Imagine this scenario: you’re at the site of a major commercial development, set to open in a few months. The foundation is poured, and steel beams stretch toward the sky, but work has come to a standstill. Equipment remains idle as crews await delayed materials. Meanwhile, costs are escalating, and the client is growing impatient. This situation highlights why construction delays are a significant concern in the industry.
Construction delays happen when projects exceed their planned timeline due to various factors, both within the contractor’s control and beyond it. These setbacks can rapidly escalate—inflating budgets, straining client relationships, and potentially leading to expensive litigation. For general contractors like us at EB3 Construction, understanding and proactively addressing the root causes of delays is crucial to keeping projects on track.
So, what exactly causes construction timelines to derail? While each project faces unique challenges, some common culprits include labor and material shortages, permitting delays, design changes, weather events, and communication breakdowns among stakeholders. In the following sections, we will explore these delay factors in more depth and share proven strategies we use to mitigate their impact. By implementing robust planning processes, leveraging technology, and fostering strong communication, we strive to safeguard project progression and deliver results on time and within budget.
What Are the Most Common Reasons for Construction Delays?
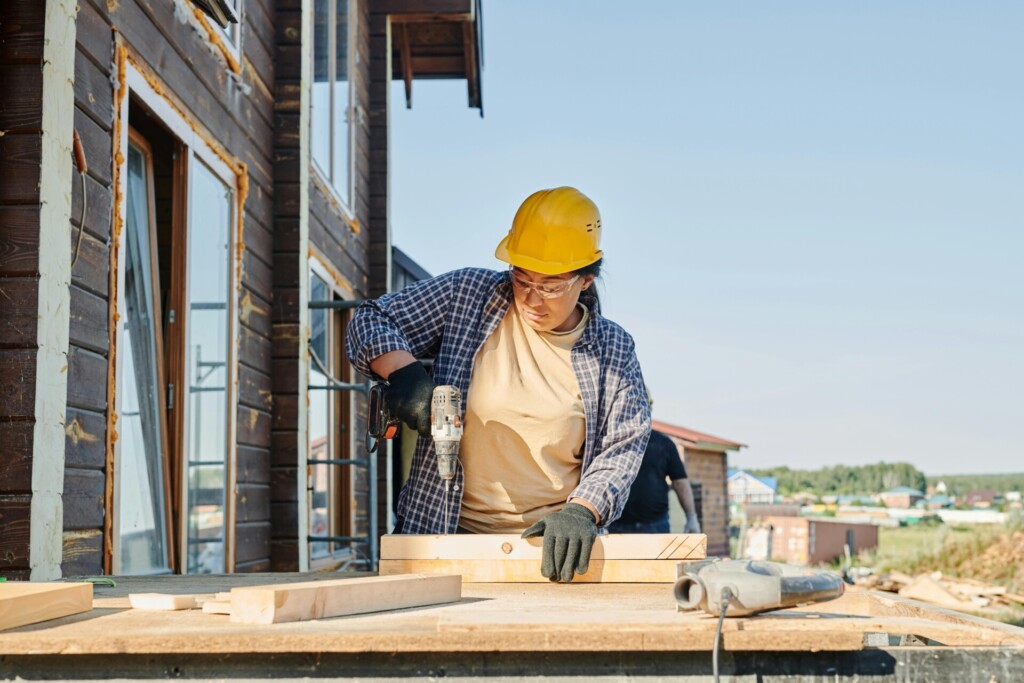
Several factors typically contribute to construction delays, with scope of work issues leading the list. Poorly defined project scopes or changes during construction can significantly impact timelines. When project requirements are not clearly outlined from the start or undergo major revisions mid-project, crews often find themselves redoing work or waiting for updated plans. This ripple effect can disrupt the entire project schedule.
Budget conflicts and funding issues present another major hurdle. When costs exceed initial estimates or promised funding falls through, work may grind to a halt until financial matters are resolved. According to industry data, over 60% of construction projects experience cost overruns, highlighting how common budget-related delays can be.
Labor shortages continue to affect the construction industry, causing delays on projects of all sizes. With skilled workers in high demand, contractors often struggle to fully staff their projects. This can slow progress considerably, especially for specialized tasks that require specific expertise.
Unrealistic schedules set projects up for delays from the start. When timelines don’t account for the full complexity of work or potential setbacks, even minor issues can derail the entire schedule. Careful, data-driven planning is essential to create achievable project timelines.
Unforeseen site conditions frequently lead to construction delays. Despite thorough site surveys, contractors may encounter unexpected soil issues, buried utilities, or environmental concerns once work begins. These surprises can require significant design changes or additional permits before work can proceed.
