On any active job site, the steel frameworks rising alongside buildings are more than just metal pipes and platforms. These critical temporary structures, known as scaffolding, provide safe access to elevated work areas during construction, renovation, and maintenance projects. At EB3 Construction, we regard scaffolding as the backbone of vertical construction, enabling our crews to work efficiently at heights that would otherwise be inaccessible.
Scaffolding systems transform construction by creating stable working platforms that support multiple tradespeople and materials simultaneously. Whether coordinating masonry work on a multi-story apartment complex or executing exterior finishes on a commercial property, properly engineered scaffolding makes these tasks safe and efficient. Alternatives like ladders or lifts simply cannot provide the same level of stability, capacity, or continuous workspace.
The construction landscape changed significantly following OSHA’s implementation of strict scaffolding safety protocols in the 1970s. Today, we incorporate these engineered systems into virtually every project plan where work extends beyond ground level. Our experience shows that comprehensive scaffolding strategies not only protect our workforce but also significantly improve project timelines by creating accessible work zones across the entire building envelope.
What Are the Most Common Types of Construction Scaffolding?
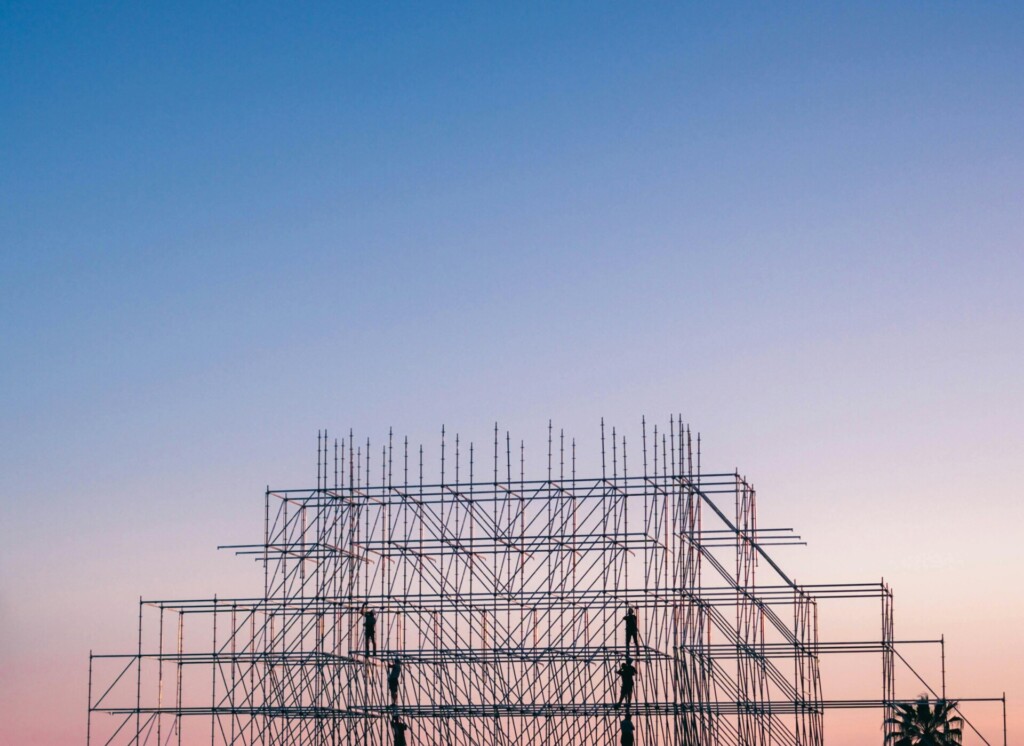
In construction operations, selecting the appropriate scaffolding system directly influences safety and efficiency. We consistently assess project requirements to determine the most suitable scaffold type for supporting our crews and materials. Understanding the characteristics of each scaffolding system allows us to enhance productivity while maintaining high safety standards across our sites.
Frame Scaffolding
Frame scaffolding, also known as fabricated scaffolding, is our most frequently used option for residential and commercial projects. We appreciate its cost-effectiveness and versatility, especially for painting and general construction tasks. The modular components enable quick assembly and disassembly, making it ideal for projects with tight deadlines.
