For construction professionals, supply chain disruptions have become an all-too-familiar obstacle that can derail even the most carefully planned projects. These material nightmares ripple through every phase of construction, threatening timelines, budgets, and quality standards.
At EB3 Construction, we believe the building and construction industry faces unique vulnerabilities regarding supply chain management. Unlike other sectors, we rely on just-in-time delivery of specialized materials and equipment to keep projects moving forward. When these critical components don’t arrive as scheduled, the impacts can be severe and long-lasting.
To understand the scale of this issue, construction input costs have risen a staggering 38.7% since February 2020, according to recent data from Associated Builders and Contractors. This dramatic increase reflects ongoing challenges such as shortages, transportation bottlenecks, and market volatility that plague the industry.
By developing a clear understanding of the key supply chain issues affecting construction, we can begin to craft strategies to mitigate their impact. Whether it’s diversifying suppliers, embracing technology for better visibility, or rethinking traditional procurement models, there are strategic steps that can help protect projects from disruption. Construction firms that successfully adapt their supply chain management practices will be better positioned to deliver projects on time and on budget in this challenging environment.
What Material Availability and Pricing Challenges Are Affecting Construction?
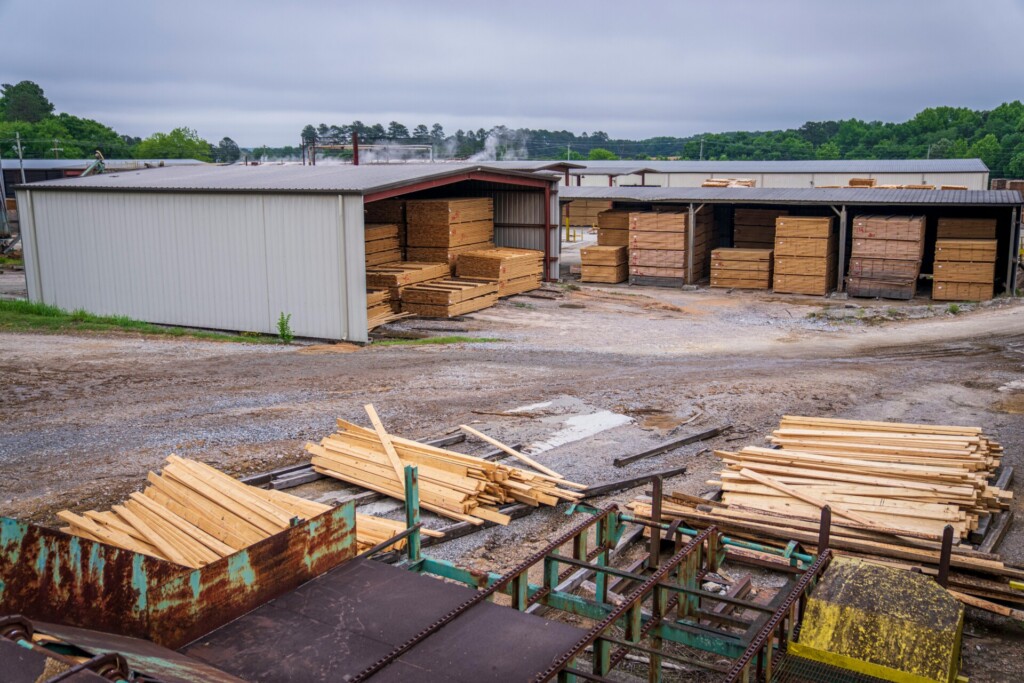
The construction industry continues to face significant challenges related to material availability and pricing in 2023. Construction input costs have risen dramatically, with prices up 38.7% compared to pre-pandemic levels. This steep increase has placed immense pressure on contractors’ budgets and project timelines.
Specific materials have experienced even more drastic price hikes. Notably:
- Iron and steel prices have increased by over 50% since 2020
- Lumber costs, while volatile, remain substantially higher than historical averages
- Concrete prices have risen over 11% year-over-year
Global conflicts continue to worsen these challenges. The ongoing Israel-Hamas war has forced transportation providers to reroute shipments around conflict zones, leading to surges in shipping rates. This ripple effect impacts material availability and prices across the board.
