At EB3 Construction, we leverage advanced construction techniques to transform how we build for our clients. These innovative approaches significantly differ from traditional methods, enabling us to deliver projects more efficiently while reducing environmental impact. Developers and property owners partnering with us experience construction approaches that streamline timelines and optimize resources without compromising quality.
The construction landscape changed dramatically following the supply chain disruptions of 2021-2022, prompting our industry to adopt smarter building methods. We utilize technologies like Building Information Modeling (BIM), prefabrication, and modular construction to address these challenges. These tools allow us to visualize entire projects digitally before breaking ground, identifying potential conflicts early and reducing costly on-site corrections.
Our implementation of advanced construction techniques delivers tangible benefits for developers and property owners beyond efficiency. The precision of these methods results in buildings that perform better over their lifecycle, with improved thermal efficiency, enhanced air-tightness, and reduced maintenance requirements. This approach allows us to construct buildings that not only meet today’s code requirements but are also ready to adapt to tomorrow’s increasingly stringent sustainability standards.
What Are the Top Digital Advanced Construction Technologies?
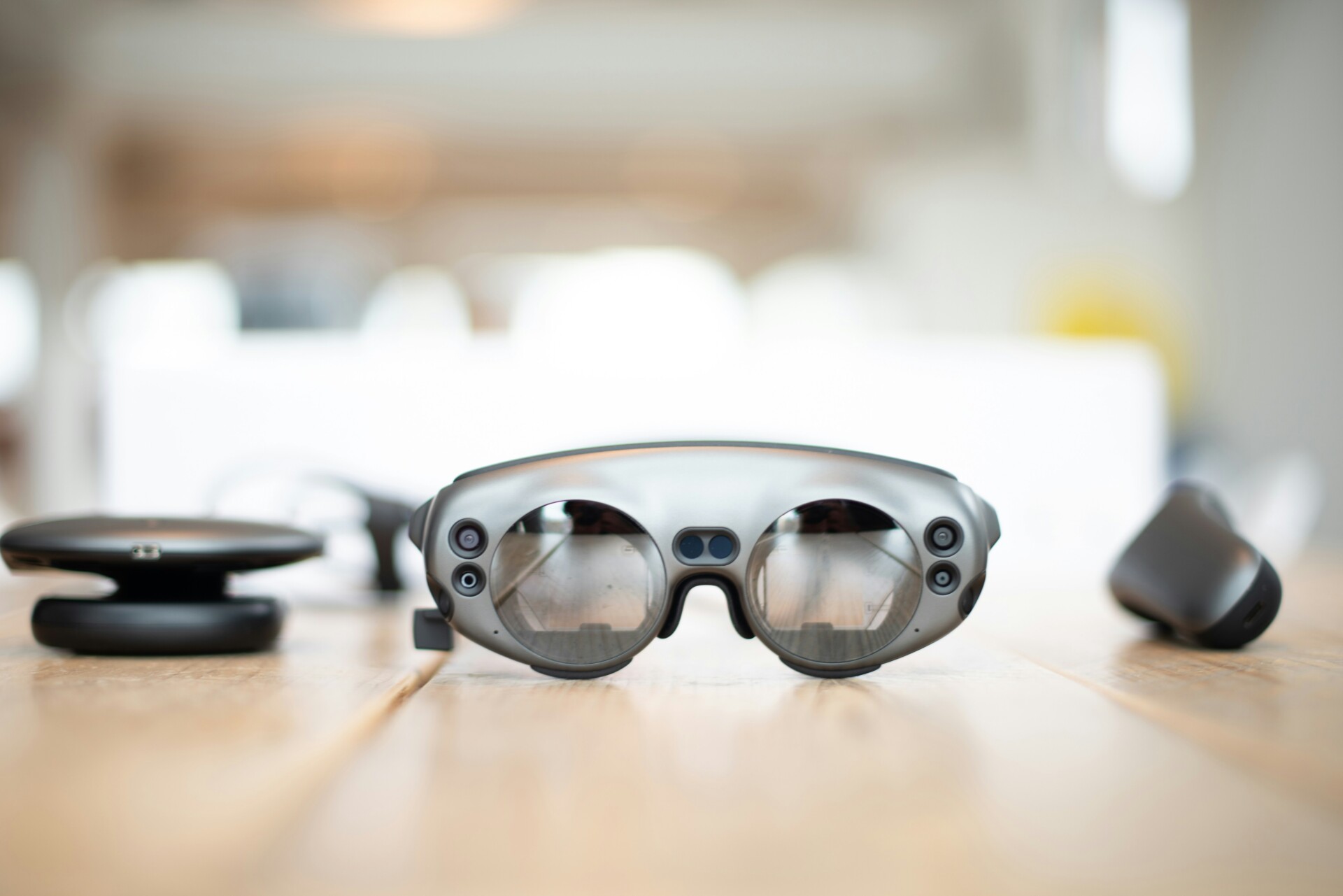
The construction industry is rapidly advancing with digital technologies that are fundamentally transforming project planning, execution, and delivery. At EB3 Construction, we’ve seen firsthand how these innovations streamline our workflows and enhance our ability to serve developers and property owners with precision and efficiency.