When deploying frame scaffolding, it’s crucial to ensure the base is perfectly level. The prefabricated steel frames typically support one or two tiers, providing stable platforms for safe access to exterior walls. This scaffolding type is integral to many of our smaller to mid-sized projects due to its adaptability and economic advantages.
Double Scaffolding
For masonry work, particularly with stone structures, we use double scaffolding. Unlike single scaffolding, this system is self-supporting and does not rely on the building wall, offering exceptional stability. We construct it with two rows of standards connected by horizontal ledgers and diagonal braces for reinforcement.
The robust design allows masons to work confidently with heavy materials while maintaining access to the work surface. This structure is beneficial for projects where the wall cannot bear additional loads or when applying specialized finishes requiring multiple work levels.
Cantilever Scaffolding
On projects with ground accessibility challenges, we implement cantilever scaffolding solutions. This system extends horizontally from the building structure using needle beams secured to the floor inside. It’s commonly used in urban construction environments where sidewalks must remain accessible or when ground conditions cannot support traditional scaffolding.
Safety is paramount when installing cantilever scaffolding, requiring meticulous engineering calculations for proper load distribution. Our experienced teams carefully secure each component, as this system demands more precise installation than standard scaffolding types. Though complex to erect, cantilever scaffolding provides essential access in otherwise inaccessible construction scenarios.
Suspended Scaffolding
For high-rise building projects, suspended scaffolding (or swing stage scaffolding) offers effective access solutions. These systems feature platforms suspended from the roof or upper levels using wire ropes and mechanical hoists. The adjustable height capabilities facilitate efficient exterior maintenance, window installations, or facade renovations.
Two-point suspension systems are standard, with platforms supported at both ends and adjustable as needed. We conduct thorough component inspections, focusing on rigging, roof anchors, and safety devices. Wind conditions are carefully monitored as they can impact platform stability during adverse weather.
Steel Scaffolding
For demanding construction applications, we rely on steel scaffolding systems. The superior strength-to-weight ratio makes this option ideal for supporting heavy loads, including workers, equipment, and materials. The durability of steel components allows reuse across multiple projects, providing long-term value despite higher initial costs.
Our steel scaffolding systems have prefabricated components that connect with standardized couplings, allowing quick assembly while maintaining structural integrity. Steel’s non-combustible nature also provides additional safety benefits for projects involving welding or hot works. For complex commercial structures needing multiple work levels and heavy material staging, steel scaffolding is our premier solution.
Mobile Scaffolding
When the work requires frequent repositioning, mobile scaffolding is implemented. These systems have a standard frame configuration mounted on lockable castor wheels, enabling easy relocation without complete disassembly. This mobility enhances productivity for tasks like painting, electrical installations, or mechanical work.
Strict safety protocols are enforced for mobile scaffolding. We ensure wheels remain locked during work, maintain proper outrigger supports for stability, and never move units while occupied. Height restrictions are carefully observed since mobile units typically have more limited vertical capacity than fixed scaffolding systems.
Scaffolding Type | Primary Applications |
---|---|
Frame Scaffolding | Residential and commercial construction, painting, general tasks |
Double Scaffolding | Stone masonry, self-supporting structures |
Cantilever Scaffolding | Urban construction, projects with ground accessibility challenges |
Suspended Scaffolding | High-rise buildings, exterior maintenance, window installation |
Steel Scaffolding | Heavy construction, projects requiring multiple work levels |
Mobile Scaffolding | Tasks requiring frequent repositioning, painting, electrical work |
Tube and Coupler Scaffolding | Complex geometries, heritage restoration |
Tube and Coupler Scaffolding
For complex construction geometries, tube and coupler scaffolding (also known as systems scaffolding) offers unmatched adaptability. This system uses individual tubes connected by adjustable couplers, allowing custom configurations for irregular building shapes or challenging site conditions.
While requiring more skilled labor than frame scaffolding, the versatility of tube and coupler systems is invaluable for heritage restoration projects or structures with non-standard dimensions. The ability to precisely adjust each component ensures level working platforms even when the underlying structure has unusual angles or projections.
What Materials and Components Make Up Scaffolding Systems?