While some materials show signs of returning to more stable pricing, specialized items face persistent shortages and extended lead times:
- HVAC equipment: 20-30 week lead times
- Electrical wire: 12-16 week lead times
- Transformers: Up to 52 weeks from order to delivery
These extended timelines pose significant challenges for project planning and scheduling. Contractors must now factor in potential multi-month delays for critical components when estimating project durations.
The combination of price volatility and supply chain disruptions has led many construction firms to adopt new strategies:
- Increased stockpiling of essential materials when available
- Implementing more flexible contract terms to account for potential price fluctuations
- Exploring alternative materials or construction methods to mitigate shortages
- Engaging in earlier procurement and adopting longer planning horizons for projects
While the industry has demonstrated remarkable resilience in the face of these challenges, material availability and pricing issues remain a primary concern for contractors in 2023. Staying informed about market trends and maintaining open communication with suppliers and clients is crucial for navigating this complex market.
As we navigate these turbulent waters, it is clear that adaptability and proactive planning are key. Contractors who can effectively manage these material challenges will be better positioned to deliver successful projects despite the ongoing market volatility.
How Do Transportation and Logistics Issues Impact Construction Projects?
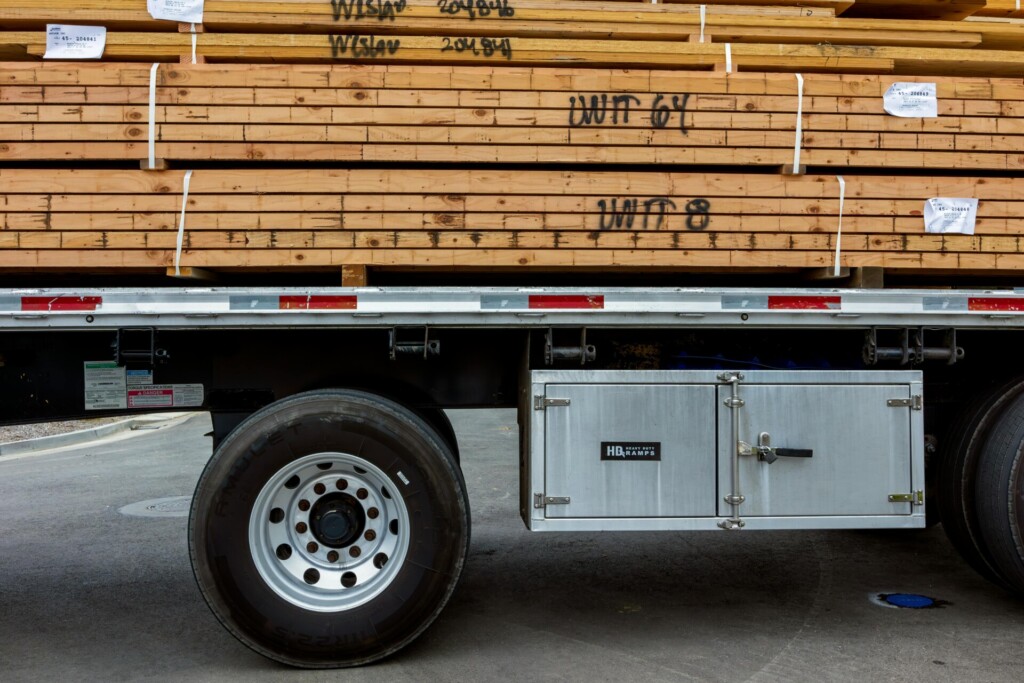
Transportation and logistics challenges significantly affect the construction industry. If not managed properly, these issues can severely impact project timelines and budgets.
One major hurdle is finding suitable vehicles for material transport, especially for projects in remote locations. This often leads to increased transportation costs and potential delays as contractors work to secure appropriate vehicles.
Delivery timelines have been significantly affected in recent years. Before the pandemic, materials like steel and timber typically had lead times of 2-4 weeks. Now, those same materials can take 12-16 weeks to arrive on site. The situation is even more dire for specialized equipment:
- Electrical switchgear: 42-60 week lead times
- Transformers: Up to 52 week lead times
These extended delivery windows create major scheduling headaches for project managers. Without real-time visibility into transit status, confusion and inefficiencies abound. We often encounter workers left idle when expected deliveries don’t arrive or unprepared job sites when materials show up sooner than anticipated.