Design errors or omissions in project plans create costly delays as teams work to resolve issues and obtain necessary approvals for changes. Clear communication between designers and builders is crucial to minimize these types of delays.
Project complexity itself can be a major factor in delays. As buildings become more technologically advanced and sustainability requirements increase, coordinating all aspects of construction grows more challenging. This complexity leaves more room for scheduling conflicts and miscommunication.
Finally, adverse weather events remain an ever-present risk in construction. While some delays due to weather are expected, severe storms or unusual conditions can set projects back significantly. Climate change is worsening this issue, with more frequent extreme weather events impacting construction timelines globally.
Cause | Details |
Waiting for other disciplines | Leading cause due to poorly executed handoffs between trades. |
Staffing shortages | Significant contributor due to ongoing labor challenges. |
Material and equipment delays | Third major contributor reflecting supply chain issues. |
Design changes | Infrequent but causes significant delays when they occur. |
Weather | Unpredictable external factor affecting project timelines. |
Economic changes | Leads to budget conflicts and project delays. |
Project Complexity | Can result in increased costs and extended timelines. |
Budget conflicts | Over 60% of projects experience cost overruns leading to delays. |
Communication issues | Weak communication contributes to project delays. |
By understanding these common causes of delays, construction firms can take proactive steps to mitigate risks and keep projects on track. Thorough planning, clear communication, and building flexibility into schedules are key strategies for avoiding costly setbacks.
How Do Labor Challenges Impact Construction Timelines?
Labor issues are among the major causes of construction delays today. The construction industry is grappling with a severe shortage of skilled workers, directly affecting project timelines and efficiency.
Several factors contribute to this persistent labor crisis:
- Many experienced workers left the industry during past economic downturns
- Few of those workers have returned to construction careers
- Younger generations are showing less interest in pursuing construction jobs
The scale of this shortage is significant. According to Associated Builders and Contractors, the construction industry needed to attract an estimated 546,000 additional laborers in 2023 beyond normal hiring levels just to meet demand. This massive workforce gap has extensive consequences:
- Difficulty allocating adequate crews to projects
- Reduced overall efficiency and productivity on job sites
- Increased safety risks due to overworked or undertrained staff
- Potential quality control issues from lack of skilled labor
As a result, construction firms often struggle to complete projects on schedule. Labor shortages can lead to work stoppages, slower progress, and difficulty coordinating subcontractors – all contributing to project delays.
While the labor shortage remains a significant challenge, the construction industry is actively working to address it through improved recruitment, training programs, and adopting new technologies. Innovations like construction management software, prefabrication, and even robotics are helping firms optimize their existing workforce and mitigate some impacts of the labor crunch. However, developing a robust skilled labor pipeline remains crucial for the industry’s long-term health and ability to deliver projects on time.
What Financial Impact Do Construction Delays Have on Projects?
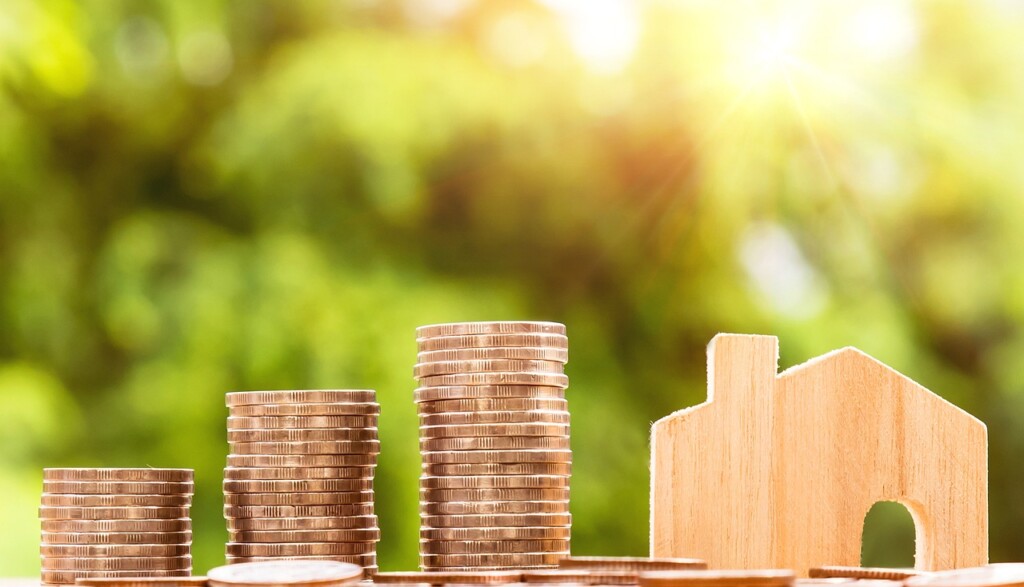
The financial consequences of construction delays can be severe and extensive. When projects extend beyond planned timelines, costs increase significantly across multiple areas:
Labor Costs
Labor expenses rise substantially due to:
- Overtime premiums for extended work hours
- Crew retention costs to keep workers on-site longer
- Additional supervision expenses
On a typical $10 million project, a 30-day delay can result in additional labor costs exceeding $300,000.