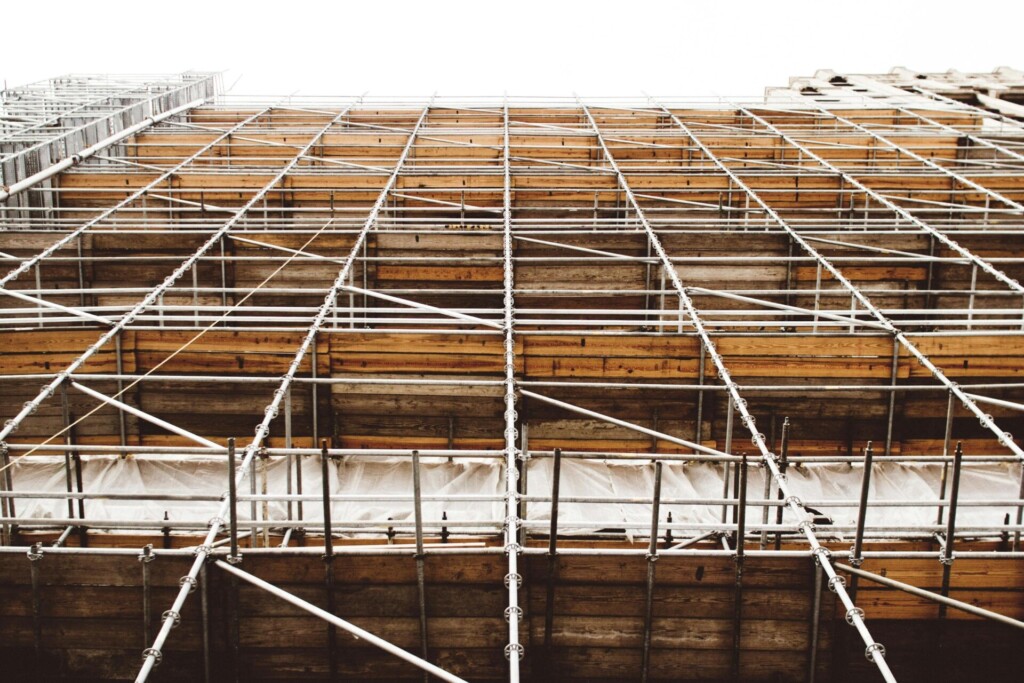
At EB3 Construction, we rely on properly assembled scaffolding systems to provide safe, stable platforms for our crews working at height. These systems consist of several key components, each playing a critical role in creating structures that can safely support workers and materials throughout a project’s lifecycle.
Essential Scaffolding Components
The backbone of any scaffolding system is formed by a series of interconnected structural elements. When we erect scaffolding on our construction sites, we ensure each component meets rigorous standards and serves its specific purpose:
Standards – These vertical tubes transfer the entire load to the ground. We position them at regular intervals and always ensure they are perfectly plumb (vertically straight) to maintain stability. The base of each standard rests on a base plate, supported by sole boards on softer ground to distribute weight properly.
Ledgers – These horizontal components run parallel to the building facade and connect between standards. We use ledgers to create the scaffold’s framework and to support transoms and working platforms. By ensuring ledgers are securely fastened, we establish lateral stability throughout the structure.
Transoms – Positioned at right angles to ledgers, transoms provide additional structural support and create the foundation for working platforms. We place main transoms next to standards and add intermediate transoms between them to prevent deflection of boards under load.
Bracing – Diagonal components that significantly enhance stability. Cross bracing forms an “X” pattern between frames, while diagonal bracing connects different scaffold levels. This prevents lateral movement and keeps the structure rigid, even when workers move about or when wind loads are present.
Base Plates and Sole Boards – Base plates distribute the load at the bottom of each standard, while sole boards provide additional support on soft or uneven ground. We never skip this critical foundation element, as it ensures weight is properly transferred to the supporting surface.
Working Platforms – These provide the actual surface where our crews perform their work. We use sturdy planks or manufactured decking that can support the combined weight of workers, tools, and materials without deflection.
Safety Components
Beyond the structural elements, we incorporate several safety-critical components into every scaffolding system:
Guardrails – We install these at approximately 42 inches above the working platform with mid-rails positioned halfway between the top rail and platform. This creates an effective barrier against falls, our industry’s most serious hazard.
Toeboards – Vertical barriers at least 3.5 inches high that run along the edges of platforms. These prevent tools and materials from being accidentally kicked off the edge, protecting personnel working below from falling objects.