The lack of in-transit tracking capability is a key pain point. When project teams can’t accurately pinpoint delivery ETAs, it becomes extremely challenging to manage labor, equipment, and site preparations effectively. This results in wasted time, increased costs, and scheduling impacts that can derail an entire project timeline.
To mitigate these risks, we recommend investing in logistics management solutions that provide end-to-end supply chain visibility. Real-time tracking of materials in transit allows for more agile planning and helps minimize costly disruptions on the job site. Proactive communication with suppliers and transporters is also critical for setting realistic delivery expectations.
While transportation and logistics challenges may seem daunting, addressing them head-on is crucial for keeping projects on schedule and within budget. With the right strategies and technologies in place, these supply chain challenges can be effectively overcome.
Why Is Labor Shortage a Critical Supply Chain Challenge?

The construction industry faces a significant supply chain challenge beyond materials and equipment—a severe shortage of skilled labor. At EB3 Construction, we’ve seen firsthand how this shortage creates bottlenecks throughout the construction process, from manufacturing and transportation to on-site execution.
The scale of the problem is substantial. Our industry needs to recruit over half a million workers just to meet current demand. Additionally, nearly 2 million construction workers are expected to leave their jobs this year. With around 20% of the workforce aged 55 or older, we face an impending wave of retirements that will further intensify the shortage.
This labor shortage affects every aspect of our projects. We often struggle to find enough skilled tradespeople to meet tight schedules. The lack of truck drivers and equipment operators can delay material deliveries and slow down crucial sitework. Even filling administrative and management roles has become more challenging, impacting project coordination and oversight.
To address this critical issue, we’re taking a multi-faceted approach. We’ve revamped our apprenticeship programs to fast-track skills development while providing competitive pay and benefits. We’re also adopting modern construction technologies and practices to improve efficiency and attract tech-savvy younger workers.
Moreover, we’re actively engaging with high schools and vocational programs to build a sustainable talent pipeline. By showcasing rewarding career paths in construction, we aim to inspire the next generation of builders and tradespeople.
The labor shortage remains an ongoing challenge, but we are committed to developing innovative solutions. By investing in our workforce and adapting our practices, we strive to maintain the skilled teams necessary to deliver exceptional results for our clients, even in this tight labor market.
Aspect | Value |
---|---|
Current Payroll Construction Workers | 8.3 million |
Residential Construction Workers | 3.4 million |
Annual Construction Worker Hiring Need | 723,000 |
Shortfall in Construction Jobs Needed by 2025 | 439,000 |
What Collaboration and Communication Failures Affect the Construction Supply Chain?
Communication breakdowns between vendors, suppliers, and project stakeholders cause significant disruptions in construction supply chains. When information doesn’t flow smoothly, materials fail to arrive when and where they’re most needed. This issue regularly manifests on job sites across the industry.
Poor coordination between material suppliers and transportation providers is a major issue. A supplier may have inventory ready, but without aligned logistics, those crucial materials remain stationary instead of reaching the construction site on time. This mismatch creates bottlenecks that impact the entire project timeline.
Many construction firms still heavily rely on phone calls, emails, and spreadsheets to manage vendor relationships and material orders. While familiar, these traditional communication methods are insufficient for the complex, fast-paced nature of modern construction supply chains. The result is a slow, unresponsive system prone to errors and delays.
Digital collaboration platforms offer a compelling solution to these persistent challenges. By connecting all tiers of the supply chain within a unified system, these technologies enable real-time information sharing across organizations. Suppliers gain visibility into project timelines and material needs, while contractors can accurately track orders and shipments. When disruptions occur, all parties can swiftly coordinate to develop contingency plans.
The most advanced platforms go beyond basic communication to enable continuous alignment of forecasts, production capacity, inventory levels, and build schedules. This holistic view allows the supply chain to adapt as conditions change. Materials arrive just in time—neither too early nor too late. Labor and equipment utilization improves, and project milestones stay on track.
While digital transformation demands upfront investment, the long-term benefits for supply chain performance are evident. As more firms embrace these collaborative technologies, we expect to see fewer shortages, less waste, and smoother project delivery across the construction industry.