Building Information Modeling (BIM): The Foundation of Digital Construction
Building Information Modeling extends beyond 3D modeling software. We use BIM as a comprehensive process to create and manage digital representations of the physical and functional characteristics of buildings throughout their lifecycle. This technology allows our teams to collaborate across disciplines in real-time, detecting clashes before they become costly issues on-site.
When we develop a BIM model for a commercial project, all stakeholders gain access to a single source of truth. Property developers especially appreciate how BIM facilitates better decision-making through comprehensive data integration. The model captures everything from structural elements and MEP systems to material specifications and construction sequencing.
During pre-construction, we utilize BIM to generate accurate quantity takeoffs, precise cost estimates, and realistic construction schedules. This data-driven approach minimizes budget overruns and schedule delays, addressing two primary concerns for our clients.
Augmented Reality (AR) and Virtual Reality (VR): Visualizing Before Building
These immersive technologies have transformed the way we communicate design intent and construction sequences to clients and field teams. Using VR headsets during client meetings, we enable property owners to experience spaces before construction begins, significantly improving their understanding of spatial relationships and design decisions.
On active job sites, our superintendents use AR through tablets and specialized headsets to overlay BIM models onto the physical environment. This capability allows us to verify installations against design intent in real-time, drastically reducing rework. For example, by overlaying mechanical ductwork models onto a partially completed ceiling, we can identify potential conflicts before they occur.
The integration between our BIM models and AR/VR applications creates a seamless workflow where design changes are immediately reflected in the visualization tools. This connectivity ensures all team members work with current information, regardless of their location—be it in the office, trailer, or field.
Construction Robotics: Automating for Precision and Safety
Robotics technology is revolutionizing how we tackle repetitive and physically demanding construction tasks. We’ve incorporated semi-autonomous robots for applications like concrete finishing and material handling, resulting in improved quality and reduced physical strain on our workforce.
For instance, bricklaying robots can place 3,000 bricks per day compared to a human’s average of 500, dramatically accelerating masonry work while maintaining consistent quality. For large-scale developments, this translates to significant schedule compression without sacrificing craftsmanship.
Beyond productivity gains, robotics enhances safety by removing workers from hazardous environments. We utilize drones for site surveys and building inspections, eliminating the need for workers to access dangerous heights or confined spaces. The high-resolution imagery captured also feeds into our digital documentation system, creating comprehensive records throughout construction.
Digital Twins: Creating Virtual Replicas for Ongoing Management
While digital twins are relatively new to construction, we’re implementing these virtual replicas of physical assets to optimize building performance long after turnover. By connecting IoT sensors to building systems and integrating this data with our BIM models, we provide property owners with powerful tools for facility management.
These digital replicas enable predictive maintenance, energy optimization, and space utilization analysis. For commercial property developers, digital twins represent a competitive advantage in attracting and retaining tenants through enhanced building performance and user experience.
Our implementation process establishes the digital twin during construction, capturing as-built conditions and equipment data. This approach ensures the model accurately reflects the physical asset at handover, creating immediate value for facility managers and building operators.