Couplers and Clamps – These connect scaffolding tubes together securely. We use right-angle couplers for 90-degree connections, swivel couplers for variable angles, and sleeve couplers for extending tubes. The quality of these connections directly impacts overall scaffold integrity.
Materials Used in Modern Scaffolding
The materials used in scaffolding systems have evolved considerably over time, with steel now dominating the industry for its combination of strength, durability, and relative weight efficiency:
Steel – The most common material in our scaffolding inventory. Steel tubes typically measure 48.3mm in outer diameter and provide exceptional load capacity and durability. Though heavier than alternatives, steel scaffolding offers unmatched structural integrity for most commercial construction applications.
Aluminum – When weight is a concern or for specialized applications, we employ aluminum scaffolding. It is approximately one-third the weight of comparable steel systems, making it easier to transport and erect. While not as strong as steel, aluminum scaffolding is corrosion-resistant and well-suited for certain interior applications.
Wood – Though less common in modern commercial construction, wooden scaffolding components (particularly planks) still find use in specific scenarios. We carefully inspect all wooden components for integrity, as they can deteriorate more rapidly than metal alternatives.
Fiberglass – For projects involving electrical work, we sometimes utilize fiberglass components which offer non-conductive properties. While specialized and more expensive, fiberglass provides critical safety benefits when working near power sources.
System Integration
The true effectiveness of scaffolding lies not just in the individual components but in how we integrate them into a cohesive system. For complex projects, we often combine frame scaffolding with tube and coupler elements to create custom configurations that adapt to unique architectural features or challenging site conditions.
Before any crew member sets foot on a scaffold, we conduct thorough inspections to verify that all components are properly installed, connections are secure, and the entire system meets both regulatory requirements and our own rigorous safety standards. This systematic approach ensures that our scaffolding provides not just access to work areas, but a fundamentally safe platform from which our teams can efficiently complete their tasks.
How Does Scaffolding Enhance Safety in Construction?
At EB3 Construction, we have seen how properly implemented scaffolding enhances worksite safety. Unlike ladders, which offer limited stability and reach, scaffolding provides secure, level platforms that significantly reduce fall hazards when working at height. This comprehensive approach to elevated work areas is one of our most critical safety investments on every project we manage.
The structural integrity of modern scaffolding systems offers more than just worker stability. When we install scaffolding according to OSHA specifications, we incorporate multiple protective elements: guardrails positioned between 38 and 45 inches high, mid-rails at approximately half that height, and toe boards to prevent tools and materials from falling to lower levels. For particularly active work zones, we often add debris netting or mesh covers to contain potential falling objects further.
Despite these advantages, scaffolding safety requires continuous attention throughout a project’s lifecycle. We maintain a rigorous inspection protocol where a competent person examines all scaffolding before each shift begins, after any modifications, and following weather events that might compromise structural integrity. This vigilance helps us identify potential issues before they become hazards – a practice that has proven invaluable, as OSHA reports that scaffold-related accidents cause approximately 4,500 injuries and 60 deaths annually in the construction industry.
Managing Scaffold-Specific Hazards
Our safety protocols address the four most common scaffolding hazards we encounter across construction sites. First, we carefully inspect all components for material defects or damage before assembly begins. Second, we implement comprehensive falling object protection, including toe boards, debris nets, and controlled access zones below work areas. Third, we closely monitor weather conditions, suspending scaffold work during high winds, storms, or when ice accumulation creates slipping hazards. Fourth, we enforce strict training requirements for all personnel working on or around scaffolding systems.
The statistics underscore why we prioritize these measures. According to OSHA data, falls from scaffolding account for approximately 25% of fatal workplace accidents in construction. When scaffold structures fail, the consequences are often catastrophic, affecting not just workers on the platform but anyone below. By maintaining a 4:1 height-to-base ratio and implementing proper guying, tying, or bracing on taller structures, we substantially reduce the risk of collapses.
Training represents our most powerful scaffold safety tool. We ensure every worker understands load capacities, proper access methods, and fall protection requirements. Our supervisors verify that no scaffold is loaded beyond its design capacity, which must support at least four times the maximum intended load. Additionally, we train crews to recognize signs of structural compromise and empower them to stop work immediately if safety concerns arise.