Benefit | Description |
---|---|
Increased Efficiency | Organizations experienced a 30% boost in supply chain efficiency by implementing digital technologies, according to a survey by Accenture. |
Cost Reduction | Operational costs decreased by 35% with the adoption of digital collaboration frameworks. |
Information Sharing | Real-time data and shared visibility help align activities, goals, and objectives closely, supporting order scheduling and inventory management, ultimately reducing lead times. |
Strengthened Supplier Relationships | Collaborative platforms foster transparent communication and collaboration on joint initiatives, leading to improved performance. |
Sustainability | Collaboration helps identify ways to lower inventory, reduce carbon emissions, and manage resources better for a lesser environmental impact. |
Conclusion: Strategies for Mitigating Construction Supply Chain Issues
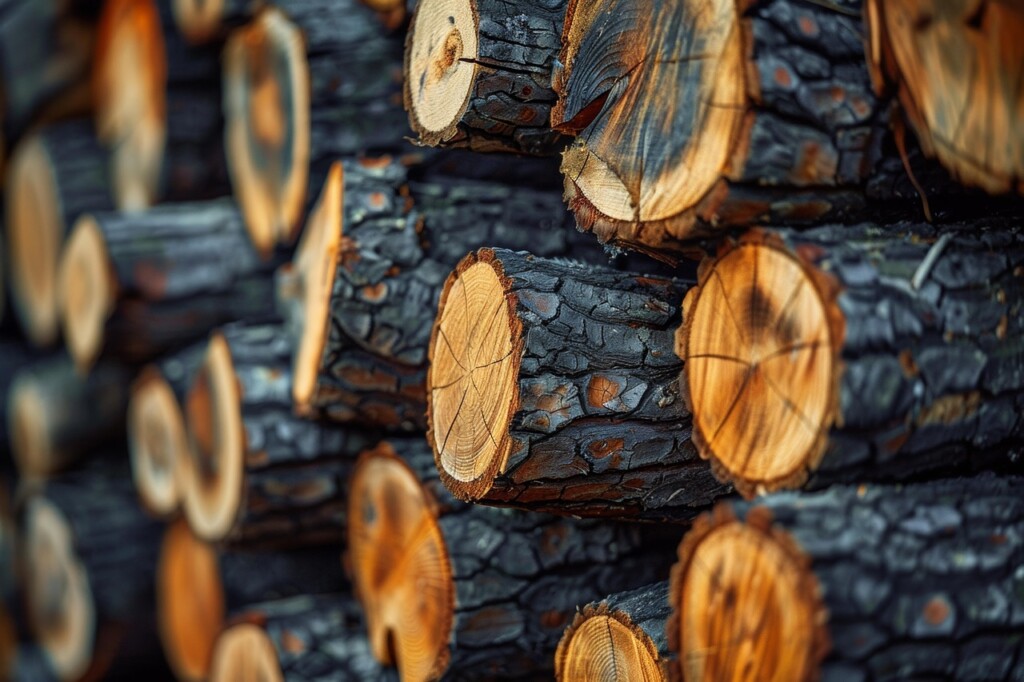
Despite ongoing challenges, the construction industry is adapting with innovative approaches to supply chain management. Firms are implementing cost escalation clauses and force majeure provisions in contracts, diversifying material sourcing, and modifying project specifications to accommodate substitutions while maintaining quality. Digital technologies such as real-time tracking systems, centralized communication platforms, and automated reconciliation tools offer promising solutions for increased visibility and efficiency.
The industry has adjusted to the new reality of supply chain complexities, but continued investment in workforce development and technological advancement will be essential for long-term resilience and competitiveness. Construction companies that proactively adopt risk mitigation strategies and embrace supply chain optimization techniques will be best positioned to handle future disruptions.
Key takeaways for construction professionals include:
- Review and update contract language to fairly allocate supply chain risks.
- Develop relationships with multiple suppliers across different regions.
- Invest in digital supply chain management tools to improve visibility and coordination.
- Train staff on strategic sourcing and supply chain risk assessment.
- Collaborate closely with owners, designers, and subcontractors on material specifications and alternatives.
By taking a strategic, technology-enabled approach to supply chain management, the construction industry can build greater resilience and adaptability in the face of ongoing global uncertainties. While challenges remain, firms that prioritize supply chain innovation will create competitive advantages and deliver more predictable project outcomes.
To learn more about construction supply chain solutions, contact EB3 Construction to discuss your project needs.