How Are Prefabrication and Modular Construction Changing the Industry?
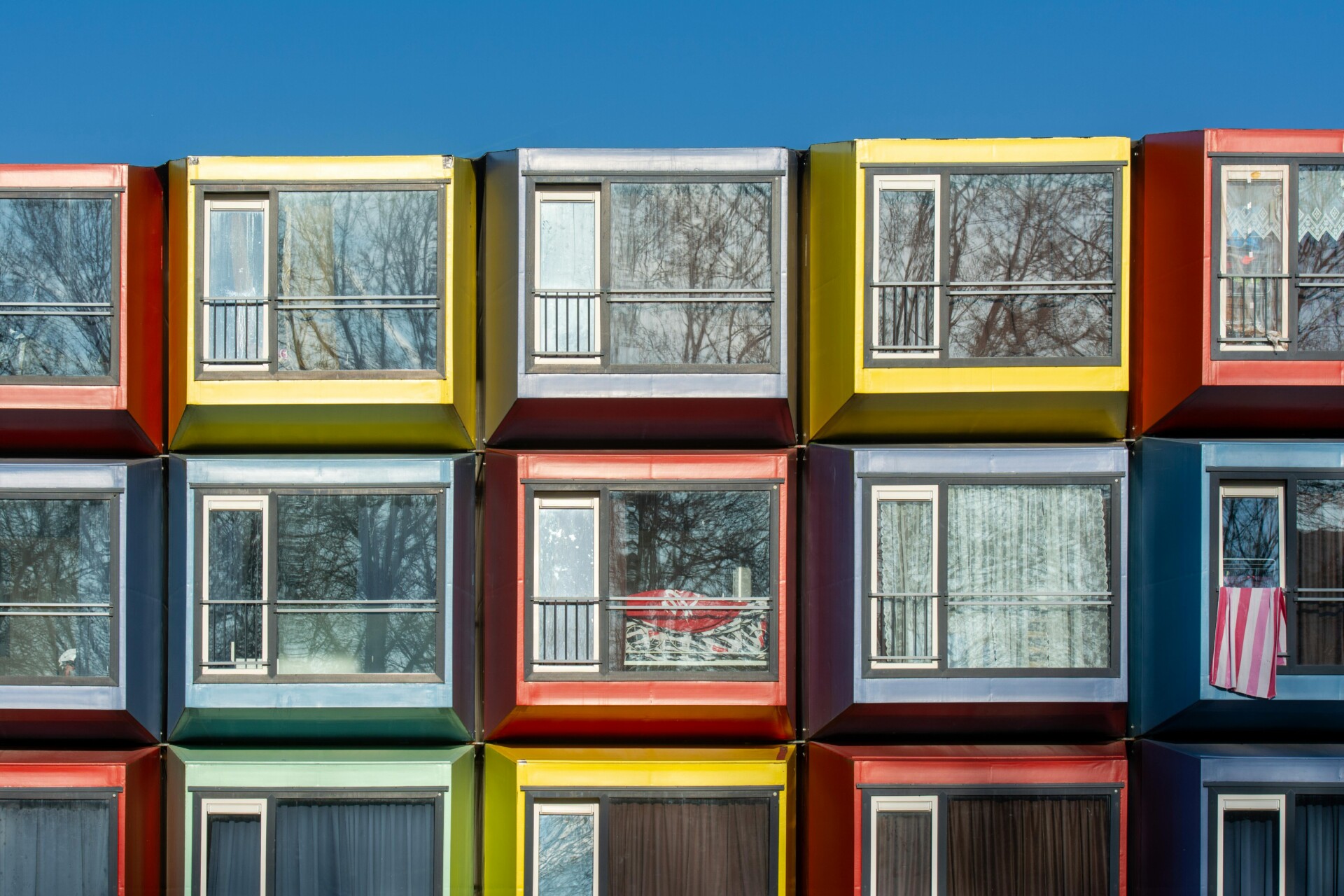
As general contractors serving developers and property owners, we’ve witnessed a significant transformation in construction practices through prefabrication and modular methods. These approaches fundamentally alter the traditional building sequence by shifting substantial portions of construction work from the jobsite to controlled manufacturing environments. The impact on project delivery has been transformative.