Customizing Scaffold Solutions for Project-Specific Needs
Different construction phases and building configurations require tailored scaffolding approaches. For facade work on complex architectural designs, we often employ suspended scaffolding with appropriate fall arrest systems. For interior work in high-ceiling spaces, we typically use mobile scaffolding with locking caster wheels that can be repositioned as work progresses. High-rise projects may require elaborate scaffold designs from professional engineers, especially when heights exceed 125 feet.
The cost of proper scaffolding represents a significant but essential investment in project safety. When analyzing project budgets, we calculate not just the immediate expense but also the productivity gains from providing stable work platforms and the risk mitigation value. Workers who feel secure can focus on quality craftsmanship rather than maintaining precarious balance, resulting in better outcomes for all project stakeholders.
The latest innovations in scaffolding technology have enhanced our safety capabilities even further. Advanced aluminum components reduce weight while maintaining strength, making assembly safer and more efficient. Integrated ladder systems with rest platforms minimize climb fatigue. Quick-lock mechanisms ensure connections remain secure but allow for faster assembly and disassembly. These improvements have helped us maintain excellent safety records while keeping projects on schedule.
What Are Common Uses of Scaffolding Beyond Construction?
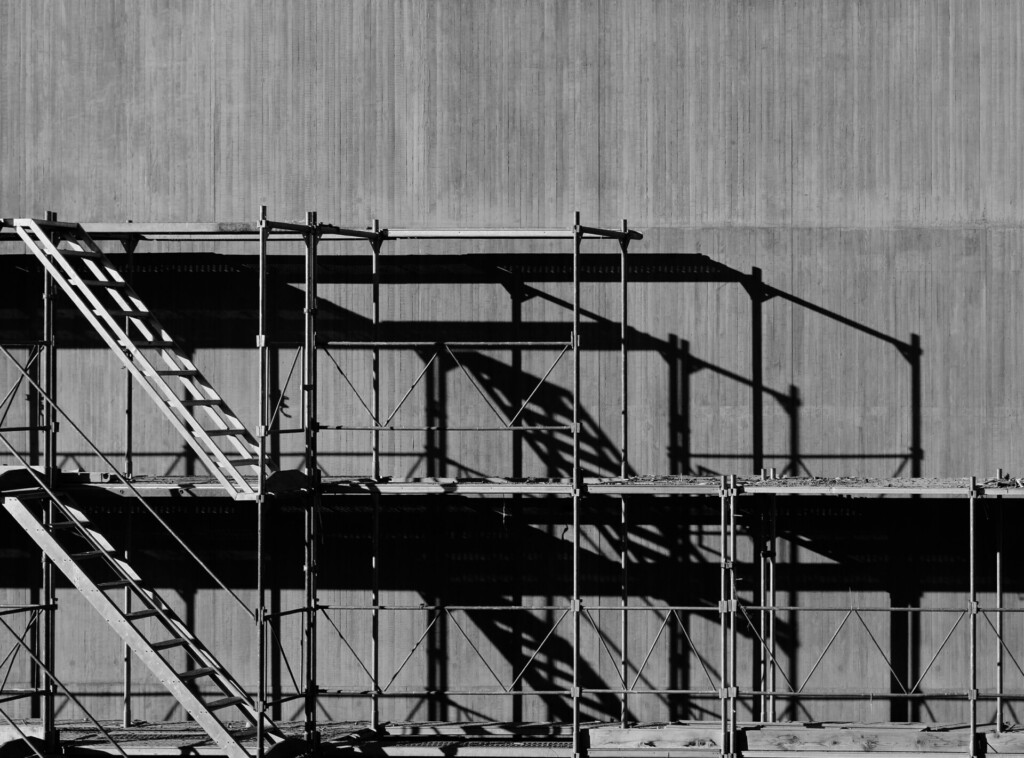
At EB3 Construction, we regularly deploy scaffolding systems for our building projects, but we’ve also seen how these versatile structures serve important functions beyond traditional construction purposes. Our experience shows that well-designed scaffolding solutions provide safe access in many industrial and commercial scenarios.
Industrial Inspections and Maintenance
In the industrial sector, scaffolding creates crucial access points for inspection teams evaluating large equipment. We coordinate scaffold installations that allow inspectors to safely reach pressure vessels, boilers, and industrial tanks for visual assessments and non-destructive testing procedures.