Material Costs
Delays also increase material expenses through:
- Price escalation over time
- Extended storage fees
- Material deterioration and waste
- Rush order premiums to expedite delivery
Cash Flow Problems
Perhaps most critically, delays lead to significant cash flow issues:
- Missed milestone payments from clients
- Extended financing costs and interest charges
- Strain on working capital
- Damaged vendor relationships due to late payments
For example, on a recent $50 million commercial construction project in Denver, a 3-month delay caused by permitting issues and labor shortages resulted in over $2 million in unanticipated costs. This included $800,000 in additional labor, $500,000 in material price increases, and $700,000 in extended financing charges and overhead.
Quantifying the Impact
While impacts vary by project, research suggests that construction delays typically increase overall project costs by 5–20%. For a $10 million project, this translates to $500,000 to $2 million in cost overruns.
The ripple effects of these financial impacts can be enduring. Cost overruns erode profit margins, strain relationships with clients and vendors, and potentially harm a construction firm’s reputation and ability to secure future work. Carefully managing timelines and proactively addressing potential delays is critical for maintaining the financial health of construction projects and companies.
Disclaimer: Pricing figures are based on publicly available market data and are intended for general estimation purposes as of July 2025. They do not represent a formal quote from EB3 Construction. Actual costs will vary by project scope, location, labor rates, and material prices.
How Can Construction Companies Prevent and Manage Delays?
Preventing and managing delays is crucial for keeping construction projects on schedule and within budget. At EB3 Construction, we’ve developed proven strategies to mitigate common causes of delays and efficiently handle unexpected issues when they arise. Here are some key approaches we implement:
Comprehensive Pre-Construction Planning
We place a strong emphasis on thorough planning before starting construction. This includes:
- Developing detailed scope of work documents that clearly define all project requirements
- Obtaining accurate cost and time estimates through careful analysis
- Identifying potential risks and creating mitigation plans
- Establishing realistic project timelines with built-in contingencies
By investing time upfront to plan meticulously, we reduce the likelihood of unforeseen issues causing delays later.
Improving Stakeholder Communication
Clear, consistent communication is vital for preventing misunderstandings that can lead to delays. We facilitate this by:
- Implementing cloud-based project management software to centralize information
- Holding regular coordination meetings with all key stakeholders
- Establishing clear channels for quickly addressing questions or concerns
- Providing real-time project updates to keep everyone informed
Effective Subcontractor Management
Coordinating multiple subcontractors is often a major challenge. We prevent delays through:
- Careful vetting and selection of reliable subcontractors
- Clear communication of project timelines and expectations
- Regular check-ins to monitor progress and address any issues
- Having backup options in case a subcontractor falls behind
Leveraging Construction Technology
We utilize advanced technology solutions to streamline processes and improve efficiency:
- Building Information Modeling (BIM) for enhanced project visualization and coordination
- Cloud-based project management platforms for real-time collaboration
- Mobile apps for on-site progress tracking and reporting
- Drones and 3D scanning for accurate site surveys and inspections
Proactive Risk Management
Anticipating and planning for potential risks is crucial. Our approach includes:
- Conducting thorough risk assessments at the project’s outset
- Developing contingency plans for likely scenarios (e.g., weather delays, material shortages)
- Regularly reviewing and updating risk management strategies throughout the project
- Maintaining financial reserves to quickly address unexpected issues
Proper Documentation and Claim Management
When delays occur despite prevention efforts, we ensure proper handling through:
- Detailed documentation of all delay causes and impacts
- Prompt notification to relevant parties as per contractual requirements
- Thorough analysis to determine responsibility and potential time/cost implications
- Proactive development of recovery plans to get back on schedule
By implementing these strategies, we at EB3 Construction work diligently to keep projects on track and deliver successful outcomes for our clients. Our proactive approach to delay prevention and management has proven effective in minimizing disruptions and maintaining project momentum.