The Prefabrication Advantage
Prefabrication involves manufacturing building components off-site under factory conditions before transporting them to the construction site for assembly. We coordinate the production of walls, floors, mechanical systems, and even entire bathrooms in specialized facilities, where weather delays become irrelevant and precision is significantly improved.
The controlled factory environment allows our teams to maintain consistent quality standards impossible to achieve in traditional field construction. Workers build components at comfortable working heights with proper lighting and ergonomic conditions, resulting in higher-quality outputs and fewer safety incidents. This approach also addresses the industry-wide skilled labor shortage, as factory production requires fewer workers per square foot than conventional methods.
When components arrive at the jobsite, our crews execute a carefully choreographed assembly process, dramatically reducing on-site construction time. A recent multi-family project we managed saw a 40% reduction in schedule duration through strategic prefabrication of wall panels, significantly accelerating the developer’s return on investment timeline.
Modular Construction: Taking Prefab Further
Modular construction extends the prefabrication concept by manufacturing complete three-dimensional building sections that arrive at the site essentially finished. We coordinate the production of these volumetric units, complete with electrical, plumbing, finishes, and sometimes even fixtures and furnishings. Upon delivery, our teams connect these modules to create a complete structure.
This approach is particularly effective for repetitive building types like multi-family housing, hotels, and student accommodation. By moving up to 90% of the construction work into a factory setting, we minimize site disruption and neighborhood impact while maintaining tight quality control. The California-based housing project we recently completed used modular units to deliver 120 apartments in just eight months from groundbreaking to occupancy, a timeline impossible with conventional methods.
Material Efficiency and Sustainability Benefits
The sustainability advantages of prefabrication and modular construction align with the growing environmental priorities of developers and property owners. Our prefabrication partners typically generate 30-40% less waste than traditional construction through optimized material usage and recycling programs within their facilities.
Factory production also enables precise material ordering and inventory management, reducing common jobsite problems like damage, theft, and weather exposure. According to recent industry studies, projects utilizing significant prefabrication can reduce material waste by up to 90% compared to conventional construction.
Energy efficiency improves as well, since factory-built components typically achieve tighter tolerances and better insulation installation. The controlled environment allows for more precise application of air barriers and insulation systems, creating buildings that perform better over their lifecycle.
Economic Impact on Project Delivery
From a financial perspective, prefabrication and modular construction deliver value through predictability rather than simply lower costs. While material costs remain comparable, the true savings emerge through shortened construction schedules, reduced financing periods, and earlier occupancy dates.
Labor costs become more predictable as weather delays and site coordination issues decrease. We’ve found that projects with significant prefabrication components maintain more reliable budgets, with fewer change orders and unexpected expenses. The cost certainty this provides has made prefabrication increasingly attractive to our developer clients working with tight pro formas.
For property owners, the accelerated schedule translates directly to revenue generation. A hotel constructed using modular methods might begin generating room revenue three to four months earlier than a conventionally built property, creating substantial financial advantage beyond the construction phase itself.
Implementation Challenges
Successfully incorporating prefabrication requires early planning and design coordination. We engage with manufacturers during preconstruction to ensure designs accommodate manufacturing processes and transportation limitations. BIM (Building Information Modeling) has become essential in this process, allowing our team to identify and resolve conflicts before fabrication begins.
Logistics planning takes center stage with prefabricated elements. We carefully coordinate delivery sequences, crane operations, and assembly schedules to maintain efficiency. Transportation regulations, load sizes, and site access all factor into the prefabrication strategy. Urban projects with limited staging areas often benefit most from prefabrication, despite the additional coordination requirements.
The construction industry’s traditional sequential design-bid-build approach creates challenges for prefabrication. We’ve found the most successful projects embrace integrated project delivery methods where designers, contractors, and manufacturers collaborate from concept through completion. This collaboration ensures designs leverage prefabrication’s strengths while addressing its constraints.
How Are Sustainable Materials and Green Building Techniques Advancing Construction?