The inspection process typically initiates the maintenance cycle. After defects are identified, our maintenance crews use the same scaffolding systems to access and repair those areas. This seamless transition from inspection to maintenance maximizes efficiency while maintaining safety standards throughout industrial facilities.
During recent refinery turnarounds, we’ve seen how proper scaffold planning can reduce facility downtime by creating simultaneous access points for multiple inspection and maintenance teams. The ability to swiftly deploy and reconfigure these systems has become essential for industrial clients adhering to strict maintenance schedules.
Event Staging and Entertainment
The entertainment industry has embraced scaffolding’s structural versatility for creating temporary performance spaces. We build scaffold systems that form the foundation for concert stages, viewing platforms, and complex rigging structures at music festivals and outdoor events.
Festival organizers value scaffolding for its quick assembly and disassembly capabilities. A properly engineered scaffold system can support substantial weight loads from sound equipment, lighting rigs, and video displays while accommodating the dynamic forces that occur during performances.
For temporary grandstand seating at sporting events and exhibitions, we implement specialized scaffold configurations that prioritize crowd safety while maximizing viewing angles. These systems require careful engineering to handle the combined weight and movement of spectators.
Application | Description |
---|---|
Construction Industry | Provides essential temporary elevated work platforms for residential and commercial building projects, including façade work and steel erection in high-rise buildings. |
Petrochemical and Industrial Plants | Enables access to equipment and infrastructure for maintenance, repair, and new construction projects, with extensive safety features for volatile equipment. |
Infrastructure Projects | Facilitates construction and repairs for bridges, dams, roads, and facilities by providing access and safety for workers. |
Entertainment Venues | Used in concerts, sporting events, and theme parks for setting up stages, lighting, and other equipment, ensuring safety and enhancing experiences. |
Shipbuilding and Maritime | Provides safe platforms for repairs, maintenance, and construction of ships, ensuring efficient and thorough work on massive vessels. |
Art Installations and Cultural Events
Artists have repurposed scaffolding as both a supporting structure and a creative medium. We’ve provided technical guidance for large-scale interactive art installations where scaffolding forms the structural backbone. The “Big Bambu” installation at New York’s Metropolitan Museum of Art exemplifies this approach, combining traditional scaffolding with bamboo to create a climbable artwork.
Cultural events worldwide incorporate scaffolding in fascinating ways. Traditional festivals like Hong Kong’s Cheung Chau Bun Festival feature bamboo scaffolding towers constructed for competitions. In urban centers, we’ve seen scaffolding support vertical gardens that transform concrete facades into living green spaces, improving aesthetics while reducing carbon footprints.
Film and photography productions frequently utilize scaffold systems to create camera platforms and support lighting equipment. These temporary structures provide stable, elevated positions for capturing unique angles while ensuring crew safety during shoots. The flexibility of modular scaffolding allows quick adjustments as production requirements change throughout filming.
Commercial and Retail Applications
The retail sector has discovered creative applications for scaffolding beyond building construction. We design temporary structures for pop-up shops and seasonal retail displays that can be quickly assembled and dismantled. During fashion weeks and trade shows, luxury brands deploy custom scaffold configurations that create distinctive retail environments while maintaining their aesthetic standards.
Window cleaning operations for high-rise buildings depend on properly engineered scaffolding systems. We implement suspended scaffold platforms that provide window cleaners with stable working surfaces while incorporating appropriate fall protection measures. These systems must account for building geometries and wind conditions to ensure worker safety at extreme heights.
As construction professionals, we recognize that scaffolding’s versatility extends far beyond its traditional applications. The fundamental principles of safe access, structural stability, and adaptability make scaffolding an indispensable tool across numerous industries requiring temporary elevated work platforms.