Strategy | Description |
Comprehensive Pre-Construction Planning | Includes developing detailed scope of work documents, obtaining accurate cost and time estimates, identifying risks, and establishing realistic timelines with contingencies. |
Improving Stakeholder Communication | Involves implementing cloud-based project management software, holding regular meetings, establishing communication channels, and providing real-time updates. |
Effective Subcontractor Management | Includes careful vetting and selection, clear communication of timelines, regular progress check-ins, and having backup options. |
Leveraging Construction Technology | Utilizes Building Information Modeling (BIM), mobile apps, cloud-based platforms, drones, and 3D scanning for improved efficiency. |
Proactive Risk Management | Involves conducting risk assessments, developing contingency plans, regular strategy reviews, and maintaining financial reserves. |
Proper Documentation and Claim Management | Ensures detailed documentation, prompt notification, thorough analysis of implications, and development of recovery plans. |
Conclusion: Safeguarding Projects Against Costly Delays
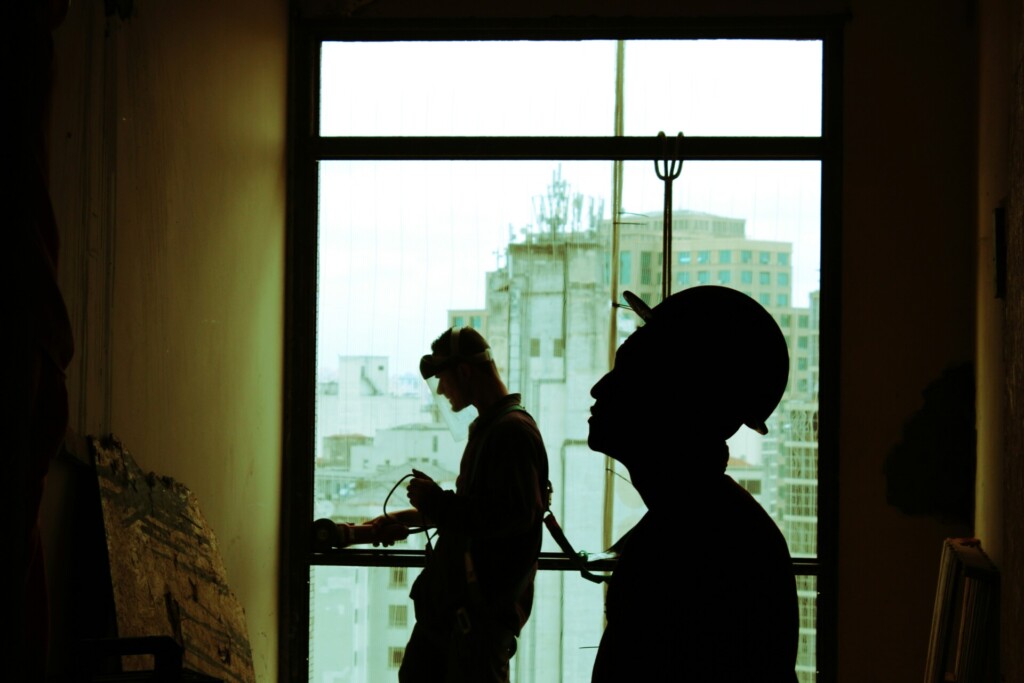
Construction delays remain one of the industry’s most significant challenges, with the potential to turn profitable projects into financial burdens. By understanding common delay causes, implementing proactive planning measures, improving communication, and leveraging modern technology solutions, construction companies can better protect their timelines and profit margins. Success hinges on anticipating potential issues before they escalate into major delays, along with having clear strategies to address them when they arise.
As the construction industry evolves, companies that prioritize delay prevention and mitigation will be best positioned for success. Forward-thinking firms are increasingly adopting data-driven approaches to identify delay risks early, enhancing collaboration across project teams, and embracing flexible planning methods to adapt to unforeseen circumstances. By viewing delay management as an ongoing process rather than a reactive measure, construction managers can create more resilient project timelines.
Safeguarding projects against delays requires a holistic approach that combines strategic planning, effective communication, and the right technological tools. Construction professionals should regularly assess and refine their delay prevention strategies to stay ahead of evolving industry challenges. Those who make delay mitigation a core part of their project management approach will be better equipped to deliver projects on time and on budget, enhancing their reputation and profitability in an increasingly competitive market.
To learn more about optimizing your construction timelines and implementing robust delay prevention strategies, contact EB3 Construction for a consultation on how we can help safeguard your next project.