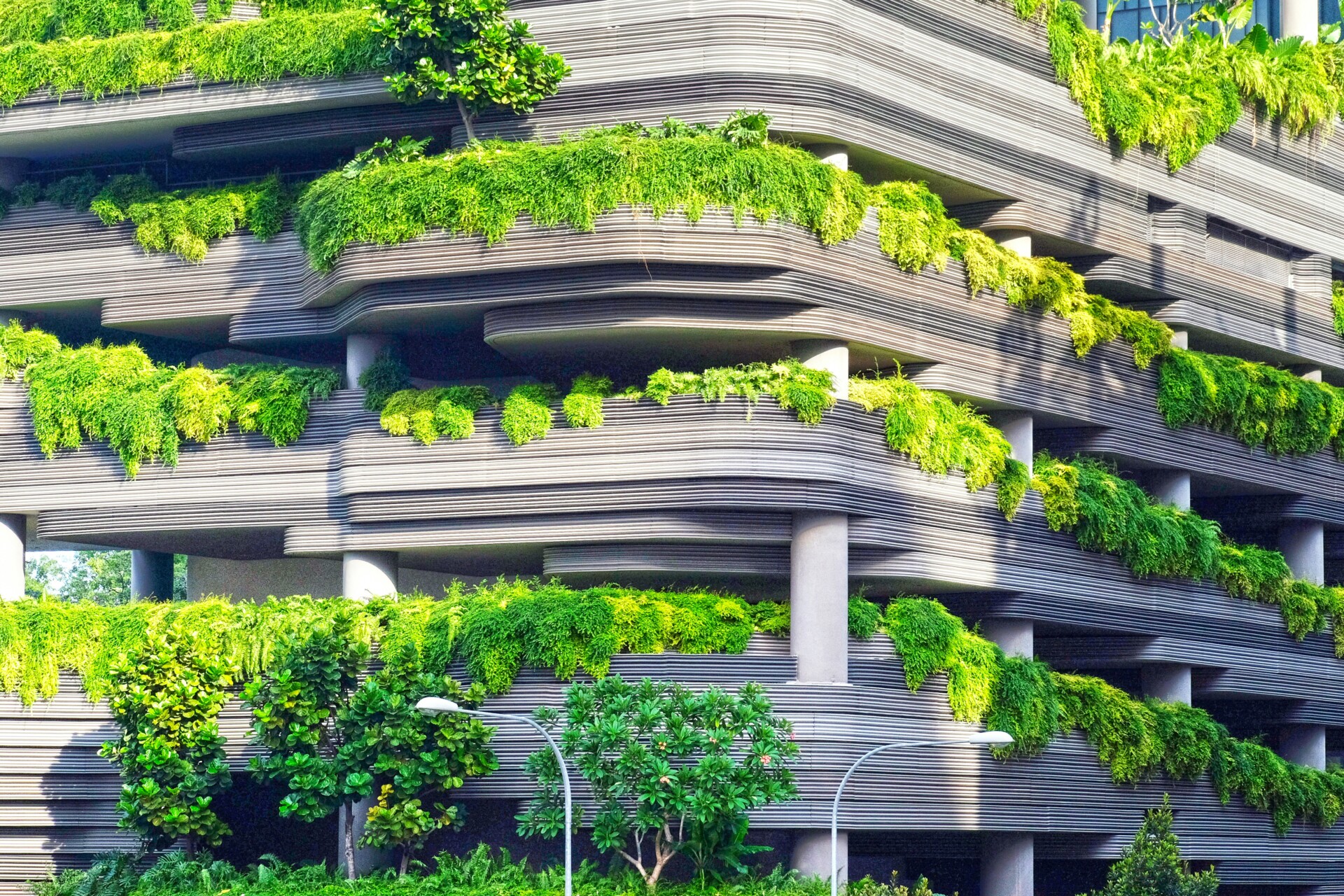
As general contractors at the forefront of industry evolution, we’ve observed a remarkable transformation in how sustainable materials and green building techniques are reshaping construction practices. The move toward environmentally conscious building is not just a trend—it’s becoming the foundation of modern construction methodology, delivering tangible benefits for developers, property owners, and our shared environment.
