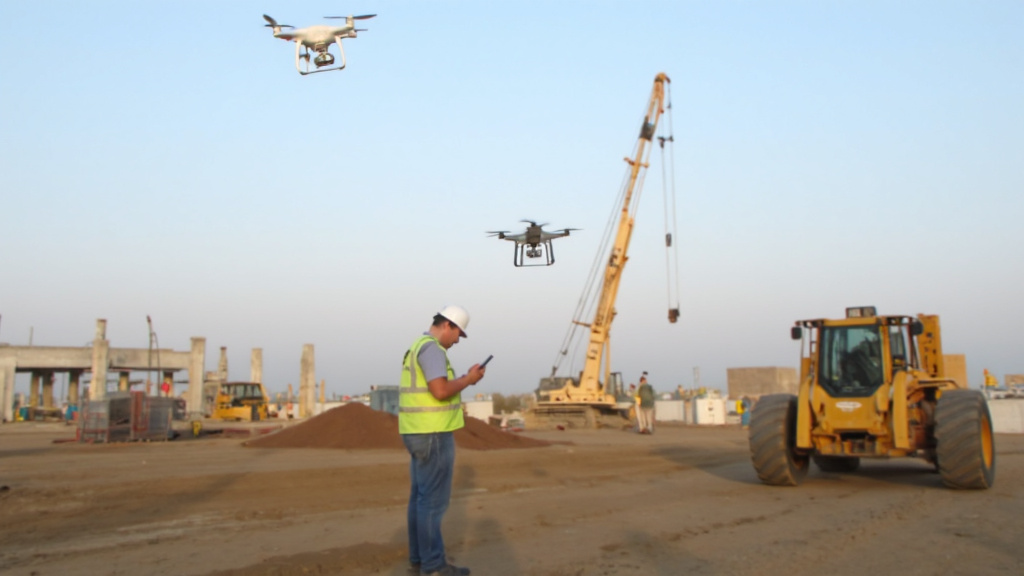
The construction landscape across Texas is changing as we integrate advanced technological solutions into our risk management framework. With over $535 billion in planned construction projects throughout the state, our teams now leverage specialized digital tools that significantly improve our ability to identify, monitor, and mitigate potential hazards before they impact project timelines or budgets.
Real-Time Monitoring Systems
Our project teams have moved beyond clipboards and manual reporting. We now deploy comprehensive monitoring systems that provide instant visibility into site conditions and progress. GPS-enabled equipment tracking allows us to monitor high-value assets, while drone technology gives us unprecedented aerial perspectives during regular site inspections.
These monitoring capabilities deliver three critical advantages in our risk management approach. First, we receive immediate updates on project status without physical site visits. Second, we can identify potential delays or plan deviations at their earliest stages. Third, we maintain enhanced accuracy in work progress tracking—critical for managing financial risk on complex projects.
Following the intense material shortages Texas contractors faced during the pandemic recovery, these monitoring tools have become particularly valuable. We now track supply chain vulnerabilities and material deliveries with precision, allowing us to adjust schedules before bottlenecks create cascading delays.
Construction Management Software and ERP Systems
At the core of our risk management strategy lies robust construction management software. We utilize enterprise resource planning (ERP) systems that function as a single source of truth across diverse project teams. These platforms centralize data collection, enabling us to identify, monitor, and report on risks in real-time with unprecedented accuracy.
Our implementation of these systems has transformed how we manage financial risk in particular. By automating critical processes and improving cross-team collaboration, we significantly reduce errors that once plagued manual systems. The enhanced decision-making capabilities and timely reporting ensure we stay ahead of potential issues before they impact project outcomes.
Construction-specific software applications also help us create detailed risk management plans with defined responsibilities and procedures for addressing potential concerns. This collaborative approach fosters shared responsibility among stakeholders and strengthens our overall risk mitigation strategy.
Building Information Modeling (BIM)
BIM technology represents perhaps the most significant advance in construction risk management. We utilize these powerful 3D digital representations during the pre-construction phase to conduct virtual walkthroughs, identify potential design conflicts, and visualize complex structural components before placing a single concrete form.
The risk reduction benefits we gain through BIM include substantially fewer design errors and clashes, improved cross-discipline collaboration, and enhanced visual insights for stakeholder communication. On complex projects, we’ve reduced costly rework by as much as 10% of planned project time through early detection of issues in the digital environment—a significant advantage when managing tight margins and strict timelines.
For Texas developers facing increasingly stringent building code requirements, our BIM implementation also facilitates code compliance checks during design stages, eliminating potentially costly violations that might otherwise emerge during inspections.
Advanced Analytics and Predictive Modeling
Our risk management toolkit now includes sophisticated data analytics platforms that analyze historical project information to predict potential hazards before they materialize. These predictive modeling tools help us prepare for challenges by identifying patterns across similar projects and regional conditions specific to Texas construction environments.
We apply these analytical capabilities across several key risk areas. We forecast potential budget overruns based on past performance data, identify safety hazards through pattern recognition, and optimize resource allocation to minimize schedule delays. With construction labor shortages continuing to challenge Texas contractors, these predictive tools help us manage workforce requirements with greater precision.
AI-driven analytics also assist our teams in monitoring weather patterns to forecast potential disruptions from storms or extreme conditions—a particularly valuable capability given Texas’ susceptibility to severe weather events that can derail outdoor construction activities.
Safety Technology and Wearables
Worker safety remains our paramount concern, especially as OSHA reporting shows that construction-related fatalities in Texas continue to exceed national averages. We’ve responded by implementing comprehensive safety technology solutions that transform how we protect our teams on site.
Smart helmets and wearable devices now monitor worker health metrics and track movements in real-time. These devices can immediately detect falls or exposure to hazardous conditions, triggering immediate alerts to safety personnel. With Texas construction sites often experiencing extreme summer temperatures, these monitoring capabilities provide crucial protection against heat-related illnesses.
Our safety protocols now incorporate IoT sensors embedded throughout job sites to monitor environmental conditions, equipment operation, and structural stability. This networked approach to safety monitoring creates a far more comprehensive risk management environment than traditional observation-based methods could achieve.
Conclusion: Strengthening Construction Risk Management in Texas
The construction landscape in Texas requires vigilance and foresight. We’ve seen how structured risk management can transform chaotic situations into manageable processes. By systematically identifying, assessing, controlling, and reviewing risks across safety, financial, and operational domains, we create resilience throughout the project lifecycle.
This methodical approach not only protects but also empowers our teams to deliver exceptional results, even when facing Texas’s unique challenges like extreme weather, complex regulations, and labor fluctuations.
Looking ahead, we recognize that risk management is dynamic. Our commitment extends beyond implementing today’s best practices to actively evolving with the industry. As technology advances and building methods transform, we continuously refine our approach to risk.
The most successful Texas construction projects are not merely those that avoid problems; they are the ones built by teams prepared to navigate complexity with confidence. By embedding risk management into every aspect of our operations, we deliver the predictability and quality that developers and property owners expect.
Ready to partner with a general contractor who understands Texas construction risks? Contact EB3 Construction today.