Conclusion: The Future of Construction Scaffolding
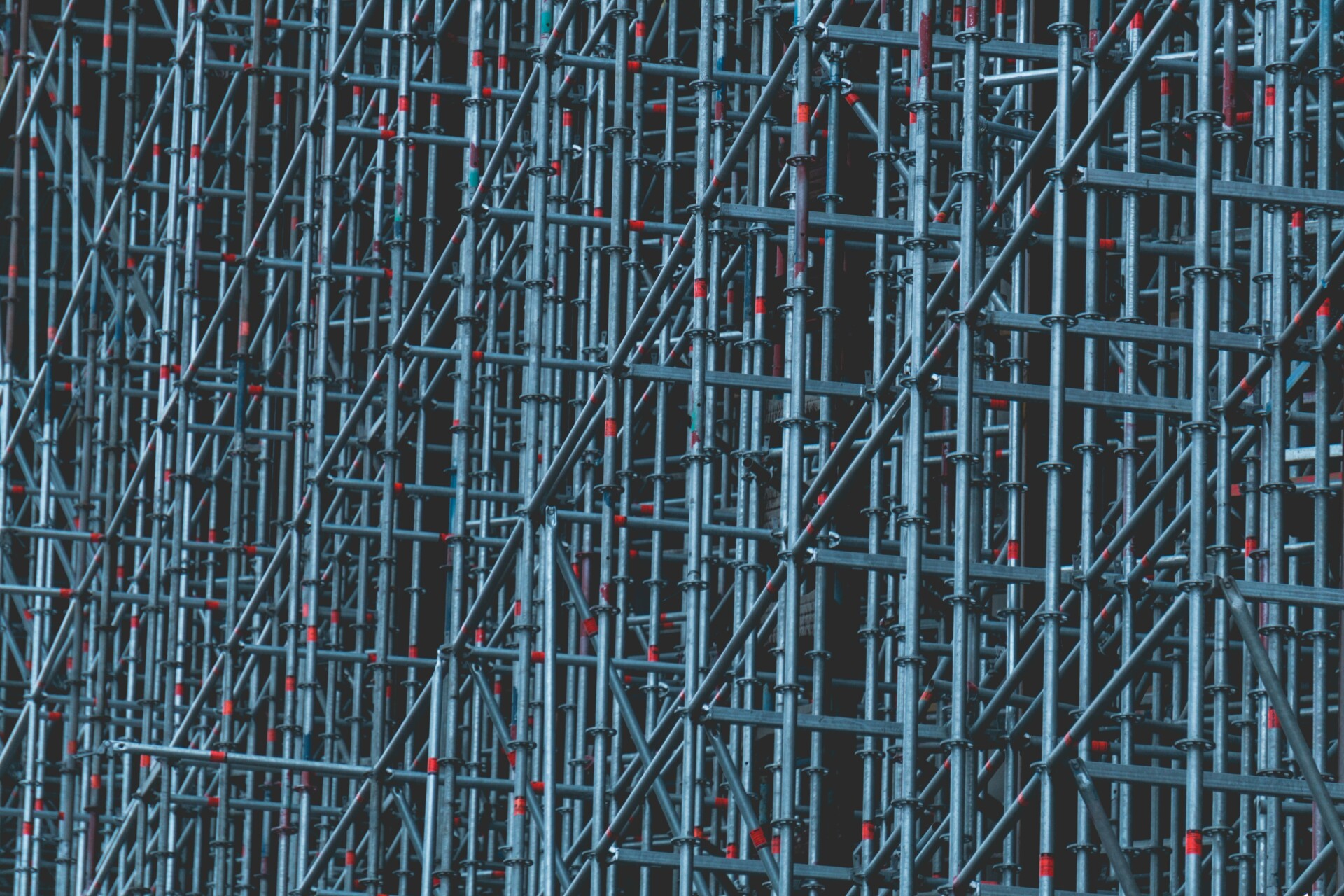
As we look toward the future of construction, scaffolding continues to evolve alongside technological advancements while retaining its essential role in project execution. Today’s innovations are establishing new standards for jobsite safety and productivity, benefiting both our teams and our clients’ bottom lines. Smart scaffolding solutions with integrated sensors for real-time monitoring are already transforming how we approach structural support on complex projects.
While we embrace emerging technologies like inspection drones that complement traditional scaffolding methods, especially for preliminary site assessments and visual inspections, we recognize the indispensable value of physical scaffolding structures. These innovations help reduce worker exposure to heights during certain phases, but providing stable, accessible work platforms remains crucial for virtually every construction project we handle. Our approach combines time-tested scaffolding principles with the strategic adoption of new technologies to deliver the safest and most efficient construction solutions for our clients’ developments, whether they are urban high-rises or suburban commercial centers. Contact us at EB3 Construction to discuss how our scaffolding expertise can support your next project.