Green building approaches have matured significantly over the past decade, evolving from experimental concepts to established construction methods. We now regularly incorporate renewable energy systems, locally-sourced sustainable materials, and energy-efficient designs that reduce both environmental impact and operational costs. A January 2023 insurance industry report indicated that construction accounts for 40% of global greenhouse gas emissions, accelerating the adoption of these sustainable practices across the industry.
Innovative Materials Transforming Construction
The materials revolution is perhaps the most visible aspect of sustainable construction advancement. We’re seeing unprecedented innovation in alternative building products that maintain structural integrity while significantly reducing environmental footprint. Recycled steel, which requires considerably less energy to produce than virgin steel, has become a cornerstone material in our commercial projects.
Bamboo continues to gain traction as a sustainable alternative to traditional wood products. Its rapid growth cycle—sometimes reaching up to three feet in a single day—makes it one of the most renewable building materials available. We’ve successfully incorporated bamboo flooring and structural elements in several recent projects, showcasing both its aesthetic appeal and practical durability.
Cork and straw bale construction present other compelling options we’re implementing more frequently, particularly in residential and light commercial applications. These materials offer excellent natural insulation properties while sequestering carbon instead of releasing it. Recent supply chain disruptions have increased interest in these locally-available alternatives as developers seek more reliable material sources.
Integrated Green Building Systems
Beyond materials, we’re implementing comprehensive green building systems that work together to reduce energy consumption and environmental impact. Green roofs are among the most effective integrated solutions we install. These vegetated roof systems provide natural insulation, reduce stormwater runoff by up to 90%, and counteract the urban heat island effect that affects developed areas.
Rainwater harvesting systems are becoming standard features in our projects, collecting precipitation for non-potable uses like irrigation and toilet flushing. A typical residential system can cut freshwater consumption by up to 50%, according to Guardian reporting—a significant saving in regions facing water scarcity challenges.
Our implementation of greywater recycling further enhances water conservation benefits. These systems capture and filter water from showers, bathroom sinks, and washing machines for reuse, addressing the fact that greywater represents 60-70% of total household wastewater production. For commercial properties with high occupancy, these systems deliver substantial operational savings over time.
Energy Efficiency and Renewable Integration
Energy efficiency remains a central focus of our sustainable construction approach. We design and construct buildings that minimize energy requirements through strategic window placement, advanced insulation techniques, and high-performance building envelopes. Insulated Concrete Forms (ICFs) have become particularly valuable in our construction toolkit, offering exceptional thermal resistance that significantly reduces heating and cooling demands.
Solar integration has evolved from an optional add-on to a fundamental design consideration. We now approach solar implementation comprehensively, assessing optimal panel placement and capacity requirements during initial design phases rather than as an afterthought. This proactive approach enables more efficient system sizing and better integration with building aesthetics and function.
Smart building technologies further enhance energy performance through automated control systems that optimize lighting, HVAC, and other building systems based on occupancy and environmental conditions. These technologies provide property owners with unprecedented visibility into building performance and enable continuous optimization for efficiency improvements.
The Economic Case for Sustainability
While environmental benefits drive much of the interest in sustainable construction, the economic advantages are increasingly compelling for developers and property owners. Green buildings typically command premium rental rates and higher occupancy levels, with studies showing values 10-20% higher compared to conventional properties.
Operational savings represent another significant economic benefit. Buildings constructed using modern green techniques generally consume 25-30% less energy and water than conventional structures, creating substantial cost savings throughout the building lifecycle. These savings often offset the modest premium for sustainable construction within a few years of operation.
The resilience factor is also crucial. Sustainable buildings often incorporate features that enhance their ability to withstand extreme weather events and other disruptions. As climate volatility increases, this resilience provides both peace of mind and tangible financial benefits through reduced insurance premiums and a decreased likelihood of costly damage.
What Are the Benefits and Future Trends of Advanced Construction?
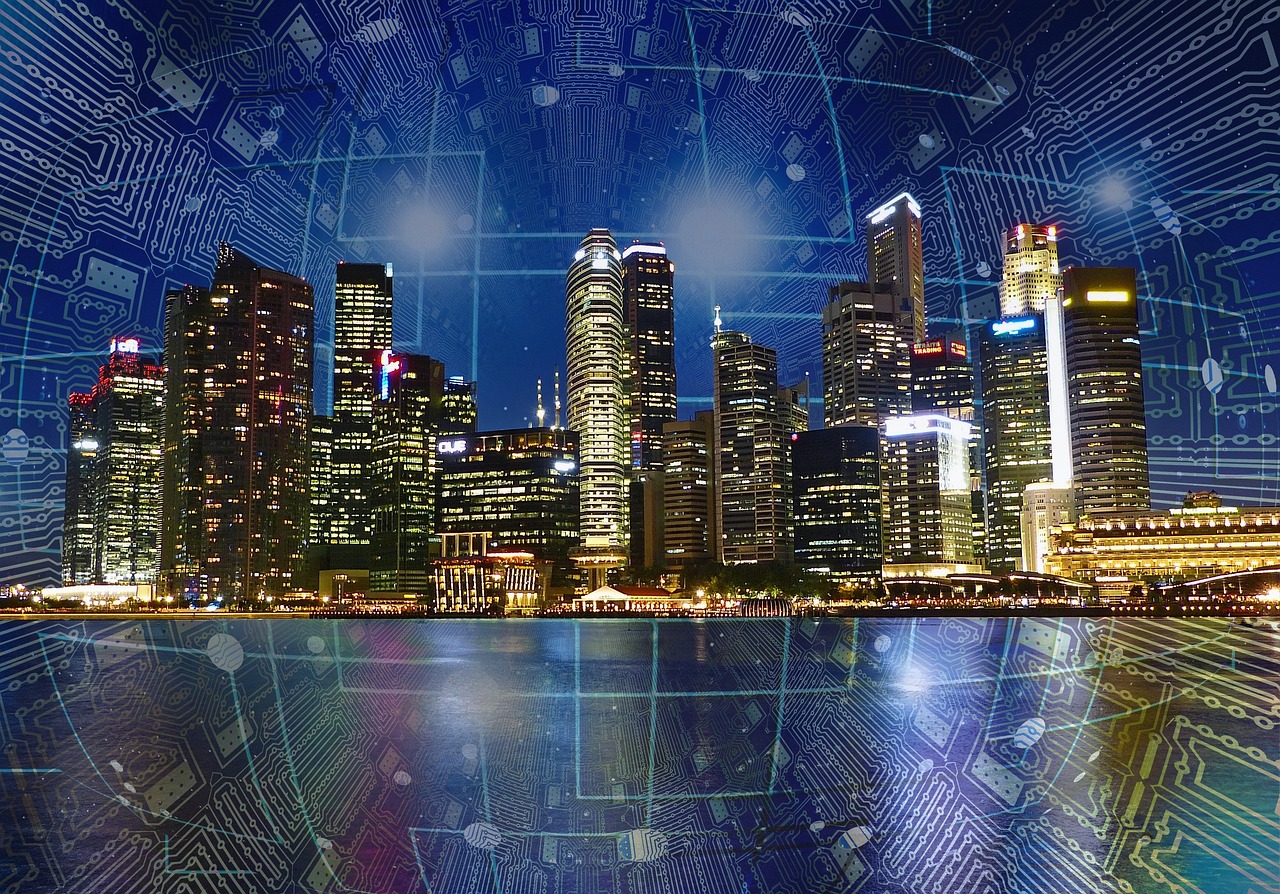
Our implementation of advanced construction technologies delivers tangible benefits throughout the building lifecycle. By integrating cutting-edge solutions into our workflow, we can overcome traditional construction challenges while simultaneously improving project outcomes for developers and property owners. The real value lies not just in the technology itself but in how we apply it to solve real-world construction problems.
Core Benefits of Advanced Construction Implementation
When we deploy technological solutions on-site, we see immediate improvements in project efficiency. Our teams coordinate more effectively, reducing costly downtime and accelerating critical path activities. This translates directly into shortened construction schedules that benefit your bottom line.
Safety enhancements represent another crucial advantage of our advanced construction approach. By utilizing drones for site inspections and real-time monitoring systems, we minimize worker exposure to hazardous conditions. This proactive safety stance reduces incident rates while maintaining productive workflows, preventing the schedule disruptions that typically follow workplace accidents.
Environmental responsibility drives many of our technology choices. Through precise material quantity calculations and intelligent waste management systems, we significantly reduce construction waste. The sustainability benefits extend beyond reduced landfill impact to include lower carbon emissions through optimized logistics and equipment usage.
Transformative Technologies Reshaping Construction
Construction cameras have evolved beyond basic security tools to become essential project management assets. We leverage these systems for comprehensive jobsite visibility, enabling real-time monitoring that supports informed decision-making. When stakeholders need current progress updates, our camera systems provide immediate, accurate visual documentation.
Artificial intelligence represents a cornerstone of our technology strategy moving forward. In 2024, responsible AI implementation offers remarkable efficiency gains while preserving human oversight where it matters most. Our teams utilize AI-enhanced tools for document management, quality control, and project forecasting without sacrificing the experienced human judgment that complex construction scenarios demand.
The accelerating digitization of construction processes forms the foundation of our technological approach. By eliminating paper-dependent workflows, we reduce error risks while creating a comprehensive digital record of project development. This digital transformation minimizes rework requirements, preventing the cost overruns and timeline extensions that frequently plague traditional construction methods.
Emerging Trends Shaping Construction’s Future
The Internet of Things (IoT) has moved beyond conceptual applications to deliver practical benefits on our jobsites. Connected sensors provide continuous monitoring of critical systems, materials, and environmental conditions. This networked approach enables preventative maintenance, quality verification, and environmental compliance without adding administrative burden to site personnel.
Prefabrication continues gaining momentum as a solution to both labor shortages and quality control challenges. We coordinate modular construction elements that arrive ready for installation, reducing on-site labor requirements while maintaining strict quality standards. The controlled manufacturing environment for these components ensures consistent performance specifications that on-site fabrication cannot match.
Material science innovations show particular promise for addressing construction sustainability concerns. New cement alternatives and advanced composites offer improved performance characteristics while reducing environmental impact. We actively evaluate these emerging materials, implementing those that meet our rigorous standards for structural integrity, durability, and cost-effectiveness.
Digital twin technology represents perhaps the most transformative development on our technology horizon. By creating comprehensive virtual models that mirror physical structures in real-time, we enable unprecedented project visualization and performance analysis. These digital replicas allow stakeholders to experience spaces before construction begins and provide valuable platforms for testing system modifications without disrupting operations.
The construction landscape continues to evolve rapidly as technology adoption accelerates industry-wide. Forward-thinking approaches to implementation will distinguish successful projects from those struggling with traditional limitations. Our commitment to responsible technology integration ensures we capture these benefits while maintaining the critical human expertise that defines quality construction.
Conclusion: The Transformative Impact of Advanced Construction
The construction landscape is undergoing a notable evolution as we integrate advanced techniques into our daily operations. At EB3 Construction, we’ve seen firsthand how digital modeling, prefabrication, and automated processes are transforming project delivery for our clients. The reliance on traditional methods is giving way to a sophisticated approach that fuses construction expertise with technological innovation.
These advancements tackle the core challenges our industry has faced for decades. Through BIM implementation, we’re significantly reducing design conflicts before they escalate into costly field issues. With modular construction and off-site fabrication, we’re compressing schedules while maintaining stringent quality standards. The use of sustainable materials and energy-efficient systems enables us to deliver buildings that perform better over their lifecycle and reduce environmental impact—an essential goal for many of our progressive clients.
Looking ahead, we understand that construction professionals who embrace these advanced methodologies won’t just endure—they’ll excel. As general contractors, we remain dedicated to balancing technological adoption with practical field experience, ensuring that innovations provide genuine value rather than unnecessary complexity. The future of construction isn’t merely about building differently; it’s about building smarter, safer, and more sustainably. Connect with our team to explore how our advanced construction approach can realize your next project.